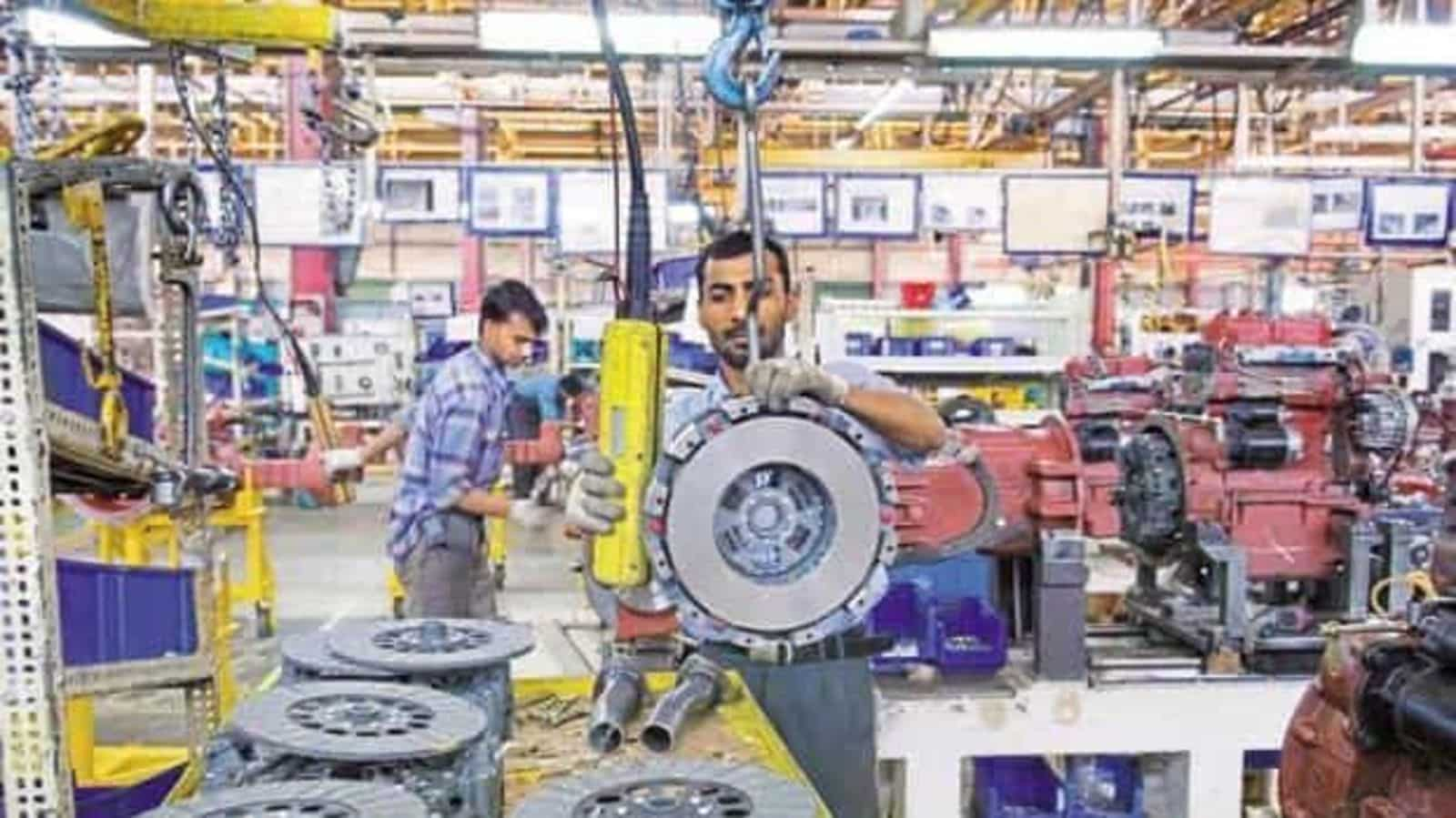
Opportunities in the manufacturing of wind turbines
There are many tasks required to manufacture wind turbines. These jobs include tower assembly, blade epoxies and gears. Some wind turbine manufacturing businesses also use third-party vendors to manufacture components. Wind turbine components are large and need to be transported quickly and efficiently. Teams of logisticians or rail freight drivers are needed by companies to complete this task.
For jobs in wind turbine production, a bachelor's is required. However, there are some cases that require masters degrees. Most jobs in the wind turbine industry require engineering or environmental engineering concentrations. In addition to a degree, entry-level engineers must have advanced computer skills and experience. They usually work with more experienced employees to ensure quality control and accuracy. They might also be responsible for more complicated projects.
Wind turbine manufacturing processes
The blades are the main component of a windturbine. Each blade is made up of two faces joined by integral shearwebs. The blades have a box spar and shell fairings to support them. These structures are strong enough to withstand edgewise and flipwise loads. The spar resists the edgewise bending caused by wind pressure and gravitational forces. These forces are not able to be absorbed by the blades.
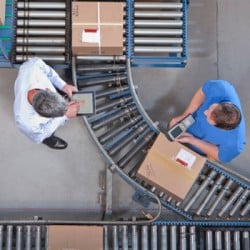
A variety of materials are used to create the blades. For commercial wind turbine blades, fiberglass is the most widely used material. However, aluminum and lightweight woodens can also be used. The blades will then be wrapped in foil, and connected to tubes with resin pumps.
Competitors in the wind turbine manufacturing industry
While Chinese turbine manufacturers are becoming a more prominent player in the global wind industry's overall structure, they still have a long way to go before they become the dominant force. Chinese turbine makers have had difficulty dethroning established manufacturers in developed market markets. Despite this, they may be poised to eventually increase their overseas activities if they invest in local manufacturing capabilities.
While turbine makers increasingly outsource parts, many choose to build them themselves. This has both its advantages and disadvantages. Vestas, a Colorado-based company that manufactures wind turbines towers for US third-party projects, has adopted this strategy. The agreement allows the tower facility to use up to 25 percent its production capacity and creates 100 local jobs. The downside to this approach is the weak quality control. Some components from offshore suppliers have had problems in the past. These include gearbox failures, blade cracking, and gearbox failures. Many offshore foundations are even made from poor quality steel.
Manufacturing wind turbines poses health and safety risks
Safety and health are two of the most critical issues in manufacturing wind turbines. Workers are often exposed to a number of hazards that could lead to long-term damage or even fatalities. Fortunately, there are ways to reduce the risk, including proper training and routine inspections. Here are some tips that will keep employees safe in a wind turbine manufacturing plant.
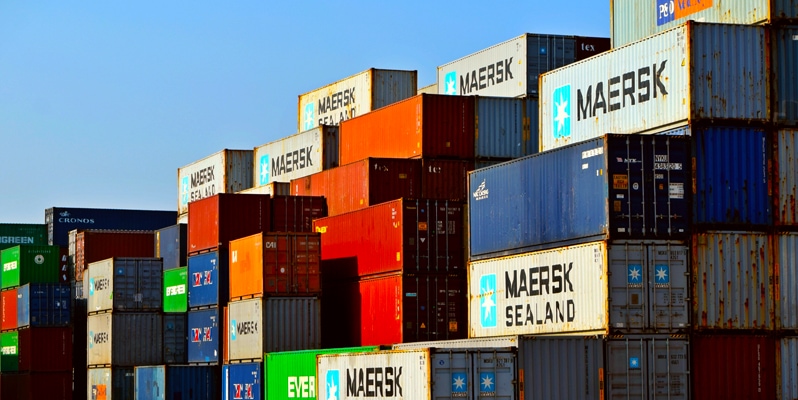
One of the most common hazards in wind turbine blade manufacturing is the exposure to harmful gases, vapors, and dust. Workers must use respirators to reduce their exposure and are trained to use them. This is possible only with proper training. Ear protection is also a critical factor.
FAQ
How can we reduce manufacturing overproduction?
Improved inventory management is the key to reducing overproduction. This would reduce the time needed to manage inventory. This could help us free up our time for other productive tasks.
This can be done by using a Kanban system. A Kanban board is a visual display used to track work in progress. In a Kanban system, work items move through a sequence of states until they reach their final destination. Each state represents a different priority level.
For instance, when work moves from one stage to another, the current task is complete enough to be moved to the next stage. However, if a task is still at the beginning stages, it will remain so until it reaches the end of the process.
This allows work to move forward and ensures that no work is missed. With a Kanban board, managers can see exactly how much work is being done at any given moment. This data allows them adjust their workflow based upon real-time data.
Lean manufacturing can also be used to reduce inventory levels. Lean manufacturing emphasizes eliminating waste in all phases of production. Anything that does not contribute to the product's value is considered waste. The following are examples of common waste types:
-
Overproduction
-
Inventory
-
Unnecessary packaging
-
Excess materials
By implementing these ideas, manufacturers can improve efficiency and cut costs.
What is the distinction between Production Planning or Scheduling?
Production Planning (PP), also known as forecasting and identifying production capacities, is the process that determines what product needs to be produced at any particular time. This is accomplished by forecasting the demand and identifying production resources.
Scheduling is the process of assigning specific dates to tasks so they can be completed within the specified timeframe.
Is automation important in manufacturing?
Automating is not just important for manufacturers, but also for service providers. Automation allows them to deliver services quicker and more efficiently. In addition, it helps them reduce costs by reducing human errors and improving productivity.
What is the job of a logistics manger?
A logistics manager makes sure that all goods are delivered on-time and in good condition. This is done using his/her knowledge of the company's products. He/she also needs to ensure adequate stock to meet demand.
Statistics
- In 2021, an estimated 12.1 million Americans work in the manufacturing sector.6 (investopedia.com)
- (2:04) MTO is a production technique wherein products are customized according to customer specifications, and production only starts after an order is received. (oracle.com)
- According to a Statista study, U.S. businesses spent $1.63 trillion on logistics in 2019, moving goods from origin to end user through various supply chain network segments. (netsuite.com)
- You can multiply the result by 100 to get the total percent of monthly overhead. (investopedia.com)
- [54][55] These are the top 50 countries by the total value of manufacturing output in US dollars for its noted year according to World Bank.[56] (en.wikipedia.org)
External Links
How To
How to use Lean Manufacturing in the production of goods
Lean manufacturing refers to a method of managing that seeks to improve efficiency and decrease waste. It was developed by Taiichi Okono in Japan, during the 1970s & 1980s. TPS founder Kanji Takoda awarded him the Toyota Production System Award (TPS). The first book published on lean manufacturing was titled "The Machine That Changed the World" written by Michael L. Watkins and published in 1990.
Lean manufacturing, often described as a set and practice of principles, is aimed at improving the quality, speed, cost, and efficiency of products, services, and other activities. It emphasizes the elimination and minimization of waste in the value stream. The five-steps of Lean Manufacturing are just-in time (JIT), zero defect and total productive maintenance (TPM), as well as 5S. Lean manufacturing focuses on eliminating non-value-added activities such as rework, inspection, and waiting.
Lean manufacturing not only improves product quality but also reduces costs. Companies can also achieve their goals faster by reducing employee turnover. Lean manufacturing has been deemed one of the best ways to manage the entire value-chain, including customers, distributors as well retailers and employees. Many industries worldwide use lean manufacturing. Toyota's philosophy has been a key driver of success in many industries, including automobiles and electronics.
Five basic principles of Lean Manufacturing are included in lean manufacturing
-
Define Value - Determine the value that your business brings to society. Also, identify what sets you apart from your competitors.
-
Reduce Waste – Eliminate all activities that don't add value throughout the supply chain.
-
Create Flow - Ensure work moves smoothly through the process without interruption.
-
Standardize & Simplify - Make processes as consistent and repeatable as possible.
-
Build relationships - Develop and maintain personal relationships with both your internal and external stakeholders.
Lean manufacturing isn’t new, but it has seen a renewed interest since 2008 due to the global financial crisis. Many businesses are now using lean manufacturing to improve their competitiveness. According to some economists, lean manufacturing could be a significant factor in the economic recovery.
Lean manufacturing is now becoming a common practice in the automotive industry, with many benefits. These include higher customer satisfaction levels, reduced inventory levels as well as lower operating costs.
You can apply Lean Manufacturing to virtually any aspect of your organization. Because it makes sure that all value chains are efficient and effectively managed, Lean Manufacturing is particularly helpful for organizations.
There are three types principally of lean manufacturing:
-
Just-in Time Manufacturing: This lean manufacturing method is commonly called "pull systems." JIT means that components are assembled at the time of use and not manufactured in advance. This approach reduces lead time, increases availability and reduces inventory.
-
Zero Defects Manufacturing: ZDM ensures that no defective units leave the manufacturing plant. Repairing a part that is damaged during assembly should be done, not scrapping. This applies to finished goods that may require minor repairs before shipment.
-
Continuous Improvement (CI): CI aims to improve the efficiency of operations by continuously identifying problems and making changes in order to eliminate or minimize waste. It involves continuous improvement of processes, people, and tools.