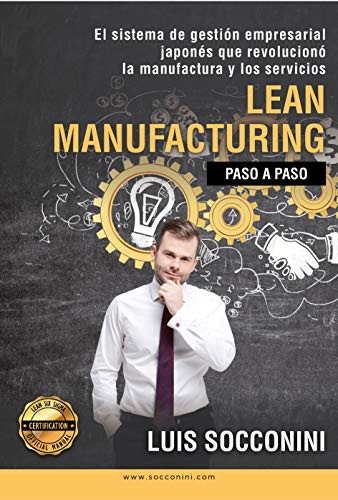
Facilities engineers, also known as maintenance and engineering engineers, provide engineering and support services for buildings and operations. Their duties include implementing and planning procedures, recommending upgrades and repairs, and managing routine and emergency maintenance. This role may include a range of engineering disciplines such as plumbing, electrical, or mechanical. In addition to their technical expertise, they also have a solid understanding of construction law, safety standards, and other regulatory requirements.
Facilities engineers are a great career choice. They can easily move up to senior positions from their entry-level position. The best way to stand out in the field is to build a strong portfolio, which may include engineering projects, research, and articles. Facilities engineers should also continue to learn about their area of expertise. This will allow them to stand out when applying to a new position.
Although it is not mandatory for all facilities engineers, a professional engineer certification can be a big advantage when applying for a new position. Professional engineers should have a solid understanding of engineering concepts and principles, and the ability to interpret data and create compelling presentations. For example, a facility engineer should have experience with predictive maintenance, asset reliability-centered maintenance strategies, and the design of facilities.
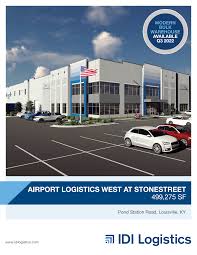
Typical jobs for facility engineers are in office, construction, or manufacturing settings. They implement and oversee processes to ensure that facility utilities systems are safe, efficient and effective. Facilities engineers often work in close collaboration with management and other engineers to help create efficient work schedules, and handle any problems that may arise.
The specific type of facility an engineer is working in will determine the responsibilities. The job requires great time management skills, problem solving abilities, and the ability to interact well with others. In a typical workday, a facilities engineer could perform hundreds upon tasks. The engineer is usually responsible for fixing or troubleshooting problems with electrical, mechanical or plumbing equipment.
Many websites offer information and news about the field, including the Association of Facility Engineers' (AFE) website. You can find a sample resume, salary information, and job-related articles on these websites.
Besides these websites, facilities engineers can read books and articles, attend training courses, and network with other engineers. A successful facilities engineer will have good organizational skills, an excellent understanding of construction and engineering disciplines, as well as a solid knowledge of safety codes and building regulations.
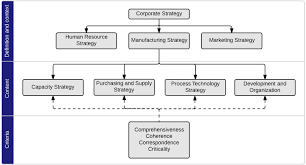
It is important to know that many of the most talented facilities engineers can perform multiple tasks at once and analyze data. They need to be familiar with AutoCAD and other construction methods such as the CAM. You will also benefit from skills such as project management, critical thinking and problem solving.
One of the best things about a job in facilities engineering is the opportunity to work closely with a diverse group of people. These engineers are skilled in working with various materials and are able coordinate the work of other engineers.
FAQ
What is the difference in Production Planning and Scheduling, you ask?
Production Planning (PP), or production planning, is the process by which you determine what products are needed at any given time. This is done through forecasting demand and identifying production capacities.
Scheduling refers to the process of allocating specific dates to tasks in order that they can be completed within a specified timeframe.
How does manufacturing avoid bottlenecks in production?
You can avoid bottlenecks in production by making sure that everything runs smoothly throughout the production cycle, from the moment you receive an order to the moment the product is shipped.
This includes planning for both capacity requirements and quality control measures.
This can be done by using continuous improvement techniques, such as Six Sigma.
Six Sigma can be used to improve the quality and decrease waste in all areas of your company.
It emphasizes consistency and eliminating variance in your work.
What are the products of logistics?
Logistics refers to the movement of goods from one place to another.
They include all aspects associated with transport including packaging, loading transporting, unloading storage, warehousing inventory management customer service, distribution returns and recycling.
Logisticians ensure the product reaches its destination in the most efficient manner. They provide information on demand forecasts as well stock levels, production schedules and availability of raw material.
They keep track and monitor the transit of shipments, maintain quality standards, order replenishment and inventories, coordinate with suppliers, vendors, and provide support for sales and marketing.
What does manufacturing mean?
Manufacturing Industries are companies that manufacture products. Consumers are people who purchase these goods. These companies use a variety processes such as distribution, retailing and management to accomplish their purpose. They create goods from raw materials, using machines and various other equipment. This includes all types and varieties of manufactured goods, such as food items, clothings, building supplies, furnitures, toys, electronics tools, machinery vehicles, pharmaceuticals medical devices, chemicals, among others.
How can efficiency in manufacturing be improved?
The first step is to identify the most important factors affecting production time. We then need to figure out how to improve these variables. You can start by identifying the most important factors that impact production time. Once you have identified them, it is time to identify solutions.
What is production management?
Production Planning refers to the development of a plan for every aspect of production. This document will ensure everything is in order and ready to go when you need it. It should also provide information about how best to produce the best results while on set. It should include information about shooting locations, casting lists, crew details, equipment requirements, and shooting schedules.
First, you need to plan what you want to film. You may have already chosen the location you want, or there are locations or sets you prefer. Once you have identified your locations and scenes it's time to begin figuring out what elements you will need for each one. Perhaps you have decided that you need to buy a car but aren't sure which model. You could look online for cars to see what options are available, and then narrow down your choices by selecting between different makes or models.
After you've found the perfect car, it's time to start thinking about adding extras. Do you need people sitting in the front seats? Maybe you need someone to move around in the back. Perhaps you would like to change the interior colour from black to white. These questions will help you determine the exact look and feel of your car. You can also think about the type of shots you want to get. You will be filming close-ups and wide angles. Maybe the engine or steering wheel is what you are looking to film. These factors will help you determine which car style you want to film.
Once you've determined the above, it is time to start creating a calendar. You will know when you should start and when you should finish shooting. You will need to know when you have to be there, what time you have to leave and when your return home. Everyone will know what they need and when. It is possible to make arrangements in advance for additional staff if you are looking to hire. It is not worth hiring someone who won’t show up because you didn’t tell him.
You will need to factor in the days that you have to film when creating your schedule. Some projects are quick and easy, while others take weeks. While creating your schedule, it is important to remember whether you will require more than one shot per day. Multiple shots at the same location can increase costs and make it more difficult to complete. It is better to be cautious and take fewer shots than you risk losing money if you are not sure if multiple takes are necessary.
Another important aspect of production planning is setting budgets. A realistic budget will help you work within your means. You can always lower the budget if you encounter unexpected problems. You shouldn't underestimate the amount you'll spend. You'll end up with less money after paying for other things if the cost is underestimated.
Planning production is a tedious process. Once you have a good understanding of how everything works together, planning future projects becomes easy.
What are manufacturing & logistics?
Manufacturing is the production of goods using raw materials. Logistics covers all aspects involved in managing supply chains, including procurement and production planning. Logistics and manufacturing are often referred to as one thing. It encompasses both the creation of products and their delivery to customers.
Statistics
- Many factories witnessed a 30% increase in output due to the shift to electric motors. (en.wikipedia.org)
- [54][55] These are the top 50 countries by the total value of manufacturing output in US dollars for its noted year according to World Bank.[56] (en.wikipedia.org)
- According to a Statista study, U.S. businesses spent $1.63 trillion on logistics in 2019, moving goods from origin to end user through various supply chain network segments. (netsuite.com)
- You can multiply the result by 100 to get the total percent of monthly overhead. (investopedia.com)
- It's estimated that 10.8% of the U.S. GDP in 2020 was contributed to manufacturing. (investopedia.com)
External Links
How To
How to Use 5S for Increasing Productivity in Manufacturing
5S stands as "Sort", Set In Order", Standardize", Separate" and "Store". Toyota Motor Corporation developed the 5S method in 1954. It improves the work environment and helps companies to achieve greater efficiency.
The idea behind standardizing production processes is to make them repeatable and measurable. This means that daily tasks such as cleaning and sorting, storage, packing, labeling, and packaging are possible. Because workers know what they can expect, this helps them perform their jobs more efficiently.
Implementing 5S requires five steps. These are Sort, Set In Order, Standardize. Separate. And Store. Each step is a different action that leads to greater efficiency. If you sort items, it makes them easier to find later. When you arrange items, you place them together. Then, after you separate your inventory into groups, you store those groups in containers that are easy to access. Labeling your containers will ensure that everything is correctly labeled.
Employees must be able to critically examine their work practices. Employees must understand why they do certain tasks and decide if there's another way to accomplish them without relying on the old ways of doing things. To be successful in the 5S system, employees will need to acquire new skills and techniques.
The 5S Method not only improves efficiency, but it also helps employees to be more productive and happier. Once they start to notice improvements, they are motivated to keep working towards their goal of increasing efficiency.