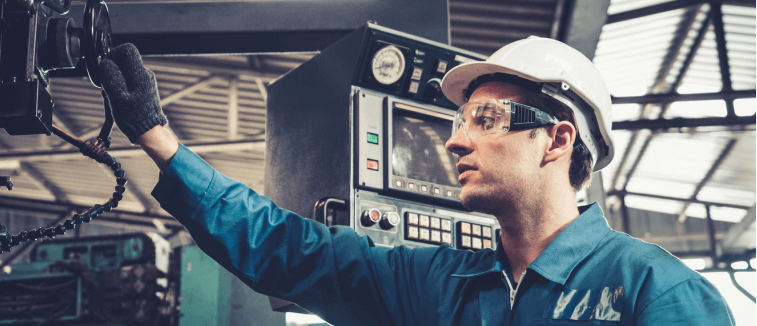
Cellular manufacturing involves dividing a production plant into segments that produce a different component of the finished product. This helps to minimize waste and to decrease lead times. Many ways can cellular manufacturing be implemented. Some are easier than others, while some require sophisticated computer models. Cellular production is one subset of the lean Manufacturing movement.
Cellular manufacturing is a new and efficient process that can lower the cost of parts as well as the time required to produce them. The goal is to minimize waste while moving products along the production line as quickly possible. Cellular manufacturing also addresses issues such as group cohesiveness and self management, as well issues involving employee inputs and supervision. Cellular manufacturing offers greater flexibility that can be used to meet customer demands. It has been proven that cellular manufacturing can also improve productivity.
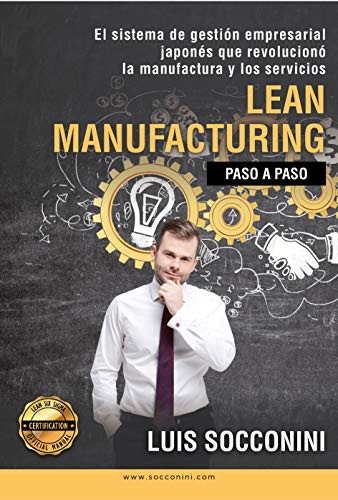
Cellular manufacturing can be used in many different ways. From simple applications like production flow analysis, to more complicated computer models. The goal is to produce similar products at the same time, which minimizes wasteful motion and takt time.
The cell layout can impact the overall takt times. The cells' design can impact the speed of motion. It can also affect how value is added or non-value. This reduces cycle times. Some cells can be configured in a U shape, which allows operators to move faster from one machine to the next. Some cells can also be configured in a U-shape that allows operators to move faster between machines. These designs can be particularly beneficial for organizations that produce many products.
The first step to creating a cell is to identify the products that will be produced in it. A process map can help you determine the production rate. Engineers need to determine the number and process steps of the workcell in order to create it. Next, engineers must decide what tools and equipment will be used in the cells. Modern-day work cells also consider the number of steps and types of holding bins. They also take into consideration how many steps each machine will require. The physical structure of the cell will determine which layout is most effective.
The cell's layout is key to the success and efficiency of cell manufacturing. Cell design can affect how much motion is lost and how many waste products are created. It can also affect fatigue. Cellular manufacturing is not only able to reduce motion, but it can also increase process efficiency and quality. By arranging cells in a way that makes it easy to catch defects quickly and reduces waste, you can improve the efficiency of cell manufacturing.
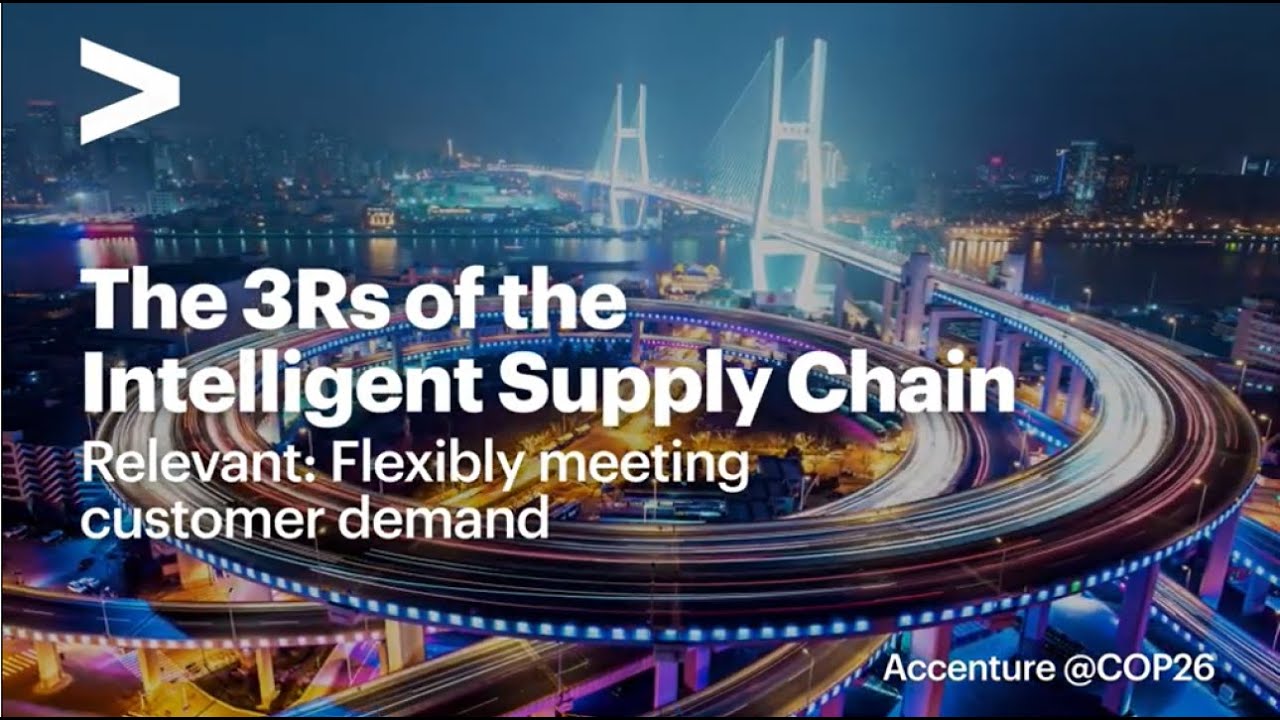
A U, Z and S are the most popular layouts. S-shaped cell can also be used for working around obstructions. It is possible to customize the layout of cells, as well as reconfigure different cells to meet different requirements in different parts of a factory.
FAQ
Why is logistics important in manufacturing?
Logistics are an integral part any business. They can help you achieve great success by helping you manage product flow from raw material to finished goods.
Logistics play an important role in reducing costs as well as increasing efficiency.
What does "warehouse" mean?
A warehouse, or storage facility, is where goods are stored prior to being sold. It can be an indoor space or an outdoor area. Sometimes, it can be both an indoor and outdoor space.
Why automate your warehouse?
Modern warehouses have become more dependent on automation. Increased demand for efficient and faster delivery has resulted in a rise in e-commerce.
Warehouses should be able adapt quickly to new needs. Technology is essential for warehouses to be able to adapt quickly to changing needs. The benefits of automating warehouses are numerous. These are just a few reasons to invest in automation.
-
Increases throughput/productivity
-
Reduces errors
-
Improves accuracy
-
Safety Boosts
-
Eliminates bottlenecks
-
Companies can scale up more easily
-
This makes workers more productive
-
It gives visibility to everything that happens inside the warehouse
-
Enhances customer experience
-
Improves employee satisfaction
-
Reduces downtime and improves uptime
-
Ensures quality products are delivered on time
-
Removing human error
-
Assure compliance with regulations
What are the 7 Rs of logistics management?
The 7R's of Logistics is an acronym for the seven basic principles of logistics management. It was developed and published by the International Association of Business Logisticians in 2004 as part of the "Seven Principles of Logistics Management".
The following letters form the acronym:
-
Responsible - to ensure that all actions are within the legal requirements and are not detrimental to others.
-
Reliable - You can have confidence that you will fulfill your promises.
-
Reasonable - use resources efficiently and don't waste them.
-
Realistic - Consider all aspects of operations, including environmental impact and cost effectiveness.
-
Respectful - show respect and treat others fairly and fairly
-
Be resourceful: Look for opportunities to save money or increase productivity.
-
Recognizable is a company that provides customers with value-added solutions.
Statistics
- In the United States, for example, manufacturing makes up 15% of the economic output. (twi-global.com)
- It's estimated that 10.8% of the U.S. GDP in 2020 was contributed to manufacturing. (investopedia.com)
- In 2021, an estimated 12.1 million Americans work in the manufacturing sector.6 (investopedia.com)
- Job #1 is delivering the ordered product according to specifications: color, size, brand, and quantity. (netsuite.com)
- Many factories witnessed a 30% increase in output due to the shift to electric motors. (en.wikipedia.org)
External Links
How To
How to Use Six Sigma in Manufacturing
Six Sigma can be described as "the use of statistical process control (SPC), techniques to achieve continuous improvement." Motorola's Quality Improvement Department in Tokyo, Japan developed Six Sigma in 1986. Six Sigma's basic concept is to improve quality and eliminate defects through standardization. In recent years, many companies have adopted this method because they believe there is no such thing as perfect products or services. The main goal of Six Sigma is to reduce variation from the mean value of production. You can calculate the percentage of deviation from the norm by taking a sample of your product and comparing it to the average. If you notice a large deviation, then it is time to fix it.
Understanding the nature of variability in your business is the first step to Six Sigma. Once you've understood that, you'll want to identify sources of variation. Also, you will need to identify the sources of variation. Random variations happen when people make errors; systematic variations are caused externally. Random variations would include, for example, the failure of some widgets to fall from the assembly line. If however, you notice that each time you assemble a widget it falls apart in exactly the same spot, that is a problem.
Once you identify the problem areas, it is time to create solutions. You might need to change the way you work or completely redesign the process. Test them again once you've implemented the changes. If they don’t work, you’ll need to go back and rework the plan.