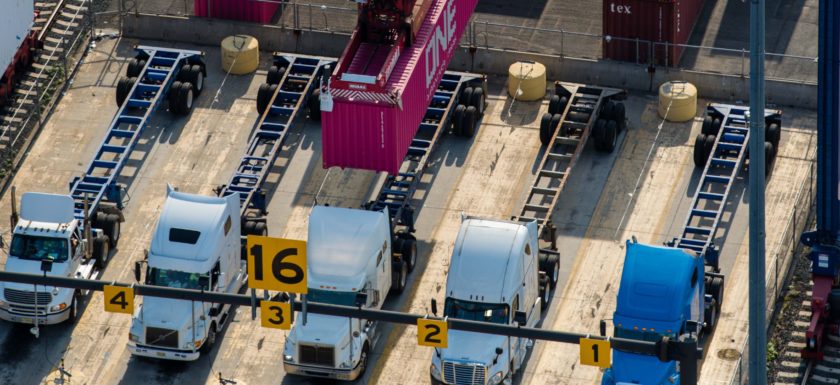
A blue collar job is generally a manual labor job. These jobs can be found in construction, manufacturing or hospitality. Some jobs require some skill, like a plumber or electrician. Others may need to be learned by others. Blue collar jobs tend to pay decent salaries and offer good career growth.
The Fourth Industrial Revolution is redefining the job market for manual workers. This revolution includes artificial intelligence and robotics, as well as machine learning and 3D printing. For companies to succeed, it will require a skilled workforce. This will require companies to move away from transactional relationships and towards more long-lasting ones.
As a result, companies are forced to hire workers from outside of the United States. These workers might be hired to make per-item payment in some cases. Other workers may be paid directly by the project. Blue collar jobs are on the rise, which is positive in all cases.
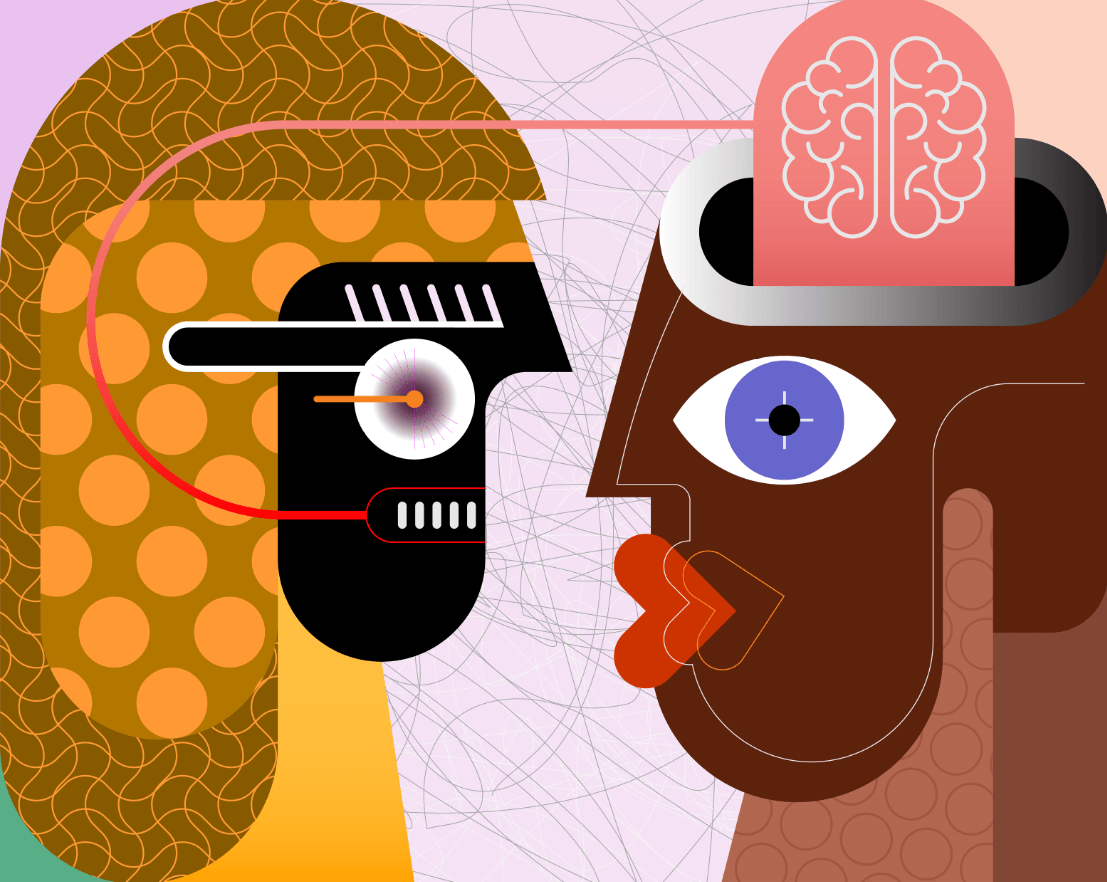
These jobs require some physical labor, but they are often better-paid than white collar work. These jobs are an excellent source of income and many companies will invest in training their staff. These jobs include signal and track switch operators, electrical and electronic repairers and nuclear power reactor operator. These jobs require only a high school diploma, while others require on-the-job training.
Also, blue collar jobs are more common than white collar jobs. In fact, blue collar workers make up a substantial part of the Indian workforce. India has 210million workers in agriculture, while 290million are employed in non-agricultural sectors. The demand for blue-collar workers is increasing at an alarming rate.
Companies will also be able to manage their blue-collar employees differently thanks to the Fourth Industrial Revolution. Not only are digital jobs replacing manual ones, but firms are also moving away form transactional relationships and toward lasting ones. Firms can create stronger relationships and better productivity by prioritizing their employees.
Although blue collar workers are highly in demand, they have to face competing realities. They may be worried about the stability of their jobs, or about retiring. Blue collar workers can be optimistic about their prospects, regardless of any concerns. Blue-collar worker's saving for retirement is increasing. As the economy recovers, blue-collar jobs are expected to rise in popularity.
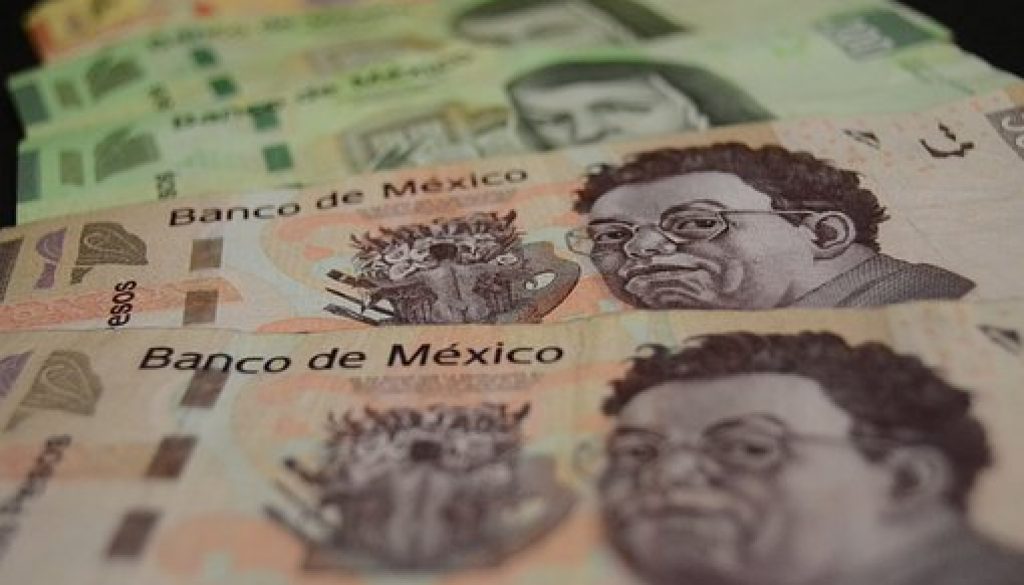
These jobs are not at risk from automation. In fact, the Association for Manufacturing Technology found that for every job that was replaced by technology, five new jobs were created. The biggest salary increase last year went to signal and track switch repairers, who earned $76,210 on average.
In addition to being more lucrative, blue collar positions are also becoming more popular. Blue collar jobs often earn well above the average national wage, which makes them a desirable option for those who are looking for a job that pays well. Many blue collar jobs demand a high level of problem solving skills and can provide excellent career growth opportunities.
FAQ
Is automation important in manufacturing?
Not only is automation important for manufacturers, but it's also vital for service providers. It allows them to offer services faster and more efficiently. It helps them to lower costs by reducing human errors, and improving productivity.
What are the 7 Rs of logistics.
The acronym 7Rs of Logistics refers to the seven core principles of logistics management. It was created by the International Association of Business Logisticians and published in 2004 under its "Seven Principles of Logistics Management".
The following letters form the acronym:
-
Responsible – ensure that all actions are legal and don't cause harm to anyone else.
-
Reliable – have faith in your ability and capability to keep promises.
-
Reasonable - make sure you use your resources well and don't waste them.
-
Realistic – Consider all aspects, including cost-effectiveness as well as environmental impact.
-
Respectful - Treat people fairly and equitably
-
You are resourceful and look for ways to save money while increasing productivity.
-
Recognizable is a company that provides customers with value-added solutions.
What is the responsibility for a logistics manager
Logistics managers are responsible for ensuring that all goods arrive in perfect condition and on time. This is done by using his/her experience and knowledge of the company's products. He/she must also ensure sufficient stock to meet the demand.
Can certain manufacturing steps be automated?
Yes! Since ancient times, automation has been in existence. The Egyptians invented the wheel thousands of years ago. We now use robots to help us with assembly lines.
There are many applications for robotics in manufacturing today. These include:
-
Robots for assembly line
-
Robot welding
-
Robot painting
-
Robotics inspection
-
Robots that produce products
Manufacturing could also benefit from automation in other ways. For instance, 3D printing allows us make custom products and not have to wait for months or even weeks to get them made.
Statistics
- It's estimated that 10.8% of the U.S. GDP in 2020 was contributed to manufacturing. (investopedia.com)
- Job #1 is delivering the ordered product according to specifications: color, size, brand, and quantity. (netsuite.com)
- According to the United Nations Industrial Development Organization (UNIDO), China is the top manufacturer worldwide by 2019 output, producing 28.7% of the total global manufacturing output, followed by the United States, Japan, Germany, and India.[52][53] (en.wikipedia.org)
- [54][55] These are the top 50 countries by the total value of manufacturing output in US dollars for its noted year according to World Bank.[56] (en.wikipedia.org)
- According to a Statista study, U.S. businesses spent $1.63 trillion on logistics in 2019, moving goods from origin to end user through various supply chain network segments. (netsuite.com)
External Links
How To
How to use the Just In-Time Production Method
Just-in time (JIT), is a process that reduces costs and increases efficiency in business operations. It's a way to ensure that you get the right resources at just the right time. This means that only what you use is charged to your account. The term was first coined by Frederick Taylor, who developed his theory while working as a foreman in the early 1900s. He noticed that workers were often paid overtime when they had to work late. He concluded that if workers were given enough time before they start work, productivity would increase.
JIT is a way to plan ahead and make sure you don't waste any money. The entire project should be looked at from start to finish. You need to ensure you have enough resources to tackle any issues that might arise. You'll be prepared to handle any potential problems if you know in advance. You won't have to pay more for unnecessary items.
There are many types of JIT methods.
-
Demand-driven: This JIT is where you place regular orders for the parts/materials that are needed for your project. This will allow you to track how much material you have left over after using it. You'll also be able to estimate how long it will take to produce more.
-
Inventory-based: You stock materials in advance to make your projects easier. This allows for you to anticipate how much you can sell.
-
Project-driven: This is an approach where you set aside enough funds to cover the cost of your project. Once you have an idea of how much material you will need, you can purchase the necessary materials.
-
Resource-based: This is the most common form of JIT. You assign certain resources based off demand. You will, for example, assign more staff to deal with large orders. If you don't have many orders, you'll assign fewer people to handle the workload.
-
Cost-based: This is a similar approach to resource-based but you are not only concerned with how many people you have, but also how much each one costs.
-
Price-based: This is very similar to cost-based, except that instead of looking at how much each individual worker costs, you look at the overall price of the company.
-
Material-based - This is a variant of cost-based. But instead of looking at the total company cost, you focus on how much raw material you spend per year.
-
Time-based JIT: This is another variant of resource-based JIT. Instead of focusing on the cost of each employee, you will focus on the time it takes to complete a project.
-
Quality-based JIT - This is another form of resource-based JIT. Instead of worrying about the costs of each employee or how long it takes for something to be made, you should think about how quality your product is.
-
Value-based JIT is the newest form of JIT. This is where you don't care about how the products perform or whether they meet customers' expectations. Instead, you're focused on how much value you add to the market.
-
Stock-based is an inventory-based system that measures the number of items produced at any given moment. This method is useful when you want to increase production while decreasing inventory.
-
Just-in-time planning (JIT): This is a combination JIT and supply-chain management. It refers to the process of scheduling the delivery of components as soon as they are ordered. It's important because it reduces lead times and increases throughput.