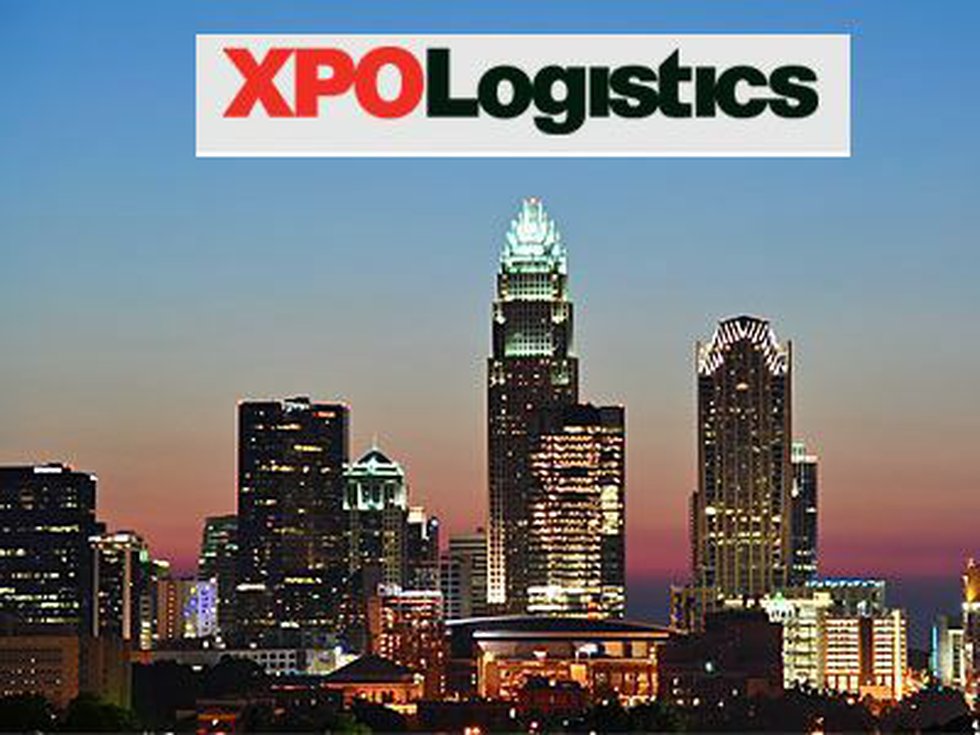
Lean to Agile can help reduce waste and improve team productivity. It emphasizes prioritizing work and eliminating waste. While empowering scrummasters and teams to do all the rest, it also focuses on prioritizing work. Also, agile teams should be empowered as product owners as well as servant leaders committed to the success and growth of their projects.
Time-to-market
One of the most important measures of product success is how long it takes to go from ideation to final release. This timeframe will determine how quickly your company can gain market share or revenue. Companies need to know their development processes, and how they use them. Companies will then be able to optimize their processes to meet the objectives of their business and to maximize their capabilities to improve their time to market.
Outsourcing can be used to speed up the time it takes to bring a product to market. It is possible to cut down on time by creating an ecosystem of reliable support partners. This approach can help reduce risk and share resources.
Iteration
Iteration plays a critical role in agile software development. Iteration emphasizes the importance small, manageable steps that can easily be tested and evaluated sooner than a whole process. These features yield better results and higher chances of success. The process is usually time-bound. Iterations must be able to produce an end product that is running and easily available. This requires that the end product be integrated, tested, then deployed on an internal server.
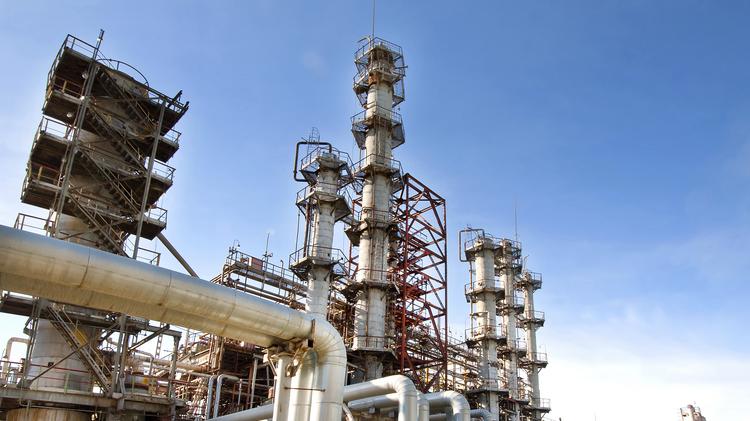
Iterations are a time when teams can work together to improve their backlog and find solutions for risks or issues that they haven't seen before. Each iteration should be better than the previous. Developers might modify or add features to existing functions. This process is repeated until the product is ready to be released.
Collaborative processes
Agile Manifesto stresses collaboration between business stakeholders as well as developers. This allows teams to prioritise work based upon business goals. Lean processes encourage a value stream. This is the end-to–end list of actions required to produce the product or services customers desire. While these approaches may seem similar, there are important differences.
Agile is more flexible that Lean. Lean UX teams use Lean instead of rigid project management tools. They work in small groups and scale up quickly to reach a goal. Agile is a system which consists of small-world networks, deliverables, and other elements. It also emphasizes autonomy exploration and collaboration. An agile approach is required for scaling from one project to multiple projects.
User research in agile teams
Agile teams are increasingly incorporating user feedback into their processes. This approach is increasingly being used in product development but is also being adopted by other departments. Teams are increasingly realizing the importance of user experience and usability, and the need for flexible and quick research. Agile teams apply agile thinking to identify processes that are connected to the product backlog in order to get user-centric research at the forefront of development.
It is essential that user research workflows are simpler and more democratic. This involves creating repeatable templates for user research that non-practitioners could use to run their tests. These templates should answer most of the questions and cover all phases of product development. To ensure consistent results, teams can also take advantage of UX platforms that offer preloaded templates and automated workflows.
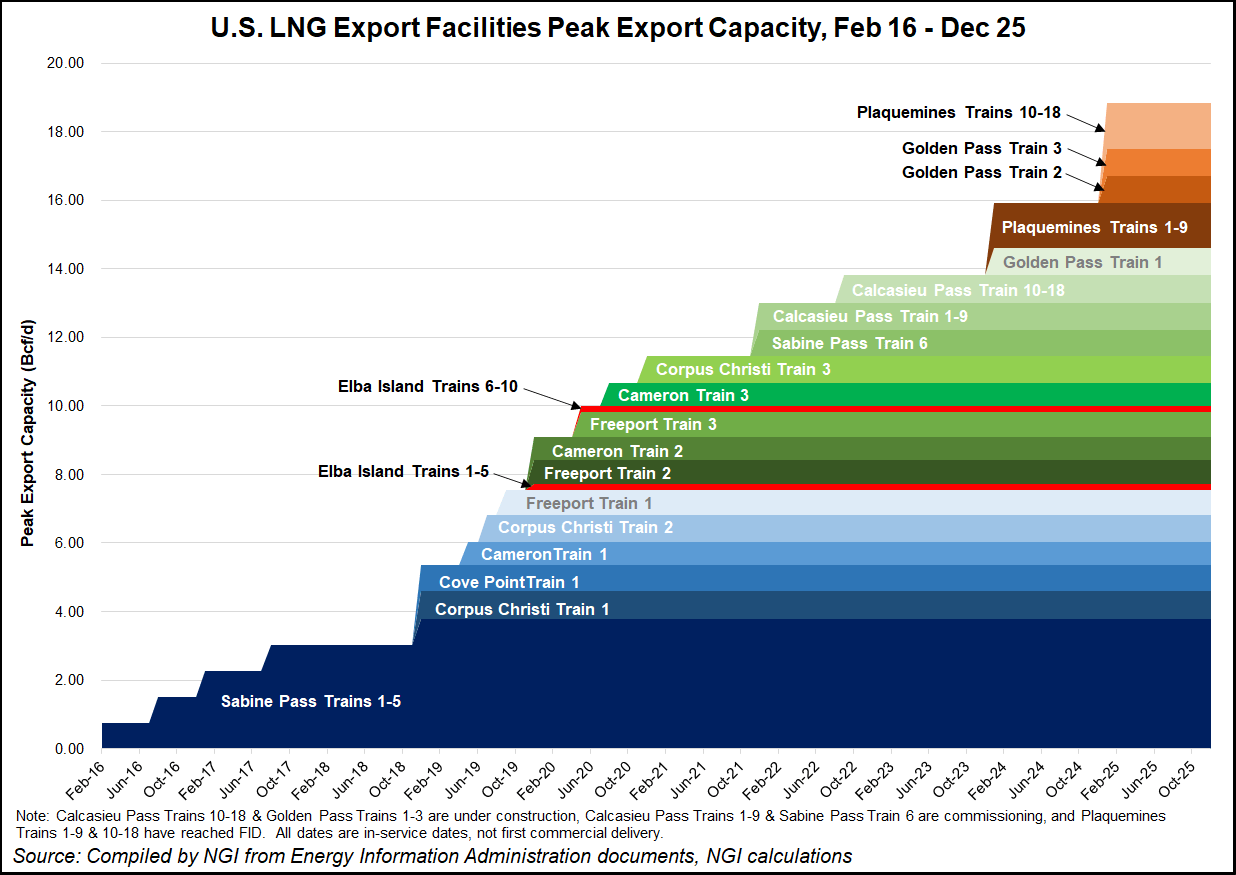
Value creation
The concept of value creation is somewhat odd, even if it makes sense. Creating value can be done in a very narrow scope or a wider one, but in neither case can the process be fully binary. In some cases, a smaller scope produces less value and a greater scope generates more. But, it is possible to have a comprehensive scope.
Lean and agile aim to provide a customer with a high-quality, focused product. Combining these two approaches allows companies to produce better products and deliver them faster. This reduces overhead, empowers employees and allows them to concentrate on the customer.
FAQ
How can overproduction in manufacturing be reduced?
In order to reduce excess production, you need to develop better inventory management methods. This would reduce the amount of time spent on unnecessary activities such as purchasing, storing, and maintaining excess stock. We could use these resources to do other productive tasks.
One way to do this is to adopt a Kanban system. A Kanban Board is a visual display that tracks work progress. A Kanban system allows work items to move through several states before reaching their final destination. Each state represents a different priority.
If work is moving from one stage to the other, then the current task can be completed and moved on to the next. But if a task remains in the beginning stages it will stay that way until it reaches its end.
This helps to keep work moving forward while ensuring that no work is left behind. Managers can view the Kanban board to see how much work they have done. This allows them to adjust their workflows based on real-time information.
Lean manufacturing can also be used to reduce inventory levels. Lean manufacturing emphasizes eliminating waste in all phases of production. Any product that isn't adding value can be considered waste. Some common types of waste include:
-
Overproduction
-
Inventory
-
Packaging that is not necessary
-
Excess materials
By implementing these ideas, manufacturers can improve efficiency and cut costs.
What are the products and services of logistics?
Logistics refers to the movement of goods from one place to another.
They include all aspects associated with transport including packaging, loading transporting, unloading storage, warehousing inventory management customer service, distribution returns and recycling.
Logisticians ensure that the right product reaches the right place at the right time and under safe conditions. They assist companies with their supply chain efficiency through information on demand forecasts. Stock levels, production times, and availability.
They keep track and monitor the transit of shipments, maintain quality standards, order replenishment and inventories, coordinate with suppliers, vendors, and provide support for sales and marketing.
What are the 7 Rs of logistics?
The acronym 7R's of Logistic is an acronym that stands for seven fundamental principles of logistics management. It was published in 2004 by the International Association of Business Logisticians as part of their "Seven Principles of Logistics Management" series.
The acronym is composed of the following letters.
-
Responsive - ensure all actions are legal and not harmful to others.
-
Reliable – have faith in your ability and capability to keep promises.
-
Be responsible - Use resources efficiently and avoid wasting them.
-
Realistic - Consider all aspects of operations, including environmental impact and cost effectiveness.
-
Respectful – Treat others fairly and equitably.
-
You are resourceful and look for ways to save money while increasing productivity.
-
Recognizable is a company that provides customers with value-added solutions.
Statistics
- In 2021, an estimated 12.1 million Americans work in the manufacturing sector.6 (investopedia.com)
- According to the United Nations Industrial Development Organization (UNIDO), China is the top manufacturer worldwide by 2019 output, producing 28.7% of the total global manufacturing output, followed by the United States, Japan, Germany, and India.[52][53] (en.wikipedia.org)
- [54][55] These are the top 50 countries by the total value of manufacturing output in US dollars for its noted year according to World Bank.[56] (en.wikipedia.org)
- According to a Statista study, U.S. businesses spent $1.63 trillion on logistics in 2019, moving goods from origin to end user through various supply chain network segments. (netsuite.com)
- Job #1 is delivering the ordered product according to specifications: color, size, brand, and quantity. (netsuite.com)
External Links
How To
How to Use Lean Manufacturing for the Production of Goods
Lean manufacturing (or lean manufacturing) is a style of management that aims to increase efficiency, reduce waste and improve performance through continuous improvement. It was first developed in Japan in the 1970s/80s by Taiichi Ahno, who was awarded the Toyota Production System (TPS), award from KanjiToyoda, the founder of TPS. Michael L. Watkins published the book "The Machine That Changed the World", which was the first to be published about lean manufacturing.
Lean manufacturing can be described as a set or principles that are used to improve quality, speed and cost of products or services. It emphasizes reducing defects and eliminating waste throughout the value chain. Just-in-time (JIT), zero defect (TPM), and 5S are all examples of lean manufacturing. Lean manufacturing is about eliminating activities that do not add value, such as inspection, rework, and waiting.
Lean manufacturing improves product quality and costs. It also helps companies reach their goals quicker and decreases employee turnover. Lean Manufacturing is one of the most efficient ways to manage the entire value chains, including suppliers and customers as well distributors and retailers. Lean manufacturing is widely used in many industries. Toyota's philosophy has been a key driver of success in many industries, including automobiles and electronics.
Five principles are the basis of lean manufacturing:
-
Define value - Find out what your business contributes to society, and what makes it different from other competitors.
-
Reduce waste - Get rid of any activity that does not add value to the supply chain.
-
Create Flow – Ensure that work flows smoothly throughout the process.
-
Standardize and simplify - Make your processes as consistent as possible.
-
Build Relationships- Develop personal relationships with both internal as well as external stakeholders.
Lean manufacturing is not a new concept, but it has been gaining popularity over the last few years due to a renewed interest in the economy following the global financial crisis of 2008. Many companies have adopted lean manufacturing methods to increase their marketability. According to some economists, lean manufacturing could be a significant factor in the economic recovery.
Lean manufacturing has many benefits in the automotive sector. These include higher customer satisfaction levels, reduced inventory levels as well as lower operating costs.
It can be applied to any aspect of an organisation. Because it makes sure that all value chains are efficient and effectively managed, Lean Manufacturing is particularly helpful for organizations.
There are three main types of lean manufacturing:
-
Just-in-Time Manufacturing (JIT): This type of lean manufacturing is commonly referred to as "pull systems." JIT is a method in which components are assembled right at the moment of use, rather than being manufactured ahead of time. This approach aims to reduce lead times, increase the availability of parts, and reduce inventory.
-
Zero Defects Manufacturing - ZDM: ZDM focuses its efforts on making sure that no defective units leave a manufacturing facility. If a part is required to be repaired on the assembly line, it should not be scrapped. This applies to finished goods that may require minor repairs before shipment.
-
Continuous Improvement (CI): CI aims to improve the efficiency of operations by continuously identifying problems and making changes in order to eliminate or minimize waste. It involves continuous improvement of processes, people, and tools.