
Supply chain analytics courses will help you to find your next career or improve your skills in order to keep up with changes in business. It is an integral component of every company's operation. Companies are able to meet customer expectations with the help of data collection and analysis tools.
Learn how to interpret massive amounts of data and identify patterns that could be used in future decisions. Supply chain analytics courses are designed to help you understand the data. It can help identify the most efficient actions, which can lead to more precise and quicker decisions. It can also increase your working capital. It can help you to identify the inventory levels required to provide the services that your customers want. It can help you reduce potential risks.
Global markets are constantly changing, which means that new products and services are continually being developed. A lot of companies are using data to improve supply chain efficiency. It can also aid in forecasting future demand. This course shows you how data mining and predictive analysis can be used to analyze your supply chain. These techniques can help to develop inventory policies and forecast future demand.

The course also explains the components of supply chains and how they can be combined in order to create an integrated system. This includes the logistics planning and export-import procedures as well as containerisation. The course also includes information on inventory management, shipping scheduling, and air cargo administration. The course also covers data cleansing and visualization.
The course also introduces you to the field of machine learning, which uses algorithms to learn patterns from data. This is especially useful in the supply chain industry. It is used to analyze customer segments, and can also be used with Python in order to develop predictive models.
Moreover, the course teaches you about the role of ethics in the supply chain industry, and it covers the key drivers of effective supply chain management. It also provides information on supplier selection and inventory management. It also explains the importance and benefits of flexibility as well as innovation.
You will also gain a better understanding of the importance of data-driven decisions in today's business environment by taking supply chain analytics courses. This will help you make better business decisions and save money. It also gives you the ability to analyze your data to find new ways to improve your organization. This can help your company improve its bottom line and it is an essential part any supply chain management program.
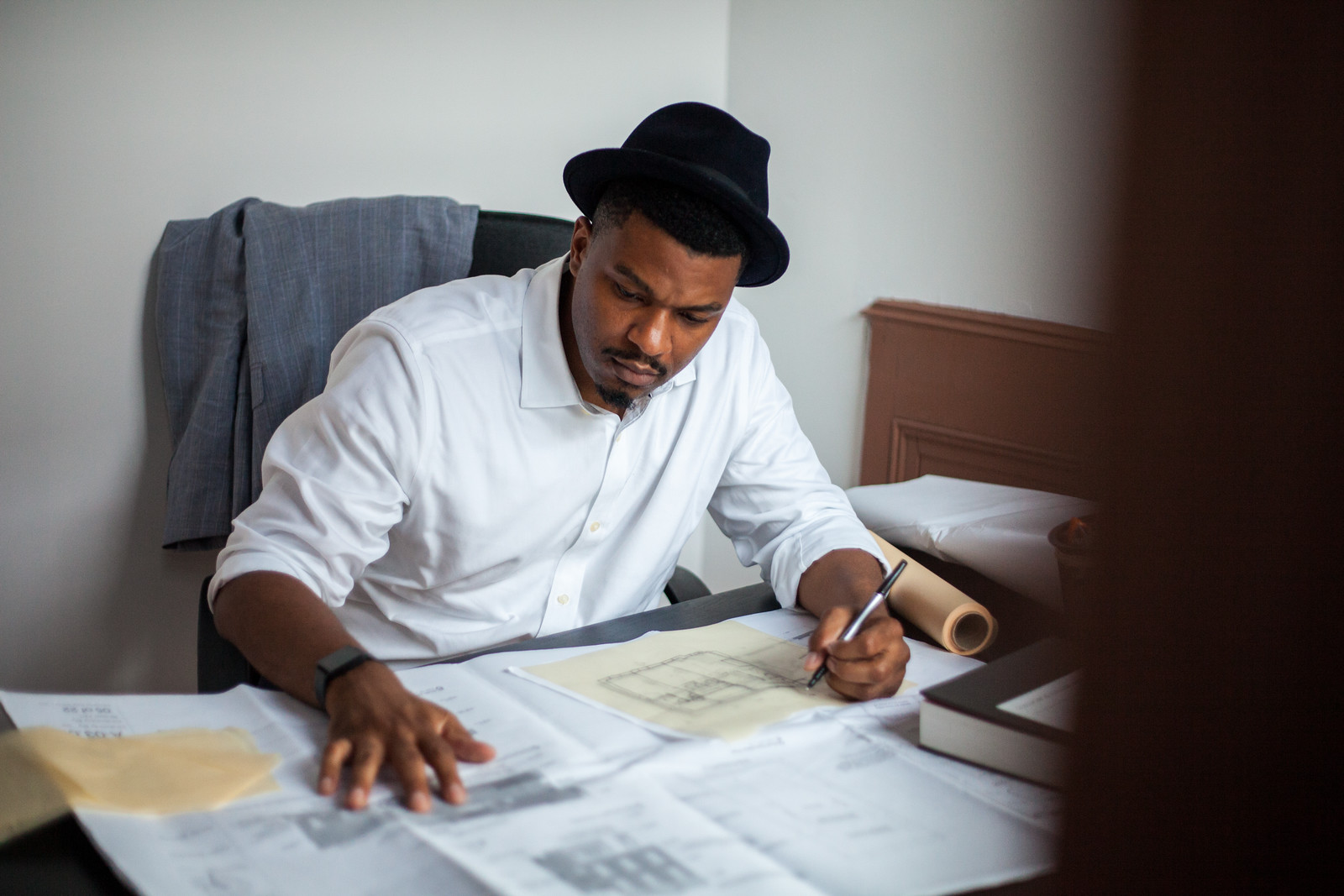
The faculty have real-world experience in supply chains management. It will provide an overview and teach you how to select the right technology for your requirements. It also introduces you to the different models that are used in supply chain management, including the inventory management model. You will also learn about the most common software tools that are used to analyze data, and how to use them to improve supply chain efficiency.
FAQ
Why is logistics so important in manufacturing?
Logistics are an essential part of any business. They are essential to any business's success.
Logistics play an important role in reducing costs as well as increasing efficiency.
What types of jobs can you find in logistics
There are many kinds of jobs available within logistics. Some examples are:
-
Warehouse workers - They load trucks and pallets.
-
Transportation drivers – They drive trucks or trailers to transport goods and perform pick-ups.
-
Freight handlers: They sort and package freight in warehouses.
-
Inventory managers - These are responsible for overseeing the stock of goods in warehouses.
-
Sales representatives - They sell products to customers.
-
Logistics coordinators - They plan and organize logistics operations.
-
Purchasing agents: They are responsible for purchasing goods and services to support company operations.
-
Customer service agents - They answer phone calls and respond to emails.
-
Shipping clerks – They process shipping orders, and issue bills.
-
Order fillers - They fill orders based on what is ordered and shipped.
-
Quality control inspectors – They inspect incoming and outgoing products to ensure that there are no defects.
-
Others – There are many other types available in logistics. They include transport supervisors, cargo specialists and others.
What are the responsibilities for a manufacturing manager
A manufacturing manager has to ensure that all manufacturing processes work efficiently and effectively. They should also be aware of any problems within the company and act accordingly.
They should also be able and comfortable communicating with other departments like sales and marketing.
They should also be aware of the latest trends in their industry and be able to use this information to help improve productivity and efficiency.
What are the differences between these four types?
Manufacturing refers to the transformation of raw materials into useful products by using machines and processes. It involves many different activities such as designing, building, testing, packaging, shipping, selling, servicing, etc.
What skills does a production planner need?
To become a successful production planner, you need to be organized, flexible, and able to multitask. You must also be able to communicate effectively with clients and colleagues.
How can excess manufacturing production be reduced?
It is essential to find better ways to manage inventory to reduce overproduction. This would reduce time spent on activities such as purchasing, stocking, and maintaining excess stock. This will allow us to free up resources for more productive tasks.
This can be done by using a Kanban system. A Kanban board is a visual display used to track work in progress. Kanban systems allow work items to move through different states until they reach their final destination. Each state is assigned a different priority.
To illustrate, work can move from one stage or another when it is complete enough for it to be moved to a new stage. If a task is still in its beginning stages, it will continue to be so until it reaches the end.
This helps to keep work moving forward while ensuring that no work is left behind. With a Kanban board, managers can see exactly how much work is being done at any given moment. This information allows managers to adjust their workflow based off real-time data.
Another way to control inventory levels is to implement lean manufacturing. Lean manufacturing focuses on eliminating waste throughout the entire production chain. Waste includes anything that does not add value to the product. The following are examples of common waste types:
-
Overproduction
-
Inventory
-
Unnecessary packaging
-
Exceed materials
Manufacturers can increase efficiency and decrease costs by implementing these ideas.
Statistics
- According to the United Nations Industrial Development Organization (UNIDO), China is the top manufacturer worldwide by 2019 output, producing 28.7% of the total global manufacturing output, followed by the United States, Japan, Germany, and India.[52][53] (en.wikipedia.org)
- You can multiply the result by 100 to get the total percent of monthly overhead. (investopedia.com)
- [54][55] These are the top 50 countries by the total value of manufacturing output in US dollars for its noted year according to World Bank.[56] (en.wikipedia.org)
- Job #1 is delivering the ordered product according to specifications: color, size, brand, and quantity. (netsuite.com)
- (2:04) MTO is a production technique wherein products are customized according to customer specifications, and production only starts after an order is received. (oracle.com)
External Links
How To
Six Sigma in Manufacturing:
Six Sigma refers to "the application and control of statistical processes (SPC) techniques in order to achieve continuous improvement." Motorola's Quality Improvement Department developed it at their Tokyo plant in Japan in 1986. Six Sigma's basic concept is to improve quality and eliminate defects through standardization. Since there are no perfect products, or services, this approach has been adopted by many companies over the years. Six Sigma seeks to reduce variation between the mean production value. You can calculate the percentage of deviation from the norm by taking a sample of your product and comparing it to the average. If the deviation is excessive, it's likely that something needs to be fixed.
Understanding how your business' variability is a key step towards Six Sigma implementation is the first. Once you understand that, it is time to identify the sources of variation. It is important to identify whether the variations are random or systemic. Random variations happen when people make errors; systematic variations are caused externally. For example, if you're making widgets, and some of them fall off the assembly line, those would be considered random variations. You might notice that your widgets always fall apart at the same place every time you put them together.
Once you identify the problem areas, it is time to create solutions. You might need to change the way you work or completely redesign the process. You should then test the changes again after they have been implemented. If they don't work, you will need to go back to the drawing boards and create a new plan.