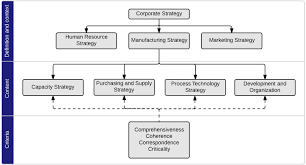
Denver is a city in Colorado that offers a wide variety of jobs. It is home to many logistics companies, which provide a wide range of logistic services. Some of these services include freight-forwarding, trucking, logistics and supply chain consultancy, as well.
You can choose from a variety of jobs in the logistics sector, such as dispatch manager, warehouse associate, and transportation director. All these positions are in charge of making sure the logistics within an organization run smoothly.
Dispatch Manager
A dispatch manager coordinates and directs the activities of an entire team in a warehouse, call center or other workplace. This includes training new employees, delegating tasks, coordinating the workload of other team members, documenting productivity, and overseeing incoming and outgoing shipments. Dispatch managers typically have a bachelor’s degree in business administration or logistics, and they are familiar with the organization of workflow.
Transportation Director
A transportation director oversees the logistics of an organization, department in government, or school. This includes planning distribution routes as well as arranging transportation such a buses or trucks for products to be transported from one point to another.
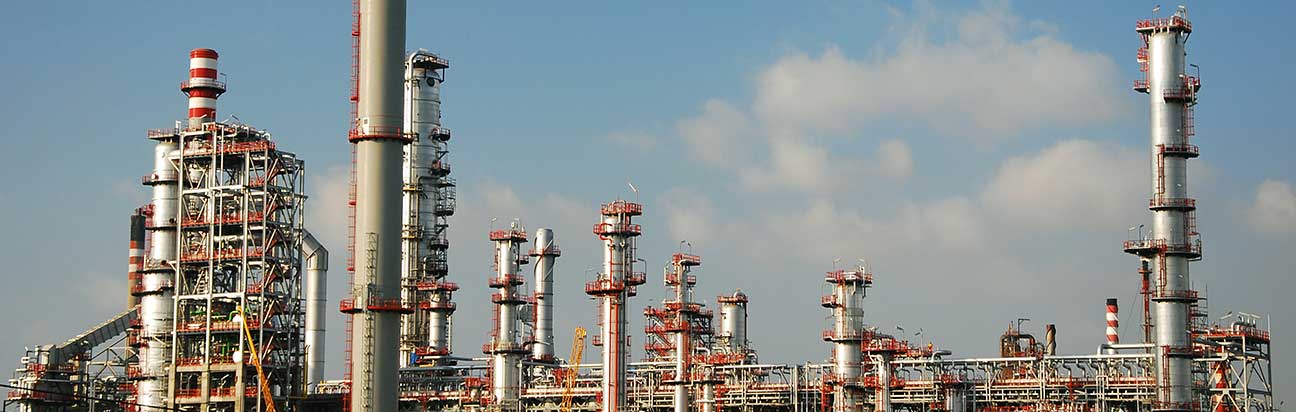
This career is best suited for those looking to join a larger organization or government. It is a very competitive job, so you should have excellent organizational skills and be willing to work long hours.
Warehouse Associate
If you're searching for a career that doesn't require as much competition, but has a more flexible work schedule, a warehouse employee may be a great option. A warehouse associate typically handles smaller projects such as picking shipments, packing products, and moving merchandise to other locations.
The best way to start your search for a job in the logistics industry is to set up a profile on Monster. It will enable you to receive notifications about the latest logistics jobs in your locality.
You will also be able receive expert advice on how to maximize your job application and how to negotiate your wage, among other things.
Logistics Manager
If you want to become a logistics manager, you should have at least a bachelor's degree in supply chain management or business administration. A minimum of one year's experience working in a warehouse is required, as are strong organizational skills. To become a senior logistic manager, you can earn a Master's Degree in Supply Chain Management or another field related.
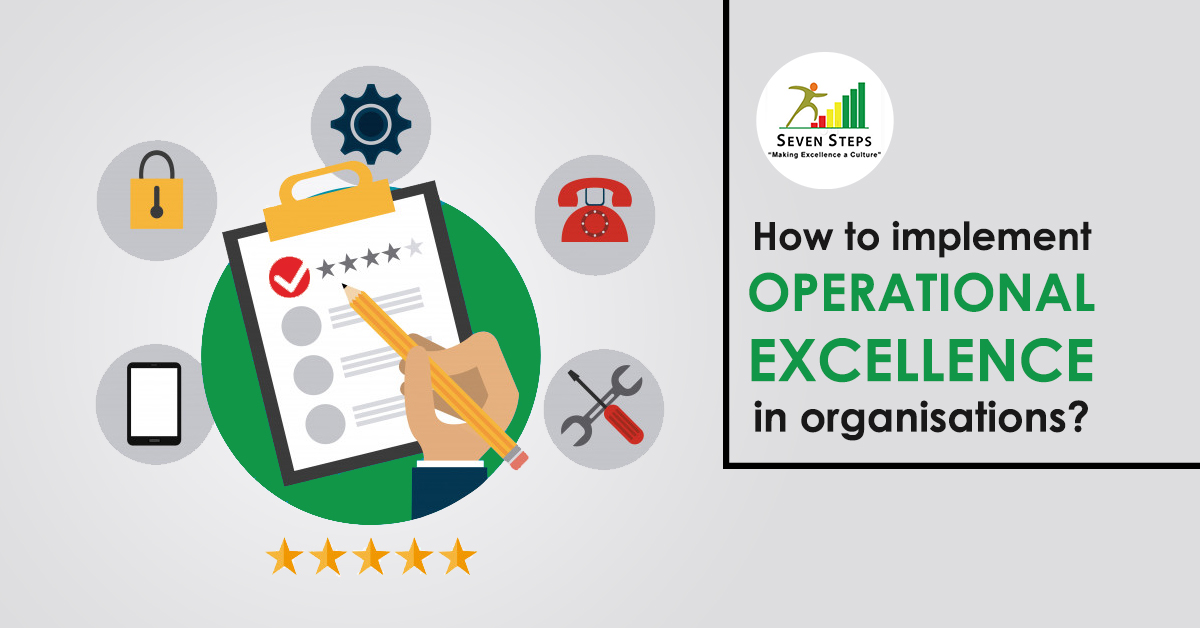
Logistik Analyst
A logistician monitors and changes the logistics within a business to better help them achieve their goals. This includes evaluating inventory levels, scheduling delivery times, and determining budget constraints. A logistics analysts must possess a bachelor’s degree, either in business or in engineering. He/she should also have some experience working with the logistics within a certain industry.
The logistics sector is expanding and offers many opportunities. Set up your free Monster account today if you're ready to begin a career. You will have a better chance to find the perfect logistics job.
FAQ
What does manufacturing industry mean?
Manufacturing Industries is a group of businesses that produce goods for sale. Consumers are the people who purchase these products. These companies use various processes such as production, distribution, retailing, management, etc., to fulfill this purpose. They manufacture goods from raw materials using machines and other equipment. This includes all types manufactured goods such as clothing, building materials, furniture, electronics, tools and machinery.
How can manufacturing efficiency improved?
First, determine which factors have the greatest impact on production time. Next, we must find ways to improve those factors. If you don't know where to start, then think about which factor(s) have the biggest impact on production time. Once you have identified them, it is time to identify solutions.
Can certain manufacturing steps be automated?
Yes! Yes. The Egyptians created the wheel thousands years ago. To help us build assembly lines, we now have robots.
In fact, there are several applications of robotics in manufacturing today. These include:
-
Automated assembly line robots
-
Robot welding
-
Robot painting
-
Robotics inspection
-
Robots that create products
Automation could also be used to improve manufacturing. 3D printing makes it possible to produce custom products in a matter of days or weeks.
What skills should a production planner have?
A production planner must be organized, flexible, and able multitask to succeed. Communication skills are essential to ensure that you can communicate effectively with clients, colleagues, and customers.
How does a Production Planner differ from a Project Manager?
The primary difference between a producer planner and a manager of a project is that the manager usually plans and organizes the whole project, while a production planner is only involved in the planning stage.
What type of jobs is there in logistics
There are many types of jobs in logistics. Some of them are:
-
Warehouse workers - They load and unload trucks and pallets.
-
Transportation drivers – They drive trucks or trailers to transport goods and perform pick-ups.
-
Freight handlers: They sort and package freight in warehouses.
-
Inventory managers: They are responsible for the inventory and management of warehouses.
-
Sales representatives - They sell products to customers.
-
Logistics coordinators: They plan and manage logistics operations.
-
Purchasing agents are those who purchase goods and services for the company.
-
Customer service agents - They answer phone calls and respond to emails.
-
Shipping clerks: They process shipping requests and issue bills.
-
Order fillers are people who fill orders based only on what was ordered.
-
Quality control inspectors (QCI) - They inspect all incoming and departing products for potential defects.
-
Others - There are many other types of jobs available in logistics, such as transportation supervisors, cargo specialists, etc.
What is the job of a logistics manger?
Logistics managers ensure that goods arrive on time and are unharmed. This is done through his/her expertise and knowledge about the company's product range. He/she should ensure that sufficient stock is available in order to meet customer demand.
Statistics
- You can multiply the result by 100 to get the total percent of monthly overhead. (investopedia.com)
- [54][55] These are the top 50 countries by the total value of manufacturing output in US dollars for its noted year according to World Bank.[56] (en.wikipedia.org)
- In 2021, an estimated 12.1 million Americans work in the manufacturing sector.6 (investopedia.com)
- (2:04) MTO is a production technique wherein products are customized according to customer specifications, and production only starts after an order is received. (oracle.com)
- In the United States, for example, manufacturing makes up 15% of the economic output. (twi-global.com)
External Links
How To
How to Use Lean Manufacturing for the Production of Goods
Lean manufacturing is an approach to management that aims for efficiency and waste reduction. It was developed by Taiichi Okono in Japan, during the 1970s & 1980s. TPS founder Kanji Takoda awarded him the Toyota Production System Award (TPS). Michael L. Watkins published the book "The Machine That Changed the World", which was the first to be published about lean manufacturing.
Lean manufacturing is often described as a set if principles that help improve the quality and speed of products and services. It emphasizes the elimination of defects and waste throughout the value stream. Just-in-time (JIT), zero defect (TPM), and 5S are all examples of lean manufacturing. Lean manufacturing eliminates non-value-added tasks like inspection, rework, waiting.
Lean manufacturing is a way for companies to achieve their goals faster, improve product quality, and lower costs. Lean manufacturing is a great way to manage the entire value chain including customers, suppliers, distributors and retailers as well as employees. Lean manufacturing is widely used in many industries. Toyota's philosophy is the foundation of its success in automotives, electronics and appliances, healthcare, chemical engineers, aerospace, paper and food, among other industries.
Five basic principles of Lean Manufacturing are included in lean manufacturing
-
Define Value: Identify the social value of your business and what sets you apart.
-
Reduce Waste – Eliminate all activities that don't add value throughout the supply chain.
-
Create Flow: Ensure that the work process flows without interruptions.
-
Standardize and simplify - Make your processes as consistent as possible.
-
Building Relationships – Establish personal relationships with both external and internal stakeholders.
Lean manufacturing, although not new, has seen renewed interest in the economic sector since 2008. Many businesses have adopted lean production techniques to make them more competitive. In fact, some economists believe that lean manufacturing will be an important factor in economic recovery.
Lean manufacturing has many benefits in the automotive sector. These include better customer satisfaction and lower inventory levels. They also result in lower operating costs.
It can be applied to any aspect of an organisation. This is because it ensures efficiency and effectiveness in all stages of the value chain.
There are three main types:
-
Just-in-Time Manufacturing (JIT): This type of lean manufacturing is commonly referred to as "pull systems." JIT stands for a system where components are assembled on the spot rather than being made in advance. This approach reduces lead time, increases availability and reduces inventory.
-
Zero Defects Manufacturing - ZDM: ZDM focuses its efforts on making sure that no defective units leave a manufacturing facility. It is better to repair a part than have it removed from the production line if it needs to be fixed. This is also true for finished products that require minor repairs before shipping.
-
Continuous Improvement (CI),: Continuous improvement aims improve the efficiency and effectiveness of operations by continuously identifying issues and making changes to reduce waste. Continuous Improvement involves continuous improvement of processes.