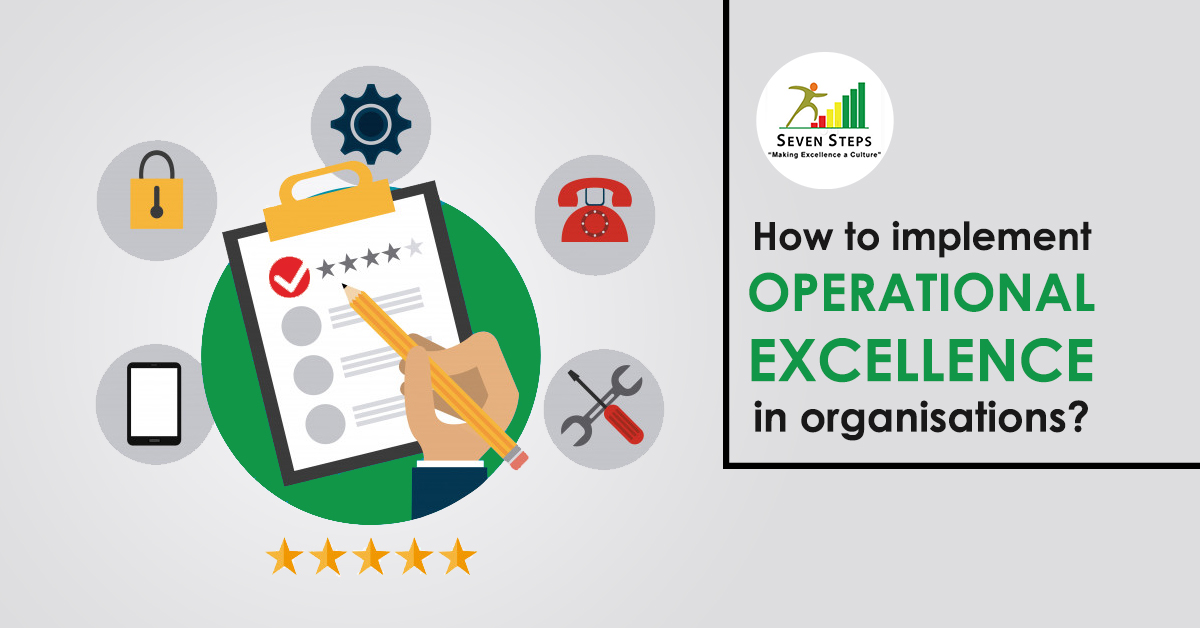
Tampa offers many different logistics jobs. You can find many jobs in the healthcare, manufacturing and construction industries. However, you can also work in wholesale trade or with consulting firms to help streamline supply chains for a variety of different businesses.
A degree can provide a wide range of career options. Entry-level positions such as shipping clerks can be found with an associate degree, while more advanced jobs are available for those who hold bachelor's degrees. If you have specific goals and interests, you can specialize in a certain area of logistics.
Careers in logistics are expanding, with BLS data predicting that employment for these professionals will rise by 5% between 2018 and 2028. The projected job growth is even higher for professionals who specialize in business operations.
You can earn a Logistics degree at either a Community College or a Four-Year University. These programs usually offer a wide range of logistics specializations. This allows you to develop more specialized skills, and make you more employable when you advance up the ladder.
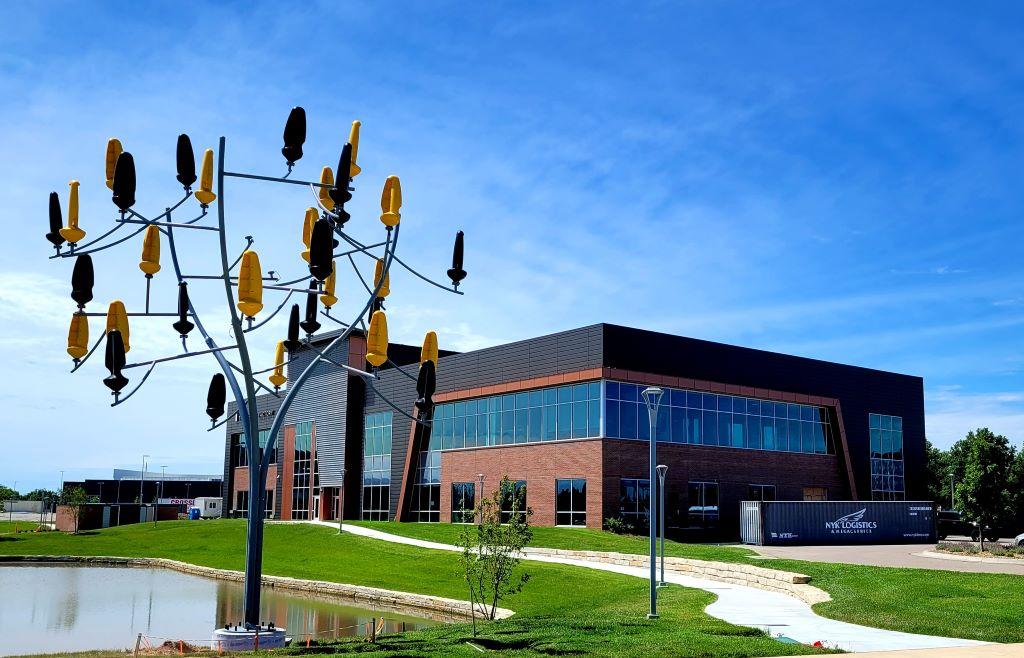
In addition to pursuing a bachelor's degree, students should consider taking part in internships and networking opportunities. These experiences can provide you with valuable, hands-on work experience. They can also help you find a logistics job.
The logistics industry has a diverse workforce, and job prospects are generally good. You can get a job in the logistics industry anywhere, but particularly in states with a large population and high growth, such as California and Texas. You can find jobs in many different sectors such as oil and gas, aerospace or other.
You should take into account the size and capabilities of a logistics provider when choosing one. The ideal 3PL is one that can customize a solution to fit your specific business needs. This will allow you to reduce your overall costs and increase your efficiencies.
Supply chain management is crucial to your business' success. To ensure that your product arrives at the correct time in perfect condition, you must have the appropriate people and tools. Selecting a third-party provider of logistics that is experienced in your industry can help you improve the efficiency and effectiveness of your supply chain.
Sheer is an all-service 3PL located in Tampa that can increase your supply chain’s efficiency, while also lowering your cost. We offer our clients a variety services, including transportation management, inventory control, and shipping.
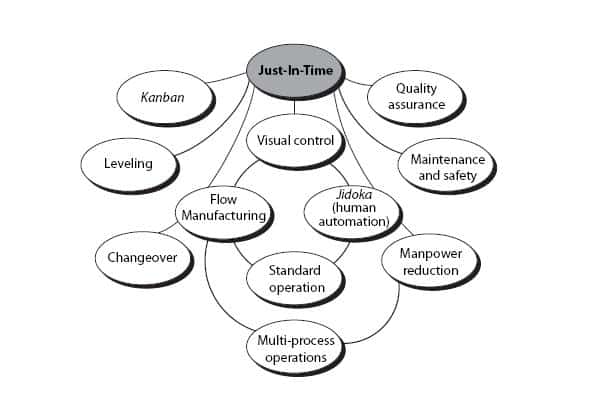
We offer a range of technology tools that will help you manage and track your supply chain. Our suite of cloud-based software integrates seamlessly with your ERP system. This allows you to manage and monitor your entire business.
Sheer's multimodal network can transform your supply chains from liabilities to assets. We will always deliver your products safely and on time.
FAQ
How can manufacturing prevent production bottlenecks?
You can avoid bottlenecks in production by making sure that everything runs smoothly throughout the production cycle, from the moment you receive an order to the moment the product is shipped.
This includes planning for both capacity requirements and quality control measures.
Continuous improvement techniques such Six Sigma are the best method to accomplish this.
Six Sigma can be used to improve the quality and decrease waste in all areas of your company.
It's all about eliminating variation and creating consistency in work.
What is the role of a manager in manufacturing?
A manufacturing manager must ensure that all manufacturing processes are efficient and effective. They should also be aware of any problems within the company and act accordingly.
They should also be able communicate with other departments, such as sales or marketing.
They should be up to date on the latest trends and be able apply this knowledge to increase productivity and efficiency.
How does a production planner differ from a project manager?
The difference between a product planner and project manager is that a planer is typically the one who organizes and plans the entire project. A production planner, however, is mostly involved in the planning stages.
What are the four types of manufacturing?
Manufacturing is the process of transforming raw materials into useful products using machines and processes. It involves many different activities such as designing, building, testing, packaging, shipping, selling, servicing, etc.
What's the difference between Production Planning & Scheduling?
Production Planning (PP) refers to the process of determining how much production is needed at any given moment. This is done through forecasting demand and identifying production capacities.
Scheduling refers the process by which tasks are assigned dates so that they can all be completed within the given timeframe.
How can manufacturing efficiency improved?
First, determine which factors have the greatest impact on production time. We then need to figure out how to improve these variables. You can start by identifying the most important factors that impact production time. Once you have identified the factors, then try to find solutions.
What skills are required to be a production manager?
A production planner must be organized, flexible, and able multitask to succeed. Effective communication with clients and colleagues is essential.
Statistics
- Many factories witnessed a 30% increase in output due to the shift to electric motors. (en.wikipedia.org)
- In 2021, an estimated 12.1 million Americans work in the manufacturing sector.6 (investopedia.com)
- (2:04) MTO is a production technique wherein products are customized according to customer specifications, and production only starts after an order is received. (oracle.com)
- According to a Statista study, U.S. businesses spent $1.63 trillion on logistics in 2019, moving goods from origin to end user through various supply chain network segments. (netsuite.com)
- You can multiply the result by 100 to get the total percent of monthly overhead. (investopedia.com)
External Links
How To
How to use 5S in Manufacturing to Increase Productivity
5S stands in for "Sort", the "Set In Order", "Standardize", or "Separate". Toyota Motor Corporation created the 5S methodology in 1954. It allows companies to improve their work environment, thereby achieving greater efficiency.
This method aims to standardize production processes so that they are repeatable, measurable and predictable. This means that every day tasks such cleaning, sorting/storing, packing, and labeling can be performed. Through these actions, workers can perform their jobs more efficiently because they know what to expect from them.
There are five steps that you need to follow in order to implement 5S. Each step involves a different action which leads to increased efficiency. If you sort items, it makes them easier to find later. When you arrange items, you place them together. After you have divided your inventory into groups you can store them in easy-to-reach containers. Labeling your containers will ensure that everything is correctly labeled.
Employees will need to be more critical about their work. Employees need to be able understand their motivations and discover alternative ways to do them. To implement the 5S system, employees must acquire new skills and techniques.
In addition to increasing efficiency, the 5S method also improves morale and teamwork among employees. They feel more motivated to work towards achieving greater efficiency as they see the results.