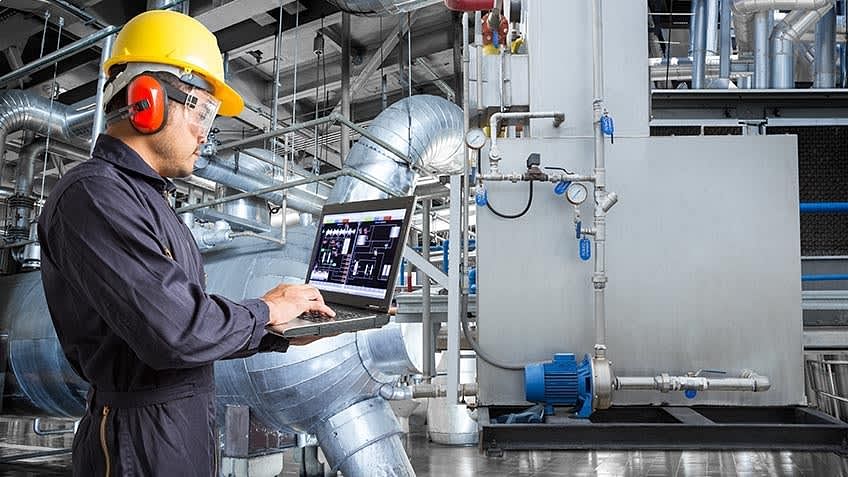
Japanese factories produce high-quality products at low costs. They are the backbone of the country's economy, accounting for five per cent of the country's GDP. However, they have struggled with tighter standards, growing competition and the cost pressures of the recent recession.
One example is the last-year government white paper that found Japanese firms unprepared for a cutoff in parts procurement. The recession took a toll on Japan's auto industry. The auto manufacturing industry relies on over 30,000 parts. Any disruption to the supply chain could cause the production to cease. Some parts cannot be replaced.
Japanese manufacturers collaborate closely with suppliers in order to fix problems and improve efficiency. This is to ensure that their products are high quality. They encourage feedback from salesmen, workers, and quality inspectors.
Japanese manufacturers have been concerned by the increasing number of factory floor accidents. There have been many safety scandals throughout the country's production sector. This has resulted in greater scrutiny of factories' work standards.
Non-regular staff is another problem that has impacted the production of Japanese products. Although non-regular staff allow companies to cut labor costs, they can also de-skill production workers and increase the likelihood of accidents. To train their regular workers, companies have been focusing on making them more reliable and safer.
Japan's growing labor shortage is due to the country's declining birthrate. Companies complaining about a shortage of labor are at an all-time high of 25 years. Japanese companies will face further challenges if their labor force shrinks.
Many factories are cutting their costs, despite the fact that there is a shortage of skilled workers. A growing number "factries" have fewer than 10 employees. These workshops are known for producing the highest quality equipment in the world.
Japan's manufacturing sector is being challenged by South Korea and China. Many factories are trying to cut costs and increase productivity as a result. However, the Japanese government warned that the industry would suffer if it loses its competitive advantage in foreign markets.
As Japan faces increased competition from Asia and abroad, it is facing questions about whether it can adjust its processes to meet demand and adapt quickly enough. Even if it is able to adapt, skilled workers are expected to increase.
Japanese factories are a major source of components for global markets. They also provide advanced materials such as silicon chips that are used in smart phones and computers. Although Chinese factories are skilled in low-cost assembly, the Japanese supply essential components.
The Japanese are now facing increased competition from foreigners, despite their efforts to improve their productivity. They have had to lower their product's value in the domestic marketplace due to the recession. But despite these challenges, the Japanese have been able to achieve a high level of excellence in their production.
FAQ
Why is logistics important in manufacturing?
Logistics are an essential component of any business. They help you achieve great results by helping you manage all aspects of product flow, from raw materials to finished goods.
Logistics also play a major role in reducing costs and increasing efficiency.
What are the products and services of logistics?
Logistics refers to all activities that involve moving goods from A to B.
They include all aspects associated with transport including packaging, loading transporting, unloading storage, warehousing inventory management customer service, distribution returns and recycling.
Logisticians ensure that products reach the right destination at the right moment and under safe conditions. They provide information on demand forecasts as well stock levels, production schedules and availability of raw material.
They coordinate with vendors and suppliers, keep track of shipments, monitor quality standards and perform inventory and order replenishment.
What jobs are available in logistics?
There are different kinds of jobs available in logistics. Some examples are:
-
Warehouse workers: They load and unload trucks, pallets, and other cargo.
-
Transport drivers - These are people who drive trucks and trailers to transport goods or perform pick-ups.
-
Freight handlers are people who sort and pack freight into warehouses.
-
Inventory managers - They oversee the inventory of goods in warehouses.
-
Sales reps - They sell products and services to customers.
-
Logistics coordinators - They plan and organize logistics operations.
-
Purchasing agents are those who purchase goods and services for the company.
-
Customer service representatives - Answer calls and email from customers.
-
Shipping clerks - They process shipping orders and issue bills.
-
Order fillers - These people fill orders based on what has been ordered.
-
Quality control inspectors are responsible for inspecting incoming and outgoing products looking for defects.
-
Others - There are many types of jobs in logistics such as transport supervisors and cargo specialists.
What is the job of a manufacturer manager?
A manufacturing manager must ensure that all manufacturing processes are efficient and effective. They must also be alert to any potential problems and take appropriate action.
They should also learn how to communicate effectively with other departments, including sales and marketing.
They must also keep up-to-date with the latest trends in their field and be able use this information to improve productivity and efficiency.
Why should you automate your warehouse?
Modern warehouses are increasingly dependent on automation. E-commerce has increased the demand for quicker delivery times and more efficient processes.
Warehouses should be able adapt quickly to new needs. Technology investment is necessary to enable warehouses to respond quickly to changing demands. Automating warehouses has many benefits. Here are some of the reasons automation is worth your investment:
-
Increases throughput/productivity
-
Reduces errors
-
Accuracy is improved
-
Safety enhancements
-
Eliminates bottlenecks
-
Allows companies scale more easily
-
Increases efficiency of workers
-
Gives you visibility into all that is happening in your warehouse
-
Enhances customer experience
-
Improves employee satisfaction
-
Reduces downtime and improves uptime
-
Quality products delivered on time
-
Removes human error
-
It helps ensure compliance with regulations
What are manufacturing and logistic?
Manufacturing refers the process of producing goods from raw materials through machines and processes. Logistics is the management of all aspects of supply chain activities, including procurement, production planning, distribution, warehousing, inventory control, transportation, and customer service. Sometimes manufacturing and logistics are combined to refer to a wider term that includes both the process of creating products as well as their delivery to customers.
What is the job of a logistics manger?
Logistics managers are responsible for ensuring that all goods arrive in perfect condition and on time. This is accomplished by using the experience and knowledge gained from working with company products. He/she also needs to ensure adequate stock to meet demand.
Statistics
- In the United States, for example, manufacturing makes up 15% of the economic output. (twi-global.com)
- It's estimated that 10.8% of the U.S. GDP in 2020 was contributed to manufacturing. (investopedia.com)
- In 2021, an estimated 12.1 million Americans work in the manufacturing sector.6 (investopedia.com)
- (2:04) MTO is a production technique wherein products are customized according to customer specifications, and production only starts after an order is received. (oracle.com)
- [54][55] These are the top 50 countries by the total value of manufacturing output in US dollars for its noted year according to World Bank.[56] (en.wikipedia.org)
External Links
How To
How to Use 5S for Increasing Productivity in Manufacturing
5S stands for "Sort", 'Set In Order", 'Standardize', & Separate>. Toyota Motor Corporation was the first to develop the 5S approach in 1954. It allows companies to improve their work environment, thereby achieving greater efficiency.
The idea behind standardizing production processes is to make them repeatable and measurable. It means tasks like cleaning, sorting or packing, labeling, and storing are done every day. Through these actions, workers can perform their jobs more efficiently because they know what to expect from them.
Implementing 5S involves five steps: Sort, Set in Order, Standardize Separate, Store, and Each step is a different action that leads to greater efficiency. For example, when you sort things, you make them easy to find later. When items are ordered, they are put together. After you have divided your inventory into groups you can store them in easy-to-reach containers. Finally, when you label your containers, you ensure everything is labeled correctly.
This process requires employees to think critically about how they do their job. Employees need to be able understand their motivations and discover alternative ways to do them. To be successful in the 5S system, employees will need to acquire new skills and techniques.
In addition to improving efficiency, the 5S system also increases morale and teamwork among employees. They are more motivated to achieve higher efficiency levels as they start to see improvement.