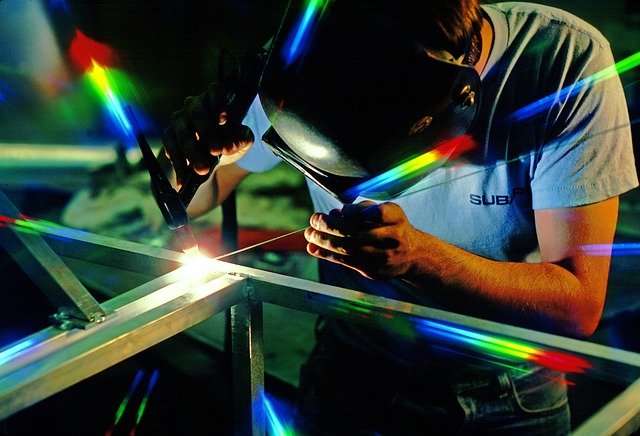
You will study microscopic forms and life processes as a microbiologist. This includes studying the interactions of organisms and how they interact with each others. There are four types of microscopic organisms that you'll be studying: bacteria, algae, mushrooms, and parasites. Microbiologists are important because microbiologists study the life forms that make up everything we eat and drink.
Education necessary
Microbiologists study microscopic processes and life forms. These microorganisms could include bacteria, yeast, parasites and algae. Microbiologists not only study how microscopic organisms function, but also how they interact.
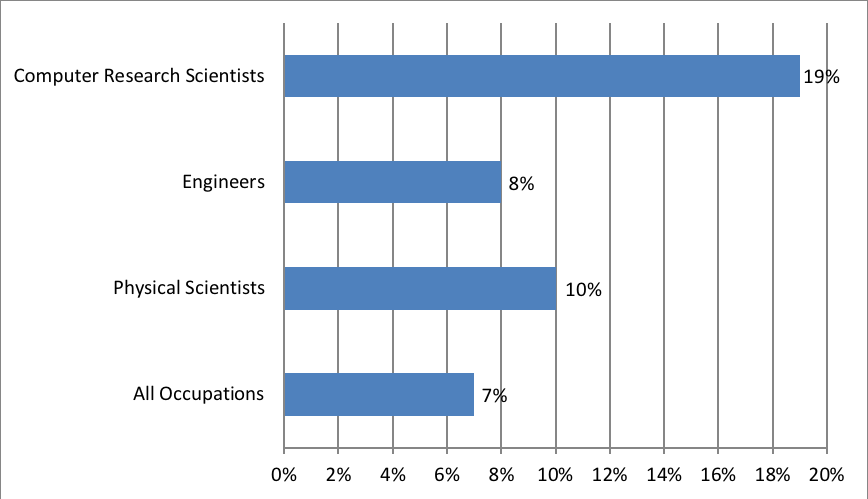
Microbiologists must be detail-oriented and able present their research findings. They should also be able manage and motivate a team. Because they often need to use complex math equations to calculate results it is important that they have a solid math background.
Your job duties
Microbiologists are responsible for identifying and tracking microorganisms across a variety of environments. This work is also useful in the development of new medicines, vaccines, or ways to prevent disease. They are responsible for overseeing lab work and conducting research. They use advanced microscopes and specialist software to analyze and collect data. They are required to pay close attention to details, and must be able coordinate large research teams.
Microbiologists study microbes, and they use many analytical techniques to do so. Their work can be in a clinical laboratory or in an environmental setting. Environmental microbiologists examine the interaction between microorganisms within soil and water. Industrial microbiologists examine how microbes affect crop growth and the efficiency of industrial processes. They may be responsible for monitoring microbial activity in cheese production lines or studying microbial growth inside pipes.
Salary
In 2004, the average salary for a Microbiologist was $81,668 annually. That figure is expected rise to $121,130 by 2021. Microbiologists might choose to do research, but also to be a part of scientific publishing, pharmaceutical sales, or patent work. There is a constant increase in demand for microbiologists in America, which has led to an increase in job opportunities in this field.
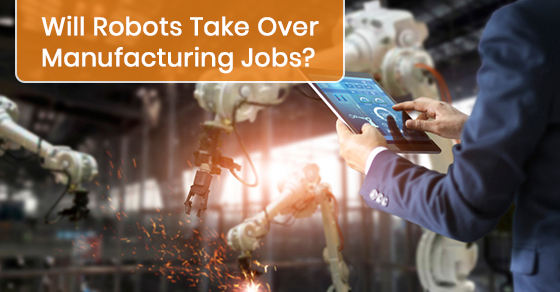
Microbiologists often work in research labs or industrial environments. They often work with potentially dangerous organisms and must adhere to strict safety protocols. Others make field visits to workplaces or work environments to collect samples. Sometimes, they may travel.
FAQ
What does warehouse refer to?
A warehouse or storage facility is where goods are stored before they are sold. It can be either an indoor or outdoor space. It may also be an indoor space or an outdoor area.
What is the difference between Production Planning and Scheduling?
Production Planning (PP), is the process of deciding what production needs to take place at any given time. This is accomplished by forecasting the demand and identifying production resources.
Scheduling refers to the process of allocating specific dates to tasks in order that they can be completed within a specified timeframe.
What are the products of logistics?
Logistics is the process of moving goods from one point to another.
They encompass all aspects transport, including packaging and loading, transporting, storage, unloading.
Logisticians ensure the product reaches its destination in the most efficient manner. They help companies manage their supply chain efficiency by providing information on demand forecasts, stock levels, production schedules, and availability of raw materials.
They can also track shipments in transit and monitor quality standards.
What is production planning?
Production Planning involves developing a plan for all aspects of the production, including scheduling, budgeting, casting, crew, location, equipment, props, etc. This document aims to ensure that everything is planned and ready when you are ready to shoot. You should also have information to ensure the best possible results on set. This includes information on shooting times, locations, cast lists and crew details.
The first step is to decide what you want. You may already know where you want the film to be shot, or perhaps you have specific locations and sets you wish to use. Once you have determined your scenes and locations, it is time to start figuring out the elements that you will need for each scene. For example, you might decide that you need a car but don't know exactly what model you want. If this is the case, you might start searching online for car models and then narrow your options by selecting from different makes.
Once you have found the right car, you can start thinking about extras. Do you have people who need to be seated in the front seat? Perhaps you have someone who needs to be able to walk around the back of your car. Perhaps you would like to change the interior colour from black to white. These questions can help you decide the right look for your car. You can also think about the type of shots you want to get. You will be filming close-ups and wide angles. Perhaps you want to show the engine or the steering wheel? This will allow you to determine the type of car you want.
Once you have established all the details, you can create a schedule. The schedule will show you when to begin shooting and when to stop. Each day will include the time when you need to arrive at the location, when you need to leave and when you need to return home. So everyone is clear about what they need to do. If you need to hire extra staff, you can make sure you book them in advance. You don't want to hire someone who won't show up because he didn't know.
Also, consider how many days you will be filming your schedule. Some projects are quick and easy, while others take weeks. It is important to consider whether you require more than one photo per day when you create your schedule. Multiple takes at the same place will result in higher costs and longer completion times. If you are unsure if you need multiple takes, it is better to err on the side of caution and shoot fewer takes rather than risk wasting money.
Budgeting is another crucial aspect of production plan. You will be able to manage your resources if you have a realistic budget. Remember that you can always reduce the budget later on if you run into unforeseen problems. You shouldn't underestimate the amount you'll spend. If you underestimate the cost of something, you will have less money left after paying for other items.
Production planning is a complicated process. But once you understand how everything works together, it becomes much easier to plan future project.
What is the best way to learn about manufacturing?
Practical experience is the best way of learning about manufacturing. You can read books, or watch instructional videos if you don't have the opportunity to do so.
How can manufacturing avoid production bottlenecks
You can avoid bottlenecks in production by making sure that everything runs smoothly throughout the production cycle, from the moment you receive an order to the moment the product is shipped.
This includes planning for capacity requirements as well as quality control measures.
The best way to do this is to use continuous improvement techniques such as Six Sigma.
Six Sigma is a management method that helps to improve quality and reduce waste.
It focuses on eliminating variation and creating consistency in your work.
Why automate your warehouse?
Modern warehouses have become more dependent on automation. Increased demand for efficient and faster delivery has resulted in a rise in e-commerce.
Warehouses have to be flexible to meet changing requirements. Technology investment is necessary to enable warehouses to respond quickly to changing demands. Automation of warehouses offers many benefits. Here are some benefits of investing in automation
-
Increases throughput/productivity
-
Reduces errors
-
Improves accuracy
-
Safety enhancements
-
Eliminates bottlenecks
-
This allows companies to scale easily
-
Increases efficiency of workers
-
Provides visibility into everything that happens in the warehouse
-
Enhances customer experience
-
Improves employee satisfaction
-
Minimizes downtime and increases uptime
-
This ensures that quality products are delivered promptly
-
Removes human error
-
Helps ensure compliance with regulations
Statistics
- In the United States, for example, manufacturing makes up 15% of the economic output. (twi-global.com)
- In 2021, an estimated 12.1 million Americans work in the manufacturing sector.6 (investopedia.com)
- According to a Statista study, U.S. businesses spent $1.63 trillion on logistics in 2019, moving goods from origin to end user through various supply chain network segments. (netsuite.com)
- According to the United Nations Industrial Development Organization (UNIDO), China is the top manufacturer worldwide by 2019 output, producing 28.7% of the total global manufacturing output, followed by the United States, Japan, Germany, and India.[52][53] (en.wikipedia.org)
- You can multiply the result by 100 to get the total percent of monthly overhead. (investopedia.com)
External Links
How To
How to use 5S in Manufacturing to Increase Productivity
5S stands to stand for "Sort", “Set In Order", “Standardize", and "Store". Toyota Motor Corporation invented the 5S strategy in 1954. It helps companies achieve higher levels of efficiency by improving their work environment.
The basic idea behind this method is to standardize production processes, so they become repeatable, measurable, and predictable. Cleaning, sorting and packing are all done daily. These actions allow workers to perform their job more efficiently, knowing what to expect.
Implementing 5S requires five steps. These are Sort, Set In Order, Standardize. Separate. And Store. Each step is a different action that leads to greater efficiency. If you sort items, it makes them easier to find later. Once you have placed items in an ordered fashion, you will put them together. After you have divided your inventory into groups you can store them in easy-to-reach containers. Finally, label all containers correctly.
Employees need to reflect on how they do their jobs. Employees need to be able understand their motivations and discover alternative ways to do them. To implement the 5S system, employees must acquire new skills and techniques.
The 5S Method not only improves efficiency, but it also helps employees to be more productive and happier. They feel more motivated to work towards achieving greater efficiency as they see the results.