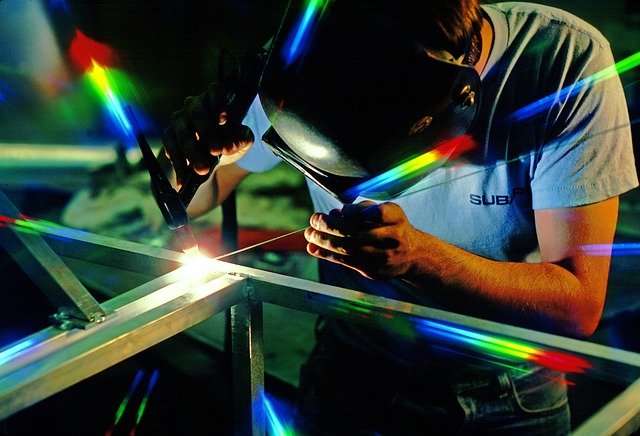
The company's manufacturing director is responsible for overseeing the entire production process. As they are responsible for managing the entire production process, their role is critical. For this job, you must have a great deal of manufacturing experience and be familiar with all new technologies. Examples of such technologies are robotics and 3-D printing. These technologies are an asset for any director. As the manufacturing industry continues to evolve, the director's role will become increasingly complex, as he or she must work with the engineering and operations departments, as well as putting a greater emphasis on quality control within the manufacturing plant.
Director of manufacturing salary
The pay scale for a Director of Manufacturing depends on where they live. Many directors are compensated in the low six-figure range, and some earn significantly more than others. The salary of a Director of Manufacturing may also vary significantly based on years of experience and education. Here are some factors that could impact your salary.
The salary for a Director Of Manufacturing varies, but in general, the more experience you have, the higher your salary will be. Like many other positions, salary can be affected by the cost of living or where you live. A large city may offer higher salaries. However, you should be aware of the fact that your salary may not cover living costs. Always be willing to negotiate for a higher salary, if offered.
The annual salary of a Director of Manufacturing Operations is between $181,500 to $66,000. The salary of a Director Manufacturing Operations is highly variable. It can vary by up 8% among different cities. Fremont's director manufacturing operations can expect to earn $128.493 to $164.500. This makes Fremont, CA a significantly better place than the national average. However, salaries for Director of Manufacturing Operations vary depending on location, experience, and company.
Education Required
The director for manufacturing is responsible in managing a manufacturing plant and supervising the production process. This job includes managing new employees, quality assurance, working with designers and meeting production standards. A director of manufacturing usually reports to the top management team. He or she executes sales and policy initiatives. Candidates should have previous experience in manufacturing, and be able to communicate effectively. There are different educational requirements to become a director in manufacturing.
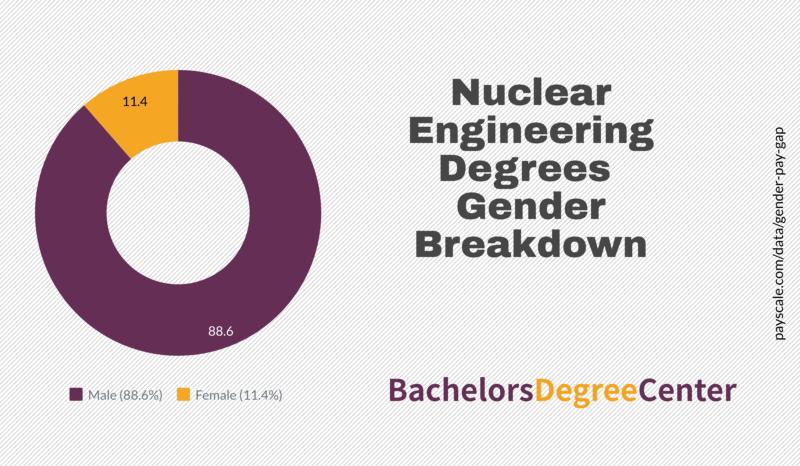
A graduate degree is not necessary for director of manufacturing jobs. However, you will be able to enhance your skill and knowledge by completing post-secondary education. A MBA program in business administration or industrial management is a great choice as it helps candidates learn about management, economics and organization. You will eventually be responsible to manage a diverse group.
You will be working closely with engineers and designers during product development. You will participate in the evaluation of new processes and setting quality standards before investing resources into larger productions. In addition to overseeing the production process, successful directors serve as coaches for employees. They mentor their employees in risk mitigation and best practices. They will also mentor them on best practices and risk mitigation.
Experience required
For this position, a bachelor's Degree in a relevant subject and 5-10 years of progressive experience are usually required. For this job, most manufacturing companies prefer to use their own employees. A candidate who is a good fit for this role will have an in-depth understanding of manufacturing processes and business goals. Employers may want to see a graduate level. Employers may require candidates to complete additional training in their chosen fields or industries.
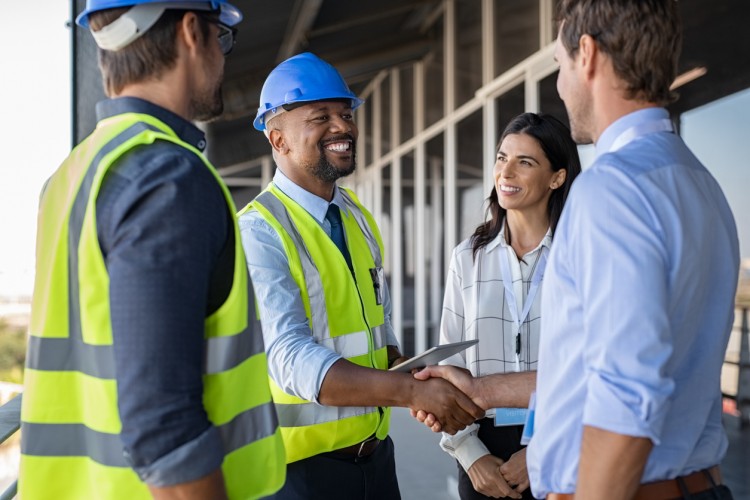
The manufacturing director oversees all aspects of the production process including workers, supervisors and engineers. They may be responsible for solving problems and developing a solution for them. They could also be responsible, in addition to supervising production, for creating and implementing quality-control programmes. A director of manufacturing reports directly to the top executive of the manufacturing organization. Manufacturing experience is a must. If you are looking to succeed in the manufacturing management position, it is important that you have some experience.
It is important to have experience as a director in manufacturing. Directors should have at least 10 years' experience in a manufacturing setting. They might have begun their careers as technicians or manufacturing supervisors. They should also have strong communication skills. A director of manufacturing should also have a thorough understanding of business strategy. Finally, a director of manufacturing must be able to work effectively with other departments within the organization. The director of manufacturing is responsible for overseeing production and ensuring it meets the highest quality standards.
FAQ
How can I find out more about manufacturing?
The best way to learn about manufacturing is through hands-on experience. You can read books, or watch instructional videos if you don't have the opportunity to do so.
What are the products of logistics?
Logistics refers to all activities that involve moving goods from A to B.
They cover all aspects of transportation, such as packing, loading, transporting and unloading.
Logisticians ensure that products reach the right destination at the right moment and under safe conditions. They assist companies with their supply chain efficiency through information on demand forecasts. Stock levels, production times, and availability.
They keep track and monitor the transit of shipments, maintain quality standards, order replenishment and inventories, coordinate with suppliers, vendors, and provide support for sales and marketing.
What is production management?
Production planning is the process of creating a plan that covers all aspects of production. This includes scheduling, budgeting and crew, location, equipment, props, and more. This document ensures that everything is prepared and available when you are ready for shooting. This document should include information about how to achieve the best results on-set. This information includes locations, crew details and equipment requirements.
It is important to first outline the type of film you would like to make. You might have an idea of where you want to film, or you may have specific locations or sets in mind. Once you've identified the locations and scenes you want to use, you can begin to plan what elements you need for each scene. One example is if you are unsure of the exact model you want but decide that you require a car. You could look online for cars to see what options are available, and then narrow down your choices by selecting between different makes or models.
Once you have found the right car, you can start thinking about extras. Are you looking for people to sit in the front seats? Or maybe you just need someone to push the car around. You might want to change your interior color from black and white. These questions will help determine the look and feel you want for your car. You can also think about the type of shots you want to get. Do you want to film close-ups, or wider angles? Maybe the engine or steering wheel is what you are looking to film. These things will help you to identify the car that you are looking for.
Once you've determined the above, it is time to start creating a calendar. The schedule will show you when to begin shooting and when to stop. You will need to know when you have to be there, what time you have to leave and when your return home. Everyone will know what they need and when. If you need to hire extra staff, you can make sure you book them in advance. It is not worth hiring someone who won’t show up because you didn’t tell him.
Also, consider how many days you will be filming your schedule. Some projects are quick and easy, while others take weeks. When creating your schedule, be aware of whether you need more shots per day. Multiplying takes in the same area will result both in increased costs and a longer time. It is better to be cautious and take fewer shots than you risk losing money if you are not sure if multiple takes are necessary.
Another important aspect of production planning is setting budgets. It is important to set a realistic budget so you can work within your budget. If you have to reduce your budget due to unexpected circumstances, you can always lower it later. But, don't underestimate how much money you'll spend. You'll end up with less money after paying for other things if the cost is underestimated.
Production planning is a very detailed process, but once you understand how everything works together, it becomes easier to plan future projects.
How can manufacturing reduce production bottlenecks?
The key to avoiding bottlenecks in production is to keep all processes running smoothly throughout the entire production cycle, from the time you receive an order until the time when the product ships.
This includes planning for both capacity requirements and quality control measures.
The best way to do this is to use continuous improvement techniques such as Six Sigma.
Six Sigma Management System is a method to increase quality and reduce waste throughout your organization.
It's all about eliminating variation and creating consistency in work.
What does it take to run a logistics business?
To be a successful businessman in logistics, you will need many skills and knowledge. For clients and suppliers to be successful, you need to have excellent communication skills. You should be able analyse data and draw inferences. You will need to be able handle pressure well and work in stressful situations. You need to be innovative and creative to come up with new ways to increase efficiency. Strong leadership qualities are essential to motivate your team and help them achieve their organizational goals.
It is also important to be efficient and well organized in order meet deadlines.
Statistics
- According to the United Nations Industrial Development Organization (UNIDO), China is the top manufacturer worldwide by 2019 output, producing 28.7% of the total global manufacturing output, followed by the United States, Japan, Germany, and India.[52][53] (en.wikipedia.org)
- According to a Statista study, U.S. businesses spent $1.63 trillion on logistics in 2019, moving goods from origin to end user through various supply chain network segments. (netsuite.com)
- You can multiply the result by 100 to get the total percent of monthly overhead. (investopedia.com)
- Many factories witnessed a 30% increase in output due to the shift to electric motors. (en.wikipedia.org)
- In the United States, for example, manufacturing makes up 15% of the economic output. (twi-global.com)
External Links
How To
How to use Lean Manufacturing in the production of goods
Lean manufacturing (or lean manufacturing) is a style of management that aims to increase efficiency, reduce waste and improve performance through continuous improvement. It was created in Japan by Taiichi Ohno during the 1970s and 80s. He received the Toyota Production System award (TPS), from Kanji Toyoda, founder of TPS. The first book published on lean manufacturing was titled "The Machine That Changed the World" written by Michael L. Watkins and published in 1990.
Lean manufacturing, often described as a set and practice of principles, is aimed at improving the quality, speed, cost, and efficiency of products, services, and other activities. It emphasizes the elimination of defects and waste throughout the value stream. The five-steps of Lean Manufacturing are just-in time (JIT), zero defect and total productive maintenance (TPM), as well as 5S. Lean manufacturing eliminates non-value-added tasks like inspection, rework, waiting.
Lean manufacturing improves product quality and costs. It also helps companies reach their goals quicker and decreases employee turnover. Lean manufacturing has been deemed one of the best ways to manage the entire value-chain, including customers, distributors as well retailers and employees. Many industries worldwide use lean manufacturing. For example, Toyota's philosophy underpins its success in automobiles, electronics, appliances, healthcare, chemical engineering, aerospace, paper, food, etc.
Five basic principles of Lean Manufacturing are included in lean manufacturing
-
Define Value: Identify the social value of your business and what sets you apart.
-
Reduce waste - Get rid of any activity that does not add value to the supply chain.
-
Create Flow. Ensure that your work is uninterrupted and flows seamlessly.
-
Standardize and simplify - Make your processes as consistent as possible.
-
Develop Relationships: Establish personal relationships both with internal and external stakeholders.
Lean manufacturing isn’t new, but it has seen a renewed interest since 2008 due to the global financial crisis. To increase their competitiveness, many businesses have turned to lean manufacturing. In fact, some economists believe that lean manufacturing will be an important factor in economic recovery.
Lean manufacturing, which has many benefits, is now a standard practice in the automotive industry. These benefits include increased customer satisfaction, reduced inventory levels and lower operating costs.
The principles of lean manufacturing can be applied in almost any area of an organization. It is especially useful for the production aspect of an organization, as it ensures that every step in the value chain is efficient and effective.
There are three main types:
-
Just-in Time Manufacturing (JIT), also known as "pull system": This form of lean manufacturing is often referred to simply as "pull". JIT means that components are assembled at the time of use and not manufactured in advance. This method reduces lead times, increases availability, and decreases inventory.
-
Zero Defects Manufacturing: ZDM ensures that no defective units leave the manufacturing plant. You should repair any part that needs to be repaired during an assembly line. This also applies to finished products that need minor repairs before being shipped.
-
Continuous Improvement (CI: Continuous improvement aims to increase the efficiency of operations by constantly identifying and making improvements to reduce or eliminate waste. Continuous Improvement (CI) involves continuous improvement in processes, people, tools, and infrastructure.