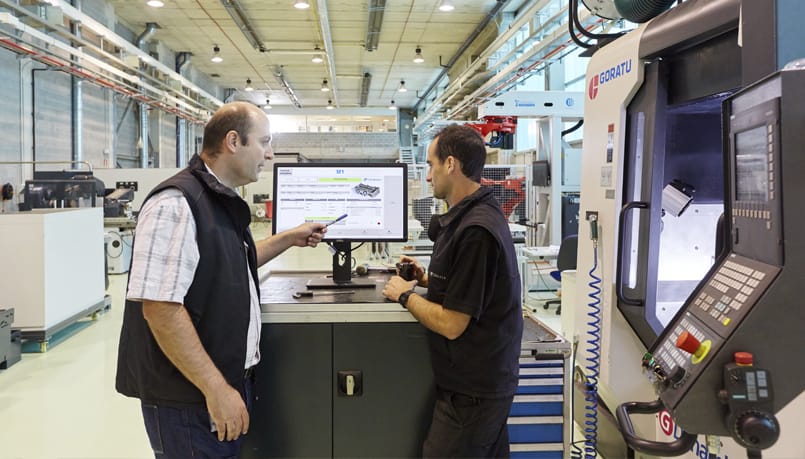
The average engineer salary varies considerably depending on the state you live in. Washington is the most highly paid state in America, followed by New York City and California. When moving to a new country, it is important that you consider the cost per capita. For example, a salary of $96,640 could not cover all of your living expenses. It is crucial to assess your cost of living before applying for a new job.
Electrical engineers earn a median salary of $96,640
According to the U.S. Bureau of Labor Statistics, the average salary for an electrical engineer is $96,640 per year. This amount may vary from one state to the next. There can be significant differences in the salaries paid by different industries. Retail trade is the most lucrative industry for electrical engineers, while education services is the lowest paying. But there are important factors that you should consider when determining the average income of an electrical engineer. Below is an overview of the average salary for different types and levels of electrical engineers.
Electricians are responsible to design and develop electrical equipment. They also supervise the manufacturing and installation of these products. This statistic includes salaries for all types of electrical engineers, but does not include Computer Hardware Engineers, who make computers. According to the Bureau of Labor Statistics this statistic shows that employment of these professionals will increase by 7 percent between 2026 and 2026. The majority of electrical engineers will work in an office environment, but they may also travel for work on the field.
Biomedical engineers make a median income of $89 130
Biomedical engineer combine their engineering knowledge with knowledge about the human body to design medical devices. Their backgrounds in biomechanics help them understand how different medical devices work and interact with the human body. This knowledge can be used for the creation of artificial organs, medical devices and diagnostic tools.
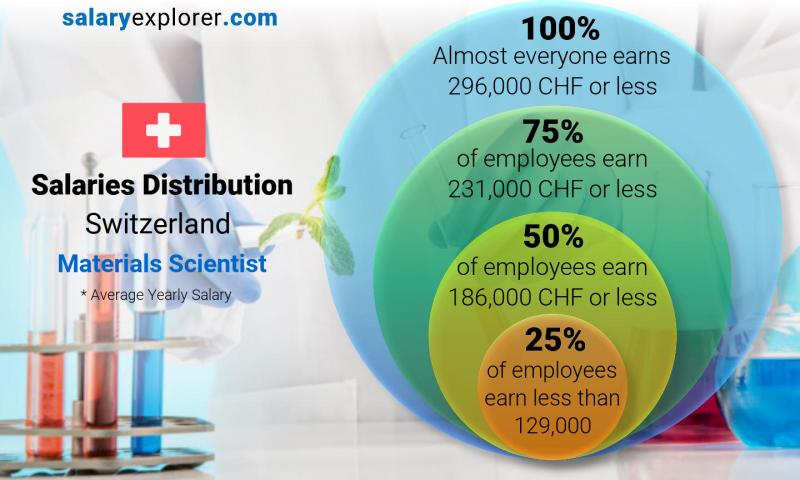
Biomedical engineers need to be able communicate effectively and apply engineering principles to medical procedures. They must present research results, publish scientific papers and collaborate with health care professionals. Additionally, they will need to be proficient at advanced mathematics.
The median salary for mechanical engineers in the United States is $91,352
There are many factors that determine the salary of an engineer in mechanical engineering. Salary levels can vary depending on where you live and what industry you work in. According to ASME's 2017 Salary Survey members, people living in the Northeastern and Southwest earn more. The Midwest earns the most.
The range of salaries for mechanical engineers is $91,352 to $123,028. The average salary is $91,352, and the highest-earning engineers earn more than the median. An average $72,400 is earned by those with less experience than two years. But, those with more experience than two years can earn up to $150,000.
Agronomy engineers make a median income of $89 130
Agricultural engineers work in agricultural settings to help solve problems related to environmental and power supplies. They are also involved in designing and overseeing construction. This occupation requires advanced engineering knowledge and a good understanding of science, including biology and math. Their salaries are comparable to those of similar occupations in the United States. However, they typically earn less than locomotive engineers and naval architects. The outlook is positive for agricultural engineers. The employment rate will increase by 7.4% between 2016-2026.
The median salary for agricultural engineers in the U.S. is $89,130, with the highest-paid individuals earning more than $110,000. The median income for agricultural engineers varies depending on where they live. Santa Clara and San Francisco are the most highly-paid cities for agricultural engineering professionals.
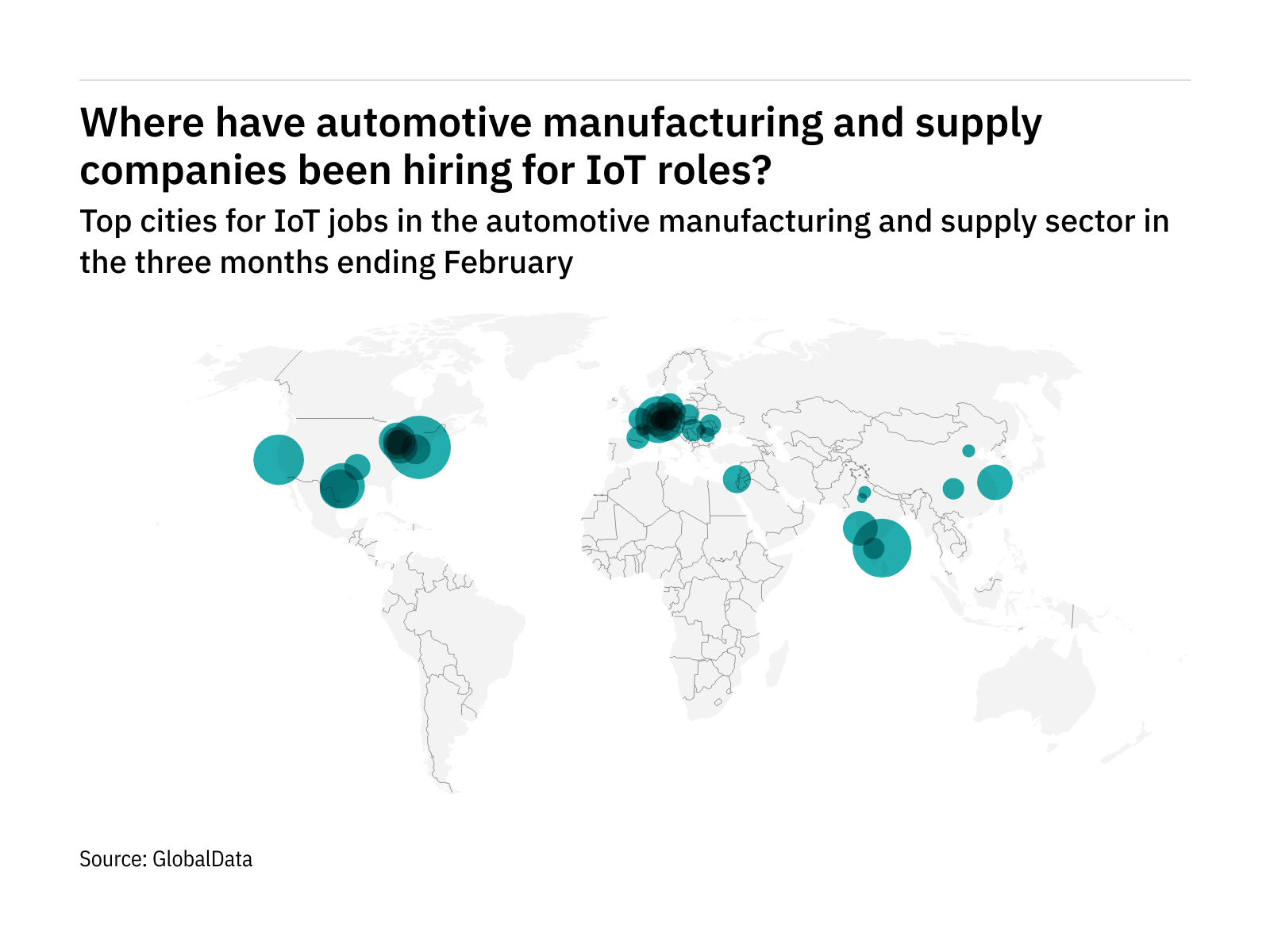
The median salary for environmental engineers is $87,620
Environment engineers are responsible for protecting the environment by finding and implementing ways to reduce negative impacts. They might work in different fields or collaborate with other engineers like urban planners and construction managers. Their training includes biology and chemical, as well data analysis and critical think. They can also help organizations comply to environmental laws.
The environment engineers must be flexible, adaptable and able use new technologies and best-practices. They should also be analytically skilled and able to work in a team. They need to be problem solvers and positive.
FAQ
Can some manufacturing processes be automated?
Yes! Since ancient times, automation has been in existence. The wheel was invented by the Egyptians thousands of years ago. To help us build assembly lines, we now have robots.
In fact, there are several applications of robotics in manufacturing today. These include:
-
Automation line robots
-
Robot welding
-
Robot painting
-
Robotics inspection
-
Robots create products
Automation can be applied to manufacturing in many other ways. For example, 3D printing allows us to make custom products without having to wait for weeks or months to get them manufactured.
What is the role of a logistics manager
Logistics managers are responsible for ensuring that all goods arrive in perfect condition and on time. This is done through his/her expertise and knowledge about the company's product range. He/she also needs to ensure adequate stock to meet demand.
What is the distinction between Production Planning or Scheduling?
Production Planning (PP) is the process of determining what needs to be produced at any given point in time. This is accomplished by forecasting the demand and identifying production resources.
Scheduling refers to the process of allocating specific dates to tasks in order that they can be completed within a specified timeframe.
What are the responsibilities of a manufacturing manager
A manufacturing manager has to ensure that all manufacturing processes work efficiently and effectively. They must also be alert to any potential problems and take appropriate action.
They should also learn how to communicate effectively with other departments, including sales and marketing.
They should be up to date on the latest trends and be able apply this knowledge to increase productivity and efficiency.
What are the 7 Rs of logistics management?
The acronym 7Rs of Logistics refers to the seven core principles of logistics management. It was developed and published by the International Association of Business Logisticians in 2004 as part of the "Seven Principles of Logistics Management".
The acronym is composed of the following letters.
-
Responsive - ensure all actions are legal and not harmful to others.
-
Reliable - You can have confidence that you will fulfill your promises.
-
Reasonable - use resources efficiently and don't waste them.
-
Realistic – consider all aspects of operations, from cost-effectiveness to environmental impact.
-
Respectful – Treat others fairly and equitably.
-
Responsive - Look for ways to save time and increase productivity.
-
Recognizable - Provide value-added services to customers
What do you mean by warehouse?
A warehouse is a place where goods are stored until they are sold. It can be an indoor space or an outdoor area. It may also be an indoor space or an outdoor area.
How can we reduce manufacturing overproduction?
In order to reduce excess production, you need to develop better inventory management methods. This would reduce time spent on activities such as purchasing, stocking, and maintaining excess stock. This will allow us to free up resources for more productive tasks.
You can do this by adopting a Kanban method. A Kanban board, a visual display to show the progress of work, is called a Kanban board. In a Kanban system, work items move through a sequence of states until they reach their final destination. Each state is assigned a different priority.
If work is moving from one stage to the other, then the current task can be completed and moved on to the next. A task that is still in the initial stages of a process will be considered complete until it moves on to the next stage.
This allows work to move forward and ensures that no work is missed. Managers can monitor the work being done by Kanban boards to see what is happening at any given time. This information allows them to adjust their workflow based on real-time data.
Lean manufacturing is another option to control inventory levels. Lean manufacturing works to eliminate waste throughout every stage of the production chain. Anything that does nothing to add value to a product is waste. These are some of the most common types.
-
Overproduction
-
Inventory
-
Unnecessary packaging
-
Materials in excess
Manufacturers can reduce their costs and improve their efficiency by using these ideas.
Statistics
- According to the United Nations Industrial Development Organization (UNIDO), China is the top manufacturer worldwide by 2019 output, producing 28.7% of the total global manufacturing output, followed by the United States, Japan, Germany, and India.[52][53] (en.wikipedia.org)
- [54][55] These are the top 50 countries by the total value of manufacturing output in US dollars for its noted year according to World Bank.[56] (en.wikipedia.org)
- In the United States, for example, manufacturing makes up 15% of the economic output. (twi-global.com)
- It's estimated that 10.8% of the U.S. GDP in 2020 was contributed to manufacturing. (investopedia.com)
- According to a Statista study, U.S. businesses spent $1.63 trillion on logistics in 2019, moving goods from origin to end user through various supply chain network segments. (netsuite.com)
External Links
How To
How to Use Six Sigma in Manufacturing
Six Sigma can be described as "the use of statistical process control (SPC), techniques to achieve continuous improvement." Motorola's Quality Improvement Department created Six Sigma at their Tokyo plant, Japan in 1986. The basic idea behind Six Sigma is to improve quality by improving processes through standardization and eliminating defects. Many companies have adopted this method in recent years. They believe there is no such thing a perfect product or service. Six Sigma's main objective is to reduce variations from the production average. If you take a sample and compare it with the average, you will be able to determine how much of the production process is different from the norm. If it is too large, it means that there are problems.
Understanding the nature of variability in your business is the first step to Six Sigma. Once you understand this, you can then identify the causes of variation. It is important to identify whether the variations are random or systemic. Random variations happen when people make errors; systematic variations are caused externally. Random variations would include, for example, the failure of some widgets to fall from the assembly line. But if you notice that every widget you make falls apart at the exact same place each time, this would indicate that there is a problem.
Once you've identified the problem areas you need to find solutions. The solution could involve changing how you do things, or redesigning your entire process. Test them again once you've implemented the changes. If they don’t work, you’ll need to go back and rework the plan.