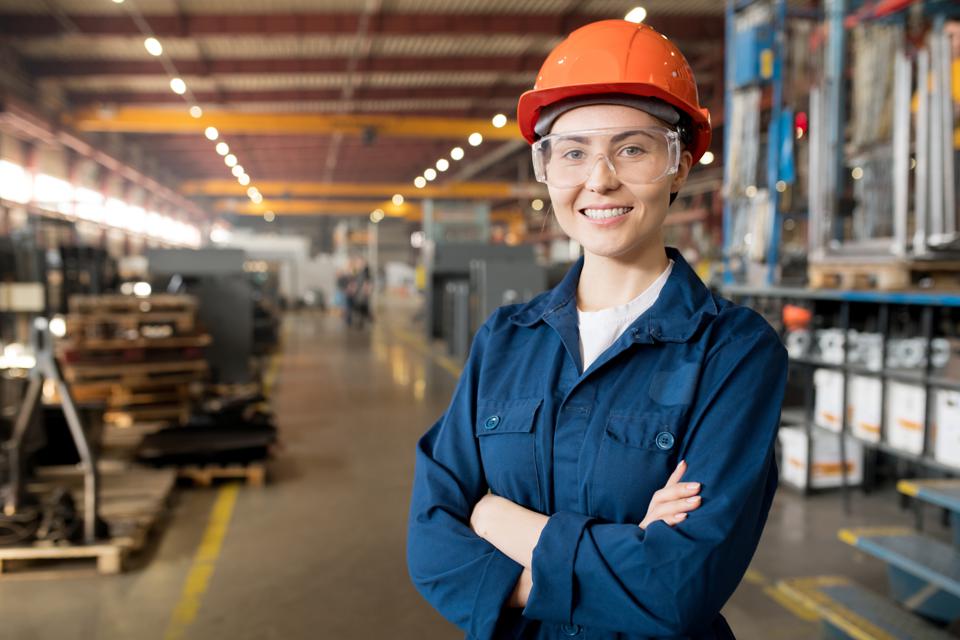
There are many industries that pay more then $50 an hour. Here are a few examples. The hourly rate for Aerospace engineers and Physician assistants is over $50. Life coaches are paid more than $50. Massage therapists get paid between $100 and 150 an hour. This article will provide information about the highest-paying jobs per hour. Find out how you can land these high-paying jobs. There are no shortage of opportunities if you want to make money fast, even in your spare time.
Aerospace engineers make more than $50 per hour
As an aerospace engineer you will be designing rockets, satellites and spacecraft. In addition, you'll test proposed projects for feasibility, safety, and acceptance criteria. You'll work with manufacturers, R&D facilities, and the federal Government. Aerospace engineers are highly sought after, so you could make well over $50 an hr. You also get great benefits from the government.
Physician assistants earn more than $50 an hour
As a physician assistant, you can earn a great salary. The average salary for a physician assistant is $47 an hour. However, there are other specialties that pay more. For example, oral and maxillofacial surgery specialists make $105 an hour. Optometrists as well as physical therapists make approximately the same salary as a physician assistant. Pharmacy workers average $43 an hour. These careers require years to learn and train, but they can offer attractive salaries.
Life coaches earn $100 to $150 an hour
The average hourly rate for life coaches is $100 to $150. The highest earners tend to be those in the corporate or executive arena. These coaches are required to complete special training and certification in order to be able earn such a high hourly wage. A life coach can make up to $50 an hour. Hosting webinars can be a lucrative business opportunity for life coaches. Some webinars are hosted weekly or monthly.
Massage therapists can earn between $100 and $150 an hour
While massage therapists don't typically make millions, they are still very valuable. Although tips are not usually required, it is worth giving more than the 20%. A small token of appreciation will show your gratitude and kindness, and can also help you earn extra cash. For additional income, you can also use a money-making program. Massage therapists make an average of $100 to $150 per hour.
Arizona's anesthesiologists make more than $50 per hour
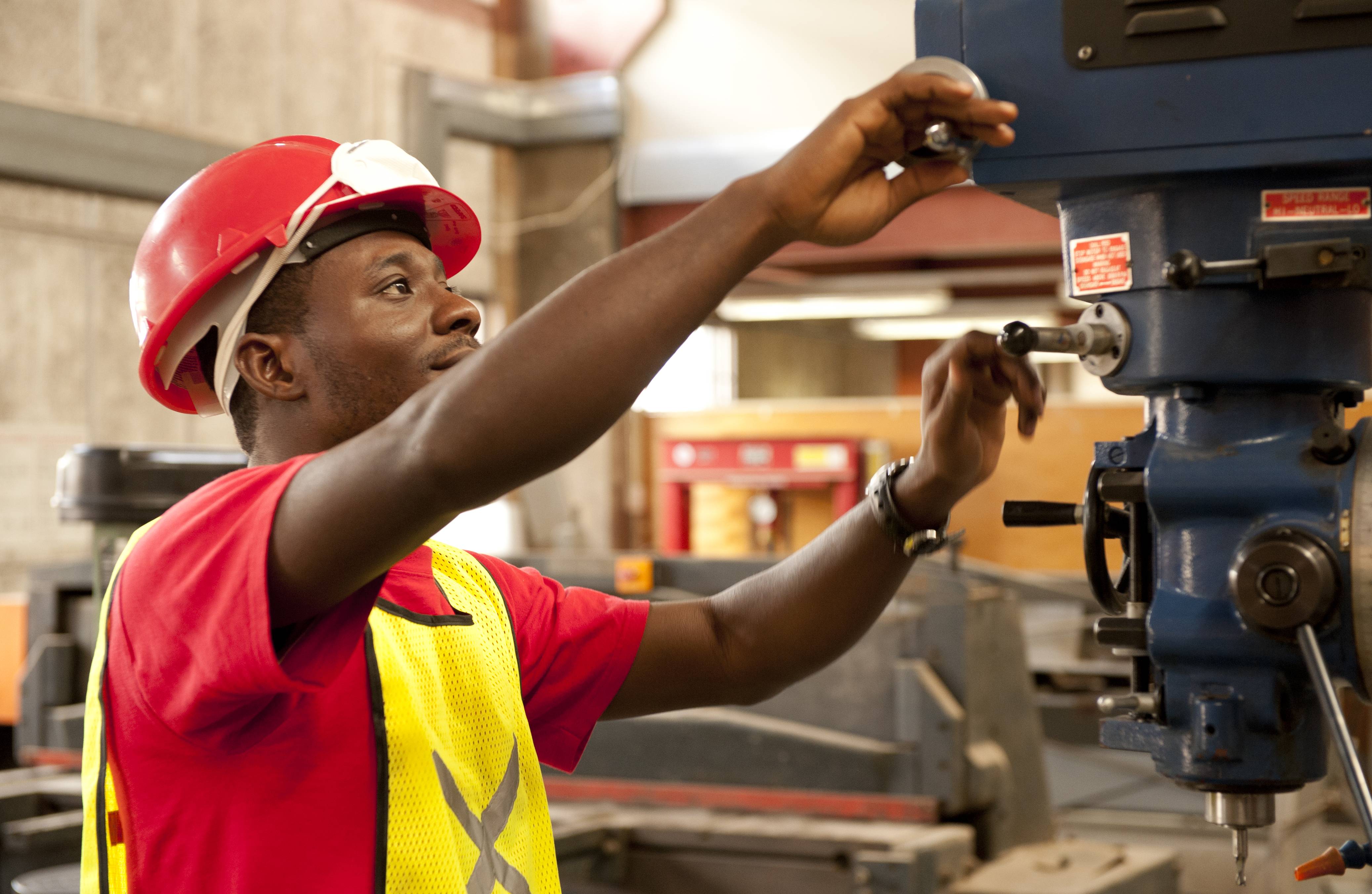
Arizona's anesthesiologists will receive a competitive wage as they are practicing. Arizona's average anesthesiologist salary is $80,254. But, there are many opportunities to earn more that $50 an hour, particularly if you focus on pain management. For example, you can work in an outpatient or hospital clinic, as well as in a surgical center. Additionally, surgeons earn less as anesthesiologists.
Tennessee's physician assistants are paid more than $50 an hour
There are many ways you can make more money. However, it takes a special set of skills to become a Tennessee physician's assistant. Tennessee's physician assistants are skilled in providing high-quality medical care. They often work in clinics and rural areas under the supervision of a doctor. According to the Robert Graham Center (which studies Tennessee's healthcare need), Tennessee will have 27% more primary doctors by 2030. This is an increase in growth than the average rate for most Southern states. Tennessee may experience a shortage of PAs over the next several years.
Arizona physician assistants can earn more than 50 dollars an hour
Being a physician assistant is an attractive career choice. Although it may appear like a quick fix job, many of these jobs require a lot more training, education, and hard work in order to be successful. The pay may be less than what you'd expect, but the rewards can outweigh the work involved. Check out these top jobs for Arizona PAs. This list will help guide you in your search for the ideal job to suit your career goals.
FAQ
What is the difference between manufacturing and logistics
Manufacturing refers to the process of making goods using raw materials and machines. Logistics manages all aspects of the supply chain, including procurement, production planning and distribution, inventory control, transportation, customer service, and transport. As a broad term, manufacturing and logistics often refer to both the creation and delivery of products.
What is the responsibility of a production planner?
Production planners make sure that every aspect of the project is delivered on-time, within budget, and within schedule. A production planner ensures that the service and product meet the client's expectations.
What do you mean by warehouse?
A warehouse is a place where goods are stored until they are sold. It can be indoors or out. In some cases, it may be a combination of both.
How can I find out more about manufacturing?
The best way to learn about manufacturing is through hands-on experience. You can also read educational videos or take classes if this isn't possible.
What does manufacturing industry mean?
Manufacturing Industries are companies that manufacture products. The people who buy these products are called consumers. To accomplish this goal, these companies employ a range of processes including distribution, sales, management, and production. They manufacture goods from raw materials using machines and other equipment. This includes all types if manufactured goods.
What skills are required to be a production manager?
A production planner must be organized, flexible, and able multitask to succeed. Also, you must be able and willing to communicate with clients and coworkers.
What is production planning?
Production Planning involves developing a plan for all aspects of the production, including scheduling, budgeting, casting, crew, location, equipment, props, etc. This document will ensure everything is in order and ready to go when you need it. This document should also include information on how to get the best result on set. This includes shooting schedules, locations, cast lists, crew details, and equipment requirements.
First, you need to plan what you want to film. You may have already decided where you would like to shoot, or maybe there are specific locations or sets that you want to use. Once you have determined your scenes and locations, it is time to start figuring out the elements that you will need for each scene. Perhaps you have decided that you need to buy a car but aren't sure which model. You could look online for cars to see what options are available, and then narrow down your choices by selecting between different makes or models.
After you've found the perfect car, it's time to start thinking about adding extras. You might need to have people in the front seats. Or maybe you just need someone to push the car around. Maybe you'd like to change the interior from black to a white color. These questions can help you decide the right look for your car. You can also think about the type of shots you want to get. Are you going to be shooting close-ups? Or wide angles? Maybe you want to show the engine and the steering wheel. These things will help you to identify the car that you are looking for.
Once you have made all the necessary decisions, you can start to create a schedule. You can create a schedule that will outline when you must start and finish your shoots. Each day will include the time when you need to arrive at the location, when you need to leave and when you need to return home. This way, everyone knows what they need to do and when. You can also make sure to book extra staff in advance if you have to hire them. There is no point in hiring someone who won't turn up because you didn't let him know.
Your schedule will also have to be adjusted to reflect the number of days required to film. Some projects only take one or two days, while others may last weeks. It is important to consider whether you require more than one photo per day when you create your schedule. Multiple takes at the same place will result in higher costs and longer completion times. If you are unsure if you need multiple takes, it is better to err on the side of caution and shoot fewer takes rather than risk wasting money.
Budget setting is another important aspect in production planning. You will be able to manage your resources if you have a realistic budget. Remember that you can always reduce the budget later on if you run into unforeseen problems. But, don't underestimate how much money you'll spend. You will end up spending less money if you underestimate the cost of something.
Production planning is a complicated process. But once you understand how everything works together, it becomes much easier to plan future project.
Statistics
- It's estimated that 10.8% of the U.S. GDP in 2020 was contributed to manufacturing. (investopedia.com)
- Many factories witnessed a 30% increase in output due to the shift to electric motors. (en.wikipedia.org)
- Job #1 is delivering the ordered product according to specifications: color, size, brand, and quantity. (netsuite.com)
- (2:04) MTO is a production technique wherein products are customized according to customer specifications, and production only starts after an order is received. (oracle.com)
- According to a Statista study, U.S. businesses spent $1.63 trillion on logistics in 2019, moving goods from origin to end user through various supply chain network segments. (netsuite.com)
External Links
How To
How to Use the Just In Time Method in Production
Just-in-time is a way to cut costs and increase efficiency in business processes. It is a process where you get the right amount of resources at the right moment when they are needed. This means you only pay what you use. The term was first coined by Frederick Taylor, who developed his theory while working as a foreman in the early 1900s. He saw how overtime was paid to workers for work that was delayed. He decided to ensure workers have enough time to do their jobs before starting work to improve productivity.
JIT is about planning ahead. You should have all the necessary resources ready to go so that you don’t waste money. The entire project should be looked at from start to finish. You need to ensure you have enough resources to tackle any issues that might arise. You will have the resources and people to solve any problems you anticipate. This will ensure that you don't spend more money on things that aren't necessary.
There are many JIT methods.
-
Demand-driven JIT: You order the parts and materials you need for your project every other day. This will let you track the amount of material left over after you've used it. This will let you know how long it will be to produce more.
-
Inventory-based: This is a type where you stock the materials required for your projects in advance. This allows you to predict how much you can expect to sell.
-
Project-driven : This is a method where you make sure that enough money is set aside to pay the project's cost. You will be able to purchase the right amount of materials if you know what you need.
-
Resource-based JIT is the most widespread form. This is where you assign resources based upon demand. For instance, if you have a lot of orders coming in, you'll assign more people to handle them. If there aren't many orders, you will assign fewer people.
-
Cost-based: This is a similar approach to resource-based but you are not only concerned with how many people you have, but also how much each one costs.
-
Price-based pricing: This is similar in concept to cost-based but instead you look at how much each worker costs, it looks at the overall company's price.
-
Material-based: This approach is similar to cost-based. However, instead of looking at the total cost for the company, you look at how much you spend on average on raw materials.
-
Time-based JIT: This is another variant of resource-based JIT. Instead of focusing on the cost of each employee, you will focus on the time it takes to complete a project.
-
Quality-based JIT is another variant of resource-based JIT. Instead of worrying about the costs of each employee or how long it takes for something to be made, you should think about how quality your product is.
-
Value-based: This is one of the newest forms of JIT. You don't worry about whether the products work or if they meet customer expectations. Instead, you're focused on how much value you add to the market.
-
Stock-based: This is an inventory-based method that focuses on the actual number of items being produced at any given time. It is used when production goals are met while inventory is kept to a minimum.
-
Just-in-time planning (JIT): This is a combination JIT and supply-chain management. It is the process of scheduling components' delivery as soon as they have been ordered. It reduces lead times and improves throughput.