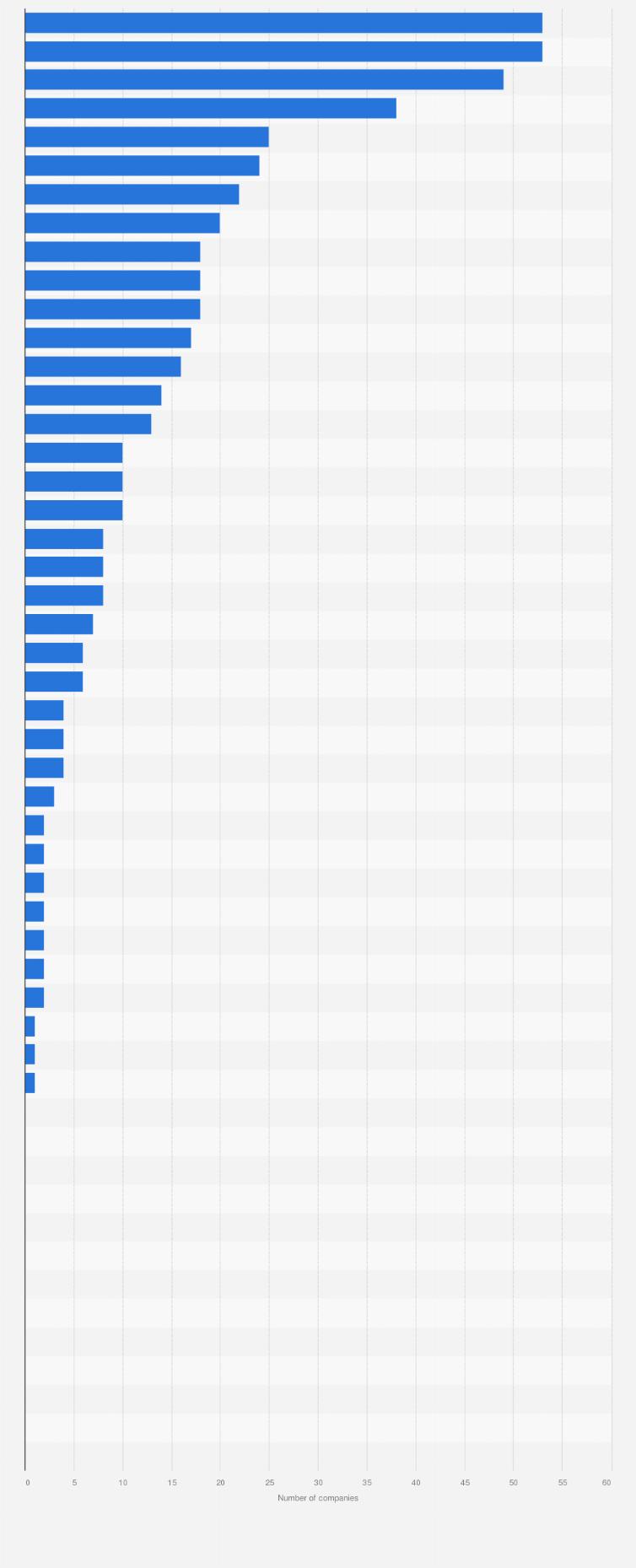
Toyota Motor Manufacturing Indiana Inc. in Gibson County is the first Toyota facility to be fully owned by Toyota in America. It produces Toyota's full-size pickup trucks including the Avalon, Corolla and Corolla as well as the Sienna minivan. The Toyota RAV4 Hybrid is also produced here, making it the most popular hybrid Toyota has ever made.
The original intention was to manufacture the Toyota Highlander. But, instead, the plant moved to Gibson County. Since 2011, the Toyota RAV4 Hybrid compact SUV has been produced here, as well as the Lexus ES 350. The plant was worth more than $1.33 Billion in 2017.
The plant also manufactures the Toyota Safety Sense 2.5+, which features automatic emergency braking. The plant also prepares all of the new 2018 Camry models. This new model has a new transmission and more power. It also features a stylish design. It will cost $25,900
Toyota's production of the Toyota Camry is the largest in the United States. It is America's most-sold midsize sedan and has been since 1995. Toyota has built 10 million Camrys here in Kentucky. The plant is the first in North America to manufacture the hybrid model.
Toyota Production System is a collection practices and techniques that increase quality and efficiency. This system will include 600 Toyota engineers. It will be the first center to build hydrogen fuel cell modules for heavy-duty commercial trucks. The facility can build up to 100,000 vehicles per year.
In the last five years, Toyota has invested $1.5 billion in the plant. The plant has also been home to 700 additional employees. This investment will help create 470k jobs in the United States over the next five years. Toyota has made over $147 Million in Kentucky non-profit partners since 1986.
The Toyota Camry has a reputation for being dependable and fashionable. It has the GA-K platform, and a new transmission. It's also fun to drive. Consumer Reports ranked the Toyota Camry among the top-selling vehicles in America in July 2018.
Toyota's production system has many elements. These include continuous improvement, just in-time parts delivery and a sophisticated robotic welding machine. Toyota's Kentucky investment is evident in the Toyota Production Engineering and Manufacturing Center.
Toyota can save money on air conditioning and construction costs with a new production hall design. The Visitor Center includes interactive video screens and exhibits about hybrid technology. Toyota will be producing up to 2,000,000 vehicles in North America over the next 10 year. This is the largest Toyota facility other than Japan.
The company's New Global Architecture, Toyota, is a significant step towards improving its production system. This strategy includes a new engine and production organization, as well as a module that unifies vehicle components. The new design keeps Toyota's innovative spirit alive while still preserving its traditional values.
FAQ
Are there ways to automate parts of manufacturing?
Yes! Since ancient times, automation has been in existence. The wheel was invented by the Egyptians thousands of years ago. We now use robots to help us with assembly lines.
In fact, there are several applications of robotics in manufacturing today. These include:
-
Line robots
-
Robot welding
-
Robot painting
-
Robotics inspection
-
Robots that produce products
Automation can be applied to manufacturing in many other ways. 3D printing makes it possible to produce custom products in a matter of days or weeks.
What are the main products of logistics?
Logistics are the activities involved in moving goods from point A to point B.
These include all aspects related to transport such as packaging, loading and transporting, storing, transporting, unloading and warehousing inventory management, customer service. Distribution, returns, recycling are some of the options.
Logisticians ensure the product reaches its destination in the most efficient manner. Logisticians assist companies in managing their supply chains by providing information such as demand forecasts, stock levels and production schedules.
They monitor shipments in transit, ensure quality standards, manage inventories, replenish orders, coordinate with suppliers and other vendors, and offer support services for sales, marketing, and customer service.
Is automation important in manufacturing?
Not only is automation important for manufacturers, but it's also vital for service providers. It enables them to provide services faster and more efficiently. It reduces human errors and improves productivity, which in turn helps them lower their costs.
Is there anything we should know about Manufacturing Processes prior to learning about Logistics.
No. You don't have to know about manufacturing processes before learning about logistics. Knowing about manufacturing processes will help you understand how logistics works.
Statistics
- Job #1 is delivering the ordered product according to specifications: color, size, brand, and quantity. (netsuite.com)
- (2:04) MTO is a production technique wherein products are customized according to customer specifications, and production only starts after an order is received. (oracle.com)
- You can multiply the result by 100 to get the total percent of monthly overhead. (investopedia.com)
- According to the United Nations Industrial Development Organization (UNIDO), China is the top manufacturer worldwide by 2019 output, producing 28.7% of the total global manufacturing output, followed by the United States, Japan, Germany, and India.[52][53] (en.wikipedia.org)
- [54][55] These are the top 50 countries by the total value of manufacturing output in US dollars for its noted year according to World Bank.[56] (en.wikipedia.org)
External Links
How To
How to use 5S to increase Productivity in Manufacturing
5S stands for "Sort", 'Set In Order", 'Standardize', & Separate>. Toyota Motor Corporation developed the 5S method in 1954. It helps companies achieve higher levels of efficiency by improving their work environment.
The idea behind standardizing production processes is to make them repeatable and measurable. It means tasks like cleaning, sorting or packing, labeling, and storing are done every day. Workers can be more productive by knowing what to expect.
There are five steps to implementing 5S, including Sort, Set In Order, Standardize, Separate and Store. Each step requires a different action, which increases efficiency. If you sort items, it makes them easier to find later. When you set items in an order, you put items together. After you have divided your inventory into groups you can store them in easy-to-reach containers. Finally, when you label your containers, you ensure everything is labeled correctly.
Employees need to reflect on how they do their jobs. Employees must be able to see why they do what they do and find a way to achieve them without having to rely on their old methods. To implement the 5S system, employees must acquire new skills and techniques.
In addition to improving efficiency, the 5S system also increases morale and teamwork among employees. As they begin to see improvements, they feel motivated to continue working towards the goal of achieving higher levels of efficiency.