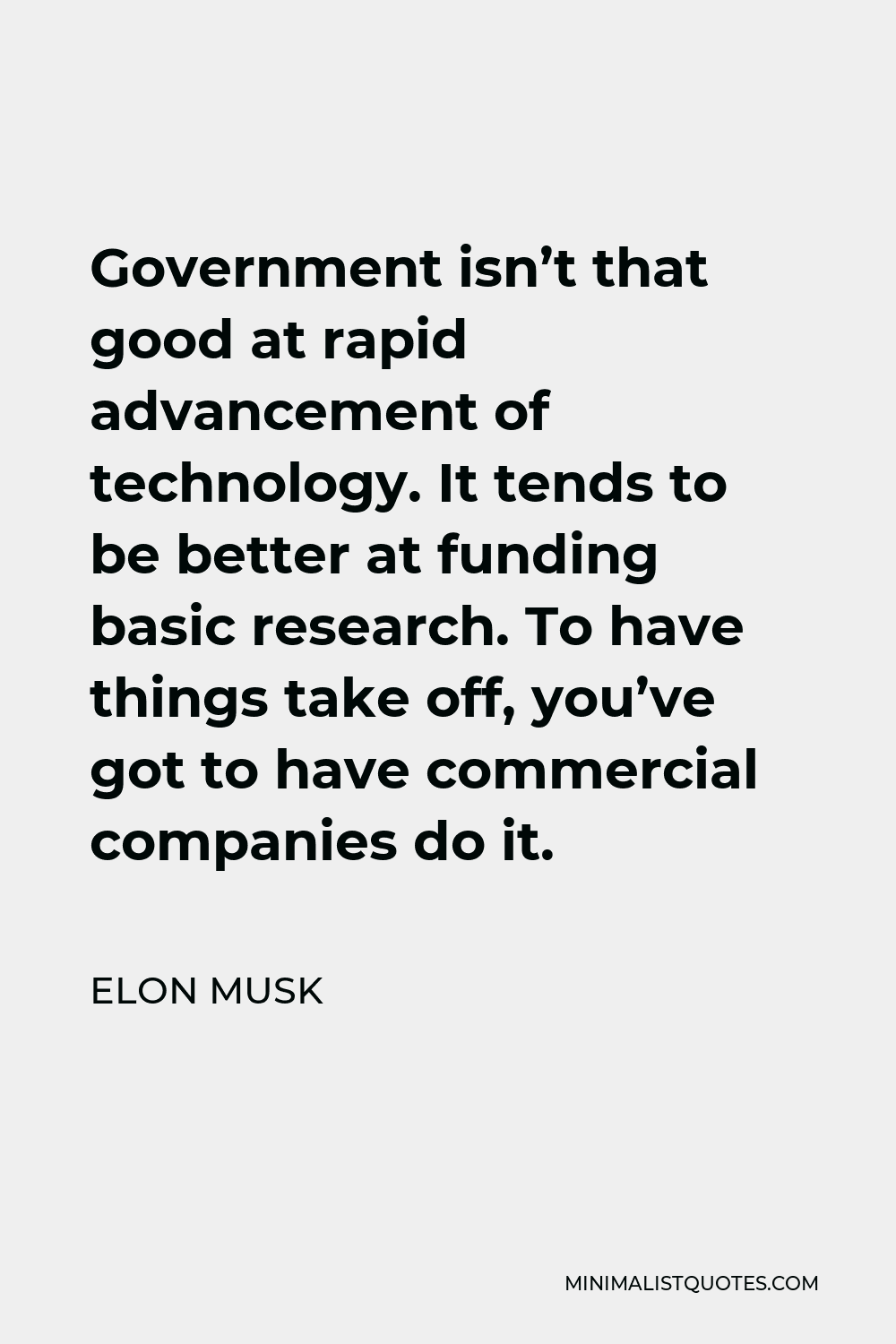
Supply chain management software, whether you manage a large organization or a small business can streamline your processes and increase your efficiency. These software systems provide a central view of your entire supply chain. This allows you to plan production, shipping plans, and delivery routes. These systems can automate and streamline processes so that employees can focus on other areas of their business. Supply chain management software is important to every organization that controls shipping and manufacturing.
You need to consider many features and capabilities when selecting the best supply chain management tool. These features include integration with other applications, scalability, usability, and ease-of-use. It's also important to look at the reputation of the provider and the features offered. A solution should be within your budget. You should also consider whether you want a SaaS package or a full-scale plan. This will allow you to adjust as your business grows.
E2open Software is a top provider of supply chain management solutions. They specialize in cloud-based software that delivers better demand forecasting. The company also offers advanced technology and features. Software is available for businesses in many industries including manufacturing, retail, and transportation.
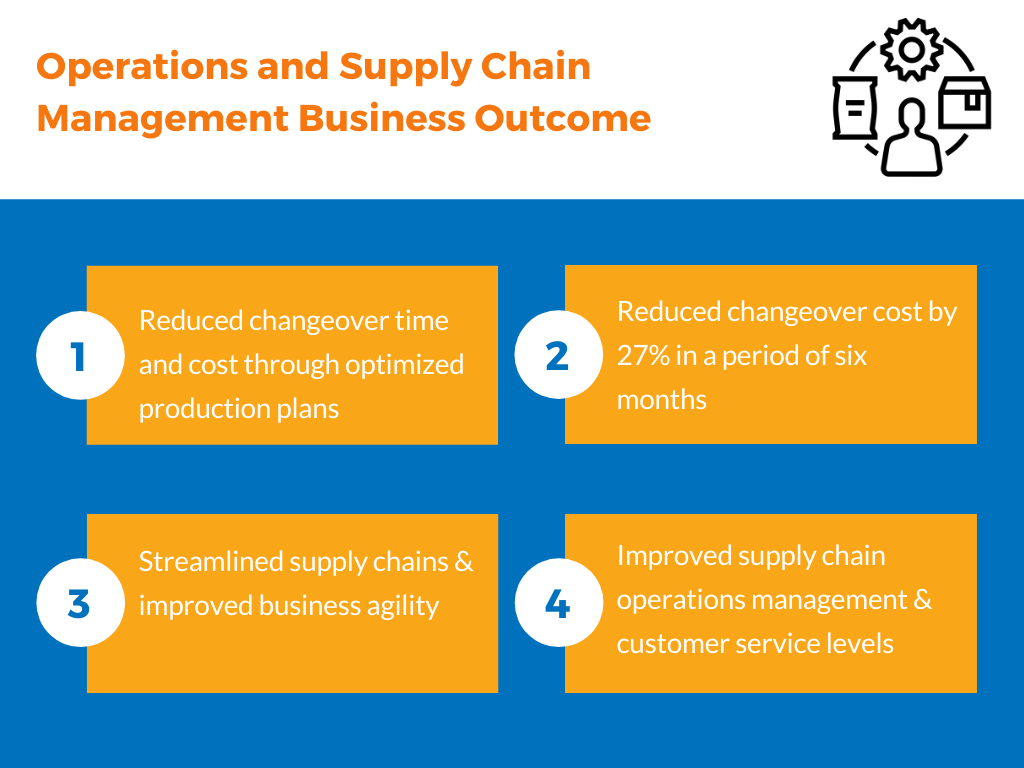
A key feature of supply chain management software is real-time visibility. This software helps you keep track of your inventory and shipments. It helps you ensure that your customers have what they need when they need it. It also helps you develop long-term strategies for managing demand-supply balance.
Kinaxis provides a comprehensive supply-chain management software solution. It breaks down silos to streamline processes. It combines machine and human intelligence to help you make better business decisions. It can help you plan inventory and capacities so that you can respond better to opportunities.
Sales forecasting software allows you to better understand historical sales, sales cycles, and seasonality. It also uses machine learning to help you anticipate sales. It helps you predict your future sales and prepares your sales staff for it. It allows you to access data across multiple sources, making your operations easier.
Descartes Systems Group is the main competitor in supply chain management software. They are the most preferred vendor for many organizations. This company has over 13,000 active users, and its products compete with SAP SCM, Megaventory, JDA, and Logility.
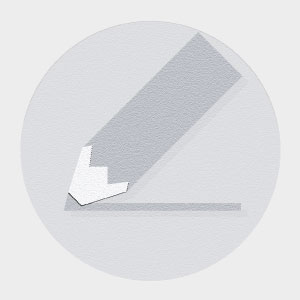
Manhattan Associates is another big competitor in supply chain management software. Manhattan Associates, which has around $617.5 Million in annual revenue, is another software company that has thousands of users. Eddie Capel currently runs it. This company competes against JDA and Logility.
Infor SCM is a top-rated supply chain management platform. It's a great solution for small and large businesses. It is a cloud-based platform that unites end-to-end enterprise processes. It also features analytics at core that can optimize your supply chain.
FAQ
Can some manufacturing processes be automated?
Yes! Since ancient times, automation has been in existence. The wheel was invented by the Egyptians thousands of years ago. To help us build assembly lines, we now have robots.
There are many applications for robotics in manufacturing today. These include:
-
Automated assembly line robots
-
Robot welding
-
Robot painting
-
Robotics inspection
-
Robots that create products
Automation can be applied to manufacturing in many other ways. 3D printing, for example, allows us to create custom products without waiting for them to be made.
What are the products of logistics?
Logistics refers to the movement of goods from one place to another.
They include all aspects associated with transport including packaging, loading transporting, unloading storage, warehousing inventory management customer service, distribution returns and recycling.
Logisticians ensure that products reach the right destination at the right moment and under safe conditions. Logisticians help companies improve their supply chain efficiency by providing information about demand forecasts and stock levels, production schedules, as well as availability of raw materials.
They keep track and monitor the transit of shipments, maintain quality standards, order replenishment and inventories, coordinate with suppliers, vendors, and provide support for sales and marketing.
How can manufacturing reduce production bottlenecks?
To avoid production bottlenecks, ensure that all processes run smoothly from the moment you receive your order to the time the product ships.
This includes planning for capacity requirements as well as quality control measures.
Continuous improvement techniques such Six Sigma can help you achieve this.
Six Sigma can be used to improve the quality and decrease waste in all areas of your company.
It emphasizes consistency and eliminating variance in your work.
How can excess manufacturing production be reduced?
Improved inventory management is the key to reducing overproduction. This would decrease the time that is spent on inefficient activities like purchasing, storing, or maintaining excess stock. This will allow us to free up resources for more productive tasks.
This can be done by using a Kanban system. A Kanbanboard is a visual tool that allows you to keep track of the work being done. Work items are moved through various states to reach their destination in a Kanban system. Each state is assigned a different priority.
For instance, when work moves from one stage to another, the current task is complete enough to be moved to the next stage. However, if a task is still at the beginning stages, it will remain so until it reaches the end of the process.
This allows work to move forward and ensures that no work is missed. Managers can see how much work has been done and the status of each task at any time with a Kanban Board. This information allows them to adjust their workflow based on real-time data.
Lean manufacturing is another option to control inventory levels. Lean manufacturing emphasizes eliminating waste in all phases of production. Waste includes anything that does not add value to the product. The following are examples of common waste types:
-
Overproduction
-
Inventory
-
Packaging that is not necessary
-
Materials in excess
By implementing these ideas, manufacturers can improve efficiency and cut costs.
How can I find out more about manufacturing?
Hands-on experience is the best way to learn more about manufacturing. You can also read educational videos or take classes if this isn't possible.
What is the difference in Production Planning and Scheduling, you ask?
Production Planning (PP) refers to the process of determining how much production is needed at any given moment. This is done through forecasting demand and identifying production capacities.
Scheduling is the process of assigning specific dates to tasks so they can be completed within the specified timeframe.
What is production planning?
Production Planning includes planning for all aspects related to production. This document is designed to make sure everything is ready for when you're ready to shoot. You should also have information to ensure the best possible results on set. It should include information about shooting locations, casting lists, crew details, equipment requirements, and shooting schedules.
It is important to first outline the type of film you would like to make. You may already know where you want the film to be shot, or perhaps you have specific locations and sets you wish to use. Once you have identified your locations and scenes it's time to begin figuring out what elements you will need for each one. If you decide you need a car and don't know what model to choose, this could be an example. You could look online for cars to see what options are available, and then narrow down your choices by selecting between different makes or models.
After you've found the perfect car, it's time to start thinking about adding extras. Do you need people sitting in the front seats? Or maybe you just need someone to push the car around. Perhaps you would like to change the interior colour from black to white. These questions will help you determine the exact look and feel of your car. You can also think about the type of shots you want to get. Are you going to be shooting close-ups? Or wide angles? Perhaps you want to show the engine or the steering wheel? These factors will help you determine which car style you want to film.
Once you have made all the necessary decisions, you can start to create a schedule. You will know when you should start and when you should finish shooting. You will need to know when you have to be there, what time you have to leave and when your return home. So everyone is clear about what they need to do. If you need to hire extra staff, you can make sure you book them in advance. You should not hire anyone who doesn't show up because of your inaction.
Also, consider how many days you will be filming your schedule. Some projects can be completed in a matter of days or weeks. Others may take several days. While creating your schedule, it is important to remember whether you will require more than one shot per day. Multiple takes at the same place will result in higher costs and longer completion times. It's better to be safe than sorry and shoot less takes if you're not certain whether you need more takes.
Budgeting is another crucial aspect of production plan. It is important to set a realistic budget so you can work within your budget. It is possible to reduce the budget at any time if you experience unexpected problems. You shouldn't underestimate the amount you'll spend. If you underestimate the cost of something, you will have less money left after paying for other items.
Production planning can be a complex process. However, once you know how everything works together it will become easier to plan future projects.
Statistics
- In 2021, an estimated 12.1 million Americans work in the manufacturing sector.6 (investopedia.com)
- It's estimated that 10.8% of the U.S. GDP in 2020 was contributed to manufacturing. (investopedia.com)
- [54][55] These are the top 50 countries by the total value of manufacturing output in US dollars for its noted year according to World Bank.[56] (en.wikipedia.org)
- According to the United Nations Industrial Development Organization (UNIDO), China is the top manufacturer worldwide by 2019 output, producing 28.7% of the total global manufacturing output, followed by the United States, Japan, Germany, and India.[52][53] (en.wikipedia.org)
- Many factories witnessed a 30% increase in output due to the shift to electric motors. (en.wikipedia.org)
External Links
How To
How to use the Just In-Time Production Method
Just-in-time is a way to cut costs and increase efficiency in business processes. It allows you to get the right amount resources at the right time. This means that you only pay the amount you actually use. Frederick Taylor was the first to coin this term. He developed it while working as a foreman during the early 1900s. After observing how workers were paid overtime for late work, he realized that overtime was a common practice. He then concluded that if he could ensure that workers had enough time to do their job before starting to work, this would improve productivity.
JIT is an acronym that means you need to plan ahead so you don’t waste your money. The entire project should be looked at from start to finish. You need to ensure you have enough resources to tackle any issues that might arise. You'll be prepared to handle any potential problems if you know in advance. This way, you won't end up paying extra money for things that weren't really necessary.
There are different types of JIT methods:
-
Demand-driven: This JIT is where you place regular orders for the parts/materials that are needed for your project. This will allow to track how much material has been used up. This will allow to you estimate the time it will take for more to be produced.
-
Inventory-based: This type allows you to stock the materials needed for your projects ahead of time. This allows one to predict how much they will sell.
-
Project-driven: This approach involves setting aside sufficient funds to cover your project's costs. Once you have an idea of how much material you will need, you can purchase the necessary materials.
-
Resource-based: This is the most common form of JIT. This is where you assign resources based upon demand. For instance, if you have a lot of orders coming in, you'll assign more people to handle them. If you don't receive many orders, then you'll assign fewer employees to handle the load.
-
Cost-based: This is the same as resource-based except that you don't care how many people there are but how much each one of them costs.
-
Price-based pricing: This is similar in concept to cost-based but instead you look at how much each worker costs, it looks at the overall company's price.
-
Material-based - This is a variant of cost-based. But instead of looking at the total company cost, you focus on how much raw material you spend per year.
-
Time-based: This is another variation of resource-based JIT. Instead of focusing on the cost of each employee, you will focus on the time it takes to complete a project.
-
Quality-based JIT: This is another variation of resource based JIT. Instead of thinking about how much each employee costs or how long it takes to manufacture something, you think about how good the quality of your product is.
-
Value-based JIT : This is the newest type of JIT. You don't worry about whether the products work or if they meet customer expectations. Instead, your goal is to add value to the market.
-
Stock-based is an inventory-based system that measures the number of items produced at any given moment. This is used to increase production and minimize inventory.
-
Just-in-time (JIT) planning: This is a combination of JIT and supply chain management. It is the process that schedules the delivery of components within a short time of their order. It's important as it reduces leadtimes and increases throughput.