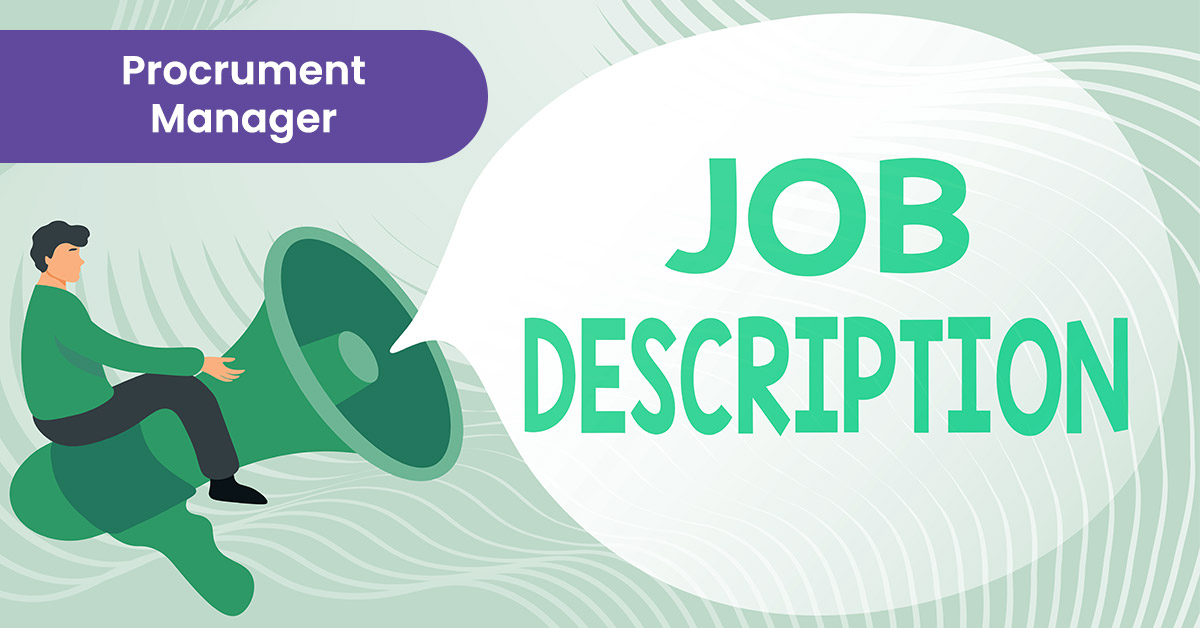
Having a good media supply chain workflow is important. Companies must invest in modern technology to ensure their content gets delivered to consumers in a timely manner. A cloud-based platform that is purpose-built for media assets can be a great way of ensuring your media assets are being used as efficiently as possible. Facilitating processes can help you gain more insight into your business.
Understanding the components of your media supply chain workflow is key to getting the best out of it. A workflow could include quality control, which ensures that media files are properly formatted, sound mapping is done, and the codec is used. This is essential to ensure the content is delivered correctly and preserved. A good metadata framework can also help you to understand the content being delivered and assist you in finding content quicker.
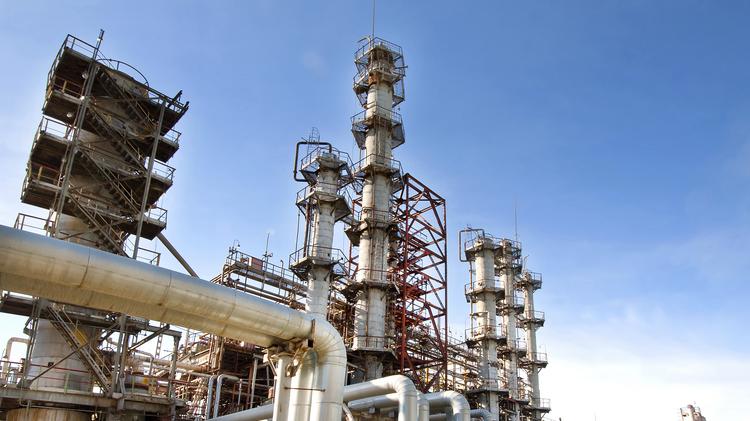
Content may come from third-party companies or individuals as part of your media flow. This can present challenges as files may arrive in multiple formats. Files may also need to be processed before you can use them. You may need to modify the file format or transcode the master files into smaller proxy ones. This can be costly and affect the continuity of your business.
The media supply chain workflows are more complex than ever. It is long past the days of inserting tape in a machine. Streaming and video editing technologies have transformed the production of content. With these technologies, you can now create multiple versions of a piece of content, ensuring that you get the highest quality. This will allow you to reduce costs and provide the highest quality content.
In order to get the most out your media supply chain workflow, you need to have an expert level understanding of the processes involved. Expertise in server and client operating systems, networking, as well as media terminology is essential. Additionally, you will need to be familiar with deploying software in cloud environments. If you aren't sure how to do that, it is a good idea to speak with an IT Analyst who is skilled in these areas.
The video engineer works closely alongside the client's team to establish a media supply channel workflow. They are responsible in improving functionality, working with vendors and delivering media to the user. They also have to create requirements for new features.
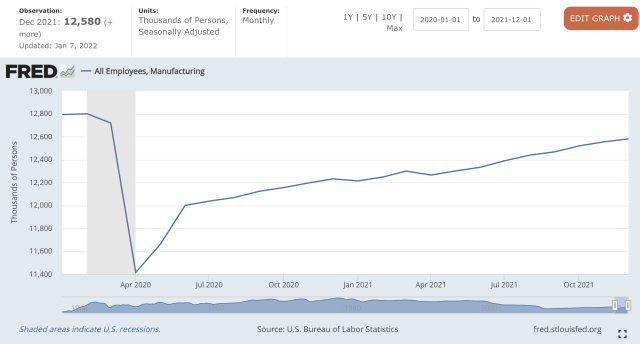
Paramount Global Media Supply Chain Platforms Operations workflows will be led by the Director, Products. They will be working with internal and externe collaborators to develop solutions and implement them for Paramount's customers. They will provide regular feedback and review product requirements. They will also manage product development cycles that use Agile methodology. They will also communicate product requirements to development teams and oversee the translation of these requirements into the product.
FAQ
What does it mean to be a manufacturer?
Manufacturing Industries is a group of businesses that produce goods for sale. Consumers are people who purchase these goods. These companies use a variety processes such as distribution, retailing and management to accomplish their purpose. They create goods from raw materials, using machines and various other equipment. This includes all types and varieties of manufactured goods, such as food items, clothings, building supplies, furnitures, toys, electronics tools, machinery vehicles, pharmaceuticals medical devices, chemicals, among others.
What are the responsibilities of a manufacturing manager
Manufacturing managers must ensure that manufacturing processes are efficient, effective, and cost-effective. They should also be aware and responsive to any company problems.
They should also know how to communicate with other departments such as sales and marketing.
They should be informed about industry trends and be able make use of this information to improve their productivity and efficiency.
How does manufacturing avoid bottlenecks in production?
You can avoid bottlenecks in production by making sure that everything runs smoothly throughout the production cycle, from the moment you receive an order to the moment the product is shipped.
This includes both quality control and capacity planning.
The best way to do this is to use continuous improvement techniques such as Six Sigma.
Six Sigma can be used to improve the quality and decrease waste in all areas of your company.
It seeks to eliminate variation and create consistency in your work.
What are the products of logistics?
Logistics involves the transportation of goods from point A and point B.
These include all aspects related to transport such as packaging, loading and transporting, storing, transporting, unloading and warehousing inventory management, customer service. Distribution, returns, recycling are some of the options.
Logisticians ensure that the product is delivered to the correct place, at the right time, and under safe conditions. They help companies manage their supply chain efficiency by providing information on demand forecasts, stock levels, production schedules, and availability of raw materials.
They monitor shipments in transit, ensure quality standards, manage inventories, replenish orders, coordinate with suppliers and other vendors, and offer support services for sales, marketing, and customer service.
What are the essential elements of running a logistics firm?
To be a successful businessman in logistics, you will need many skills and knowledge. For clients and suppliers to be successful, you need to have excellent communication skills. You must be able analyze data and draw out conclusions. You will need to be able handle pressure well and work in stressful situations. To increase efficiency and creativity, you need to be creative. To motivate and guide your team towards reaching organizational goals, you must have strong leadership skills.
It is also important to be efficient and well organized in order meet deadlines.
What's the difference between Production Planning & Scheduling?
Production Planning (PP), or production planning, is the process by which you determine what products are needed at any given time. Forecasting and identifying production capacity are two key elements to this process.
Scheduling is the process of assigning specific dates to tasks so they can be completed within the specified timeframe.
How can I learn about manufacturing?
Practical experience is the best way of learning about manufacturing. If that is not possible, you could always read books or view educational videos.
Statistics
- You can multiply the result by 100 to get the total percent of monthly overhead. (investopedia.com)
- In 2021, an estimated 12.1 million Americans work in the manufacturing sector.6 (investopedia.com)
- [54][55] These are the top 50 countries by the total value of manufacturing output in US dollars for its noted year according to World Bank.[56] (en.wikipedia.org)
- According to the United Nations Industrial Development Organization (UNIDO), China is the top manufacturer worldwide by 2019 output, producing 28.7% of the total global manufacturing output, followed by the United States, Japan, Germany, and India.[52][53] (en.wikipedia.org)
- Many factories witnessed a 30% increase in output due to the shift to electric motors. (en.wikipedia.org)
External Links
How To
How to Use Six Sigma in Manufacturing
Six Sigma is defined as "the application of statistical process control (SPC) techniques to achieve continuous improvement." Motorola's Quality Improvement Department, Tokyo, Japan, developed it in 1986. Six Sigma is a method to improve quality through standardization and elimination of defects. In recent years, many companies have adopted this method because they believe there is no such thing as perfect products or services. Six Sigma aims to reduce variation in the production's mean value. This means that if you take a sample of your product, then measure its performance against the average, you can find out what percentage of the time the process deviates from the norm. If you notice a large deviation, then it is time to fix it.
Understanding the dynamics of variability within your business is the first step in Six Sigma. Once you've understood that, you'll want to identify sources of variation. It is important to identify whether the variations are random or systemic. Random variations are caused when people make mistakes. While systematic variations are caused outside of the process, they can occur. Random variations would include, for example, the failure of some widgets to fall from the assembly line. If however, you notice that each time you assemble a widget it falls apart in exactly the same spot, that is a problem.
After identifying the problem areas, you will need to devise solutions. It might mean changing the way you do business or redesigning it entirely. Once you have implemented the changes, it is important to test them again to ensure they work. If they didn't work, then you'll need to go back to the drawing board and come up with another plan.