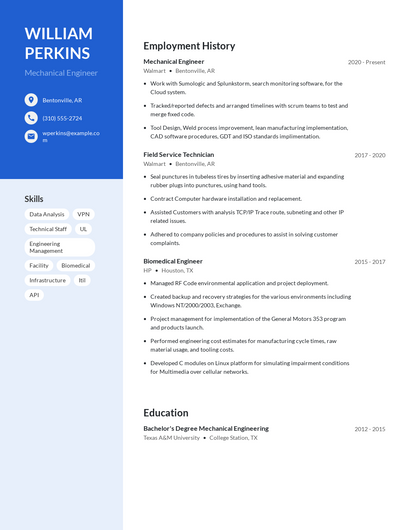
Supply chain management software will help you improve your efficiency and streamline your processes, no matter if you work for a large corporation or small business. These systems offer a centralized view of your entire supply chain, allowing you to plan production, shipment planning, and delivery routes. They allow you to streamline and automate processes, which allows your employees to spend their time on other areas of business. Software for supply chain management is essential to any organization that handles shipping and manufacturing.
You need to consider many features and capabilities when selecting the best supply chain management tool. These features include integration with other applications, scalability, usability, and ease-of-use. You also need to consider the provider's credibility and the features that they offer. Additionally, it is important to find a solution within your budget. No matter whether you are looking for a SaaS option or a full-scale package, you should be able to adapt to your changing needs.
E2open is one of the leading supply chain management software providers, specializing in cloud-based solutions that deliver better demand forecasting and operations management. The company also offers advanced technology and features. The software is designed for businesses in a variety of industries, including retail, transportation, and manufacturing.
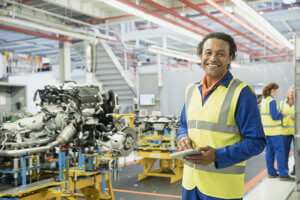
The key feature of supply-chain management software is real time visibility. This allows you track your product inventory and shipments. It will help you make sure your customers have what is needed when they want it. Also, it helps you create long-term strategies to manage demand-supply balancing.
Kinaxis provides a comprehensive supply-chain management software solution. It breaks down silos to streamline processes. It combines human-machine intelligence to enable you to make better decision. It also helps you to plan inventory, capacity, and other resources so you can be more responsive to opportunities.
The sales forecasting software helps you better understand past sales, sales cycles and seasonality. Machine learning is also used to predict sales. This software predicts sales and helps to prepare sales teams for the future. This software also allows you to access data from many sources, making it easier to view the entire picture of your operation.
Descartes Systems Group (the main competitor) is supply chain management software. Many organizations consider them the best vendor. The company boasts over 13,000 users and competes with SAP SCM and Megaventory as well as JDA and Logility.
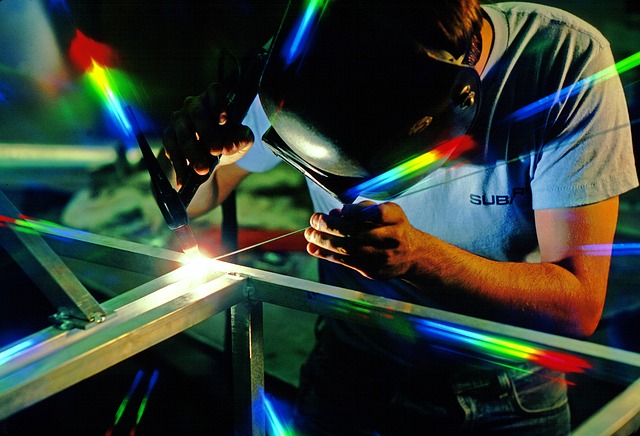
Manhattan Associates is another big competitor in supply chain management software. Manhattan Associates, which has around $617.5 Million in annual revenue, is another software company that has thousands of users. Eddie Capel currently runs it. This company competes against JDA and Logility.
Infor SCM, a supply chain management software platform, is one of the most popular. It is perfect for businesses of all sizes, and it is one of the best-known supply chain management solutions. It is a cloud-based software that unifies enterprise processes from end to end. It also includes analytics at the core, which can help you optimize your end-to-end supply chain.
FAQ
Can we automate some parts of manufacturing?
Yes! Yes! Automation has existed since ancient times. The wheel was invented by the Egyptians thousands of years ago. Today, robots assist in the assembly of lines.
Actually, robotics can be used in manufacturing for many purposes. They include:
-
Assembly line robots
-
Robot welding
-
Robot painting
-
Robotics inspection
-
Robots that make products
Manufacturing can also be automated in many other ways. 3D printing is a way to make custom products quickly and without waiting weeks or months for them to be manufactured.
How can we increase manufacturing efficiency?
First, we need to identify which factors are most critical in affecting production times. Then we need to find ways to improve these factors. If you don’t know how to start, look at which factors have the greatest impact upon production time. Once you have identified them, it is time to identify solutions.
Why is logistics important in manufacturing
Logistics are an essential component of any business. They enable you to achieve outstanding results by helping manage product flow from raw materials through to finished goods.
Logistics are also important in reducing costs and improving efficiency.
What is the difference between Production Planning and Scheduling?
Production Planning (PP) refers to the process of determining how much production is needed at any given moment. Forecasting demand is one way to do this.
Scheduling refers to the process of allocating specific dates to tasks in order that they can be completed within a specified timeframe.
How can I learn about manufacturing?
You can learn the most about manufacturing by getting involved in it. If that is not possible, you could always read books or view educational videos.
How can manufacturing prevent production bottlenecks?
Avoiding production bottlenecks is as simple as keeping all processes running smoothly, from the time an order is received until the product ships.
This includes planning for capacity requirements as well as quality control measures.
Continuous improvement techniques like Six Sigma are the best way to achieve this.
Six Sigma is a management system used to improve quality and reduce waste in every aspect of your organization.
It seeks to eliminate variation and create consistency in your work.
What are the requirements to start a logistics business?
To run a successful logistics company, you need a lot knowledge and skills. Effective communication skills are necessary to work with suppliers and clients. You should be able analyse data and draw inferences. You must be able manage stress and pressure under pressure. You must be creative and innovative to develop new ideas to improve efficiency. You will need strong leadership skills to motivate and direct your team members towards achieving their organizational goals.
It is important to be organized and efficient in order to meet tight deadlines.
Statistics
- Many factories witnessed a 30% increase in output due to the shift to electric motors. (en.wikipedia.org)
- In the United States, for example, manufacturing makes up 15% of the economic output. (twi-global.com)
- [54][55] These are the top 50 countries by the total value of manufacturing output in US dollars for its noted year according to World Bank.[56] (en.wikipedia.org)
- It's estimated that 10.8% of the U.S. GDP in 2020 was contributed to manufacturing. (investopedia.com)
- In 2021, an estimated 12.1 million Americans work in the manufacturing sector.6 (investopedia.com)
External Links
How To
How to Use the Just-In-Time Method in Production
Just-intime (JIT), which is a method to minimize costs and maximize efficiency in business process, is one way. It is a process where you get the right amount of resources at the right moment when they are needed. This means you only pay what you use. Frederick Taylor first coined this term while working in the early 1900s as a foreman. He saw how overtime was paid to workers for work that was delayed. He realized that workers should have enough time to complete their jobs before they begin work. This would help increase productivity.
JIT is an acronym that means you need to plan ahead so you don’t waste your money. Also, you should look at the whole project from start-to-finish and make sure you have the resources necessary to address any issues. If you anticipate that there might be problems, you'll have enough people and equipment to fix them. This will prevent you from spending extra money on unnecessary things.
There are different types of JIT methods:
-
Demand-driven: This type of JIT allows you to order the parts/materials required for your project on a regular basis. This will let you track the amount of material left over after you've used it. This will allow you to calculate how long it will take to make more.
-
Inventory-based: This allows you to store the materials necessary for your projects in advance. This allows you to forecast how much you will sell.
-
Project-driven: This means that you have enough money to pay for your project. You will be able to purchase the right amount of materials if you know what you need.
-
Resource-based JIT: This is the most popular form of JIT. This is where you assign resources based upon demand. For instance, if you have a lot of orders coming in, you'll assign more people to handle them. If you don't receive many orders, then you'll assign fewer employees to handle the load.
-
Cost-based : This is similar in concept to resource-based. But here, you aren't concerned about how many people your company has but how much each individual costs.
-
Price-based: This is very similar to cost-based, except that instead of looking at how much each individual worker costs, you look at the overall price of the company.
-
Material-based is an alternative to cost-based. Instead of looking at the total cost in the company, this method focuses on the average amount of raw materials that you consume.
-
Time-based JIT: A variation on resource-based JIT. Instead of focusing solely on the amount each employee costs, focus on how long it takes for the project to be completed.
-
Quality-based JIT: This is another variation of resource based JIT. Instead of thinking about how much each employee costs or how long it takes to manufacture something, you think about how good the quality of your product is.
-
Value-based JIT: One of the most recent forms of JIT. This is where you don't care about how the products perform or whether they meet customers' expectations. Instead, you focus on the added value that you provide to your market.
-
Stock-based: This inventory-based approach focuses on how many items are being produced at any one time. It's used when you want to maximize production while minimizing inventory.
-
Just-intime (JIT), planning is a combination JIT management and supply chain management. It refers to the process of scheduling the delivery of components as soon as they are ordered. It's important as it reduces leadtimes and increases throughput.