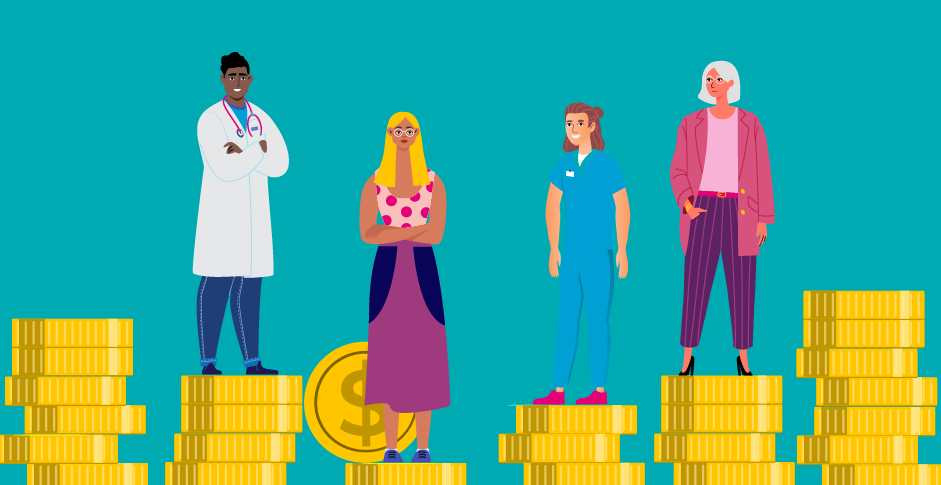
Are you searching for a job as an industrial engineer? Find out what jobs are available by reading on. We'll be discussing the types of jobs and the average salary. We'll also cover the required skills and where to search for them. Next, choose the job that interests you most and apply! Good luck! Before you apply for an industrial engineering job in the future, be sure to read through the job description.
Job description
Industrial engineers aren't for everyone. The job requires the application of engineering principles and technology to improve production layouts and processes in companies. This type of engineer is responsible for developing tools and analytics that help companies monitor their costs and schedules. This engineer reviews production data in order to identify areas for improvement. He or she also compiles equipment lists and material lists. Cost analyses, production cost estimations and purchase orders are all part of his or her responsibilities before implementing new projects.
An engineering degree is required to work as an industrial engineer. A broad understanding of engineering principles and practices is required for this field. An industrial engineer needs to have a good understanding of the human abilities and needs. Industrial engineers must be well organized, be able to use analytical skills and communicate effectively. They are responsible for improving the production process in companies and managing factories and warehouses.
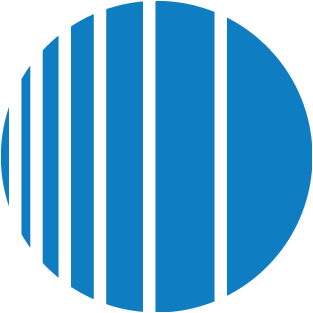
Salary range
The starting salary for industrial engineers is around $85,000, but it varies depending on the experience. The starting salary is around $85,000 but can rise to as high as $100,000 depending on experience. The following table shows the average salary for industrial engineers according to experience. Ventura, California Entry-Level Engineers can expect to earn approximately $86,000 annually. An experienced Industrial Engineer can expect to earn between $85,000- $100,000 annually. As a Project Engineer, you can also be hired. This requires typically a four-year degree.
The average income for an industrial engineer varies according to where you live, your industry, and your years of experience. In New York, industrial engineers can expect to earn from $60,700 to $140,000 annually. Although it is hard to see the upward trend in salaries, national averages have increased by more than 40% over the past 10 years. They are expected to continue rising. Monster's Salary Tool will help you to find out about local salary ranges.
Education required
While licensing may not be required for industrial engineers it is a requirement for government contracts. License is not necessary for industrial engineers. To be eligible for professional licensure, they must have relevant work experience and a degree obtained from an accredited institution. Industrial engineers can be found working in offices, factories, and labs. Many industrial engineers find employment in aerospace product manufacturing, architectural and engineering services, navigational equipment, and medical and control instruments manufacturing.
Many industrial engineers opt to do internships while in college. This can give them valuable experience. While entry-level jobs in industrial engineering do not require professional experience, it can help you gain more experience by working in other engineering positions. Internships might be beneficial if the goal is to work for a government entity or another organization. Along with internships, industrial engineers may need security clearance.
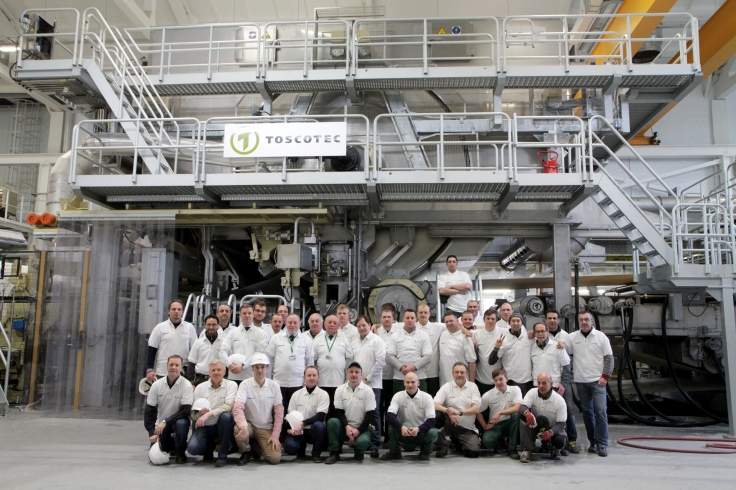
Locations
The variety of industrial engineering jobs available can make you very happy. Entry-level positions in the field typically involve completing calculations, installing monitoring and testing devices, and documenting findings. They might also help develop budgets or track metrics. A lot of standing is required for industrial engineers. Industrial engineers must be able and confident to communicate. In some cases, they work under the supervision of a more senior engineer.
Industrial engineers help companies create efficient production processes using the most energy and resources. Their goal is to improve the efficiency of production and maximize labor efficiency. Industrial engineers work in factories and offices. Their main goal is to improve the operations of businesses. Entry-level positions in industrial engineering require a bachelor's degree in industrial engineering or a related field. The Bureau of Labor Statistics predicts that the median income for industrial engineers in 2021 will be $95,300.
FAQ
What is production planning?
Production Planning refers to the development of a plan for every aspect of production. This document is designed to make sure everything is ready for when you're ready to shoot. You should also have information to ensure the best possible results on set. This includes shooting schedules, locations, cast lists, crew details, and equipment requirements.
The first step is to decide what you want. You may have decided where to shoot or even specific locations you want to use. Once you've identified the locations and scenes you want to use, you can begin to plan what elements you need for each scene. You might decide you need a car, but not sure what make or model. This is where you can look up car models online and narrow down your options by choosing from different makes and models.
After you have chosen the right car, you will be able to begin thinking about accessories. Do you have people who need to be seated in the front seat? Maybe you need someone to move around in the back. You may want to change the interior's color from black or white. These questions can help you decide the right look for your car. You can also think about the type of shots you want to get. Do you want to film close-ups, or wider angles? Maybe you want to show the engine and the steering wheel. These factors will help you determine which car style you want to film.
Once you have made all the necessary decisions, you can start to create a schedule. You will know when you should start and when you should finish shooting. Each day will include the time when you need to arrive at the location, when you need to leave and when you need to return home. It will help everyone know exactly what they have to do and when. Book extra staff ahead of time if you need them. It is not worth hiring someone who won’t show up because you didn’t tell him.
It is important to calculate the amount of filming days when you are creating your schedule. Some projects only take one or two days, while others may last weeks. When creating your schedule, be aware of whether you need more shots per day. Multiple takes at the same place will result in higher costs and longer completion times. It is better to be cautious and take fewer shots than you risk losing money if you are not sure if multiple takes are necessary.
Budget setting is an important part of production planning. It is important to set a realistic budget so you can work within your budget. If you have to reduce your budget due to unexpected circumstances, you can always lower it later. However, you shouldn't overestimate the amount of money you will spend. You'll end up with less money after paying for other things if the cost is underestimated.
Production planning can be a complex process. However, once you know how everything works together it will become easier to plan future projects.
What skills does a production planner need?
A production planner must be organized, flexible, and able multitask to succeed. Effective communication with clients and colleagues is essential.
How can manufacturing efficiency be improved?
The first step is to identify the most important factors affecting production time. Then we need to find ways to improve these factors. If you don't know where to start, then think about which factor(s) have the biggest impact on production time. Once you've identified them all, find solutions to each one.
Statistics
- In 2021, an estimated 12.1 million Americans work in the manufacturing sector.6 (investopedia.com)
- According to a Statista study, U.S. businesses spent $1.63 trillion on logistics in 2019, moving goods from origin to end user through various supply chain network segments. (netsuite.com)
- (2:04) MTO is a production technique wherein products are customized according to customer specifications, and production only starts after an order is received. (oracle.com)
- Many factories witnessed a 30% increase in output due to the shift to electric motors. (en.wikipedia.org)
- According to the United Nations Industrial Development Organization (UNIDO), China is the top manufacturer worldwide by 2019 output, producing 28.7% of the total global manufacturing output, followed by the United States, Japan, Germany, and India.[52][53] (en.wikipedia.org)
External Links
How To
How to Use the Just-In-Time Method in Production
Just-in-time (JIT) is a method that is used to reduce costs and maximize efficiency in business processes. This is where you have the right resources at the right time. This means that only what you use is charged to your account. Frederick Taylor, a 1900s foreman, first coined the term. Taylor observed that overtime was paid to workers if they were late in working. He realized that workers should have enough time to complete their jobs before they begin work. This would help increase productivity.
The idea behind JIT is that you should plan ahead and have everything ready so you don't waste money. You should also look at the entire project from start to finish and make sure that you have sufficient resources available to deal with any problems that arise during the course of your project. If you anticipate that there might be problems, you'll have enough people and equipment to fix them. This will prevent you from spending extra money on unnecessary things.
There are several types of JIT techniques:
-
Demand-driven: This JIT is where you place regular orders for the parts/materials that are needed for your project. This will allow for you to track the material that you have left after using it. This will allow to you estimate the time it will take for more to be produced.
-
Inventory-based: This is a type where you stock the materials required for your projects in advance. This allows one to predict how much they will sell.
-
Project-driven: This is an approach where you set aside enough funds to cover the cost of your project. You will be able to purchase the right amount of materials if you know what you need.
-
Resource-based JIT: This type of JIT is most commonly used. This is where you assign resources based upon demand. For example, if there is a lot of work coming in, you will have more people assigned to them. You'll have fewer orders if you have fewer.
-
Cost-based: This is similar to resource-based, except that here you're not just concerned about how many people you have but how much each person costs.
-
Price-based: This is very similar to cost-based, except that instead of looking at how much each individual worker costs, you look at the overall price of the company.
-
Material-based is an alternative to cost-based. Instead of looking at the total cost in the company, this method focuses on the average amount of raw materials that you consume.
-
Time-based JIT is another form of resource-based JIT. Instead of focusing solely on the amount each employee costs, focus on how long it takes for the project to be completed.
-
Quality-based JIT is another variant of resource-based JIT. Instead of thinking about the cost of each employee or the time it takes to produce something, you focus on how good your product quality.
-
Value-based: This is one of the newest forms of JIT. In this scenario, you're not concerned about how products perform or whether customers expect them to meet their expectations. Instead, you focus on the added value that you provide to your market.
-
Stock-based is an inventory-based system that measures the number of items produced at any given moment. It's useful when you want maximum production and minimal inventory.
-
Just-intime (JIT), planning is a combination JIT management and supply chain management. It refers to the process of scheduling the delivery of components as soon as they are ordered. It reduces lead times and improves throughput.