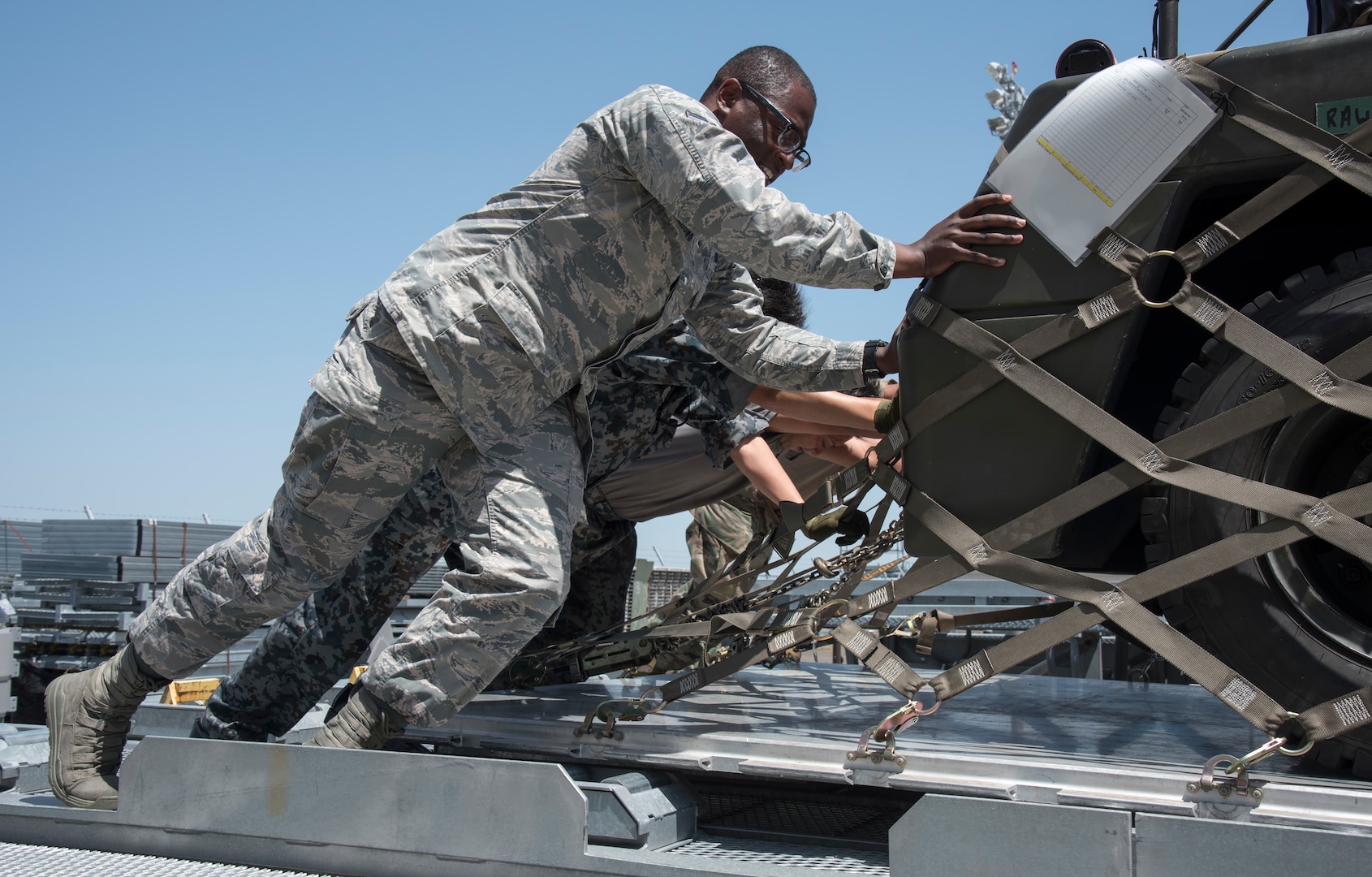
In advanced manufacturing, companies employ innovative technologies to make better products. These technologies are known as advanced, cutting-edge and innovative. These technologies are being integrated into more companies' operations. Robotics, material deposition, additive manufacturing are just a few of the technologies. These technologies are available for more information.
Additive manufacturing
Many businesses see additive manufacturing as the future of manufacturing. This type of manufacturing involves the use of additive manufacturing technologies, also known as 3D printing. This type of manufacturing offers several benefits, such as increased flexibility and reduced inventory costs. It also reduces the need to import labor-intensive components and parts.
Technology advancements in additive manufacture have dramatically increased the speed and flexibility that manufacturing can be done. Businesses can respond quickly to supply-chain disruptions thanks to them. They can even make custom parts in minutes or days. This process is especially valuable in industries that experience supply-chain problems. Advanced manufacturing can even produce parts with complex geometries.
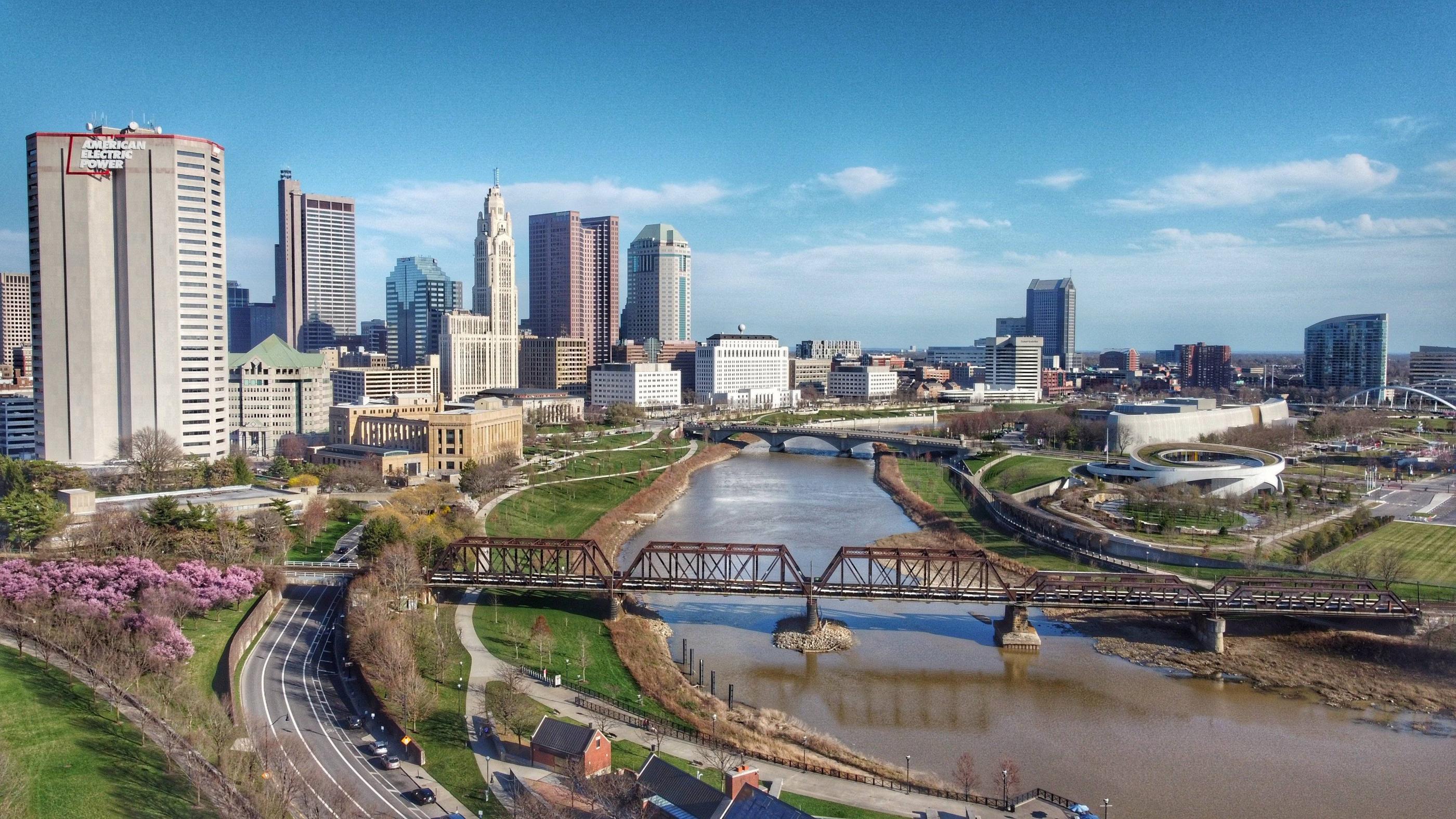
Manufacturers can also produce very small quantities. You can use additive manufacturing to make custom dental appliances. It also makes it possible to manufacture complex structures, like internal heat pipes. Advanced manufacturing through additive manufacturing helps reduce the inventory requirements and makes it possible to produce specialized components. It can reduce materials costs by ninety-five percent and energy consumption by half.
Robotics
Many industrial producers recognize the potential of advanced robotics and plan to implement them within their plants. However, they are not satisfied with their current progress in implementation and performance. Many of them point out the limitations and high cost of current technology as barriers that prevent wider deployment. They also lack key enablers to fully deploy advanced robotics in their factories.
Advanced robotics integration requires that manufacturers evaluate their system architecture. These systems should include infrastructure and analytics as well as data and workflow management. When these capabilities are in place companies can begin to look for strategic robotics partners. These partners will be able to help the company choose which processes and technologies are most suitable for their business. In the case of robotics, this can be accomplished with the use of simulation models.
There are many industries that are using advanced robotics. Robotic automation has been applied to a wide range of areas including automotive, medical, aerospace and automotive manufacturing. This technology has made manufacturing more efficient. Aside from reducing labor costs, advanced robotic automaton also saves electricity by working 24 hours a week and does not require lighting.
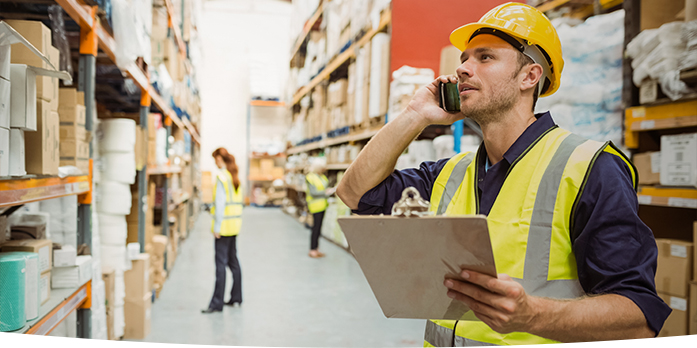
Material deposition
Material deposition is an important technique in advanced manufacturing. This involves the use of both arc plasma energy sources and laser beam to deposit thin film of a substance on a target. A substrate is usually made up of wire or powder. The deposition takes place in an inert or vacuum. Other energy sources may also be used.
Plasma metal deposition is one of the most promising direct energy deposition techniques. It uses a plasma source for metals to be deposited. The process can be used with wire, powder, and both as a feedstock. It can also produce large, complex components. This process offers a lower machining time and shorter lead times.
This process can also be used to create ceramics, polymers and metals. Metals are typically used in wire and powder forms.
FAQ
What is production plan?
Production planning is the process of creating a plan that covers all aspects of production. This includes scheduling, budgeting and crew, location, equipment, props, and more. This document ensures that everything is prepared and available when you are ready for shooting. You should also have information to ensure the best possible results on set. This includes location information, crew details, equipment specifications, and casting lists.
The first step in filming is to define what you want. You might have an idea of where you want to film, or you may have specific locations or sets in mind. Once you have identified the scenes and locations, you can start to determine which elements are required for each scene. Perhaps you have decided that you need to buy a car but aren't sure which model. This is where you can look up car models online and narrow down your options by choosing from different makes and models.
Once you have found the right car, you can start thinking about extras. Do you need people sitting in the front seats? You might also need someone to help you get around the back. Maybe you'd like to change the interior from black to a white color. These questions will help guide you in determining the ideal look and feel for your car. The type of shots that you are looking for is another thing to consider. Do you want to film close-ups, or wider angles? Maybe you want to show your engine or the steering wheel. These details will help identify the exact car you wish to film.
Once you've determined the above, it is time to start creating a calendar. The schedule will show you when to begin shooting and when to stop. The schedule will show you when to get there, what time to leave, and when to return home. Everyone knows exactly what they should do and when. If you need to hire extra staff, you can make sure you book them in advance. You should not hire anyone who doesn't show up because of your inaction.
When creating your schedule, you will also need to consider the number of days you need to film. Some projects are quick and easy, while others take weeks. When you are creating your schedule, you should always keep in mind whether you need more than one shot per day or not. Multiplying takes in the same area will result both in increased costs and a longer time. If you aren't sure whether you need multiple shots, it is best to take fewer photos than you would like.
Budgeting is another important aspect of production planning. You will be able to manage your resources if you have a realistic budget. It is possible to reduce the budget at any time if you experience unexpected problems. You shouldn't underestimate the amount you'll spend. You will end up spending less money if you underestimate the cost of something.
Planning production is a tedious process. Once you have a good understanding of how everything works together, planning future projects becomes easy.
What skills should a production planner have?
A production planner must be organized, flexible, and able multitask to succeed. Also, you must be able and willing to communicate with clients and coworkers.
What is the difference between Production Planning, Scheduling and Production Planning?
Production Planning (PP), or production planning, is the process by which you determine what products are needed at any given time. This is done through forecasting demand and identifying production capacities.
Scheduling refers to the process of allocating specific dates to tasks in order that they can be completed within a specified timeframe.
How can efficiency in manufacturing be improved?
First, identify the factors that affect production time. Next, we must find ways to improve those factors. You can start by identifying the most important factors that impact production time. Once you've identified them, try to find solutions for each of those factors.
What are the products and services of logistics?
Logistics involves the transportation of goods from point A and point B.
These include all aspects related to transport such as packaging, loading and transporting, storing, transporting, unloading and warehousing inventory management, customer service. Distribution, returns, recycling are some of the options.
Logisticians ensure that the product is delivered to the correct place, at the right time, and under safe conditions. They help companies manage their supply chain efficiency by providing information on demand forecasts, stock levels, production schedules, and availability of raw materials.
They coordinate with vendors and suppliers, keep track of shipments, monitor quality standards and perform inventory and order replenishment.
Statistics
- In the United States, for example, manufacturing makes up 15% of the economic output. (twi-global.com)
- According to a Statista study, U.S. businesses spent $1.63 trillion on logistics in 2019, moving goods from origin to end user through various supply chain network segments. (netsuite.com)
- It's estimated that 10.8% of the U.S. GDP in 2020 was contributed to manufacturing. (investopedia.com)
- In 2021, an estimated 12.1 million Americans work in the manufacturing sector.6 (investopedia.com)
- Job #1 is delivering the ordered product according to specifications: color, size, brand, and quantity. (netsuite.com)
External Links
How To
Six Sigma and Manufacturing
Six Sigma is defined as "the application of statistical process control (SPC) techniques to achieve continuous improvement." Motorola's Quality Improvement Department developed it at their Tokyo plant in Japan in 1986. Six Sigma's main goal is to improve process quality by standardizing processes and eliminating defects. Many companies have adopted Six Sigma in recent years because they believe that there are no perfect products and services. Six Sigma seeks to reduce variation between the mean production value. You can calculate the percentage of deviation from the norm by taking a sample of your product and comparing it to the average. If this deviation is too big, you know something needs fixing.
Understanding the nature of variability in your business is the first step to Six Sigma. Once you have a good understanding of the basics, you can identify potential sources of variation. It is important to identify whether the variations are random or systemic. Random variations happen when people make errors; systematic variations are caused externally. For example, if you're making widgets, and some of them fall off the assembly line, those would be considered random variations. You might notice that your widgets always fall apart at the same place every time you put them together.
Once you've identified where the problems lie, you'll want to design solutions to eliminate those problems. It might mean changing the way you do business or redesigning it entirely. To verify that the changes have worked, you need to test them again. If they don't work you need to rework them and come up a better plan.