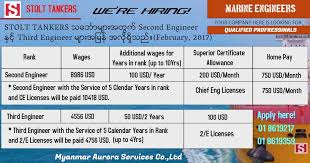
Robotics manufacturers and suppliers employ robotics technicians. They are responsible of the repair and maintenance of equipment used for building and operating robotic systems. A degree is required as well as practical experience. There are many salaries for robotics technicians, depending on experience and education.
An associate's degree is usually required for robotics technicians. This could be in electronics or mathematics. The degree typically provides a solid background in science, mathematics and computer programming. A robotics technician can work alongside a team made up of robotics professionals to develop, test and maintain robot systems after completing the program.
These systems are used in almost every aspect of our lives. From material handling and transportation to the defense department and the medical field, robots are employed in a wide variety of industries. A robot is able to gather information, such land mines, and provide it to troops in the military. Mechatronics, an engineering discipline, combines electrical, computer, and mechanical engineering.
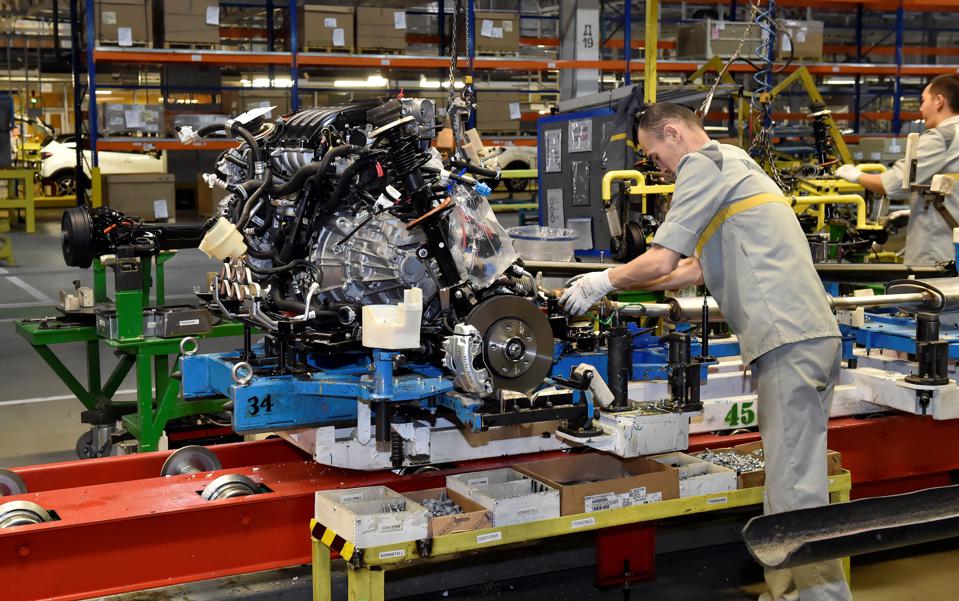
Robotics technician programs are offered by many universities and colleges in the United States. There are also opportunities for students to work directly with companies that hire robotics techs. Robot operators must be interested in solving problems and have an aptitude for math and science. However, employers will also generally require applicants to have a high school diploma.
The robotics technician's average salary is not high but the job requires a lot of education. Robotics technicians typically have a two year associate's degree. You may be required to complete additional training, but most employers will provide on-the job training.
Robotics technicians are expected to work around the clock, depending on the industry. Robotics operators are responsible for programming robots in order to complete specific tasks. Operators must diagnose the root cause of malfunctioning robots and then repair them. Operators will be required to work nights or weekends.
Robotics Technicians are typically paid in the range of $44,175 to $84,520. Atlanta, GA is the ideal place for Robotics Technicians. It has the best quality of life. Robotics Technicians earn an average $1,841 per week.
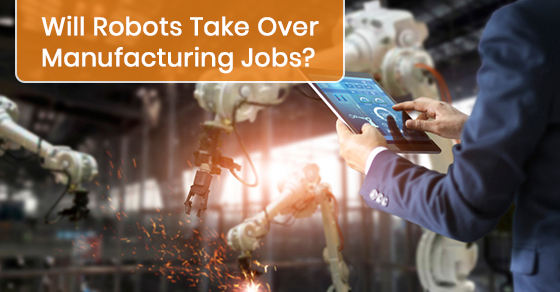
Another advantage of living in Atlanta is that the state tax rate for robotics technicians is lower. Georgia's robotics technicians, for example, pay 6% in taxes each year. This is significantly more than the national standard. Atlanta is a great place for people to settle.
Robotics technicians are an ideal fit for people who want to make a difference in the world. A robotics technician can make a great living as an expert in their field. Whether they are working as a maintenance technician or a robotics operator, these individuals will have the opportunity to use their knowledge and skills to make their employer and the world a safer place.
FAQ
How can manufacturing overproduction be reduced?
Better inventory management is key to reducing excess production. This would reduce time spent on activities such as purchasing, stocking, and maintaining excess stock. We could use these resources to do other productive tasks.
You can do this by adopting a Kanban method. A Kanban board, a visual display to show the progress of work, is called a Kanban board. Kanban systems are where work items travel through a series of states until reaching their final destination. Each state represents a different priority.
To illustrate, work can move from one stage or another when it is complete enough for it to be moved to a new stage. A task that is still in the initial stages of a process will be considered complete until it moves on to the next stage.
This allows for work to continue moving forward, while also ensuring that there is no work left behind. Managers can see how much work has been done and the status of each task at any time with a Kanban Board. This allows them to adjust their workflows based on real-time information.
Lean manufacturing, another method to control inventory levels, is also an option. Lean manufacturing is about eliminating waste from all stages of the production process. Anything that does nothing to add value to a product is waste. There are several types of waste that you might encounter:
-
Overproduction
-
Inventory
-
Unnecessary packaging
-
Materials in excess
By implementing these ideas, manufacturers can improve efficiency and cut costs.
What are the 7 Rs of logistics management?
The acronym 7R's for Logistics stands to represent the seven basic principles in logistics management. It was developed by International Association of Business Logisticians (IABL), and published as part of their "Seven Principles of Logistics Management Series" in 2004.
The acronym consists of the following letters:
-
Responsible - ensure that actions are in compliance with legal requirements and do not cause harm to others.
-
Reliable – have faith in your ability and capability to keep promises.
-
Be responsible - Use resources efficiently and avoid wasting them.
-
Realistic – Consider all aspects, including cost-effectiveness as well as environmental impact.
-
Respectful - treat people fairly and equitably.
-
Be resourceful: Look for opportunities to save money or increase productivity.
-
Recognizable - Provide value-added services to customers
What is the role of a logistics manager
A logistics manager ensures that all goods are delivered on time and without damage. This is done by using his/her experience and knowledge of the company's products. He/she also needs to ensure adequate stock to meet demand.
How can manufacturing avoid production bottlenecks
To avoid production bottlenecks, ensure that all processes run smoothly from the moment you receive your order to the time the product ships.
This includes planning for capacity requirements as well as quality control measures.
Continuous improvement techniques such Six Sigma are the best method to accomplish this.
Six Sigma Management System is a method to increase quality and reduce waste throughout your organization.
It's all about eliminating variation and creating consistency in work.
Statistics
- According to the United Nations Industrial Development Organization (UNIDO), China is the top manufacturer worldwide by 2019 output, producing 28.7% of the total global manufacturing output, followed by the United States, Japan, Germany, and India.[52][53] (en.wikipedia.org)
- (2:04) MTO is a production technique wherein products are customized according to customer specifications, and production only starts after an order is received. (oracle.com)
- [54][55] These are the top 50 countries by the total value of manufacturing output in US dollars for its noted year according to World Bank.[56] (en.wikipedia.org)
- In the United States, for example, manufacturing makes up 15% of the economic output. (twi-global.com)
- It's estimated that 10.8% of the U.S. GDP in 2020 was contributed to manufacturing. (investopedia.com)
External Links
How To
Six Sigma: How to Use it in Manufacturing
Six Sigma can be described as "the use of statistical process control (SPC), techniques to achieve continuous improvement." Motorola's Quality Improvement Department developed it at their Tokyo plant in Japan in 1986. Six Sigma's main goal is to improve process quality by standardizing processes and eliminating defects. This method has been adopted by many companies in recent years as they believe there are no perfect products or services. The main goal of Six Sigma is to reduce variation from the mean value of production. This means that if you take a sample of your product, then measure its performance against the average, you can find out what percentage of the time the process deviates from the norm. If the deviation is excessive, it's likely that something needs to be fixed.
Understanding the nature of variability in your business is the first step to Six Sigma. Once you have this understanding, you will need to identify sources and causes of variation. Also, you will need to identify the sources of variation. Random variations are caused when people make mistakes. While systematic variations are caused outside of the process, they can occur. Random variations would include, for example, the failure of some widgets to fall from the assembly line. You might notice that your widgets always fall apart at the same place every time you put them together.
After identifying the problem areas, you will need to devise solutions. That solution might involve changing the way you do things or redesigning the process altogether. After implementing the new changes, you should test them again to see if they worked. If they fail, you can go back to the drawing board to come up with a different plan.