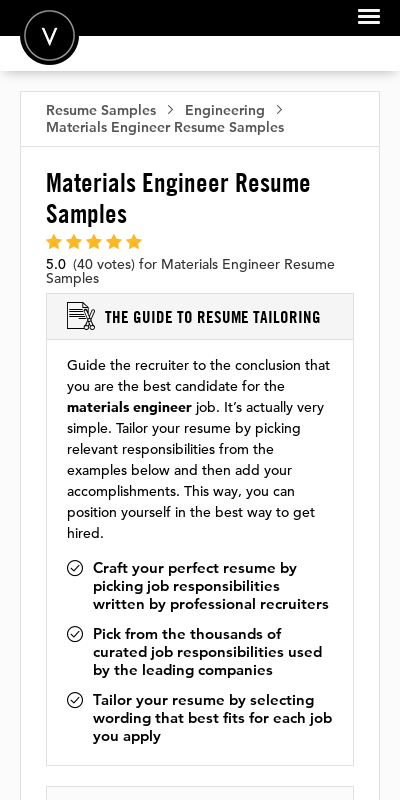
An industrial engineer applies his or her knowledge to improve products and processes by engineering and testing. Industrial engineers use shake tables to test products at different temperatures, humidity, vibrations, and in product development. Failure data is used to improve manufacturing and engineering processes. Simple changes like mold-resistant painting can significantly improve the product's quality and lifespan. Even the smallest of changes can increase a product’s service life, such as lock-washed positioning.
Job description
If you are considering a career as an industrial engineer, you should write your job description carefully. It is the people who are able to combine technical expertise and human intelligence that make industrial engineers the most successful. A well-written job description will help you attract top candidates. You can get some inspiration for a job description by checking out engineering job listings on Monster. You should begin with an enticing intro paragraph that sells the company's benefits to applicants. Your employer must be attractive, regardless of whether you're interested in joining a global brand, an innovative startup, or an open-minded young company that fosters creativity and innovation.
Along with excellent technical skills and communication skills, industrial engineers should also be able to communicate well. Because industrial processes often involve several different departments and personnel, an industrial engineer must know how to work effectively with each of them. The industrial engineer must also be able convince managers and employees that the proposed strategies will improve productivity. Increasing productivity is usually a result of good relationship management. It isn't just technical skills that are essential in the job of an industrial engineer.
Education requirements
For a position in industrial engineering, a degree in math and analytical skills is essential. A strong communication skill is also essential for industrial engineers. They are expected to communicate the results to others. Additionally, industrial engineers must be able and willing to create processes and designs that are cost-effective and reduce labor. This field can also be achieved through education. Here are some of the essential educational requirements for this position.
Industrial engineers need to have a college degree. They also need excellent interpersonal and communication skills. Industrial engineers should also possess strong communication and analytical skills to communicate effectively with business leaders and employees. This occupation requires exceptional problem-solving and leadership skills. Also, industrial engineers need to have high levels of technical proficiency and mechanical aptitude.
Different career options
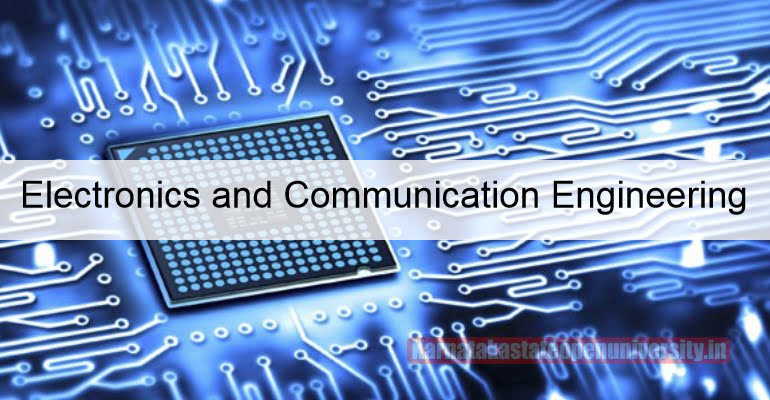
If you're interested in industrial engineering, you have many career options. Industrial engineers typically start in manufacturing. However, there are other options such as hospitals and government agencies. Other possible careers for industrial engineers include the food industry as well as retail trade, professional trade organizations, education agencies, and computer service centres. There are many possible jobs for industrial engineers, but these are the most popular. Read on to find out more about the various career opportunities available to you.
An industrial engineer can focus on getting work done efficiently and effectively. They must balance many factors, including time, workers required, technology available, and the actions that workers need to take. They must also consider safety and environmental concerns. Many industrial engineers also participate in quality assurance and supply chain management. This is important because many industries are constantly trying to cut costs while increasing their productivity. They can also be used to help companies develop new product ideas and improve work flow.
Salary
In 2004 the average Industrial Engineer salary was $87,513 USD, and that figure is expected to increase to $114,146 by 2020. The salary depends on which industry you work in. Salaries in thriving industries are likely to receive larger raises. Industrial Engineers get bonuses that are frequently changing and often moderate. Many bonus recipients are involved with the revenue generation cycle. For this job to be considered for the highest salary, you will need to have an industrial engineering degree.
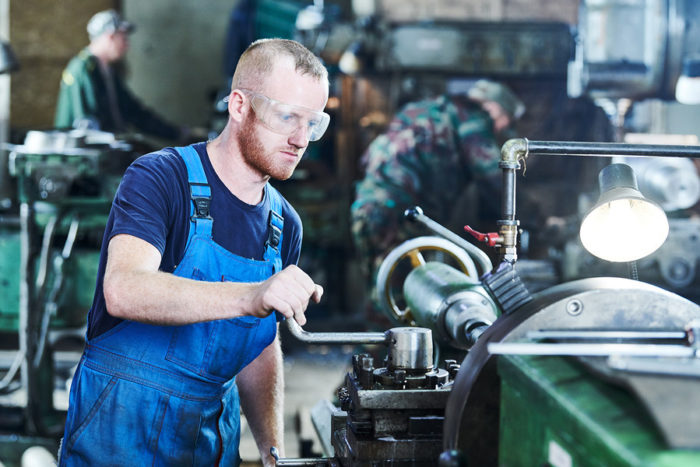
A bachelor's degree is required to be an industrial engineer. Some employers, however, prefer PhDs. An industrial engineer can earn between $56,000 and $121,000 in the U.S. but this amount can vary greatly. Industrial engineers can work in offices, but many jobs require extra time and protective clothing. Because of this, an industrial engineer must be flexible.
FAQ
What are the logistics products?
Logistics refers to the movement of goods from one place to another.
They include all aspects of transport, including packaging, loading, transporting, unloading, storing, warehousing, inventory management, customer service, distribution, returns, and recycling.
Logisticians ensure that products reach the right destination at the right moment and under safe conditions. They assist companies with their supply chain efficiency through information on demand forecasts. Stock levels, production times, and availability.
They also keep track of shipments in transit, monitor quality standards, perform inventories and order replenishment, coordinate with suppliers and vendors, and provide support services for sales and marketing.
Why should you automate your warehouse?
Modern warehouses have become more dependent on automation. The rise of e-commerce has led to increased demand for faster delivery times and more efficient processes.
Warehouses should be able adapt quickly to new needs. To do so, they must invest heavily in technology. The benefits of automating warehouses are numerous. These are some of the benefits that automation can bring to warehouses:
-
Increases throughput/productivity
-
Reduces errors
-
Accuracy is improved
-
Boosts safety
-
Eliminates bottlenecks
-
Companies can scale more easily
-
This makes workers more productive
-
The warehouse can be viewed from all angles.
-
Enhances customer experience
-
Improves employee satisfaction
-
Reduces downtime and improves uptime
-
Ensures quality products are delivered on time
-
Eliminates human error
-
It ensures compliance with regulations
How can I learn about manufacturing?
Practical experience is the best way of learning about manufacturing. If that is not possible, you could always read books or view educational videos.
How can efficiency in manufacturing be improved?
The first step is to identify the most important factors affecting production time. Then we need to find ways to improve these factors. You can start by identifying the most important factors that impact production time. Once you've identified them all, find solutions to each one.
How can overproduction in manufacturing be reduced?
In order to reduce excess production, you need to develop better inventory management methods. This would reduce the time spent on unproductive activities like purchasing, storing and maintaining excess stock. This will allow us to free up resources for more productive tasks.
This can be done by using a Kanban system. A Kanban board, a visual display to show the progress of work, is called a Kanban board. Kanban systems are where work items travel through a series of states until reaching their final destination. Each state has a different priority level.
When work is completed, it can be transferred to the next stage. It is possible to keep a task in the beginning stages until it gets to the end.
This keeps work moving and ensures no work is lost. A Kanban board allows managers to monitor how much work is being completed at any given moment. This data allows them adjust their workflow based upon real-time data.
Another way to control inventory levels is to implement lean manufacturing. Lean manufacturing emphasizes eliminating waste in all phases of production. Anything that doesn't add value to the product is considered waste. The following are examples of common waste types:
-
Overproduction
-
Inventory
-
Unnecessary packaging
-
Material surplus
By implementing these ideas, manufacturers can improve efficiency and cut costs.
Statistics
- You can multiply the result by 100 to get the total percent of monthly overhead. (investopedia.com)
- In 2021, an estimated 12.1 million Americans work in the manufacturing sector.6 (investopedia.com)
- According to the United Nations Industrial Development Organization (UNIDO), China is the top manufacturer worldwide by 2019 output, producing 28.7% of the total global manufacturing output, followed by the United States, Japan, Germany, and India.[52][53] (en.wikipedia.org)
- It's estimated that 10.8% of the U.S. GDP in 2020 was contributed to manufacturing. (investopedia.com)
- In the United States, for example, manufacturing makes up 15% of the economic output. (twi-global.com)
External Links
How To
How to Use Six Sigma in Manufacturing
Six Sigma is "the application statistical process control (SPC), techniques for continuous improvement." Motorola's Quality Improvement Department created Six Sigma at their Tokyo plant, Japan in 1986. Six Sigma's main goal is to improve process quality by standardizing processes and eliminating defects. This method has been adopted by many companies in recent years as they believe there are no perfect products or services. Six Sigma aims to reduce variation in the production's mean value. This means that if you take a sample of your product, then measure its performance against the average, you can find out what percentage of the time the process deviates from the norm. If it is too large, it means that there are problems.
Understanding the nature of variability in your business is the first step to Six Sigma. Once you've understood that, you'll want to identify sources of variation. These variations can also be classified as random or systematic. Random variations are caused by human errors. Systematic variations can be caused by outside factors. For example, if you're making widgets, and some of them fall off the assembly line, those would be considered random variations. However, if you notice that every time you assemble a widget, it always falls apart at exactly the same place, then that would be a systematic problem.
Once you have identified the problem, you can design solutions. You might need to change the way you work or completely redesign the process. To verify that the changes have worked, you need to test them again. If they don't work you need to rework them and come up a better plan.