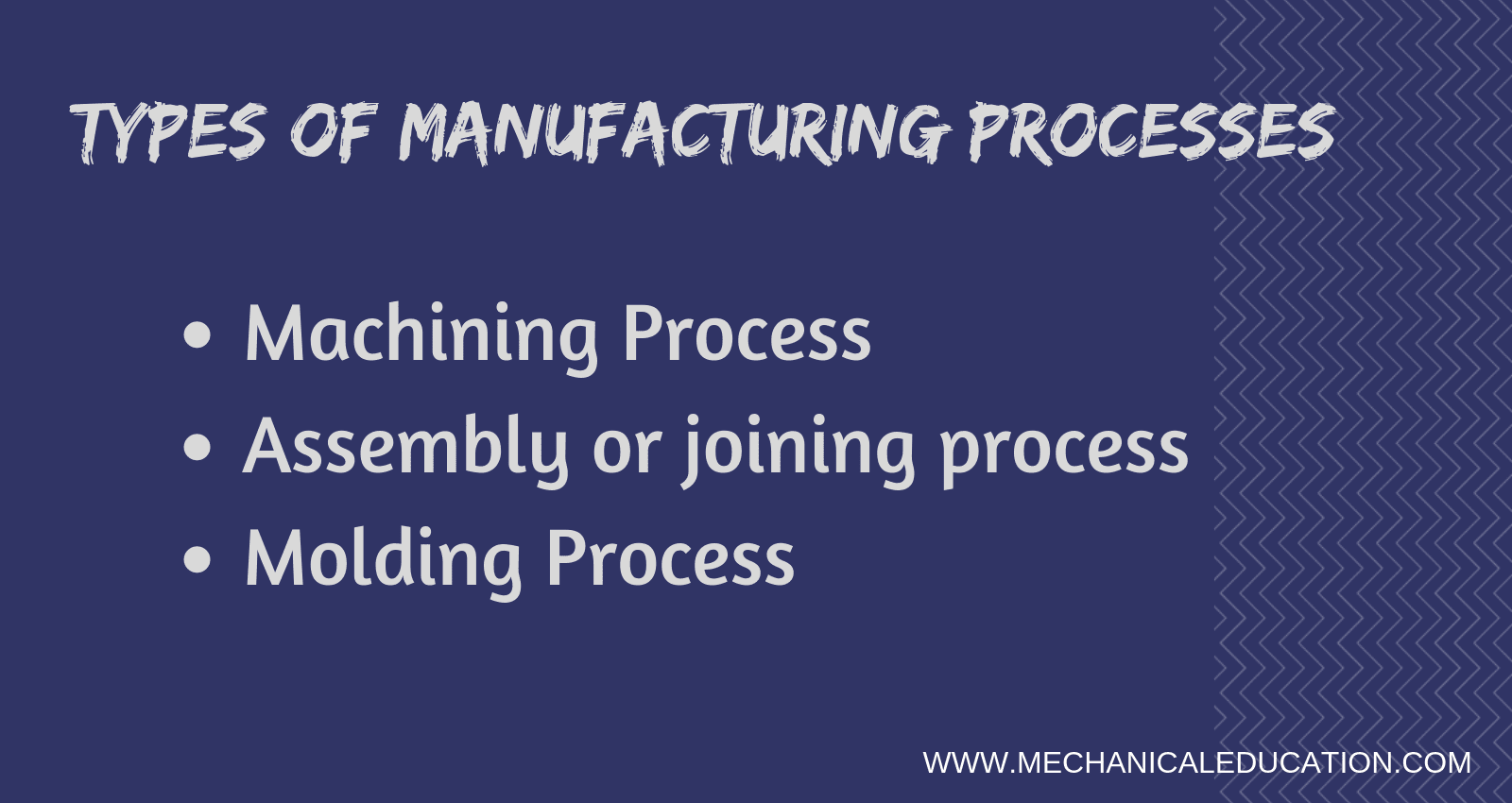
Supply chain risk management is essential for maintaining a strong operation, no matter if you're a small business owner or an enterprise unit of a large corporation. There are many risk factors, from the common to the most serious. You can prevent losses by creating a plan and following the implementation strategy.
Data sharing is an integral part of a supply chains continuity plan. If your organization relies on a single supplier, you are prone to vendor failures and supplier dispute. You will be more likely to avoid supply interruptions if your company is part-of a multisupplier group. You may also be able to negotiate an alternative supplier.
Similarly, if your company has a complex network of contractors, you are at greater risk of vendor fraud, duplicate billing, and improper related-party billing. You can create a risk assessment method to help reduce these risks. This can include a thorough assessment of your partners, suppliers, and other tier-one components.
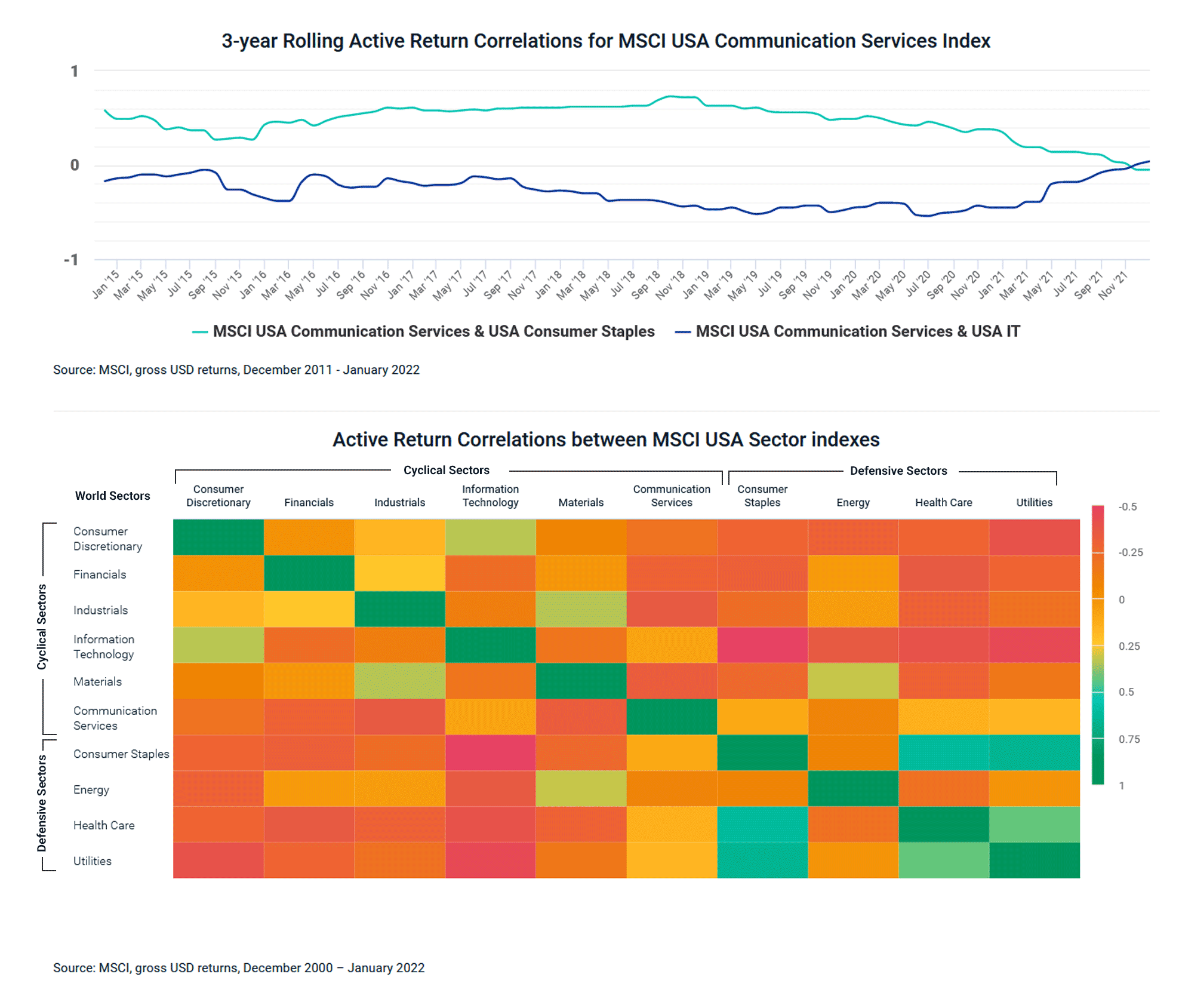
You must first identify the essential elements of a supply supply chain. After that, quantify them and create an action plan. These items should be combined with a few additional. A proactive monitoring system is the most important component. Your executives need to have real-time, accurate data about supply chain risk. If you can track supply risks in real-time, you will be better equipped to make informed decisions as well as to respond quickly.
It is important to remember that the resilience of your supply chains is dependent on governance as you assess and quantify your risks. It is important to take into account the role of stakeholders. If the company had properly scoredcarded its suppliers, it could have prevented the supply-chain disruption that resulted in the bankruptcy of a supplier in the pharmaceutical industry.
It is crucial to have a plan that addresses the supply chain crisis. But, it is not always simple to put in place the right contingency strategies. Many businesses do not take the time necessary to prepare enough contingency plan for each risk that they manage. These plans should begin with the most significant potential impact.
The PPPR is a globally accepted standard for supply chain management. It stands for preventive, preparation, response, recovery and mitigation. This is a strong approach that will help improve your ability monitor and respond to disruptions in supply chains. It can also be used in conjunction other strategies to protect your business from potential risks. Using a PPPR as a guide can help you make the right decisions and stay ahead of your competition in today's marketplace.
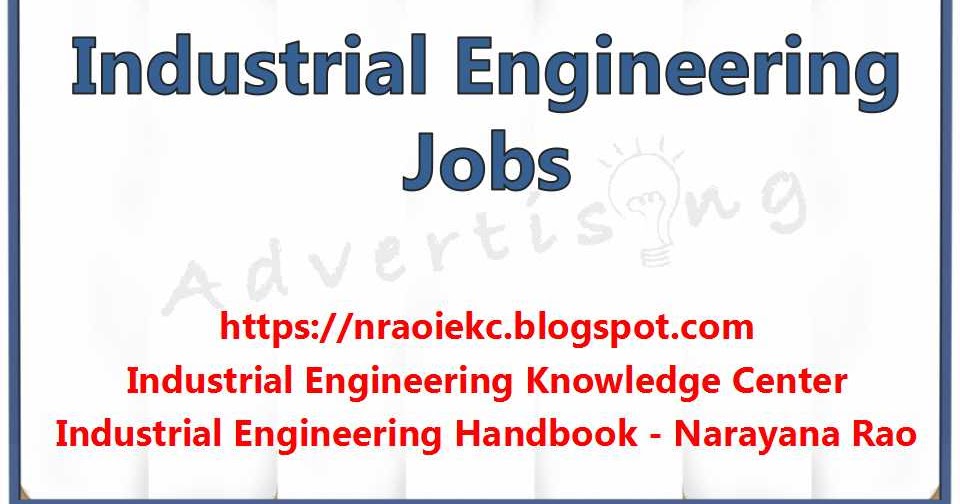
Get the right data from suppliers to understand their history, and what they can offer. This data can be used to inform your decision-making. You can give your insurers the right premiums by using reliable data.
FAQ
What does it take for a logistics enterprise to succeed?
To run a successful logistics company, you need a lot knowledge and skills. For clients and suppliers to be successful, you need to have excellent communication skills. You need to understand how to analyze data and draw conclusions from it. You must be able manage stress and pressure under pressure. You must be creative and innovative to develop new ideas to improve efficiency. You will need strong leadership skills to motivate and direct your team members towards achieving their organizational goals.
It is important to be organized and efficient in order to meet tight deadlines.
How can I learn about manufacturing?
Experience is the best way for you to learn about manufacturing. You can also read educational videos or take classes if this isn't possible.
What are manufacturing & logistics?
Manufacturing is the production of goods using raw materials. Logistics includes all aspects related to supply chain management, such as procurement, distribution planning, inventory control and transportation. As a broad term, manufacturing and logistics often refer to both the creation and delivery of products.
Statistics
- According to the United Nations Industrial Development Organization (UNIDO), China is the top manufacturer worldwide by 2019 output, producing 28.7% of the total global manufacturing output, followed by the United States, Japan, Germany, and India.[52][53] (en.wikipedia.org)
- According to a Statista study, U.S. businesses spent $1.63 trillion on logistics in 2019, moving goods from origin to end user through various supply chain network segments. (netsuite.com)
- In the United States, for example, manufacturing makes up 15% of the economic output. (twi-global.com)
- It's estimated that 10.8% of the U.S. GDP in 2020 was contributed to manufacturing. (investopedia.com)
- Many factories witnessed a 30% increase in output due to the shift to electric motors. (en.wikipedia.org)
External Links
How To
How to Use the 5S to Increase Productivity In Manufacturing
5S stands for "Sort", 'Set In Order", 'Standardize', & Separate>. Toyota Motor Corporation created the 5S methodology in 1954. It improves the work environment and helps companies to achieve greater efficiency.
This method has the basic goal of standardizing production processes to make them repeatable. This means that tasks such as cleaning, sorting, storing, packing, and labeling are performed daily. These actions allow workers to perform their job more efficiently, knowing what to expect.
Implementing 5S requires five steps. These are Sort, Set In Order, Standardize. Separate. And Store. Each step has a different action and leads to higher efficiency. For example, when you sort things, you make them easy to find later. Once you have placed items in an ordered fashion, you will put them together. You then organize your inventory in groups. You can also label your containers to ensure everything is properly labeled.
Employees need to reflect on how they do their jobs. Employees should understand why they do the tasks they do, and then decide if there are better ways to accomplish them. To implement the 5S system, employees must acquire new skills and techniques.
The 5S method increases efficiency and morale among employees. They will feel motivated to strive for higher levels of efficiency once they start to see results.