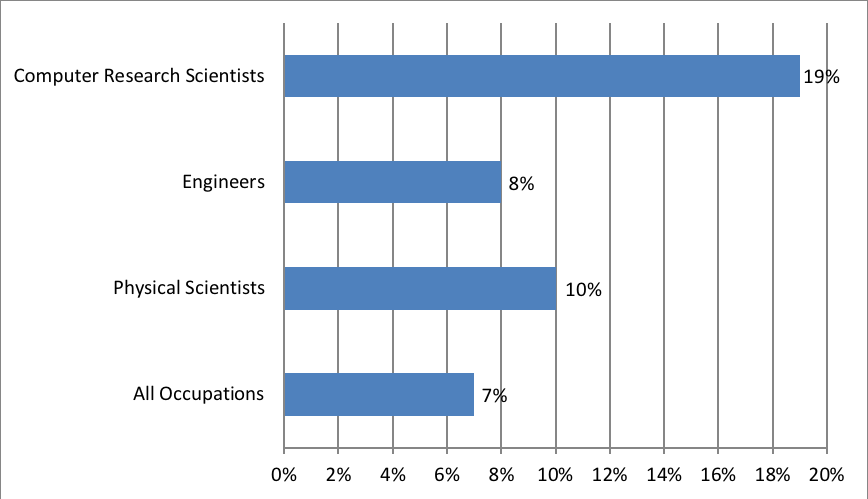
Materials Scientists are responsible for studying the properties of metals and ceramics. You are responsible for determining how to improve, develop and apply these materials in various applications. You might also be responsible to design new products or process. Although you will be working independently, you will sometimes need to work alongside other professionals to ensure the success of your ideas.
A bachelor's degree in a related field is necessary to begin a career as Materials Scientist. While most people are able to enter the field with a basic bachelor's degree, employers often prefer candidates with a master's and even a PhD. The salary you can expect as a Materials Scientist depends on your education, skills, and experience. A master's degree, for example in chemistry, will raise your salary. Also, a PhD degree in process engineering could lead to a greater salary.
Materials scientists often collaborate closely with engineers. They study the physical and chemical properties of materials to discover new ways to use them. This might include creating new forms of plastic, or performing experiments to verify the strength bonds between molecules. A solid understanding of the material's properties will allow you to design more practical products for many different purposes.
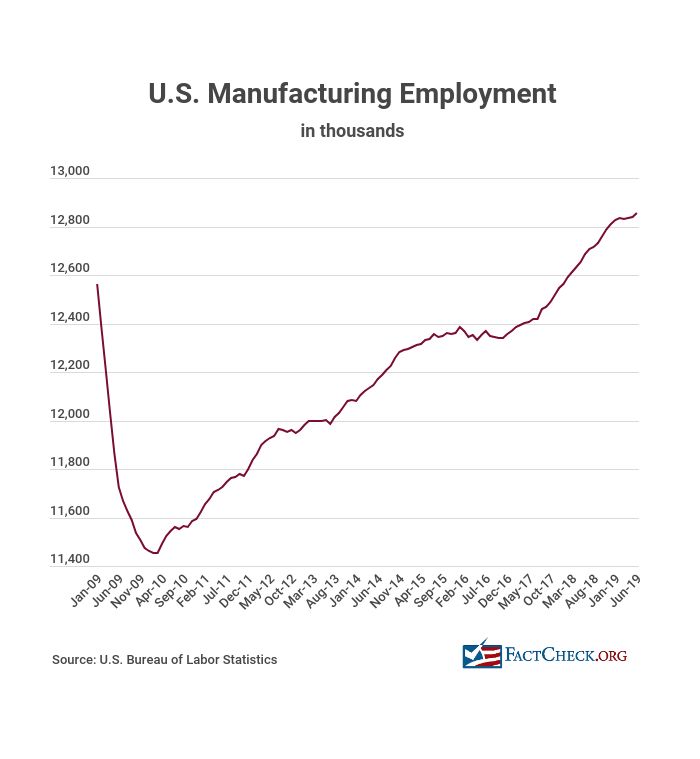
As a Materials Scientist, you will have to demonstrate your ability to understand and communicate the benefits of materials. In addition, you will need to demonstrate your ability to solve problems. Throughout your career, you will need to learn and improve your skills to stay on top of the latest research advancements in your field.
A solid background in computer modeling is also necessary. This will enable you to collaborate better with other professionals. Also, it is vital that you possess a number of technical skills, such as the ability to work with machinery, analyze and interpret technical documents, and use software.
As a Materials Scientist, you can expect to make a salary between $35,000 and $180,000. There is a wide range of salaries, but the top 83 percent of Materials Scientists earn at least $180,000. California, New York, Vermont, and Vermont have the highest salaries. In addition, a Materials Scientist in Italy can expect a salary that averages 8% per year.
According to the Bureau of Labor Statistics (BLS), the employment of Materials Scientists is projected to grow at a rate of 3 percent from 2019 to 2029. Although the expected growth rate is not very high, it will still exceed the national average. There will be around 7,500 jobs by the end of this decade.
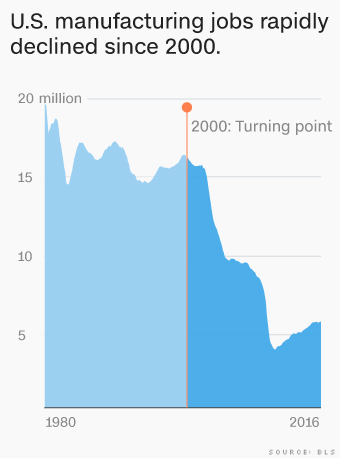
Materials scientists often work with other specialists to develop products and solutions that are more effective. This includes working closely with environmental experts to understand how certain chemicals impact the Earth and human activity. These experts will often be responsible for the development of new technologies.
FAQ
What are the requirements to start a logistics business?
It takes a lot of skills and knowledge to run a successful logistics business. To communicate effectively with clients and suppliers, you must be able to communicate well. You must be able analyze data and draw out conclusions. You must be able to work well under pressure and handle stressful situations. You must be creative and innovative to develop new ideas to improve efficiency. Strong leadership qualities are essential to motivate your team and help them achieve their organizational goals.
You must be organized to meet tight deadlines.
Why automate your factory?
Modern warehousing has seen automation take center stage. Increased demand for efficient and faster delivery has resulted in a rise in e-commerce.
Warehouses must adapt quickly to meet changing customer needs. Technology is essential for warehouses to be able to adapt quickly to changing needs. The benefits of automating warehouses are numerous. These are some of the benefits that automation can bring to warehouses:
-
Increases throughput/productivity
-
Reduces errors
-
Increases accuracy
-
Safety Boosts
-
Eliminates bottlenecks
-
Allows companies scale more easily
-
Increases efficiency of workers
-
The warehouse can be viewed from all angles.
-
Enhances customer experience
-
Improves employee satisfaction
-
Minimizes downtime and increases uptime
-
This ensures that quality products are delivered promptly
-
Removing human error
-
It ensures compliance with regulations
What are the differences between these four types?
Manufacturing is the process that transforms raw materials into useful products. Manufacturing can include many activities such as designing and building, testing, packaging shipping, selling, servicing, and other related activities.
What are the products and services of logistics?
Logistics refers to all activities that involve moving goods from A to B.
They encompass all aspects transport, including packaging and loading, transporting, storage, unloading.
Logisticians make sure that the right product arrives at the right place at the correct time and in safe conditions. Logisticians help companies improve their supply chain efficiency by providing information about demand forecasts and stock levels, production schedules, as well as availability of raw materials.
They can also track shipments in transit and monitor quality standards.
Can certain manufacturing steps be automated?
Yes! Yes. The Egyptians discovered the wheel thousands and years ago. Today, robots assist in the assembly of lines.
Robotics is used in many manufacturing processes today. These include:
-
Automated assembly line robots
-
Robot welding
-
Robot painting
-
Robotics inspection
-
Robots that create products
Automation can be applied to manufacturing in many other ways. 3D printing, for example, allows us to create custom products without waiting for them to be made.
How can we reduce manufacturing overproduction?
In order to reduce excess production, you need to develop better inventory management methods. This would decrease the time that is spent on inefficient activities like purchasing, storing, or maintaining excess stock. By doing this, we could free up resources for other productive tasks.
One way to do this is to adopt a Kanban system. A Kanban board, a visual display to show the progress of work, is called a Kanban board. Work items are moved through various states to reach their destination in a Kanban system. Each state represents an individual priority level.
If work is moving from one stage to the other, then the current task can be completed and moved on to the next. But if a task remains in the beginning stages it will stay that way until it reaches its end.
This helps to keep work moving forward while ensuring that no work is left behind. Managers can see how much work has been done and the status of each task at any time with a Kanban Board. This allows them the ability to adjust their workflow using real-time data.
Lean manufacturing can also be used to reduce inventory levels. Lean manufacturing focuses on eliminating waste throughout the entire production chain. Anything that does not contribute to the product's value is considered waste. These are some of the most common types.
-
Overproduction
-
Inventory
-
Packaging that is not necessary
-
Exceed materials
These ideas will help manufacturers increase efficiency and lower costs.
Statistics
- According to a Statista study, U.S. businesses spent $1.63 trillion on logistics in 2019, moving goods from origin to end user through various supply chain network segments. (netsuite.com)
- Many factories witnessed a 30% increase in output due to the shift to electric motors. (en.wikipedia.org)
- In the United States, for example, manufacturing makes up 15% of the economic output. (twi-global.com)
- In 2021, an estimated 12.1 million Americans work in the manufacturing sector.6 (investopedia.com)
- It's estimated that 10.8% of the U.S. GDP in 2020 was contributed to manufacturing. (investopedia.com)
External Links
How To
How to Use lean manufacturing in the Production of Goods
Lean manufacturing (or lean manufacturing) is a style of management that aims to increase efficiency, reduce waste and improve performance through continuous improvement. It was first developed in Japan in the 1970s/80s by Taiichi Ahno, who was awarded the Toyota Production System (TPS), award from KanjiToyoda, the founder of TPS. The first book published on lean manufacturing was titled "The Machine That Changed the World" written by Michael L. Watkins and published in 1990.
Lean manufacturing is often described as a set if principles that help improve the quality and speed of products and services. It is about eliminating defects and waste from all stages of the value stream. Lean manufacturing is also known as just in time (JIT), zero defect total productive maintenance(TPM), and five-star (S). Lean manufacturing eliminates non-value-added tasks like inspection, rework, waiting.
Lean manufacturing not only improves product quality but also reduces costs. Companies can also achieve their goals faster by reducing employee turnover. Lean Manufacturing is one of the most efficient ways to manage the entire value chains, including suppliers and customers as well distributors and retailers. Lean manufacturing is widely practiced in many industries around the world. Toyota's philosophy, for example, is what has enabled it to be successful in electronics, automobiles, medical devices, healthcare and chemical engineering as well as paper and food.
Five principles are the basis of lean manufacturing:
-
Define value - Find out what your business contributes to society, and what makes it different from other competitors.
-
Reduce Waste - Eliminate any activity that doesn't add value along the supply chain.
-
Create Flow. Ensure that your work is uninterrupted and flows seamlessly.
-
Standardize and simplify - Make your processes as consistent as possible.
-
Build relationships - Develop and maintain personal relationships with both your internal and external stakeholders.
Lean manufacturing isn’t new, but it has seen a renewed interest since 2008 due to the global financial crisis. Many businesses are now using lean manufacturing to improve their competitiveness. In fact, some economists believe that lean manufacturing will be an important factor in economic recovery.
Lean manufacturing, which has many benefits, is now a standard practice in the automotive industry. These include higher customer satisfaction levels, reduced inventory levels as well as lower operating costs.
It can be applied to any aspect of an organisation. Because it makes sure that all value chains are efficient and effectively managed, Lean Manufacturing is particularly helpful for organizations.
There are three main types in lean manufacturing
-
Just-in Time Manufacturing, (JIT): This kind of lean manufacturing is also commonly known as "pull-systems." JIT is a process in which components can be assembled at the point they are needed, instead of being made ahead of time. This approach reduces lead time, increases availability and reduces inventory.
-
Zero Defects Manufacturing: ZDM ensures that no defective units leave the manufacturing plant. Repairing a part that is damaged during assembly should be done, not scrapping. This applies to finished goods that may require minor repairs before shipment.
-
Continuous Improvement (CI: Continuous improvement aims to increase the efficiency of operations by constantly identifying and making improvements to reduce or eliminate waste. Continuous Improvement (CI) involves continuous improvement in processes, people, tools, and infrastructure.