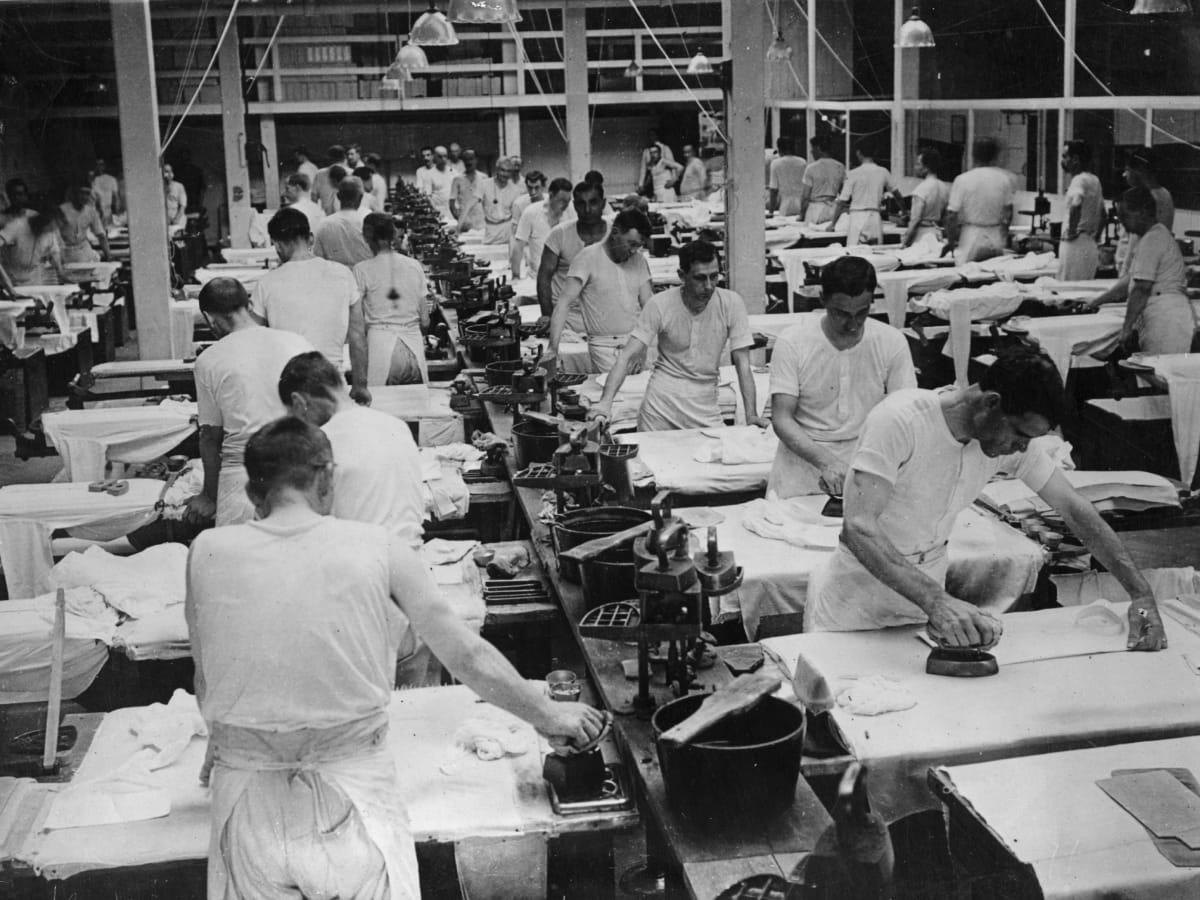
The key elements of bringing back manufacturing to America are reshoring and Opportunity zones, Deregulatory strategy, and lower transportation cost. What can the United States help to do? Here are some examples:
Relocation
Many companies have started to reshoring production to the U.S., such as Intel, which has invested $20 billion to construct two new Arizona semiconductor plants. General Motors is one of the companies that has begun to shift their production to Michigan. Michigan is expected to be a hub for lithium-based products. US Steel is instead building a plant in Alabama and Arkansas, rather than investing $3 billion to build its new steelmaking facility abroad. Other companies considering reshoring include Lockheed Electric, General Electric, as well as Thermo Fisher.
Opportunity zones
Trump is a passionate supporter for opportunity zones. To further support the creation of these zones, it created the White House Opportunity and Revitalization Council. The council has expanded the quoting form and prioritized them. However, local investors in California have one arm tied when it comes to opportunity zones. These are five strategies local investors could use to maximize investment opportunities.
Deregulatory Policy
The United States has struggled for years to attract major manufacturers. It is currently losing out on countries like China, which subsidizes new manufacturing facilities. The tide is turning, however. Walmart and other major companies are increasing their investment in the U.S. A recent study by the Manufacturing Institute reveals that American manufacturing is 9 per cent cheaper than manufacturing in nine high-cost countries.
Transport costs can be reduced
Reducing transportation costs is one of the most significant factors driving companies to relocate their manufacturing to the United States. Because labor costs in the United States are lower than abroad, companies can bring back manufacturing jobs. It is not easy to move manufacturing operations to the United States. However, it can take several years to bring new jobs to the United States. The cost of goods will rise, but there would be numerous benefits. Covid-19 was a recent example of supply chain issues being brought to the forefront. Products like pharmaceuticals, toilet paper, and other products were affected.
Qualified labor
The recent presidential elections have revealed the surprising political relevance of manufacturing. Commentators said that "U.S. manufacturers is having a moment." Unfortunately, campaign rhetoric rarely leads to long-term commitment. Washington D.C. debates tend to focus only on trade and issues that aren't directly beneficial to manufacturing. They also neglect to address strategies that would support manufacturing communities and clusters.
FAQ
How is a production manager different from a producer planner?
The primary difference between a producer planner and a manager of a project is that the manager usually plans and organizes the whole project, while a production planner is only involved in the planning stage.
How can efficiency in manufacturing be improved?
First, determine which factors have the greatest impact on production time. We then need to figure out how to improve these variables. If you don’t know where to begin, consider which factors have the largest impact on production times. Once you identify them, look for solutions.
What is the distinction between Production Planning or Scheduling?
Production Planning (PP) refers to the process of determining how much production is needed at any given moment. Forecasting demand is one way to do this.
Scheduling is the process of assigning specific dates to tasks so they can be completed within the specified timeframe.
What is the best way to learn about manufacturing?
The best way to learn about manufacturing is through hands-on experience. You can read books, or watch instructional videos if you don't have the opportunity to do so.
Can some manufacturing processes be automated?
Yes! Since ancient times, automation has been in existence. The Egyptians created the wheel thousands years ago. Today, robots assist in the assembly of lines.
Robotics is used in many manufacturing processes today. These include:
-
Assembly line robots
-
Robot welding
-
Robot painting
-
Robotics inspection
-
Robots that produce products
Manufacturing could also benefit from automation in other ways. For instance, 3D printing allows us make custom products and not have to wait for months or even weeks to get them made.
Statistics
- (2:04) MTO is a production technique wherein products are customized according to customer specifications, and production only starts after an order is received. (oracle.com)
- It's estimated that 10.8% of the U.S. GDP in 2020 was contributed to manufacturing. (investopedia.com)
- You can multiply the result by 100 to get the total percent of monthly overhead. (investopedia.com)
- Job #1 is delivering the ordered product according to specifications: color, size, brand, and quantity. (netsuite.com)
- According to the United Nations Industrial Development Organization (UNIDO), China is the top manufacturer worldwide by 2019 output, producing 28.7% of the total global manufacturing output, followed by the United States, Japan, Germany, and India.[52][53] (en.wikipedia.org)
External Links
How To
How to Use 5S to Increase Productivity in Manufacturing
5S stands for "Sort", 'Set In Order", 'Standardize', & Separate>. Toyota Motor Corporation created the 5S methodology in 1954. It improves the work environment and helps companies to achieve greater efficiency.
This method aims to standardize production processes so that they are repeatable, measurable and predictable. Cleaning, sorting and packing are all done daily. This knowledge allows workers to be more efficient in their work because they are aware of what to expect.
There are five steps that you need to follow in order to implement 5S. Each step requires a different action to increase efficiency. By sorting, for example, you make it easy to find the items later. You arrange items by placing them in an order. Then, after you separate your inventory into groups, you store those groups in containers that are easy to access. You can also label your containers to ensure everything is properly labeled.
Employees must be able to critically examine their work practices. Employees must be able to see why they do what they do and find a way to achieve them without having to rely on their old methods. They will need to develop new skills and techniques in order for the 5S system to be implemented.
In addition to increasing efficiency, the 5S method also improves morale and teamwork among employees. They feel more motivated to work towards achieving greater efficiency as they see the results.