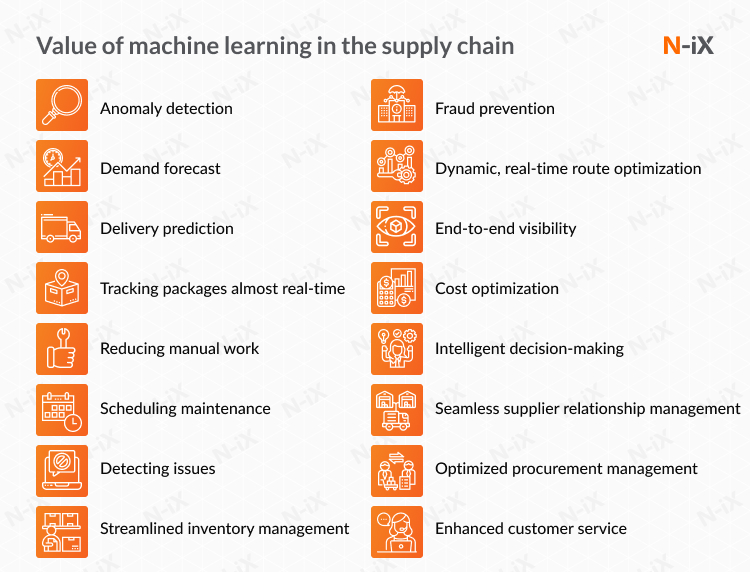
This article will cover the different types companies that are manufacturing in the U.S. The list will also include Industry trends and the costs involved in doing business in the U.S. Dun & Bradstreet is an excellent resource for manufacturers, as they gather information from a wide range of credible sources. This information is useful for manufacturers to assess their performance, growth potential and competitive pressures. This information is invaluable for any company looking to expand their operations.
List of manufacturing companies in the United States
The United States has 50 states, covering a large part of North America. Hawaii and Alaska are located in the northwestern part of the country, while major cities on the Atlantic coast include New York and Washington, DC. Los Angeles and Chicago, two of the most important cities in America, are both known for their iconic architecture and filmmaking. There are many different manufacturing companies in the United States, so it's important to find one that meets your requirements.
Contacts at all levels of the manufacturing company list in the United States must be included, from the top management to the floor. This can include all contacts involved in every aspect of the operation. It should also contain contacts for marketing and sales development as well as purchasing and quality assurance. It is important that you note that the list could be outdated as there are frequently updates.
Industry trends
Manufacturers have become more concerned about rising labor cost and raw material prices as the world demands goods. Some are turning to reshoring. Others are seeking to increase their flexibility to quickly change production lines. With this in place, manufacturers are increasingly looking to automated production and other sustainable manufacturing practices. Here are some key trends that you should be paying attention to. This article focuses on three of the most important trends for manufacturers manufacturing in the USA.
The U.S.'s manufacturing sector is a key indicator of its economic health. A rebound in manufacturing signals that the economy is moving towards extended growth and recovery. Manufacturers still face many challenges. Abhijit Bhide is the Managing Director at BofA Securities and discusses five trends that are driving the manufacturing sector. In addition to technological advances, the manufacturing sector is also becoming more resilient.
Costs of doing business at the U.S.
Although the U.S. is still a strong economy, rising prices and tariffs are having a negative impact on the business outlook. Many have predicted the impending global recession, but no one knows exactly when. In any event, in 2020, it is expected that the cost of doing American business will rise. This is good news both for American businesses and for newcomers.
While the cost of raw materials and labor may seem insignificant, you can't avoid the registration costs and startup costs. These expenses can have a negative impact on your business' profitability. However, you can reduce your overall costs to keep your business moving. Look for cost-saving options if you can't reduce these expenses. You might consider leasing or hiring equipment or finding more efficient ways of using your existing resources.
FAQ
What are manufacturing & logistics?
Manufacturing refers the process of producing goods from raw materials through machines and processes. Logistics covers all aspects involved in managing supply chains, including procurement and production planning. Manufacturing and logistics can often be grouped together to describe a larger term that covers both the creation of products, and the delivery of them to customers.
What are the responsibilities of a logistic manager?
A logistics manager makes sure that all goods are delivered on-time and in good condition. This is done using his/her knowledge of the company's products. He/she should ensure that sufficient stock is available in order to meet customer demand.
What does manufacturing mean?
Manufacturing Industries refers to businesses that manufacture products. Consumers are the people who purchase these products. To accomplish this goal, these companies employ a range of processes including distribution, sales, management, and production. These companies produce goods using raw materials and other equipment. This covers all types of manufactured goods including clothing, food, building supplies and furniture, as well as electronics, tools, machinery, vehicles and pharmaceuticals.
Statistics
- In the United States, for example, manufacturing makes up 15% of the economic output. (twi-global.com)
- In 2021, an estimated 12.1 million Americans work in the manufacturing sector.6 (investopedia.com)
- [54][55] These are the top 50 countries by the total value of manufacturing output in US dollars for its noted year according to World Bank.[56] (en.wikipedia.org)
- It's estimated that 10.8% of the U.S. GDP in 2020 was contributed to manufacturing. (investopedia.com)
- You can multiply the result by 100 to get the total percent of monthly overhead. (investopedia.com)
External Links
How To
How to Use the 5S to Increase Productivity In Manufacturing
5S stands for "Sort", 'Set In Order", 'Standardize', & Separate>. Toyota Motor Corporation created the 5S methodology in 1954. It helps companies achieve higher levels of efficiency by improving their work environment.
The basic idea behind this method is to standardize production processes, so they become repeatable, measurable, and predictable. This means that every day tasks such cleaning, sorting/storing, packing, and labeling can be performed. Through these actions, workers can perform their jobs more efficiently because they know what to expect from them.
There are five steps that you need to follow in order to implement 5S. Each step involves a different action which leads to increased efficiency. If you sort items, it makes them easier to find later. You arrange items by placing them in an order. You then organize your inventory in groups. Labeling your containers will ensure that everything is correctly labeled.
This process requires employees to think critically about how they do their job. Employees need to understand the reasons they do certain jobs and determine if there is a better way. In order to use the 5S system effectively, they must be able to learn new skills.
The 5S method not only increases efficiency but also boosts morale and teamwork. Once they start to notice improvements, they are motivated to keep working towards their goal of increasing efficiency.