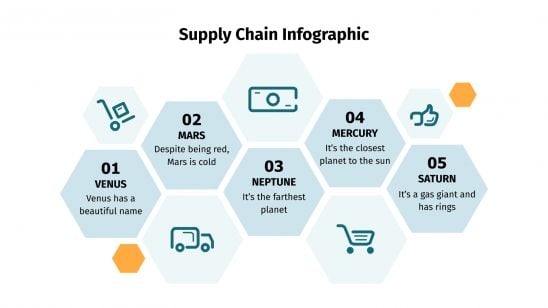
A manufacturing job in the Capital Region of Texas is more than just a job. These jobs require extensive education and training to be successful in the industry. The region's average annual wage for a manufacturer is $88,406, with wages expected to rise by 2.5% over the next year. A number of manufacturing companies have adopted a number of safeguards to prevent workers from becoming susceptible to health and safety issues.
The Capital Region of Texas actually houses 30 percent of Texas' manufacturing jobs. And while the number of workers in the sector declined by -800 in February 2021, it was by no means a retrenchment. Acme Brick is home to some of the nation's most innovative companies, as well as Samsung Austin Semiconductor. This is why the metropolitanplex is one reason that it is so vibrant.
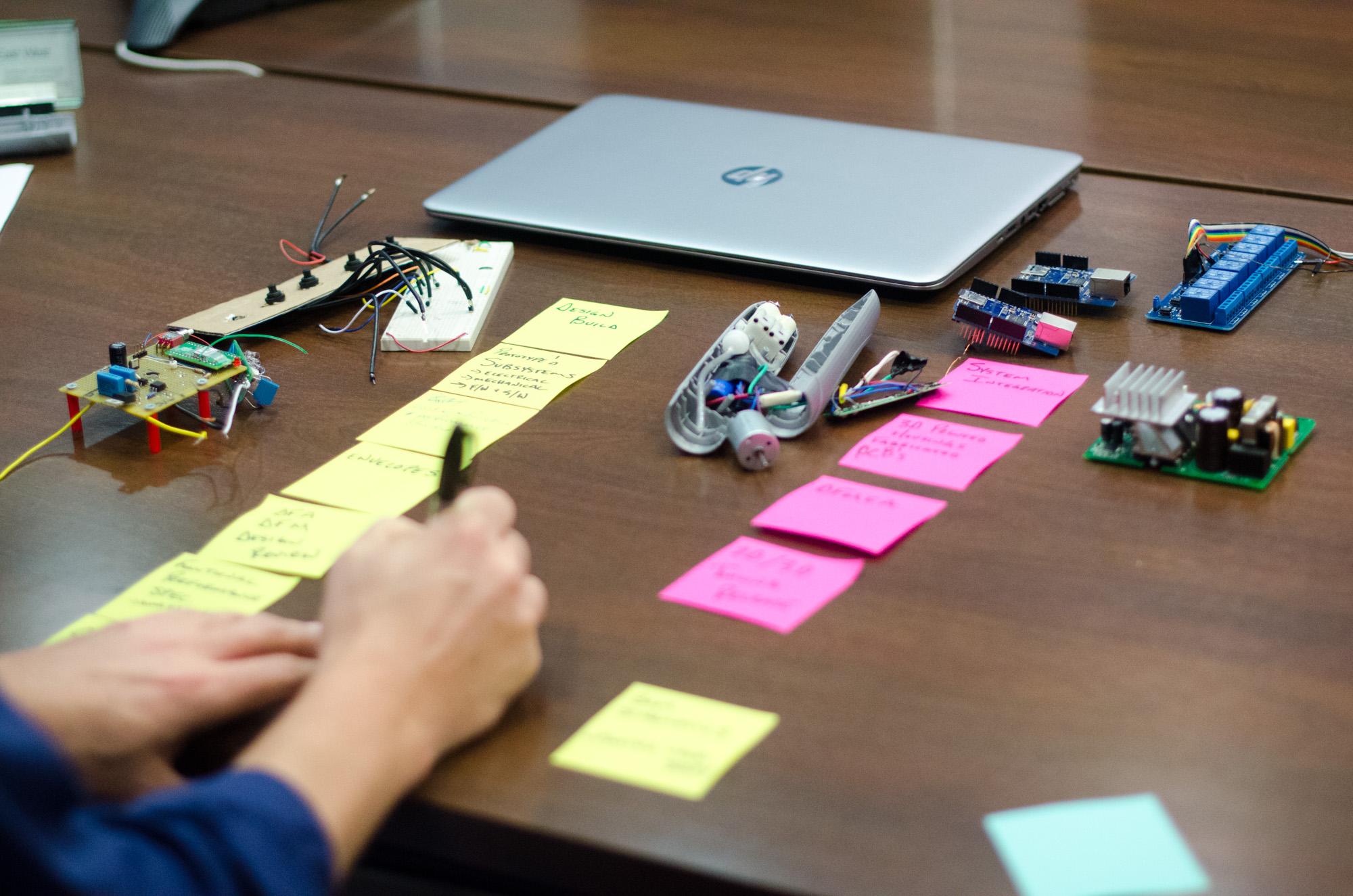
To show off the impressive manufacturing industry in the Capital Region, the Texas Commission on Economic Opportunity (TCEO) has created a new interactive exhibit on the subject. It includes an interesting chart on the manufacturing industry in the area, as well as a plethora of useful information on a variety of topics. The most notable feature is the "Essential Texas", a mobile app that allows visitors to access data about local businesses, tourism and the history of the area. Another cool feature is the virtual visitor's center, where you can learn about the region's most important industries and how they benefit the community.
The interactive exhibit is impressive but you should also check out other TCEO resources. The Capital Region of Texas is one of them. It provides a comprehensive overview of Texas from Llano to San Marcos. Here you will find out how this region has managed to rebound from the national recession, and how it has been successful in attracting new industries. The region is also a good place to start a new career, as it is home to a large pool of qualified and trained candidates. There are many options for part-time and full-time jobs.
The area is home to many of the top technology companies, such as Apple, Dell and Oracle. The capital city is also the home of the Rhythm Superfoods, a natural and organic snack brand. Manufacturing has never been more exciting in this area. The Capital Region is home a diverse group highly skilled and talented individuals.
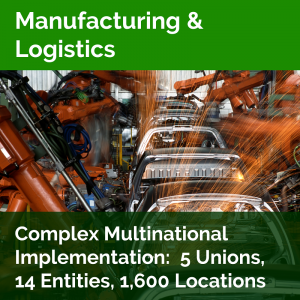
However, the capital city's manufacturing industry isn’t a monopoly. Despite the recession, the region has managed to maintain a strong employment base that has led to more than 65,000 jobs in the manufacturing sector. These jobs are not cheap, and the country's manufacturing achievements surpass them all.
FAQ
What is the job of a production plan?
A production planner makes sure all project elements are delivered on schedule, within budget, as well as within the agreed scope. They ensure that the product or service is of high quality and meets client requirements.
What skills do production planners need?
You must be flexible and organized to become a productive production planner. Effective communication with clients and colleagues is essential.
How can I find out more about manufacturing?
You can learn the most about manufacturing by getting involved in it. But if that is not possible you can always read books and watch educational videos.
How can manufacturing excess production be decreased?
Improved inventory management is the key to reducing overproduction. This would decrease the time that is spent on inefficient activities like purchasing, storing, or maintaining excess stock. By doing this, we could free up resources for other productive tasks.
One way to do this is to adopt a Kanban system. A Kanban Board is a visual display that tracks work progress. Kanban systems are where work items travel through a series of states until reaching their final destination. Each state represents an individual priority level.
As an example, if work is progressing from one stage of the process to another, then the current task is complete and can be transferred to the next. However, if a task is still at the beginning stages, it will remain so until it reaches the end of the process.
This helps to keep work moving forward while ensuring that no work is left behind. Managers can see how much work has been done and the status of each task at any time with a Kanban Board. This information allows them to adjust their workflow based on real-time data.
Another way to control inventory levels is to implement lean manufacturing. Lean manufacturing works to eliminate waste throughout every stage of the production chain. Anything that does not contribute to the product's value is considered waste. Here are some examples of common types.
-
Overproduction
-
Inventory
-
Packaging that is not necessary
-
Overstock materials
These ideas can help manufacturers improve efficiency and reduce costs.
What does warehouse refer to?
Warehouses and storage facilities are where goods are kept before being sold. It can be either an indoor or outdoor space. Sometimes, it can be both an indoor and outdoor space.
Statistics
- According to a Statista study, U.S. businesses spent $1.63 trillion on logistics in 2019, moving goods from origin to end user through various supply chain network segments. (netsuite.com)
- [54][55] These are the top 50 countries by the total value of manufacturing output in US dollars for its noted year according to World Bank.[56] (en.wikipedia.org)
- According to the United Nations Industrial Development Organization (UNIDO), China is the top manufacturer worldwide by 2019 output, producing 28.7% of the total global manufacturing output, followed by the United States, Japan, Germany, and India.[52][53] (en.wikipedia.org)
- (2:04) MTO is a production technique wherein products are customized according to customer specifications, and production only starts after an order is received. (oracle.com)
- It's estimated that 10.8% of the U.S. GDP in 2020 was contributed to manufacturing. (investopedia.com)
External Links
How To
How to use Lean Manufacturing in the production of goods
Lean manufacturing (or lean manufacturing) is a style of management that aims to increase efficiency, reduce waste and improve performance through continuous improvement. It was first developed in Japan in the 1970s/80s by Taiichi Ahno, who was awarded the Toyota Production System (TPS), award from KanjiToyoda, the founder of TPS. The first book published on lean manufacturing was titled "The Machine That Changed the World" written by Michael L. Watkins and published in 1990.
Lean manufacturing, often described as a set and practice of principles, is aimed at improving the quality, speed, cost, and efficiency of products, services, and other activities. It emphasizes eliminating waste and defects throughout the value stream. Lean manufacturing is called just-in-time (JIT), zero defect, total productive maintenance (TPM), or 5S. Lean manufacturing emphasizes reducing non-value-added activities like inspection, rework and waiting.
Lean manufacturing not only improves product quality but also reduces costs. Companies can also achieve their goals faster by reducing employee turnover. Lean manufacturing has been deemed one of the best ways to manage the entire value-chain, including customers, distributors as well retailers and employees. Many industries worldwide use lean manufacturing. Toyota's philosophy has been a key driver of success in many industries, including automobiles and electronics.
Five basic principles of Lean Manufacturing are included in lean manufacturing
-
Define Value - Determine the value that your business brings to society. Also, identify what sets you apart from your competitors.
-
Reduce Waste – Eliminate all activities that don't add value throughout the supply chain.
-
Create Flow: Ensure that the work process flows without interruptions.
-
Standardize and simplify – Make processes as repeatable and consistent as possible.
-
Develop Relationships: Establish personal relationships both with internal and external stakeholders.
Lean manufacturing isn’t new, but it has seen a renewed interest since 2008 due to the global financial crisis. Many companies have adopted lean manufacturing methods to increase their marketability. Many economists believe lean manufacturing will play a major role in economic recovery.
Lean manufacturing is becoming a popular practice in automotive. It has many advantages. These include higher customer satisfaction, lower inventory levels, lower operating expenses, greater productivity, and improved overall safety.
You can apply Lean Manufacturing to virtually any aspect of your organization. It is especially useful for the production aspect of an organization, as it ensures that every step in the value chain is efficient and effective.
There are three types of lean manufacturing.
-
Just-in-Time Manufacturing (JIT): This type of lean manufacturing is commonly referred to as "pull systems." JIT stands for a system where components are assembled on the spot rather than being made in advance. This approach reduces lead time, increases availability and reduces inventory.
-
Zero Defects Manufacturing, (ZDM): ZDM is focused on ensuring that no defective products leave the manufacturing facility. If a part needs to be fixed during the assembly line, it should be repaired rather than scrapped. This is true even for finished products that only require minor repairs prior to shipping.
-
Continuous Improvement: Continuous Improvement aims to improve efficiency by continually identifying problems and making adjustments to eliminate or minimize waste. It involves continuous improvement of processes, people, and tools.