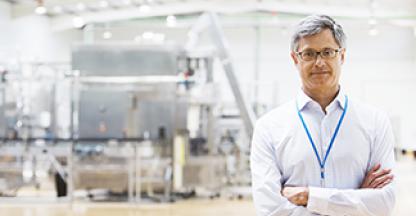
Creating a "Smart Factory" is more than just installing new technology. It's about changing the mindset of your factory and adapting to changes. With the right technology, you can help your customers, and help your business succeed in a new phase of manufacturing.
The first step is to determine what you want. Perhaps you want to build an intelligent factory that responds to drastic swings in demand. A smart factory can also be built to support global supply chain partners. Or you may want to create a smart factory that responds to an industry that is heavily reliant on manual labor. The next step is to create an ecosystem that supports your goal, no matter what it may be.
One key obstacle to a smart factory is a lack of connectivity. It can be hard to overcome this obstacle if you have outdated machinery and equipment. You might also have difficulty accessing the correct information regarding your systems and machines. According to the study, 33% of smart factory leaders believed that lack of IT infrastructure was a major obstacle to their ability build smart factories.
Technology is second. Many advanced manufacturing technologies are available at the moment. These technologies can help you increase your productivity and quality. These technologies can also make your plant more cost-effective.
Another aspect to be considered is the people. It is important to invest in the right skills at just the right time. You will need the right people as well as a talent strategy. It is important to have a clear scope and align everyone's priorities and timelines. It is important to ensure that the right people work on the right projects.
Process is the third important factor. It is important to ensure that all your processes and applications can connect to the network. This will help you to share information with other systems and processes in your factory. Lastly, you need to make sure that you have data and analytics in place. This will allow for data-driven decisions that can be used to your advantage and enable self-healing.
People are the fourth most important aspect to be considered. It is essential that you have a committed executive team. It can help to have a convener that can help coordinate and align efforts across multiple vendors. This can help ensure that your executive team is aware of the scope of the project.
Security is the fifth most critical factor. New technologies are available to help reduce the risk of cyberattacks on manufacturing environments. You need to ensure that you have the right cybersecurity strategy in place. You also need to ensure that you have a cybersecurity strategy that is ongoing.
You should also consider how you will connect your equipment and machines. Although you can use your existing systems, you might consider looking at newer solutions. This will help you to create new data sets that you can use to support your smart factory initiatives.
FAQ
What does manufacturing industry mean?
Manufacturing Industries are businesses that produce products for sale. Consumers are the people who purchase these products. These companies use various processes such as production, distribution, retailing, management, etc., to fulfill this purpose. They make goods from raw materials with machines and other equipment. This includes all types manufactured goods such as clothing, building materials, furniture, electronics, tools and machinery.
How does a production planner differ from a project manager?
The difference between a product planner and project manager is that a planer is typically the one who organizes and plans the entire project. A production planner, however, is mostly involved in the planning stages.
What are the jobs in logistics?
There are many kinds of jobs available within logistics. Here are some examples:
-
Warehouse workers - They load and unload trucks and pallets.
-
Transport drivers - These are people who drive trucks and trailers to transport goods or perform pick-ups.
-
Freight handlers – They sort and package freight at warehouses.
-
Inventory managers - These are responsible for overseeing the stock of goods in warehouses.
-
Sales reps - They sell products and services to customers.
-
Logistics coordinators: They plan and manage logistics operations.
-
Purchasing agents - They purchase goods and services needed for company operations.
-
Customer service representatives - Answer calls and email from customers.
-
Shipping clerks: They process shipping requests and issue bills.
-
Order fillers are people who fill orders based only on what was ordered.
-
Quality control inspectors - They check incoming and outgoing products for defects.
-
Others - There are many types of jobs in logistics such as transport supervisors and cargo specialists.
What are the 4 types manufacturing?
Manufacturing refers the process of turning raw materials into useful products with machines and processes. Manufacturing involves many activities, including designing, building, testing and packaging, shipping, selling, service, and so on.
What skills are required to be a production manager?
A production planner must be organized, flexible, and able multitask to succeed. Communication skills are essential to ensure that you can communicate effectively with clients, colleagues, and customers.
Statistics
- (2:04) MTO is a production technique wherein products are customized according to customer specifications, and production only starts after an order is received. (oracle.com)
- Job #1 is delivering the ordered product according to specifications: color, size, brand, and quantity. (netsuite.com)
- [54][55] These are the top 50 countries by the total value of manufacturing output in US dollars for its noted year according to World Bank.[56] (en.wikipedia.org)
- According to a Statista study, U.S. businesses spent $1.63 trillion on logistics in 2019, moving goods from origin to end user through various supply chain network segments. (netsuite.com)
- Many factories witnessed a 30% increase in output due to the shift to electric motors. (en.wikipedia.org)
External Links
How To
How to use the Just-In Time Method in Production
Just-in-time is a way to cut costs and increase efficiency in business processes. It's a way to ensure that you get the right resources at just the right time. This means that only what you use is charged to your account. Frederick Taylor, a 1900s foreman, first coined the term. He noticed that workers were often paid overtime when they had to work late. He then concluded that if he could ensure that workers had enough time to do their job before starting to work, this would improve productivity.
JIT is an acronym that means you need to plan ahead so you don’t waste your money. It is important to look at your entire project from beginning to end and ensure that you have enough resources to handle any issues that may arise. If you expect problems to arise, you will be able to provide the necessary equipment and personnel to address them. This way you won't be spending more on things that aren’t really needed.
There are several types of JIT techniques:
-
Demand-driven: This type of JIT allows you to order the parts/materials required for your project on a regular basis. This will let you track the amount of material left over after you've used it. This will let you know how long it will be to produce more.
-
Inventory-based: This type allows you to stock the materials needed for your projects ahead of time. This allows you to forecast how much you will sell.
-
Project-driven : This is a method where you make sure that enough money is set aside to pay the project's cost. Once you have an idea of how much material you will need, you can purchase the necessary materials.
-
Resource-based JIT : This is probably the most popular type of JIT. You assign certain resources based off demand. For instance, if you have a lot of orders coming in, you'll assign more people to handle them. If you don't have many orders, you'll assign fewer people to handle the workload.
-
Cost-based: This is a similar approach to resource-based but you are not only concerned with how many people you have, but also how much each one costs.
-
Price-based: This is very similar to cost-based, except that instead of looking at how much each individual worker costs, you look at the overall price of the company.
-
Material-based - This is a variant of cost-based. But instead of looking at the total company cost, you focus on how much raw material you spend per year.
-
Time-based: Another variation of resource-based JIT. Instead of focusing on the cost of each employee, you will focus on the time it takes to complete a project.
-
Quality-based JIT - This is another form of resource-based JIT. Instead of worrying about the costs of each employee or how long it takes for something to be made, you should think about how quality your product is.
-
Value-based JIT : This is the newest type of JIT. In this scenario, you're not concerned about how products perform or whether customers expect them to meet their expectations. Instead, your goal is to add value to the market.
-
Stock-based: This stock-based method focuses on the actual quantity of products being made at any given time. It's useful when you want maximum production and minimal inventory.
-
Just-in-time (JIT) planning: This is a combination of JIT and supply chain management. It is the process that schedules the delivery of components within a short time of their order. It is essential because it reduces lead-times and increases throughput.