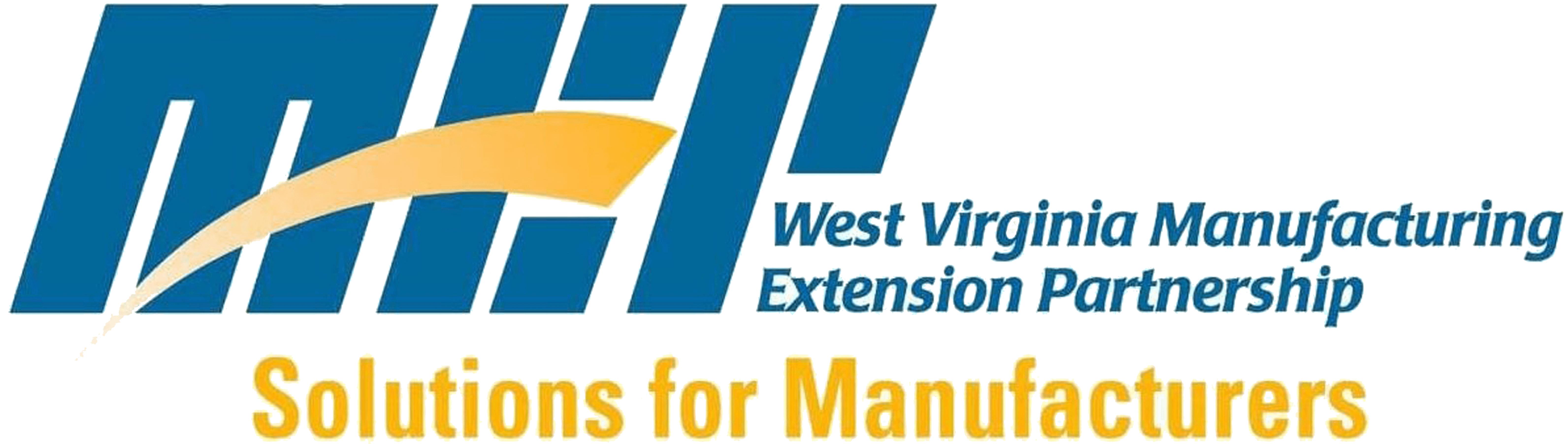
CEVA Logistics provides logistics services. Whether you're looking for a new career or simply need a new place to work, these logistics companies offer a variety of benefits to their employees. Here's how you can apply to a logistics job at one of these companies. First, you can search by location for job opportunities.
Job description
CEVA Logistics offers many jobs to individuals with diverse education and experience. The company's core values revolve around customer service and prompt delivery. The company is looking for people who are enthusiastic about logistics and are willing to work hard. If you have no prior experience in logistics, and if you have a positive attitude, then you will be preferred for the job.
CEVA Logistics is looking for a Process/Industrial engineer to help design, implement and improve new processes. The ideal candidate will be self-driven, energetic, and able collaborate with plant personnel. These tasks include managing projects and designing process layouts. They will need to be skilled in robotics, as well as other manufacturing processes, to improve efficiency and quality.
Education required
CEVA Logistics has many career options for those who are interested in working there. These include warehouse manager and sales rep. You can also choose to be operations supervisors. This involves overseeing all aspects of the company's day, including inventory and scheduling. These positions are often accompanied by a team. These positions require candidates to have a bachelor's degree, supervisory experience, strong management and leadership skills.
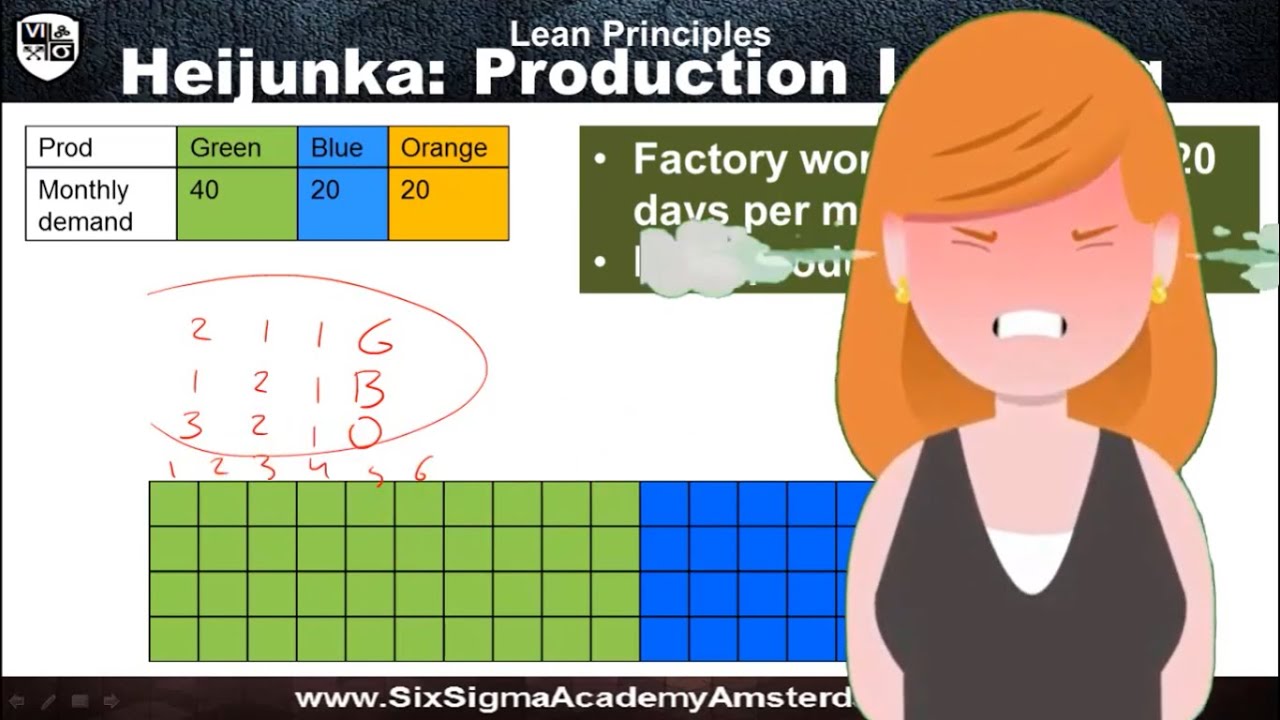
The online application process is easy for interested candidates. To apply online, candidates first need to create a profile with the company's career portal. Candidates can connect to their LinkedIn profiles to create a profile and attach their resumes. After their profile is completed, they can select the region or country that interests them and contact a recruiter.
Salary range
The first step in applying for a CEVA Logistics job is to create an online profile through the company's Career Portal. You can connect to your LinkedIn profile and upload a resume. You can also add information about your qualifications, experience, and other relevant information. Next, select the country or region in which you would like to work. After this step, you will be provided with contact information by a recruiter from that region.
CEVA Logistics's salaries are determined by job title, experience, location, and other factors. A Vice President at CEVA Logistics is paid $166,000 per year, while an Air Break Bulk Specialist receives $24,000. However, salaries can be different in each location, depending on the economic conditions in that area.
Locations
If you're looking for a great career in logistics, consider a position with CEVA Logistics. The company has a number of different positions, each with its own responsibilities and qualifications. To apply for a specific job, just type the job title in search box along with your location. You can search for Edison jobs, NJ. The listings will be for that location. You will need to have some driving experience, be able talk to customers internally and externally, and perform many other tasks.
CEVA Logistics offers many opportunities for career advancement, including supervisory roles. Supervisors manage the company's day-to-day operations. Supervisors manage inventory, coordinate schedules, oversee employees' activities, and monitor their performance. A supervisor of operations typically has a team that reports to him. They usually need a bachelor's degree, or another related experience. Leadership and management skills are essential.
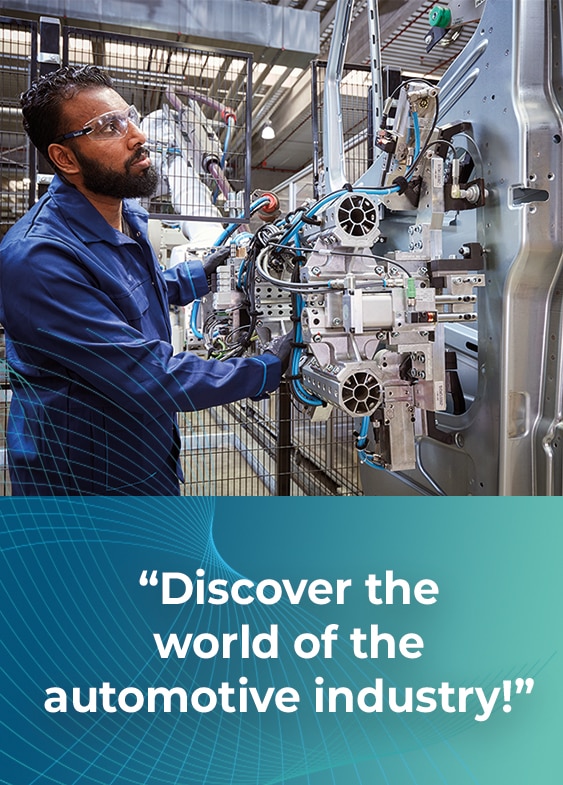
Applying online
CEVA Logistics has a position for you if you are looking for a job within the logistics industry. Ceva Logistics is an international company that was created in 2006 through the merger two Australian and Texan logistics companies. It has more than 9500 employees and operates in over 170 countries. Job seekers are eligible to apply for either full-time or partial-time positions.
While most jobs at CEVA require some prior experience, many positions can be filled as entry-level. Others require minimal to moderate experience. Some of the more entry-level positions include customer service representative, admin clerk, and dispatcher.
FAQ
Why automate your factory?
Modern warehousing has seen automation take center stage. With the rise of ecommerce, there is a greater demand for faster delivery times as well as more efficient processes.
Warehouses have to be flexible to meet changing requirements. Technology is essential for warehouses to be able to adapt quickly to changing needs. Automating warehouses has many benefits. These are some of the benefits that automation can bring to warehouses:
-
Increases throughput/productivity
-
Reduces errors
-
Improves accuracy
-
Safety Boosts
-
Eliminates bottlenecks
-
This allows companies to scale easily
-
This makes workers more productive
-
Gives you visibility into all that is happening in your warehouse
-
Enhances customer experience
-
Improves employee satisfaction
-
Reduces downtime and improves uptime
-
This ensures that quality products are delivered promptly
-
Eliminates human error
-
It ensures compliance with regulations
What are the four types of manufacturing?
Manufacturing is the process by which raw materials are transformed into useful products through machines and processes. It involves many different activities such as designing, building, testing, packaging, shipping, selling, servicing, etc.
What is the role of a manager in manufacturing?
The manufacturing manager should ensure that every manufacturing process is efficient and effective. They should be alert for any potential problems in the company and react accordingly.
They should also learn how to communicate effectively with other departments, including sales and marketing.
They should also be aware of the latest trends in their industry and be able to use this information to help improve productivity and efficiency.
What skills should a production planner have?
A production planner must be organized, flexible, and able multitask to succeed. It is also important to be able communicate with colleagues and clients.
Statistics
- It's estimated that 10.8% of the U.S. GDP in 2020 was contributed to manufacturing. (investopedia.com)
- According to the United Nations Industrial Development Organization (UNIDO), China is the top manufacturer worldwide by 2019 output, producing 28.7% of the total global manufacturing output, followed by the United States, Japan, Germany, and India.[52][53] (en.wikipedia.org)
- In the United States, for example, manufacturing makes up 15% of the economic output. (twi-global.com)
- [54][55] These are the top 50 countries by the total value of manufacturing output in US dollars for its noted year according to World Bank.[56] (en.wikipedia.org)
- In 2021, an estimated 12.1 million Americans work in the manufacturing sector.6 (investopedia.com)
External Links
How To
How to Use Six Sigma in Manufacturing
Six Sigma is "the application statistical process control (SPC), techniques for continuous improvement." Motorola's Quality Improvement Department, Tokyo, Japan, developed it in 1986. Six Sigma is a method to improve quality through standardization and elimination of defects. Since there are no perfect products, or services, this approach has been adopted by many companies over the years. Six Sigma seeks to reduce variation between the mean production value. This means that you can take a sample from your product and then compare its performance to the average to find out how often the process differs from the norm. If this deviation is too big, you know something needs fixing.
The first step toward implementing Six Sigma is understanding how variability works in your business. Once you've understood that, you'll want to identify sources of variation. This will allow you to decide if these variations are random and systematic. Random variations happen when people make errors; systematic variations are caused externally. These are, for instance, random variations that occur when widgets are made and some fall off the production line. It would be considered a systematic problem if every widget that you build falls apart at the same location each time.
Once you've identified the problem areas you need to find solutions. This could mean changing your approach or redesigning the entire process. To verify that the changes have worked, you need to test them again. If they don’t work, you’ll need to go back and rework the plan.