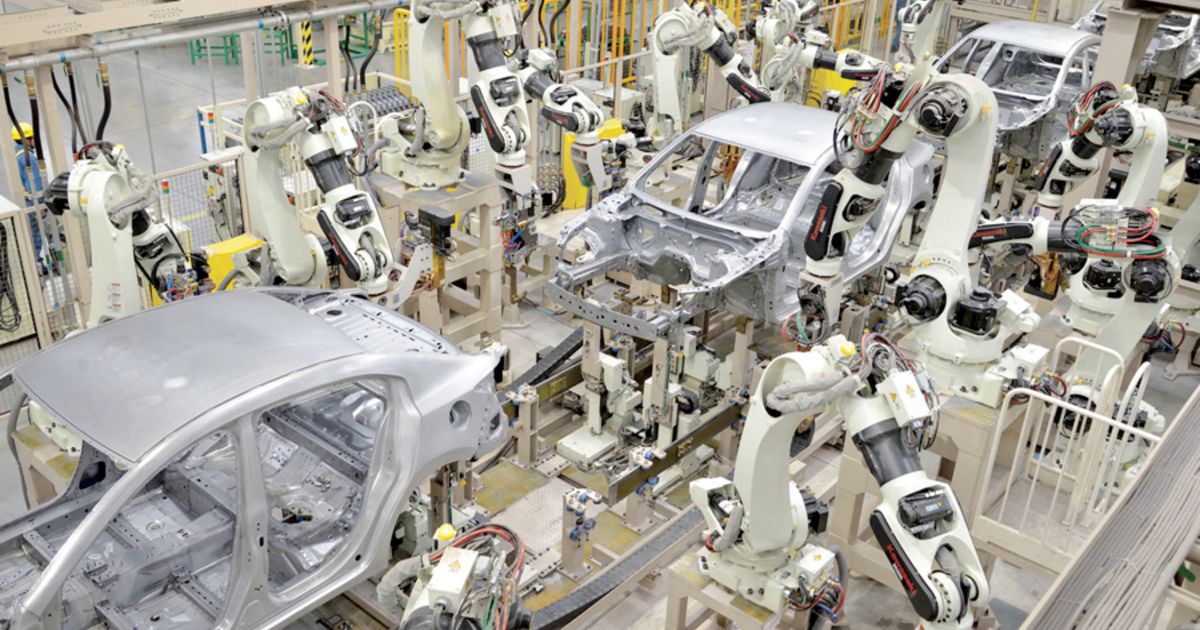
Visual management is the act of using visual signals to convey information. This method increases efficiency and clarity by recognizing information immediately. There are several types of visual control, including: process control charts, FIFO lane, and Lean daily management board. These are just a few of the most commonly used examples. Also, you can read more about visual control in Lean manufacturing. Continue reading for more information. This method can help you get your company on the right path to lean manufacturing.
Lean manufacturing
One of the many methods used for visual management in lean manufacturing is the use of Andon, a Japanese word for status-display visualization. This helps supervisors and workers to see the status of their work, process flow, and any other relevant information. Visual management also allows you to label workspaces, materials and parts. It allows for the identification of inefficiencies and simplifies processes. Below are some of the many benefits of visual control in lean manufacturing.
Lean is a system that relies on visual tools to manage the process. Operators and supervisors can identify waste and improve process flow to avoid mistakes. It can also reduce safety risks. Floor markings and other visual indicators help forklift drivers to stay in the right areas. By using visual management in lean manufacturing, workers can work more efficiently. Visual management can reduce waste as well as minimize safety risks.
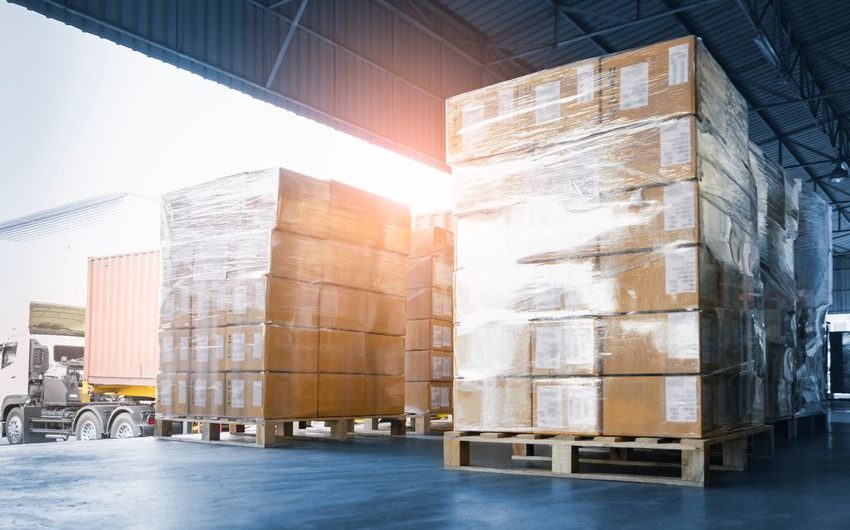
Process control charts
Process control charts can be a useful tool to visualize performance metrics and set a baseline for future enhancements. They also help improve output. These charts help operators, managers, and other stakeholders to get on the same page. They identify common causes of variation, set the right path for improvement, and help them communicate with each other. These charts are especially useful for processes with unusual patterns of variation. Because they are very easy to make, process control charts can be used for visual management. They can also be used to show the status of any system or process.
The primary function of a control chart is to track process performance over time. These charts display the sequence of samples and measurements that allow managers to determine whether or not the process is stable. These charts can be used to identify problems and suggest solutions. The centerline of the control chart is usually a line segment, based on which an operator can easily compare the process's performance with its baseline. The control limits typically have three standard deviations above or below the centerline.
FIFO Lane
FIFO lanes may increase throughput or utilization of a system. Imagine a line of assembly or a counter selling fast food. Most people have experienced the frustration of waiting in long lines to get what they want. The FiFo lane helps you manage the flow of work by establishing priority in queues by using visual management. These lanes can be defined by marking shelf spaces with labels, roller conveyor marks, or painted lines. The first job from Process A would move into the first FIFO lane. The next job will be moved to the next vacant position.
Implementing time registration can be a great way to improve FIFO lane visual organization. Employees can log the date and time of each item that is placed in a FIFO lane when carts have been loaded. Some employees use digital clocks for counting the products as soon as they are placed in the FIFO lane. To record time on carts you can use whiteboard stickers. These whiteboard stickers can be used to indicate the order of each step.
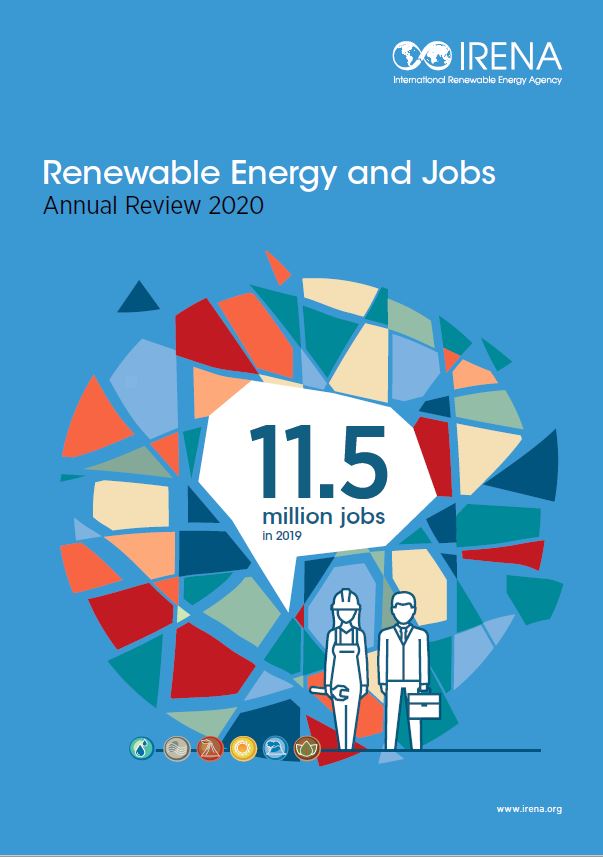
Lean daily management board
A multidisciplinary team was responsible for creating the Lean Daily Management Board. The board is based in part on five predetermined indicators: patient outcomes; documentation adherence; employee engagement and productivity. Each day, the team met to review each area's progress. The team used a checklist for daily activities such as medication compliance and medication drops to verify them. To deal with any falls, the team used a problem-solving instrument. Initial data was collected in January 2014. It showed a 75% rate for medication scanning and a fall rate that was 1.32/1000 patient day. These initial data did not include patient care or continuing education.
Instead of looking at a process's performance over a long time period, daily management makes it visible. This allows managers to react to issues as they arise. Poor performers are able to stretch their work in order to not be asked to do more. Poor performers must be able to clearly see the stretching work and account for the additional time and effort required to complete the work. Even though daily management isn’t intended to be punishing, it will highlight any inefficient or ineffective processes. People issues should be addressed for those who can't point out a process's failure.
FAQ
What does it take to run a logistics business?
To be a successful businessman in logistics, you will need many skills and knowledge. Effective communication skills are necessary to work with suppliers and clients. It is important to be able to analyse data and draw conclusions. You must be able to work well under pressure and handle stressful situations. To increase efficiency and creativity, you need to be creative. Strong leadership qualities are essential to motivate your team and help them achieve their organizational goals.
It is important to be organized and efficient in order to meet tight deadlines.
How can we increase manufacturing efficiency?
First, determine which factors have the greatest impact on production time. We then need to figure out how to improve these variables. If you don’t know how to start, look at which factors have the greatest impact upon production time. Once you've identified them all, find solutions to each one.
What is the role of a production manager?
A production planner ensures all aspects of the project are delivered on time, within budget, and within scope. They also ensure that the product/service meets the client’s needs.
What does warehouse refer to?
A warehouse or storage facility is where goods are stored before they are sold. It can be indoors or out. In some cases, it may be a combination of both.
Statistics
- According to the United Nations Industrial Development Organization (UNIDO), China is the top manufacturer worldwide by 2019 output, producing 28.7% of the total global manufacturing output, followed by the United States, Japan, Germany, and India.[52][53] (en.wikipedia.org)
- In 2021, an estimated 12.1 million Americans work in the manufacturing sector.6 (investopedia.com)
- [54][55] These are the top 50 countries by the total value of manufacturing output in US dollars for its noted year according to World Bank.[56] (en.wikipedia.org)
- Many factories witnessed a 30% increase in output due to the shift to electric motors. (en.wikipedia.org)
- (2:04) MTO is a production technique wherein products are customized according to customer specifications, and production only starts after an order is received. (oracle.com)
External Links
How To
Six Sigma in Manufacturing
Six Sigma is "the application statistical process control (SPC), techniques for continuous improvement." Motorola's Quality Improvement Department developed it at their Tokyo plant in Japan in 1986. Six Sigma is a method to improve quality through standardization and elimination of defects. In recent years, many companies have adopted this method because they believe there is no such thing as perfect products or services. Six Sigma seeks to reduce variation between the mean production value. If you take a sample and compare it with the average, you will be able to determine how much of the production process is different from the norm. If there is a significant deviation from the norm, you will know that something needs to change.
Understanding the nature of variability in your business is the first step to Six Sigma. Once you have a good understanding of the basics, you can identify potential sources of variation. This will allow you to decide if these variations are random and systematic. Random variations occur when people do mistakes. Symmetrical variations are caused due to factors beyond the process. These are, for instance, random variations that occur when widgets are made and some fall off the production line. It would be considered a systematic problem if every widget that you build falls apart at the same location each time.
After identifying the problem areas, you will need to devise solutions. This could mean changing your approach or redesigning the entire process. You should then test the changes again after they have been implemented. If they don't work you need to rework them and come up a better plan.