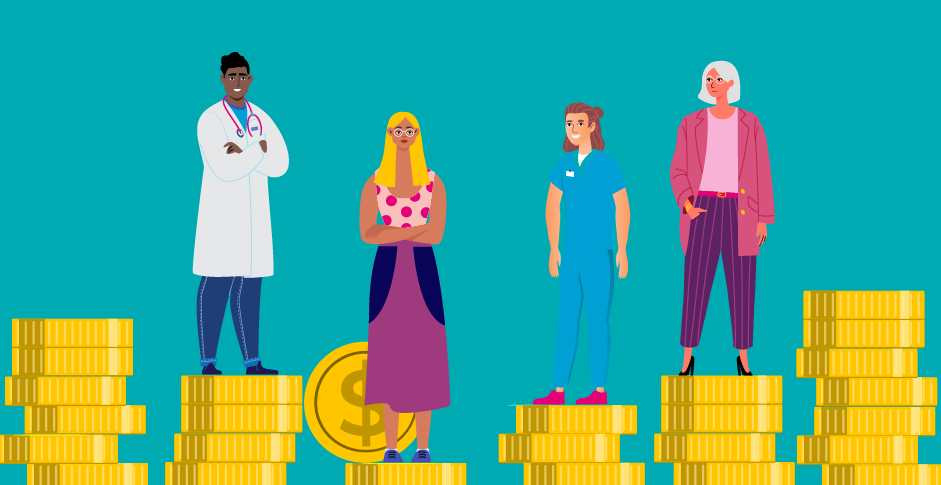
Regardless of what type of engineering career you are interested in, there are plenty of industrial engineering jobs in Dallas. There are many choices available, from transportation equipment and computer manufacturers to electronics manufacturers. Many plants require qualified industrial engineers in order to maintain smooth production.
Industrial engineers can help improve processes by identifying ways to improve and analyzing their effectiveness. Most of the time, industrial engineers work in teams with other engineers. These professionals require strong project management skills and math skills in order to implement changes efficiently. They are also responsible to train and report. These engineers are often employed in corporations as well small- and mid-sized businesses.
Many industrial engineers work as consultants and clients-facing professionals. These roles can include software development, business analysis, and data analysis. Industrial engineers work on projects that improve production efficiency and lower costs. Many industrial engineers work in the manufacturing and transport equipment industries. They can also work in the aviation and consumer goods sectors. According to the Bureau of Labor Statistics (BLS), the number of jobs in industrial engineering will rise by 10% over the next ten years.
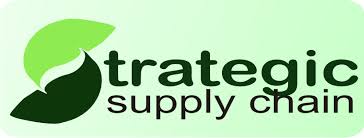
An industrial engineer's primary task is to spot wasteful practices in the production process. This requires the engineer to work with the right teams to identify opportunities for improvement. Also, industrial engineers are responsible for saving energy and time. This goal requires strong math skills as well as a desire for less waste. It can be very rewarding to work as an industrial engineer.
Dallas is home to many industrial engineering jobs. These cities include Plano, McKinney, and Frisco. Dallas is home to the majority of industrial engineers. Other industries that are looking for qualified engineers include computer and electronics manufacturers, and professional scientific and technical services.
Industrial engineers are often employed in a variety of roles, from a team leader to a manager. You can apply for a Monster profile if you're interested in a career in industrial engineering. This site allows users to upload their resumes, create job alerts and receive expert advice. Find an industrial engineering job in Dallas by starting your search now.
An internship is a great option if you are interested in pursuing a career as an industrial engineer. The majority of industrial engineering internships require that you commute less than 30 miles. These internships are great for gaining industry experience and learning valuable career skills. Business classes are also available for industrial engineers. Many universities offer business courses and parallel IE classes.
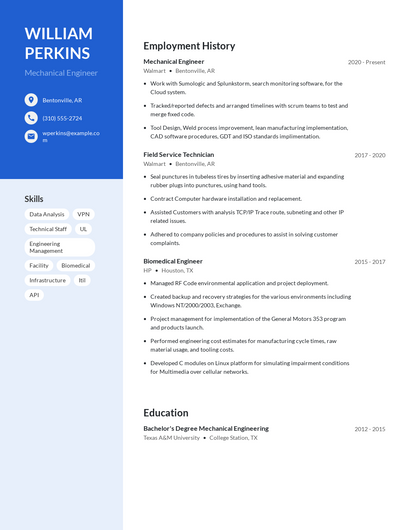
Industrial engineers will work closely with other engineers and analysts to improve company processes. You might also be responsible for analyzing and tracking labor standards as well as maintaining labor management systems.
FAQ
What are the 4 types manufacturing?
Manufacturing is the process that transforms raw materials into useful products. It can involve many activities like designing, manufacturing, testing packaging, shipping, selling and servicing.
How can manufacturing efficiency be improved?
First, identify the factors that affect production time. The next step is to identify the most important factors that affect production time. You can start by identifying the most important factors that impact production time. Once you've identified them, try to find solutions for each of those factors.
What does it take for a logistics enterprise to succeed?
A successful logistics business requires a lot more than just knowledge. Good communication skills are essential to effectively communicate with your suppliers and clients. You should be able analyse data and draw inferences. You must be able and able to handle stress situations and work under pressure. To improve efficiency, you must be innovative and creative. You will need strong leadership skills to motivate and direct your team members towards achieving their organizational goals.
You should also be organized and efficient to meet tight deadlines.
How can manufacturing avoid production bottlenecks
Production bottlenecks can be avoided by ensuring that processes are running smoothly during the entire production process, starting with the receipt of an order and ending when the product ships.
This includes planning for capacity requirements as well as quality control measures.
Continuous improvement techniques such Six Sigma can help you achieve this.
Six Sigma is a management method that helps to improve quality and reduce waste.
It seeks to eliminate variation and create consistency in your work.
What are my options for learning more about manufacturing
Hands-on experience is the best way to learn more about manufacturing. You can read books, or watch instructional videos if you don't have the opportunity to do so.
Statistics
- In 2021, an estimated 12.1 million Americans work in the manufacturing sector.6 (investopedia.com)
- (2:04) MTO is a production technique wherein products are customized according to customer specifications, and production only starts after an order is received. (oracle.com)
- According to the United Nations Industrial Development Organization (UNIDO), China is the top manufacturer worldwide by 2019 output, producing 28.7% of the total global manufacturing output, followed by the United States, Japan, Germany, and India.[52][53] (en.wikipedia.org)
- According to a Statista study, U.S. businesses spent $1.63 trillion on logistics in 2019, moving goods from origin to end user through various supply chain network segments. (netsuite.com)
- It's estimated that 10.8% of the U.S. GDP in 2020 was contributed to manufacturing. (investopedia.com)
External Links
How To
How to use lean manufacturing in the production of goods
Lean manufacturing is a management style that aims to increase efficiency and reduce waste through continuous improvement. It was created in Japan by Taiichi Ohno during the 1970s and 80s. He received the Toyota Production System award (TPS), from Kanji Toyoda, founder of TPS. The first book published on lean manufacturing was titled "The Machine That Changed the World" written by Michael L. Watkins and published in 1990.
Lean manufacturing, often described as a set and practice of principles, is aimed at improving the quality, speed, cost, and efficiency of products, services, and other activities. It is about eliminating defects and waste from all stages of the value stream. Lean manufacturing is called just-in-time (JIT), zero defect, total productive maintenance (TPM), or 5S. Lean manufacturing focuses on eliminating non-value-added activities such as rework, inspection, and waiting.
Lean manufacturing can help companies improve their product quality and reduce costs. Additionally, it helps them achieve their goals more quickly and reduces employee turnover. Lean manufacturing is considered one of the most effective ways to manage the entire value chain, including suppliers, customers, distributors, retailers, and employees. Lean manufacturing is widely used in many industries. For example, Toyota's philosophy underpins its success in automobiles, electronics, appliances, healthcare, chemical engineering, aerospace, paper, food, etc.
Five fundamental principles underlie lean manufacturing.
-
Define value - Find out what your business contributes to society, and what makes it different from other competitors.
-
Reduce waste - Stop any activity that isn't adding value to the supply chains.
-
Create Flow – Ensure that work flows smoothly throughout the process.
-
Standardize and Simplify – Make processes as consistent, repeatable, and as simple as possible.
-
Develop Relationships: Establish personal relationships both with internal and external stakeholders.
Lean manufacturing, although not new, has seen renewed interest in the economic sector since 2008. Many companies have adopted lean manufacturing methods to increase their marketability. In fact, some economists believe that lean manufacturing will be an important factor in economic recovery.
Lean manufacturing has many benefits in the automotive sector. These benefits include increased customer satisfaction, reduced inventory levels and lower operating costs.
You can apply Lean Manufacturing to virtually any aspect of your organization. It is especially useful for the production aspect of an organization, as it ensures that every step in the value chain is efficient and effective.
There are three main types in lean manufacturing
-
Just-in-Time Manufacturing (JIT): This type of lean manufacturing is commonly referred to as "pull systems." JIT refers to a system in which components are assembled at the point of use instead of being produced ahead of time. This approach aims to reduce lead times, increase the availability of parts, and reduce inventory.
-
Zero Defects Manufacturing - ZDM: ZDM focuses its efforts on making sure that no defective units leave a manufacturing facility. It is better to repair a part than have it removed from the production line if it needs to be fixed. This is also true for finished products that require minor repairs before shipping.
-
Continuous Improvement (CI): CI aims to improve the efficiency of operations by continuously identifying problems and making changes in order to eliminate or minimize waste. Continuous Improvement (CI) involves continuous improvement in processes, people, tools, and infrastructure.