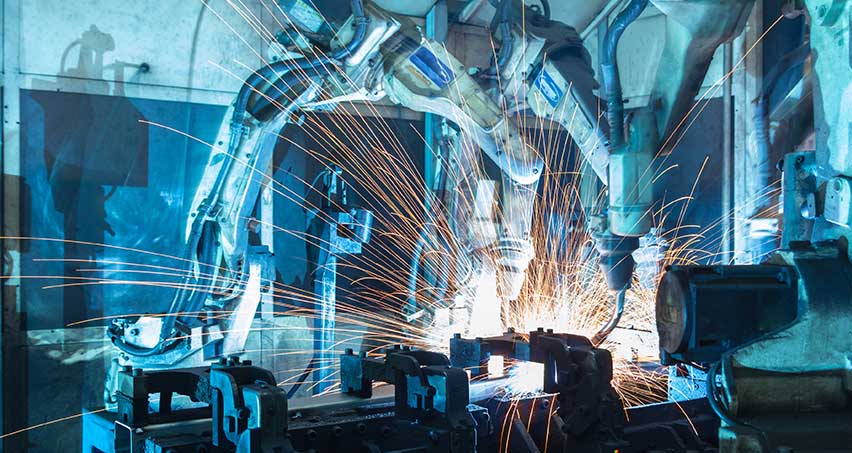
The key elements of bringing back manufacturing to America are reshoring and Opportunity zones, Deregulatory strategy, and lower transportation cost. What can the United States do? Here are a few suggestions:
Reshoring
Companies are shifting production to the U.S., with Intel investing $20 billion to create two new Arizonan semiconductor plants. General Motors is just one company that has started to move its battery production to Michigan. Michigan is poised to become an important hub for lithium-based goods. US Steel is instead building a plant in Alabama and Arkansas, rather than investing $3 billion to build its new steelmaking facility abroad. Other companies that are interested in reshoring include Lockheed, General Electric, or Thermo Fisher.
Opportunity zones
Trump's administration supports opportunity zones enthusiastically. To further support the creation of these zones, it created the White House Opportunity and Revitalization Council. The council has expanded the quoting form and prioritized them. California's local investors are tied in the area of opportunity zones. These are five strategies local investors could use to maximize investment opportunities.
Deregulatory strategy
The United States has been struggling to attract major manufacturing companies for a long time. At the moment, it is losing out to countries like China which subsidizes construction and equipment of new production plants. The tide is changing, however. Walmart, one of the world's largest companies, is increasing its investments in the U.S. and a new study from the Manufacturing Institute has shown that American manufacturing costs are 9 percent less than those in nine other high cost countries.
Transport costs reduced
Reduced transportation costs are one of the main reasons companies move manufacturing to the United States. Companies are able to move manufacturing jobs to the United States because labor costs are less than in other countries. Although moving manufacturing operations to America is not an immediate process, it would take many years to bring the jobs back. The cost of goods will rise, but there would be numerous benefits. Covid-19 was a recent example of supply chain issues being brought to the forefront. Products such as toilet paper and pharmaceuticals were also affected.
Qualified labor
Manufacturing is a key political issue, as has the surprise revelation of recent presidential election results. Commentators said that "U.S. manufacturers is having a moment." Unfortunately, campaign rhetoric does not translate into long-term commitment. Washington D.C. is a place where debates are dominated by trade and other issues, which doesn't directly benefit the manufacturing sector. This is because they don't talk about strategies to strengthen manufacturing communities and clusters.
FAQ
What are the requirements to start a logistics business?
To run a successful logistics company, you need a lot knowledge and skills. Good communication skills are essential to effectively communicate with your suppliers and clients. You will need to know how to interpret data and draw conclusions. You must be able manage stress and pressure under pressure. You need to be innovative and creative to come up with new ways to increase efficiency. Strong leadership qualities are essential to motivate your team and help them achieve their organizational goals.
To meet tight deadlines, you must also be efficient and organized.
What are the responsibilities of a logistic manager?
Logistics managers make sure all goods are delivered on schedule and without damage. This is achieved by using their knowledge and experience with the products of the company. He/she should ensure that sufficient stock is available in order to meet customer demand.
How can we increase manufacturing efficiency?
The first step is to determine the key factors that impact production time. We then need to figure out how to improve these variables. If you don’t know how to start, look at which factors have the greatest impact upon production time. Once you've identified them, try to find solutions for each of those factors.
Statistics
- [54][55] These are the top 50 countries by the total value of manufacturing output in US dollars for its noted year according to World Bank.[56] (en.wikipedia.org)
- Job #1 is delivering the ordered product according to specifications: color, size, brand, and quantity. (netsuite.com)
- In the United States, for example, manufacturing makes up 15% of the economic output. (twi-global.com)
- According to a Statista study, U.S. businesses spent $1.63 trillion on logistics in 2019, moving goods from origin to end user through various supply chain network segments. (netsuite.com)
- According to the United Nations Industrial Development Organization (UNIDO), China is the top manufacturer worldwide by 2019 output, producing 28.7% of the total global manufacturing output, followed by the United States, Japan, Germany, and India.[52][53] (en.wikipedia.org)
External Links
How To
Six Sigma in Manufacturing:
Six Sigma is defined by "the application SPC (statistical process control) techniques to achieve continuous improvements." Motorola's Quality Improvement Department in Tokyo, Japan developed Six Sigma in 1986. Six Sigma's core idea is to improve the quality of processes by standardizing and eliminating defects. Many companies have adopted Six Sigma in recent years because they believe that there are no perfect products and services. Six Sigma aims to reduce variation in the production's mean value. This means that if you take a sample of your product, then measure its performance against the average, you can find out what percentage of the time the process deviates from the norm. If you notice a large deviation, then it is time to fix it.
Understanding how variability works in your company is the first step to Six Sigma. Once you have this understanding, you will need to identify sources and causes of variation. You'll also want to determine whether these variations are random or systematic. Random variations are caused when people make mistakes. While systematic variations are caused outside of the process, they can occur. These are, for instance, random variations that occur when widgets are made and some fall off the production line. You might notice that your widgets always fall apart at the same place every time you put them together.
Once you identify the problem areas, it is time to create solutions. That solution might involve changing the way you do things or redesigning the process altogether. After implementing the new changes, you should test them again to see if they worked. If they don't work you need to rework them and come up a better plan.