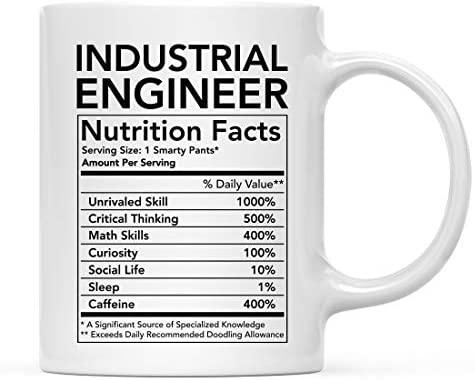
Civil engineers create infrastructure like roads, railways airports, dams, harbors, and bridges. Also, they manage and design water, sewerage and irrigation systems.
For a career in civil engineering, it is important to have a few skills and be committed to education. Students who want to enter the field must earn a bachelor's degree in civil engineering or a related discipline, such as construction or business administration. About one-fifth have a master's. It increases your chances of landing a job as a Senior Engineer, which could require a license issued by the Accreditation board for Engineering and technology (ABET).
A bachelor's in civil engineering or a closely-related discipline like construction management is usually required for entry-level positions. Most civil engineering programs take between four and five years to finish. However, many schools offer special programs which allow you to earn your degree for less money.
Graduates of civil engineering can take on a number of different roles. They may work as design engineers or project managers. They start out in a graduate programme, where they develop their skills under the guidance of an experienced professional. They can then move to a full-time position and become a lead engineering.
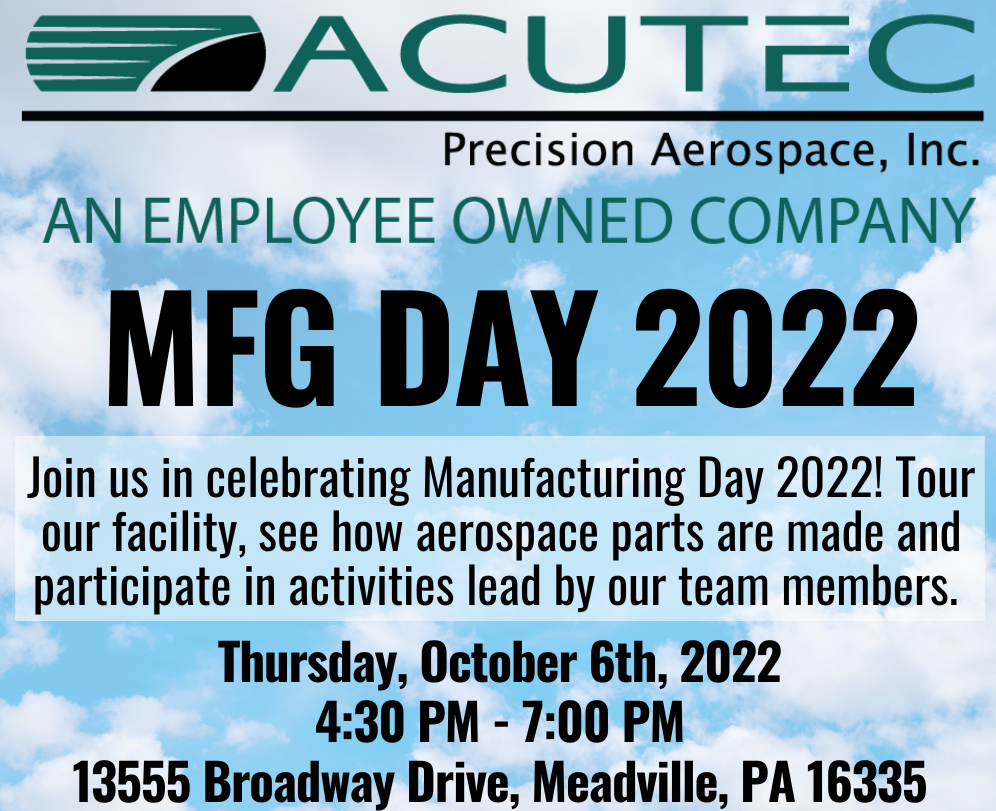
A career in civil engineering can be rewarding and challenging. There is also plenty of room to advance. You can find civil engineering careers in many different industries such as manufacturing, transportation, energy and energy.
Employers want candidates with excellent communication, creativity and critical thinking skills. These skills will allow you to improve your employer's technical processes and solve engineering challenges.
It is also essential to possess leadership and communication skills, as you will often be overseeing construction on your projects. You will need to communicate effectively with your team and vendors to quickly resolve any issues.
As the civil engineering profession is constantly evolving, it's essential to stay on top of trends and new regulations. To keep up, you can pursue continuing education and membership in a professional organization.
Also, decision-making is key to this job. This job requires you to make important decisions about budget and safety, while balancing the expertise of your team with that of others.
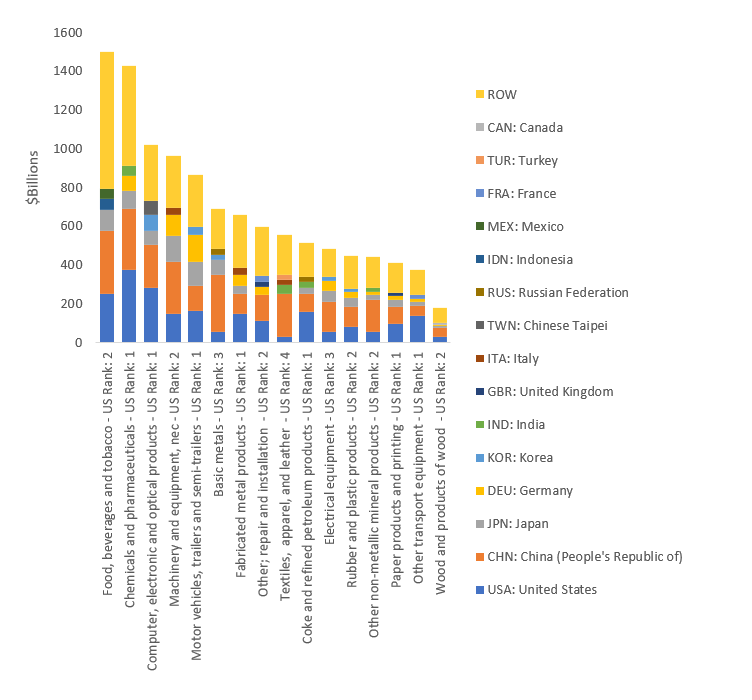
Your educational and training background will play a big role in your ability to succeed as a civil engineer, and you'll need to prove your worth on the job by completing projects and meeting deadlines. This includes communicating with clients, coworkers and contractors.
Other skills that will help you succeed in this career include a strong understanding of mathematics and physics, as well as the ability to think creatively and come up with innovative solutions. You'll need to be able analyze data and effectively present your findings.
Salary ranges for civil engineers are dependent on both the position held and the state in which you reside. California, Texas and Florida pay the most for this career. Alaska, Rhode Island, Wyoming and Alaska are other states that pay well for civil engineers.
FAQ
What are the responsibilities of a production planner
Production planners ensure that all project aspects are completed on time, within budget and within the scope. A production planner ensures that the service and product meet the client's expectations.
Is automation important for manufacturing?
Not only is automation important for manufacturers, but it's also vital for service providers. Automation allows them to deliver services quicker and more efficiently. It also helps to reduce costs and improve productivity.
Why automate your warehouse?
Modern warehouses have become more dependent on automation. Increased demand for efficient and faster delivery has resulted in a rise in e-commerce.
Warehouses have to be flexible to meet changing requirements. They must invest heavily in technology to do this. Automating warehouses is a great way to save money. Here are some of the reasons automation is worth your investment:
-
Increases throughput/productivity
-
Reduces errors
-
Increases accuracy
-
Safety is boosted
-
Eliminates bottlenecks
-
Companies can scale up more easily
-
This makes workers more productive
-
Provides visibility into everything that happens in the warehouse
-
Enhances customer experience
-
Improves employee satisfaction
-
Reduces downtime and improves uptime
-
You can be sure that high-quality products will arrive on time
-
Eliminates human error
-
This helps to ensure compliance with regulations
Statistics
- In 2021, an estimated 12.1 million Americans work in the manufacturing sector.6 (investopedia.com)
- Many factories witnessed a 30% increase in output due to the shift to electric motors. (en.wikipedia.org)
- (2:04) MTO is a production technique wherein products are customized according to customer specifications, and production only starts after an order is received. (oracle.com)
- [54][55] These are the top 50 countries by the total value of manufacturing output in US dollars for its noted year according to World Bank.[56] (en.wikipedia.org)
- In the United States, for example, manufacturing makes up 15% of the economic output. (twi-global.com)
External Links
How To
How to use 5S in Manufacturing to Increase Productivity
5S stands for "Sort", "Set In Order", "Standardize", "Separate" and "Store". The 5S methodology was developed at Toyota Motor Corporation in 1954. It assists companies in improving their work environments and achieving higher efficiency.
This approach aims to standardize production procedures, making them predictable, repeatable, and easily measurable. This means that every day tasks such cleaning, sorting/storing, packing, and labeling can be performed. Because workers know what they can expect, this helps them perform their jobs more efficiently.
Implementing 5S requires five steps. These are Sort, Set In Order, Standardize. Separate. And Store. Each step requires a different action to increase efficiency. If you sort items, it makes them easier to find later. Once you have placed items in an ordered fashion, you will put them together. Next, organize your inventory into categories and store them in containers that are easily accessible. Make sure everything is correctly labeled when you label your containers.
This requires employees to critically evaluate how they work. Employees must understand why they do certain tasks and decide if there's another way to accomplish them without relying on the old ways of doing things. They must learn new skills and techniques in order to implement the 5S system.
In addition to improving efficiency, the 5S system also increases morale and teamwork among employees. Once they start to notice improvements, they are motivated to keep working towards their goal of increasing efficiency.