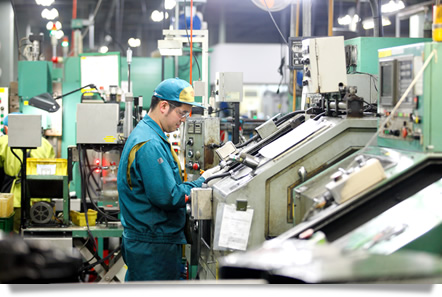
The creation of a sustainable supply-chain can be difficult. Transport logistics and packaging can lead to waste and greenhouse gas emissions. For example, investing in compact packaging can reduce the shipping weight and lower costs. Compact packaging can reduce waste and protect your bottom line.
Supply chain sustainability requires a combination of processes, policies, and technology. Many companies are looking for ways to use sustainable materials, measure performance, and make operational improvements. To make their suppliers more sustainable, some companies offer training.
A sustainable supply network can be a boon for the company and the local community. Companies can choose suppliers that emphasize renewables and recycled materials, and they can reduce the number of offerings they make. They can also encourage suppliers who use sustainable material and establish a code to ensure the integrity of their suppliers.
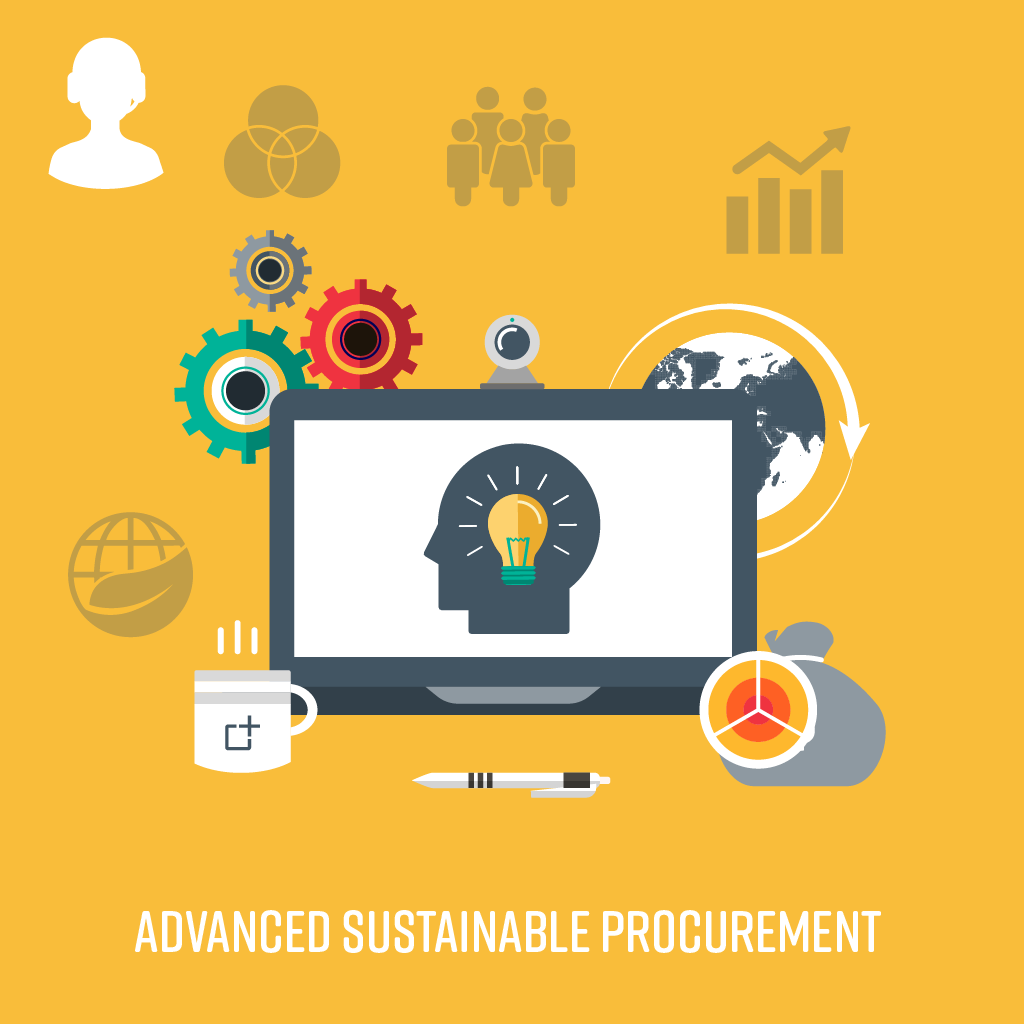
Businesses can reduce their waste by remarketing unused products. They can also reduce the amount of water they use. Companies can set goals that are measurable to improve their supply chains and can involve internal and external stakeholders to bring about change. A strong governance system can help companies meet their sustainability goals.
Many companies have taken steps to reduce emissions from their facilities, purchased energy, and transportation partners. Many companies have not taken steps to reduce indirect emissions from their supply chain partners. These include distribution and transportation partners. Carbon Disclosure Project reported that some companies made progress in reducing greenhouse gases emissions. However, there is still much to do.
To improve the sustainability of their supply chains, companies need to set goals that can be measured, engage external and internal stakeholders, as well as establish and maintain measurable targets. In order to meet their goals, companies should involve their suppliers and customers. They should also use data in their decision-making process and provide a clear roadmap for success.
A company can improve its supply chain resilience by adopting robust risk management strategies and nearshoring or diversifying suppliers. Bed Bath & Beyond, for example, has eight brands it owns and has increased its control over the supply chain. It claims that at minimum half of its wood, cotton and other materials are sustainably sourced. It has also identified key locations for warehousing.
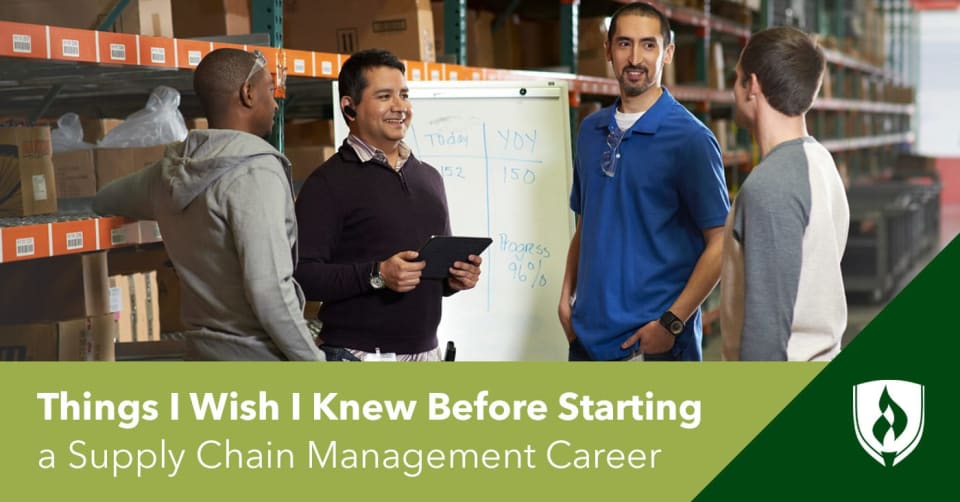
Companies should also be aware of the impact that packaging has on the environment. Some innovations may allow products to either be recycled or reused. These innovations also can help reduce the size of shipments, as well the number of trips they make. Businesses can also invest in small packaging and update their warehouse refrigeration equipment. These innovations can be long-lasting and reduce the carbon footprint.
Many companies have also begun to adopt more circular economy models. They are developing products that can either be reused or repurposed, and are focusing their attention on the finite resources they do have. This will help decrease greenhouse gas emissions and reduce the waste.
FAQ
What is the best way to learn about manufacturing?
Practical experience is the best way of learning about manufacturing. You can also read educational videos or take classes if this isn't possible.
How is a production manager different from a producer planner?
The difference between a product planner and project manager is that a planer is typically the one who organizes and plans the entire project. A production planner, however, is mostly involved in the planning stages.
What is the role of a logistics manager
A logistics manager ensures that all goods are delivered on time and without damage. This is achieved by using their knowledge and experience with the products of the company. He/she must also ensure sufficient stock to meet the demand.
Statistics
- [54][55] These are the top 50 countries by the total value of manufacturing output in US dollars for its noted year according to World Bank.[56] (en.wikipedia.org)
- In the United States, for example, manufacturing makes up 15% of the economic output. (twi-global.com)
- Job #1 is delivering the ordered product according to specifications: color, size, brand, and quantity. (netsuite.com)
- In 2021, an estimated 12.1 million Americans work in the manufacturing sector.6 (investopedia.com)
- It's estimated that 10.8% of the U.S. GDP in 2020 was contributed to manufacturing. (investopedia.com)
External Links
How To
How to Use the 5S to Increase Productivity In Manufacturing
5S stands for "Sort", "Set In Order", "Standardize", "Separate" and "Store". The 5S methodology was developed at Toyota Motor Corporation in 1954. It improves the work environment and helps companies to achieve greater efficiency.
This approach aims to standardize production procedures, making them predictable, repeatable, and easily measurable. This means that tasks such as cleaning, sorting, storing, packing, and labeling are performed daily. Workers can be more productive by knowing what to expect.
Implementing 5S involves five steps: Sort, Set in Order, Standardize Separate, Store, and Each step is a different action that leads to greater efficiency. You can make it easy for people to find things later by sorting them. When items are ordered, they are put together. Once you have separated your inventory into groups and organized them, you will store these groups in easily accessible containers. Finally, label all containers correctly.
Employees will need to be more critical about their work. Employees must be able to see why they do what they do and find a way to achieve them without having to rely on their old methods. To implement the 5S system, employees must acquire new skills and techniques.
In addition to improving efficiency, the 5S system also increases morale and teamwork among employees. Once they start to notice improvements, they are motivated to keep working towards their goal of increasing efficiency.