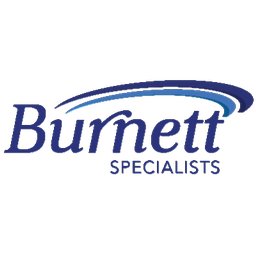
Toyota Motor Manufacturing Indiana Inc., located in Gibson County in Indiana, is the first Toyota plant that is wholly owned by Toyota. It produces Toyota's full-size pickup trucks including the Avalon, Corolla and Corolla as well as the Sienna minivan. It also produces the Toyota RAV4 Hybrid, which is the best selling hybrid in Toyota history.
The plant was originally planned to manufacture the Toyota Highlander, but instead moved to Gibson County, Indiana. The plant has been producing Toyota's RAV4 Hybrid compact SUV and the Lexus ES 350 since 2011. Toyota spent more that $1.33billion at the plant in 2017.
The plant also manufactures the Toyota Safety Sense 2.5+, which features automatic emergency braking. The plant is also preparing all new Camry models for 2018. New features include a new transmission, greater power and a stylish design. It will cost $25,900
Toyota's production of the Toyota Camry is the largest in the United States. It is America's best-selling midsize sedan, and it has been for over 15 years. In Kentucky, Toyota has made 10 million Camry cars. The hybrid model is being manufactured in the plant's first production facility in North America.
Toyota Production System is an assortment of practices and techniques that improve efficiency and quality. This system includes 600 Toyota engineers. It also houses the Toyota Production Engineering and Manufacturing Center. The center will also be the first to assemble hydrogen fuel cell modules for heavy duty commercial trucks. The facility can make up to 100,000 vehicles per annum.
Toyota has spent $1.5 billion on the plant in the last five year. It also hired 700 more employees. The investment will result in 470,100 new jobs in the United States by 2020. Toyota has also invested more than $147 million in Kentucky's nonprofit partners since 1986.
The Toyota Camry has a reputation for being dependable and fashionable. It has the GA-K platform, and a new transmission. It also has a fun driving experience. Consumer Reports ranked the Toyota Camry among the top-selling vehicles in America in July 2018.
Toyota's production system has many elements. These include continuous improvement, just in-time parts delivery and a sophisticated robotic welding machine. Toyota's Kentucky Investment in Kentucky has been demonstrated by the Toyota Production Engineering and Manufacturing Center.
Toyota's new production hall design saves on construction and cooling costs. The Visitor Center includes interactive video screens and exhibits about hybrid technology. During the next 10 years, Toyota will produce up to 2 million vehicles in North America. This facility is the largest Toyota outside Japan.
Toyota's New Global Architecture represents a major step forward in improving the company’s production system. This strategy includes a revamped engine and organization of production. It also includes a module that unifies all vehicle components. While the new design is a reflection of Toyota's traditional values, it retains its innovative spirit.
FAQ
How can manufacturing reduce production bottlenecks?
Production bottlenecks can be avoided by ensuring that processes are running smoothly during the entire production process, starting with the receipt of an order and ending when the product ships.
This includes both planning for capacity and quality control.
Continuous improvement techniques such Six Sigma are the best method to accomplish this.
Six Sigma is a management method that helps to improve quality and reduce waste.
It emphasizes consistency and eliminating variance in your work.
What are manufacturing and logistic?
Manufacturing is the act of producing goods from raw materials using machines and processes. Logistics covers all aspects involved in managing supply chains, including procurement and production planning. Sometimes manufacturing and logistics are combined to refer to a wider term that includes both the process of creating products as well as their delivery to customers.
What does warehouse refer to?
Warehouses and storage facilities are where goods are kept before being sold. It can be either an indoor or outdoor space. In some cases, it may be a combination of both.
Is automation important for manufacturing?
Automation is important not only for manufacturers but also for service providers. It allows them provide faster and more efficient services. In addition, it helps them reduce costs by reducing human errors and improving productivity.
How does a production planner differ from a project manager?
The major difference between a Production Planner and a Project Manager is that a Project Manager is often the person responsible for organizing and planning the entire project. While a Production Planner is involved mainly in the planning stage,
Statistics
- Job #1 is delivering the ordered product according to specifications: color, size, brand, and quantity. (netsuite.com)
- According to a Statista study, U.S. businesses spent $1.63 trillion on logistics in 2019, moving goods from origin to end user through various supply chain network segments. (netsuite.com)
- (2:04) MTO is a production technique wherein products are customized according to customer specifications, and production only starts after an order is received. (oracle.com)
- Many factories witnessed a 30% increase in output due to the shift to electric motors. (en.wikipedia.org)
- In the United States, for example, manufacturing makes up 15% of the economic output. (twi-global.com)
External Links
How To
Six Sigma: How to Use it in Manufacturing
Six Sigma is defined as "the application of statistical process control (SPC) techniques to achieve continuous improvement." Motorola's Quality Improvement Department, Tokyo, Japan, developed it in 1986. Six Sigma's core idea is to improve the quality of processes by standardizing and eliminating defects. Since there are no perfect products, or services, this approach has been adopted by many companies over the years. The main goal of Six Sigma is to reduce variation from the mean value of production. This means that you can take a sample from your product and then compare its performance to the average to find out how often the process differs from the norm. If the deviation is excessive, it's likely that something needs to be fixed.
Understanding how variability works in your company is the first step to Six Sigma. Once you've understood that, you'll want to identify sources of variation. It is important to identify whether the variations are random or systemic. Random variations occur when people do mistakes. Symmetrical variations are caused due to factors beyond the process. You could consider random variations if some widgets fall off the assembly lines. However, if you notice that every time you assemble a widget, it always falls apart at exactly the same place, then that would be a systematic problem.
Once you've identified where the problems lie, you'll want to design solutions to eliminate those problems. The solution could involve changing how you do things, or redesigning your entire process. To verify that the changes have worked, you need to test them again. If they don't work you need to rework them and come up a better plan.