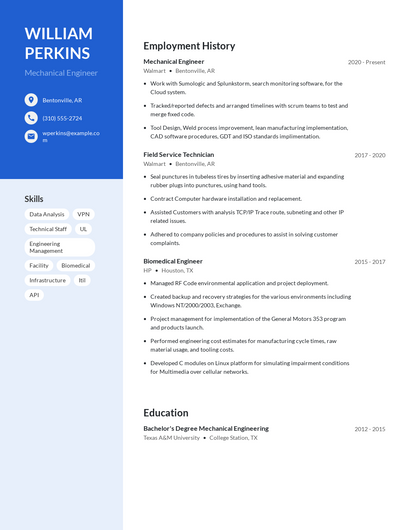
If you're looking to cut costs and improve lead times while minimizing set-up and turnaround time, consider using lean manufacturing. The benefits of lean manufacturing are clear: they reduce costs and lead time while improving the customer experience. These improvements make Lean Manufacturing the best way for your business to grow. You might still be skeptical, but here are three reasons it is the best way to produce products and reduce costs.
Reduces costs
Lean manufacturing can lead to significant efficiencies. Lean manufacturing can help manufacturers save money by reducing labor costs and reducing defects. As a result, labor costs become less of a motivating factor in decision-making. Eliminating hazardous waste is another advantage. The cost of direct labor in many industries is less than 15%. This makes outsourcing to low-cost areas more difficult. This can help reduce manufacturing costs and improve customer service.
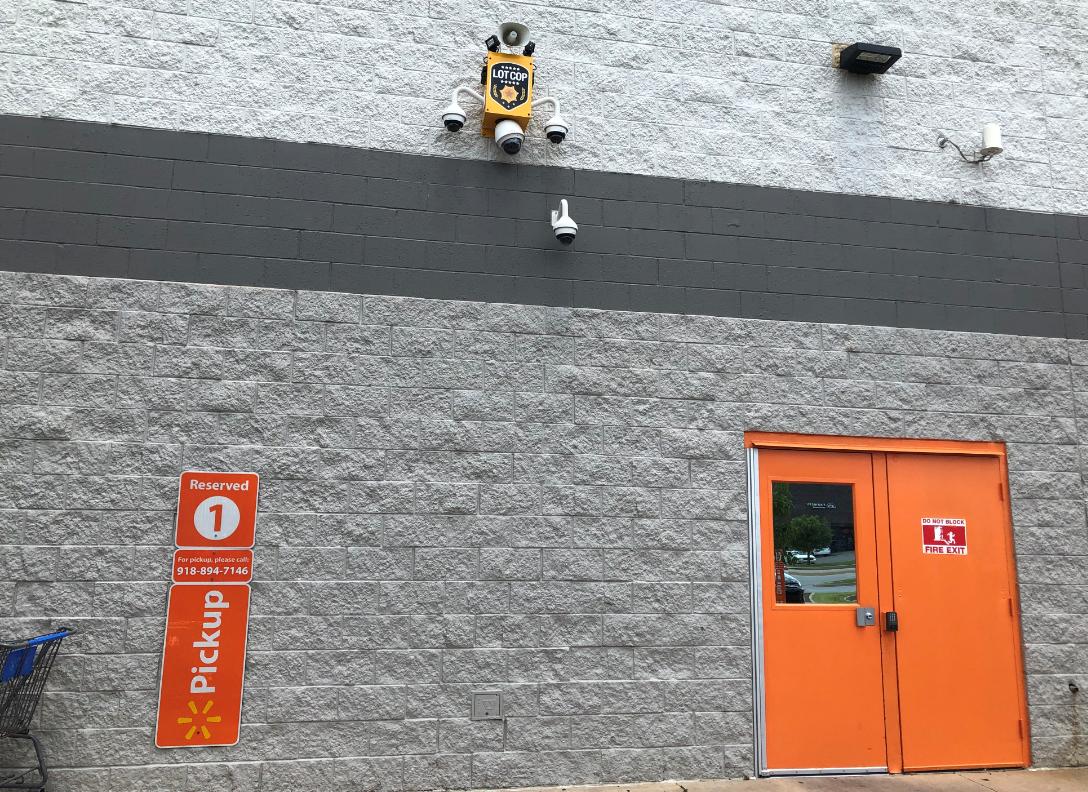
Lead times are improved
Lean manufacturing has many benefits, including the ability reduce waste and increase lead times. Lean manufacturing is a philosophy that emphasizes continuous improvement or kaizen. It unites the talents of employees, encourages accountability and collaboration, and is a way to bring out the best in them. The process can improve lead times by as much as 20%. Lean manufacturing's most important feature is its ability to make small, but significant improvements to product quality and efficiency.
Shortens set-up times
Reduced set-up time is a great way to cut down on the time it takes to make a product. Setup time is how long it takes to switch between the last item in a previous order and the first good one on the next. Setting up time covers preparation, replacement, location, and other activities. These activities may be internal or externe. Although internal activities are inactive, such as moving a machine or putting an item in its place, external setup activities can still be completed while the process remains operational.
This reduces the time taken to bring products to market
Lean manufacturing, also known as continuous improvement, was first developed in Japan in the period of rebuilding after World War II. It aimed to increase competition and reduce lead times. Companies can reduce the time required for products to reach the marketplace and meet customer demand. This will increase their profitability. This production approach can improve the efficiency of the manufacturing process and make the facility more efficient.
Improves product quality
The process of reducing waste, improving product quality, and minimizing costs are all important to the success of lean manufacturing. It is used by both large manufacturers and smaller businesses alike. It decreases lead times, costs, and labor. Read on for more information on how lean manufacturing can improve your business. Here are some key areas to concentrate on. Lean principles can help reduce lead time by 90%, improve product quality and lower your costs.
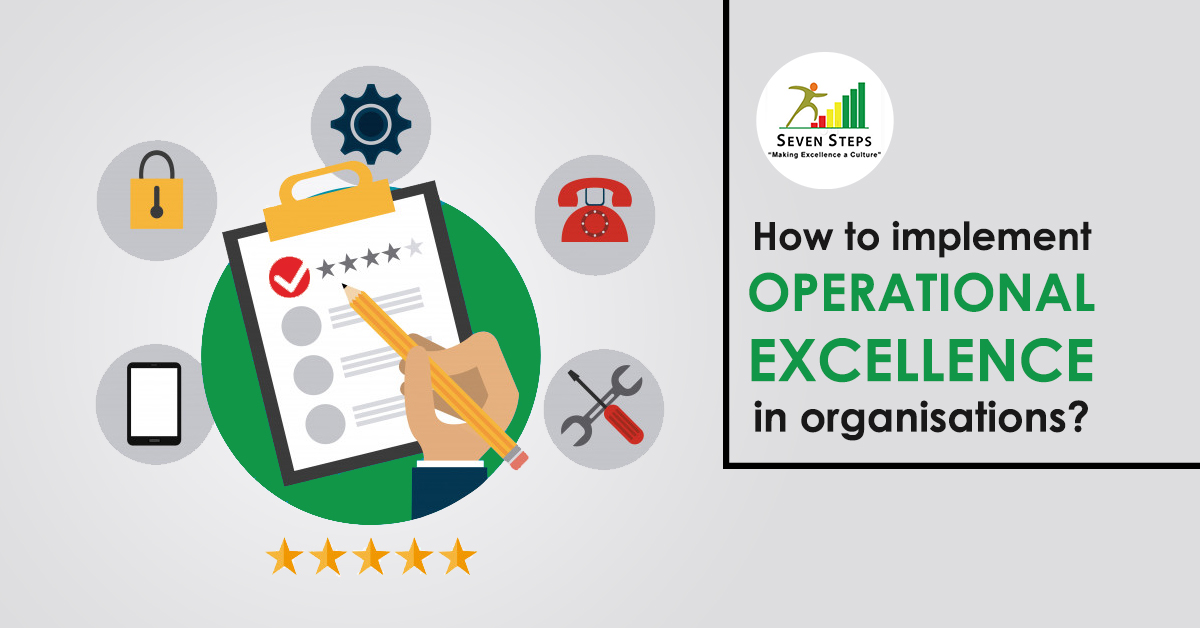
Lower indirect labor costs
Lean manufacturing's low hanging fruit is the reduction of indirect labor cost. True lean companies are not concerned with direct labor efficiency but rather look at ways to cut indirect labor cost. This includes eliminating management, material handling, inspection and management jobs as well as pushing production decisions to the floor. Toyota and other lean manufacturers use this same approach. We'll be looking at how lean manufacturing can reduce indirect labor costs in this article.
FAQ
Is automation important in manufacturing?
Not only is automation important for manufacturers, but it's also vital for service providers. It enables them to provide services faster and more efficiently. They can also reduce their costs by reducing human error and improving productivity.
What does manufacturing industry mean?
Manufacturing Industries are companies that manufacture products. Consumers are those who purchase these products. To accomplish this goal, these companies employ a range of processes including distribution, sales, management, and production. They create goods from raw materials, using machines and various other equipment. This includes all types if manufactured goods.
What is the role of a production manager?
Production planners ensure all aspects of the project are delivered within time and budget. They make sure that the product and services meet client expectations.
How can manufacturing avoid production bottlenecks
Avoiding production bottlenecks is as simple as keeping all processes running smoothly, from the time an order is received until the product ships.
This includes both planning for capacity and quality control.
This can be done by using continuous improvement techniques, such as Six Sigma.
Six Sigma management is a system that improves quality and reduces waste within your organization.
It's all about eliminating variation and creating consistency in work.
Statistics
- Many factories witnessed a 30% increase in output due to the shift to electric motors. (en.wikipedia.org)
- In 2021, an estimated 12.1 million Americans work in the manufacturing sector.6 (investopedia.com)
- (2:04) MTO is a production technique wherein products are customized according to customer specifications, and production only starts after an order is received. (oracle.com)
- According to the United Nations Industrial Development Organization (UNIDO), China is the top manufacturer worldwide by 2019 output, producing 28.7% of the total global manufacturing output, followed by the United States, Japan, Germany, and India.[52][53] (en.wikipedia.org)
- In the United States, for example, manufacturing makes up 15% of the economic output. (twi-global.com)
External Links
How To
How to Use 5S for Increasing Productivity in Manufacturing
5S stands for "Sort", 'Set In Order", 'Standardize', & Separate>. Toyota Motor Corporation was the first to develop the 5S approach in 1954. It improves the work environment and helps companies to achieve greater efficiency.
This approach aims to standardize production procedures, making them predictable, repeatable, and easily measurable. This means that daily tasks such as cleaning and sorting, storage, packing, labeling, and packaging are possible. Because workers know what they can expect, this helps them perform their jobs more efficiently.
Implementing 5S involves five steps: Sort, Set in Order, Standardize Separate, Store, and Each step has a different action and leads to higher efficiency. If you sort items, it makes them easier to find later. When you set items in an order, you put items together. You then organize your inventory in groups. Finally, label all containers correctly.
This process requires employees to think critically about how they do their job. Employees must understand why they do certain tasks and decide if there's another way to accomplish them without relying on the old ways of doing things. To be successful in the 5S system, employees will need to acquire new skills and techniques.
In addition to improving efficiency, the 5S system also increases morale and teamwork among employees. As they begin to see improvements, they feel motivated to continue working towards the goal of achieving higher levels of efficiency.