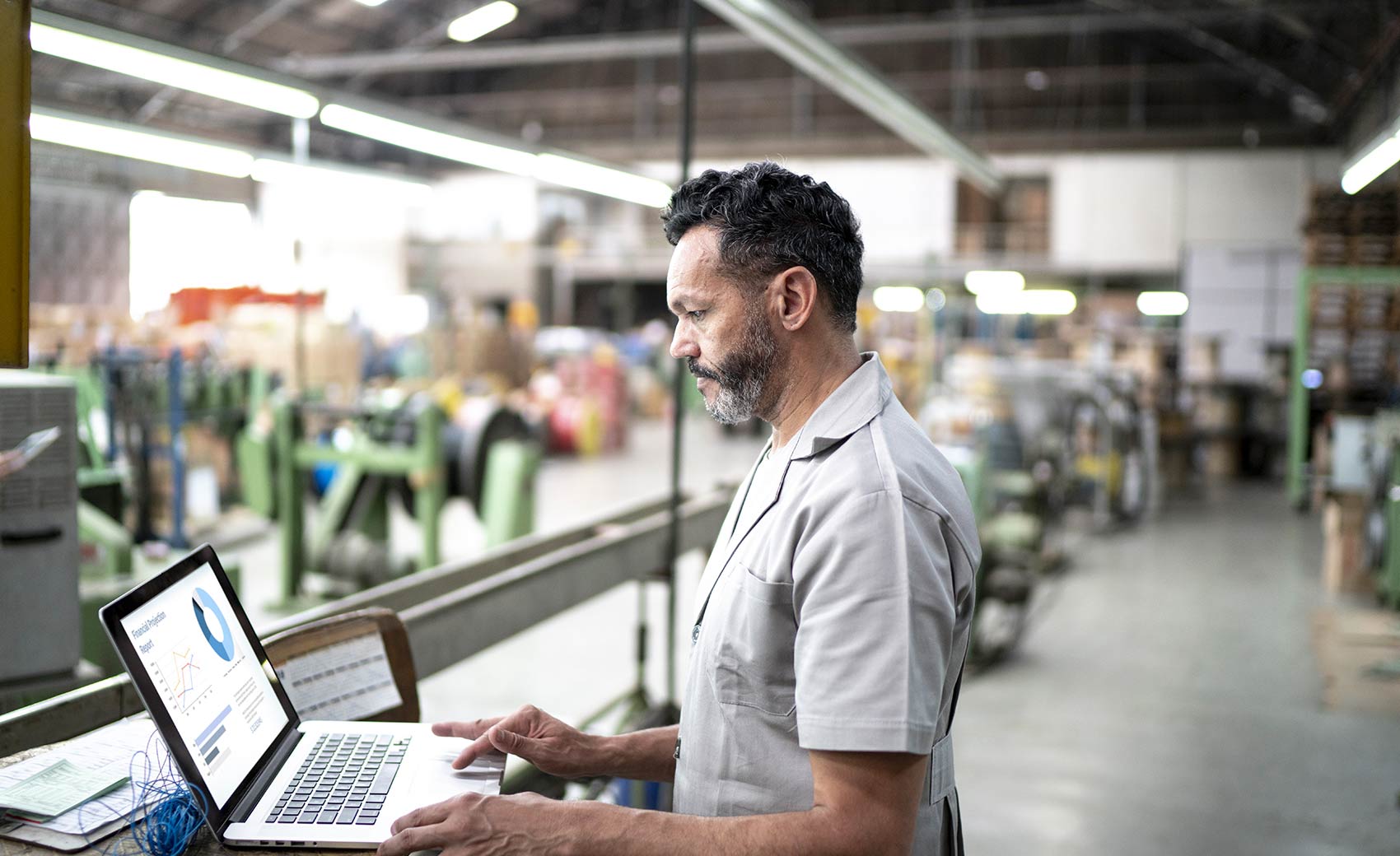
The Defense Industrial Base, or DIB, is a network of nearly 200,000 companies that supplies goods and services to Department of Defense. It includes small businesses as well as large corporations and startups. A new report by the Government Accountability Office outlines the risks the DIB faces and the challenges it faces in addressing them.
Over the past 10 years, the defense industrial base has declined by nearly 40 percent. Accordingly, the Department of Defense is having difficulty recruiting new members to the sector. The Defense Department has attempted to address this problem by making a range of initiatives to encourage new businesses. Despite these attempts, many smaller firms are being left behind. This has created a growing national security risk.
Multiple DOD offices currently work to mitigate the risks associated with the DIB. However, the department has not developed a comprehensive strategy to assess and manage these risks. GAO reviewed several reports and interviewed DOD personnel to determine areas that could be improved. GAO identified five elements which could help the department reach its goals.
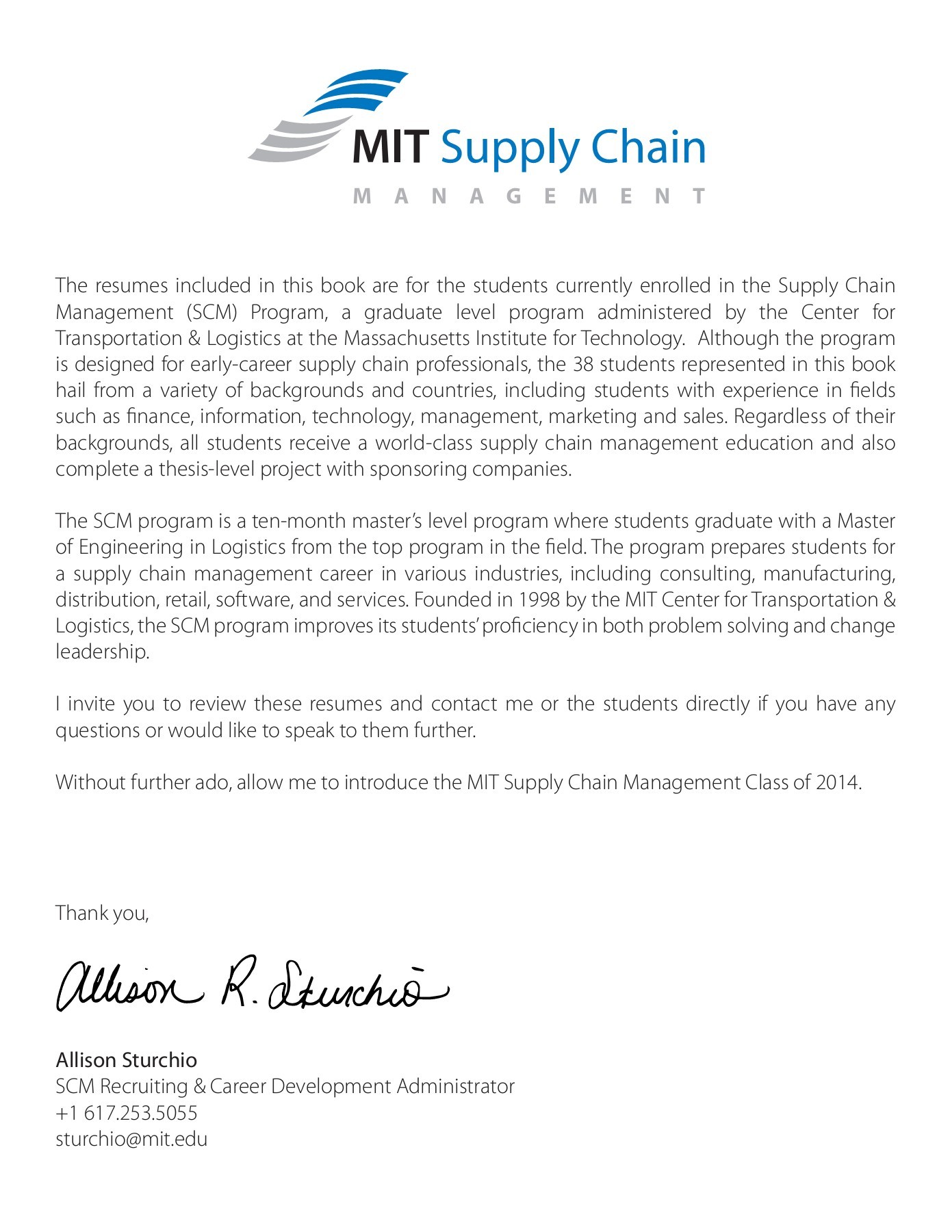
Loss of commercial suppliers will be a concern. Many of these suppliers provide parts for military weapon systems. The industry's small business sector has been declining over the last decade. It is not easy to know how many new companies will enter the market.
Another issue is material shortages, and reliance upon foreign suppliers. Additionally, the military's acquisition process is often slowed by intellectual property restrictions, and there is no standard definition for what is considered a "new entrant" into the defense industrial base.
GAO recommends that the Department of Defense updates its policy on mitigating DIB risks. It is important that the department continues to engage traditional defense contractors, and develop tools that will allow commercial technology providers to gain access to the DoD marketplace. These recommendations should be part a larger strategy to address concerns about the industrial base.
As part of this strategy the Defense Department should think about how its OTAs or CSOs can be utilized to speed up acquisition strategy development. You can restructure the supply chain to achieve dynamic results by using the right people, processes and technologies.
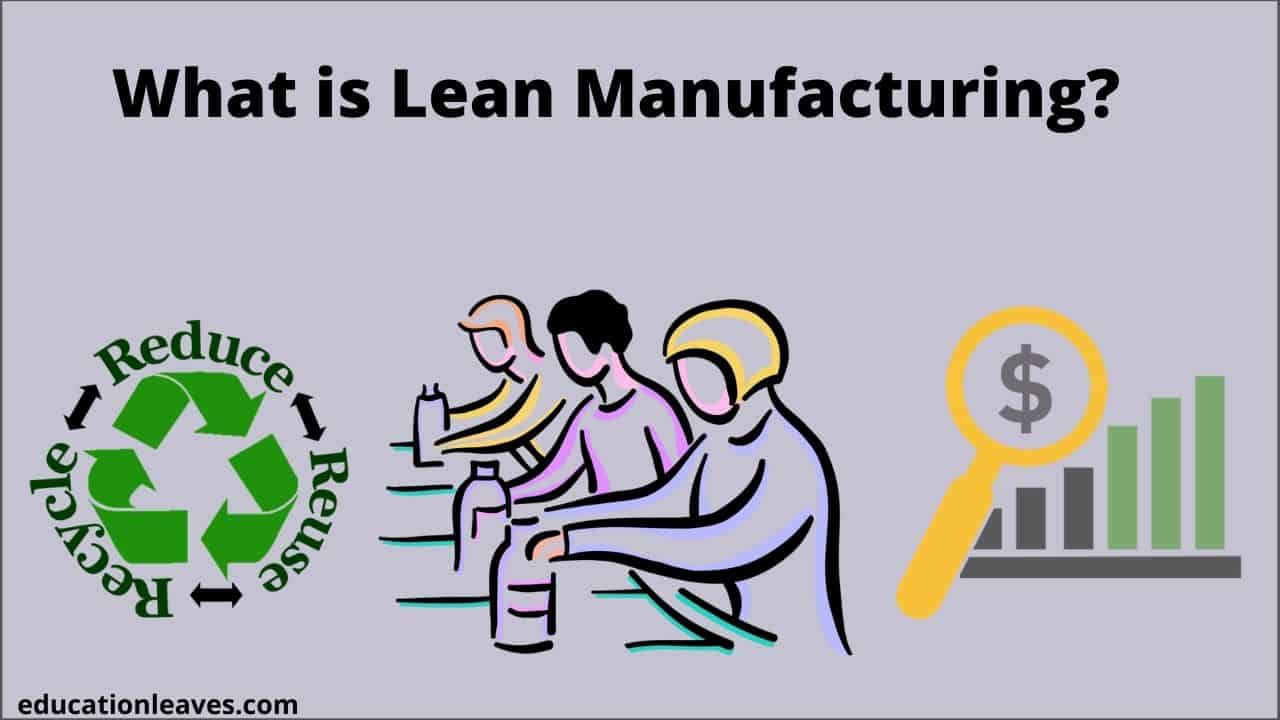
Despite the fact that the number has dropped over the past decade in defense industry, it is still developing. Many companies don't like the Federal Acquisition Regulation (FAR), as it is not easy to follow. A current landscape might make it more difficult for small businesses compete.
Innovation is key for the defense industrial sector. Small businesses and startups play a crucial role. Part of the resilient DIB, companies can support National Security needs while allowing Department of Defense to develop new and better military equipment.
Overall, the defense industrial industry is a complex sector that requires a thorough strategy to ensure that its resources meet the military's requirements. It is vital that the Department of Defense studies best practices in technology integration to ensure more efficient and innovative products.
FAQ
Why automate your factory?
Modern warehouses are increasingly dependent on automation. E-commerce has increased the demand for quicker delivery times and more efficient processes.
Warehouses need to adapt quickly to meet changing needs. They must invest heavily in technology to do this. The benefits of automating warehouses are numerous. Here are some of the reasons automation is worth your investment:
-
Increases throughput/productivity
-
Reduces errors
-
Improves accuracy
-
Safety increases
-
Eliminates bottlenecks
-
Allows companies to scale more easily
-
It makes workers more efficient
-
Gives you visibility into all that is happening in your warehouse
-
Enhances customer experience
-
Improves employee satisfaction
-
Reducing downtime and increasing uptime
-
This ensures that quality products are delivered promptly
-
Removing human error
-
It helps ensure compliance with regulations
What's the difference between Production Planning & Scheduling?
Production Planning (PP), also known as forecasting and identifying production capacities, is the process that determines what product needs to be produced at any particular time. This can be done by forecasting demand and identifying production capabilities.
Scheduling is the process of assigning specific dates to tasks so they can be completed within the specified timeframe.
What does it take for a logistics enterprise to succeed?
It takes a lot of skills and knowledge to run a successful logistics business. Good communication skills are essential to effectively communicate with your suppliers and clients. You must be able analyze data and draw out conclusions. You must be able and able to handle stress situations and work under pressure. In order to innovate and create new ways to improve efficiency, creativity is essential. To motivate and guide your team towards reaching organizational goals, you must have strong leadership skills.
You should also be organized and efficient to meet tight deadlines.
How can manufacturing avoid production bottlenecks
The key to avoiding bottlenecks in production is to keep all processes running smoothly throughout the entire production cycle, from the time you receive an order until the time when the product ships.
This includes both planning for capacity and quality control.
Continuous improvement techniques such Six Sigma can help you achieve this.
Six Sigma is a management system used to improve quality and reduce waste in every aspect of your organization.
It seeks to eliminate variation and create consistency in your work.
Statistics
- You can multiply the result by 100 to get the total percent of monthly overhead. (investopedia.com)
- (2:04) MTO is a production technique wherein products are customized according to customer specifications, and production only starts after an order is received. (oracle.com)
- According to the United Nations Industrial Development Organization (UNIDO), China is the top manufacturer worldwide by 2019 output, producing 28.7% of the total global manufacturing output, followed by the United States, Japan, Germany, and India.[52][53] (en.wikipedia.org)
- [54][55] These are the top 50 countries by the total value of manufacturing output in US dollars for its noted year according to World Bank.[56] (en.wikipedia.org)
- In the United States, for example, manufacturing makes up 15% of the economic output. (twi-global.com)
External Links
How To
How to use the Just-In Time Method in Production
Just-in time (JIT), is a process that reduces costs and increases efficiency in business operations. It's a way to ensure that you get the right resources at just the right time. This means that you only pay the amount you actually use. Frederick Taylor, a 1900s foreman, first coined the term. Taylor observed that overtime was paid to workers if they were late in working. He decided to ensure workers have enough time to do their jobs before starting work to improve productivity.
JIT is about planning ahead. You should have all the necessary resources ready to go so that you don’t waste money. It is important to look at your entire project from beginning to end and ensure that you have enough resources to handle any issues that may arise. You can anticipate problems and have enough equipment and people available to fix them. You won't have to pay more for unnecessary items.
There are many types of JIT methods.
-
Demand-driven: This JIT is where you place regular orders for the parts/materials that are needed for your project. This will allow for you to track the material that you have left after using it. It will also allow you to predict how long it takes to produce more.
-
Inventory-based: This allows you to store the materials necessary for your projects in advance. This allows for you to anticipate how much you can sell.
-
Project-driven: This means that you have enough money to pay for your project. Knowing how much money you have available will help you purchase the correct amount of materials.
-
Resource-based JIT is the most widespread form. Here you can allocate certain resources based purely on demand. You might assign more people to help with orders if there are many. If you don’t have many orders you will assign less people to the work.
-
Cost-based: This is a similar approach to resource-based but you are not only concerned with how many people you have, but also how much each one costs.
-
Price-based: This is very similar to cost-based, except that instead of looking at how much each individual worker costs, you look at the overall price of the company.
-
Material-based is an alternative to cost-based. Instead of looking at the total cost in the company, this method focuses on the average amount of raw materials that you consume.
-
Time-based JIT is another form of resource-based JIT. Instead of focusing on the cost of each employee, you will focus on the time it takes to complete a project.
-
Quality-based JIT - This is another form of resource-based JIT. Instead of looking at the labor costs and time it takes to make a product, think about its quality.
-
Value-based JIT: One of the most recent forms of JIT. This is where you don't care about how the products perform or whether they meet customers' expectations. Instead, you're focused on how much value you add to the market.
-
Stock-based: This stock-based method focuses on the actual quantity of products being made at any given time. This is used to increase production and minimize inventory.
-
Just-intime (JIT), planning is a combination JIT management and supply chain management. It refers to the process of scheduling the delivery of components as soon as they are ordered. It's important as it reduces leadtimes and increases throughput.