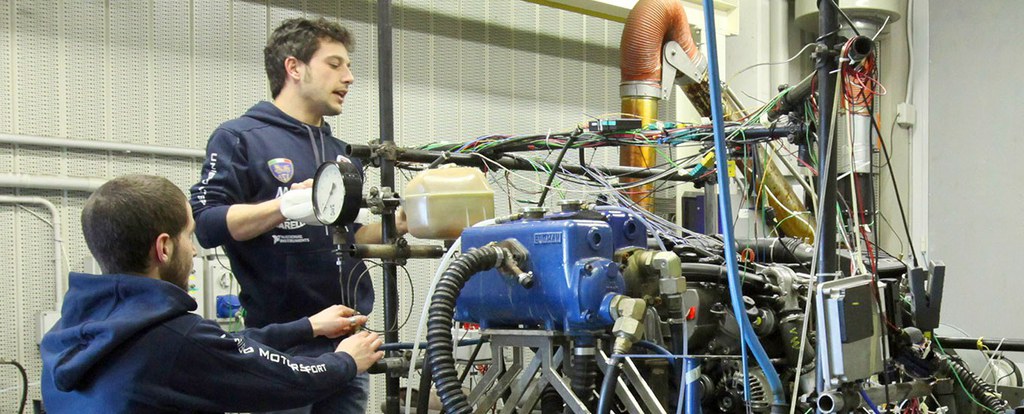
You're here because you are interested in a salary in biochemistry. This article will explain biochemical salaries in BOTHELL, WA and San Mateo, CA. Learn more about the different salary options for biochemical professionals to get you started in your career. Learn more about the job descriptions and salary requirements at Worthington Biochemical and Youtell Biochemical. Both companies have BOTHELL, WA headquarters and offer competitive benefits.
Youtell Biochemical pay is $29 an Hour
Youtell Biochemical averages $99854. Salaries range from $88,159 up to $114,509. Salary ranges from $88,159 up to $114,509, depending on what the position is, how much education they have and the skills required. Here are some examples for the types and salaries at Youtell Biochemical. The salary ranges are also based on experience and education, so keep this in mind when evaluating salaries.
The headquarters of Youtell Biochemical is located in BOTHELL WA
Youtell Biochemical is a chemical company headquartered in BOTHELL, WA that focuses on enzyme products. They have a state of the art biotechnology research centre in Bothell and two downstream processing or fermentation factories in China. The enzyme products are produced by these companies using patented technologies. Youtell Biochemical, located at BOTHELL, WA, produces over 80,000 tons each year.
Worthington Biochemical has its headquarters in San Mateo, CA.
Worthington Biochemical was founded in 1947. Charles Worthington founded Worthington Biochemical in 1947. He had previously worked as a Rockefeller Institute research associate, where he prepared crystalline enzymes that could be used in biochemical research. He saw that the biochemical community was growing and needed high-purity enzymes. Researchers would have to spend a lot time purifying them. Worthington started his own company in 1947, in Freehold, New Jersey, to supply these enzymes.
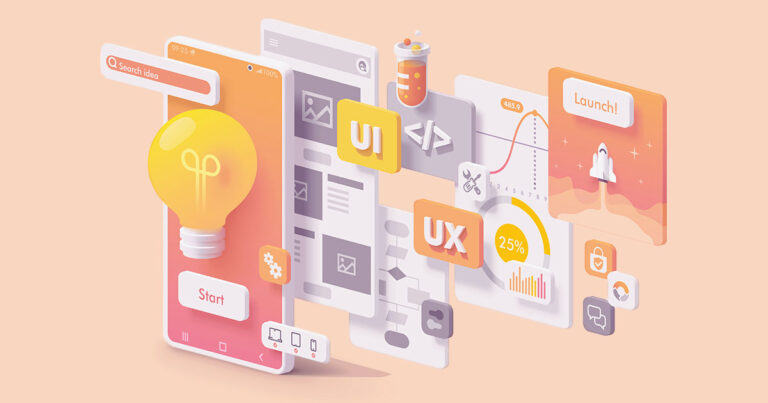
Worthington bought Cooper's Clinical Division in 1985. This was a biotech company based in New Jersey. Worthington was able to expand its operations while still focusing on the lucrative clinical market. But, the company didn't expand into immunology and molecular biology. Instead, the company expanded its capability to produce diagnostic kits and devoted less resources to enzyme manufacturing.
FAQ
Do we need to know about Manufacturing Processes before learning about Logistics?
No. No. Understanding the manufacturing process will allow you to better understand logistics.
What is the job of a production plan?
Production planners ensure all aspects of the project are delivered within time and budget. A production planner ensures that the service and product meet the client's expectations.
What's the difference between Production Planning & Scheduling?
Production Planning (PP), also known as forecasting and identifying production capacities, is the process that determines what product needs to be produced at any particular time. This can be done by forecasting demand and identifying production capabilities.
Scheduling involves the assignment of dates and times to tasks in order to complete them within the timeframe.
What is the job of a logistics manger?
Logistics managers ensure that goods arrive on time and are unharmed. This is done through his/her expertise and knowledge about the company's product range. He/she must also ensure sufficient stock to meet the demand.
Why automate your factory?
Automation has become increasingly important in modern warehousing. E-commerce has increased the demand for quicker delivery times and more efficient processes.
Warehouses must be able to quickly adapt to changing demands. Technology is essential for warehouses to be able to adapt quickly to changing needs. The benefits of automating warehouses are numerous. These are just a few reasons to invest in automation.
-
Increases throughput/productivity
-
Reduces errors
-
Increases accuracy
-
Safety enhancements
-
Eliminates bottlenecks
-
Allows companies to scale more easily
-
Increases efficiency of workers
-
Gives you visibility into all that is happening in your warehouse
-
Enhances customer experience
-
Improves employee satisfaction
-
Reducing downtime and increasing uptime
-
High quality products delivered on-time
-
Eliminates human error
-
This helps to ensure compliance with regulations
What are the 4 types manufacturing?
Manufacturing is the process by which raw materials are transformed into useful products through machines and processes. Manufacturing can include many activities such as designing and building, testing, packaging shipping, selling, servicing, and other related activities.
Statistics
- Many factories witnessed a 30% increase in output due to the shift to electric motors. (en.wikipedia.org)
- According to a Statista study, U.S. businesses spent $1.63 trillion on logistics in 2019, moving goods from origin to end user through various supply chain network segments. (netsuite.com)
- (2:04) MTO is a production technique wherein products are customized according to customer specifications, and production only starts after an order is received. (oracle.com)
- [54][55] These are the top 50 countries by the total value of manufacturing output in US dollars for its noted year according to World Bank.[56] (en.wikipedia.org)
- You can multiply the result by 100 to get the total percent of monthly overhead. (investopedia.com)
External Links
How To
Six Sigma in Manufacturing:
Six Sigma is defined as "the application of statistical process control (SPC) techniques to achieve continuous improvement." Motorola's Quality Improvement Department in Tokyo, Japan developed Six Sigma in 1986. Six Sigma's core idea is to improve the quality of processes by standardizing and eliminating defects. Many companies have adopted Six Sigma in recent years because they believe that there are no perfect products and services. Six Sigma seeks to reduce variation between the mean production value. It is possible to measure the performance of your product against an average and find the percentage of time that it differs from the norm. If this deviation is too big, you know something needs fixing.
Understanding how your business' variability is a key step towards Six Sigma implementation is the first. Once you have a good understanding of the basics, you can identify potential sources of variation. This will allow you to decide if these variations are random and systematic. Random variations are caused by human errors. Systematic variations can be caused by outside factors. These are, for instance, random variations that occur when widgets are made and some fall off the production line. But if you notice that every widget you make falls apart at the exact same place each time, this would indicate that there is a problem.
After identifying the problem areas, you will need to devise solutions. It might mean changing the way you do business or redesigning it entirely. To verify that the changes have worked, you need to test them again. If they fail, you can go back to the drawing board to come up with a different plan.