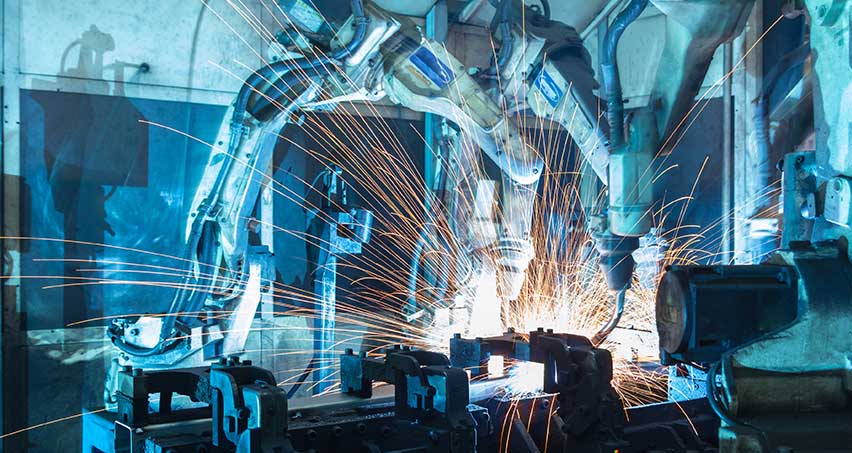
But value stream mapping can make your manufacturing processes more efficient. It's not simple. This involves mapping product families and their products. Training is essential for the team. You might also need a value-stream manager. Your team should get support from the leadership in order to successfully implement the strategy. Larger companies often have their own value stream managers who oversee the mapping process. Even though smaller companies can manage without a VSM Manager, it is a good idea to let the leadership know the possible improvements.
Lean Six Sigma
When you use Value Stream Mapping in Lean Six Sigma, you'll document the flow of information from customers to suppliers. Your customer is the most important thing to include on your value-stream map. Start at the shipping point and work your way upstream. Include a box with a customer's data, which will tell you how often a product must be produced in order to meet the demand. The Takt time is the amount of time it takes for a product to be produced. It should also be compared to the cycle times of the product. If Takt is longer than the cycle times, it means that there is a bottleneck.
Value Stream Maps are a way for companies to identify waste at each stage of their processes. Value stream mapping is a way to identify non-value-added activities, analyze the flow of information and identify threats and opportunities in your business. It is also useful in identifying bottlenecks or determining how to improve the efficiency of the whole process. Value Stream mapping in Lean Six Sigma is more than just improving the flow information. A Value Stream Map may be a valuable tool to help implement Lean Six Sigma.
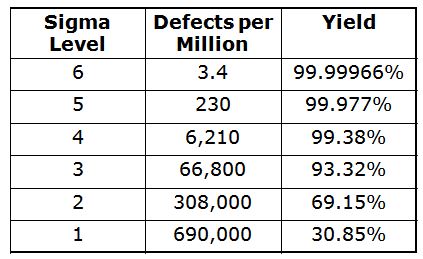
Lean Healthcare
Value stream mapping can be used to improve the synchronization between activities within the medical field. It helps to identify opportunities for improvement and determines strategies for implementation. A map, for example, can show how a patient flows from the moment they arrive at the hospital to the time when they leave the hospital after treatment. You can visualize these flow paths and create a timeline to guide you through the entire process. This will help you identify waste-generating activities and value-added activities.
To make VSM in Lean Healthcare more efficient, the authors recommend that clear definitions be established for all terms. They also suggest sharing examples of successes and failures and establishing appropriate indicators. These indicators can be used to replicate the results and adapt them to specific situations. Lean methodologies in the healthcare sector are more likely to produce positive outcomes. The authors recommend that healthcare professionals agree on a common definition for value stream mapping to ensure that this methodology is widely used.
Lean Manufacturing
In order to begin value stream mapping, you need input from key stakeholders. The team should include all people responsible to fulfill customer needs. They should also include people who perform critical tasks and activities to ensure the flow of information. This value stream mapping process can be used to identify waste and increase efficiency by gathering input from key stakeholders. First, determine the scope of value stream mapping.
Next, select the product or process to improve and train the team on value stream mapping. The mapping process starts with the customer's needs and covers all aspects of the decision-making, communication and communications processes. Value stream mapping ultimately aims to eliminate waste while increasing customer satisfaction. Lean manufacturing is a sustainable and viable solution to any company's challenges by identifying what factors contribute to customer satisfaction.
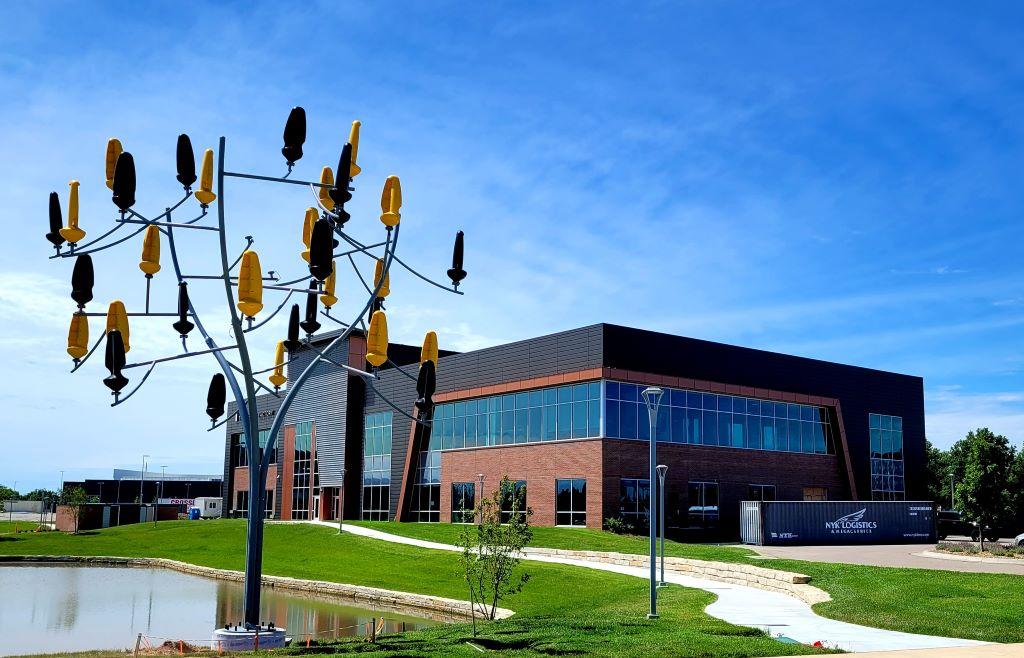
Future state value stream mapping
Future state value streaming mapping is an excellent tool to identify waste. This mapping has two goals: to identify and eliminate the causes of waste. Future state ideas can be marked with the exact same symbols as current state maps. Takt Time is an important concept to consider in future state value stream mapping. It helps you efficiently allocate resources and pinpoint areas of waste. The future state value stream map can be a powerful tool for your company, too.
Once you have identified where there are problems and how they relate to the future, it's now time to map the steps necessary to get there. For teams, the future state map can act as a constant point-of-reference to assist them in completing projects and reaching their target value. It is important to update your future stream mapping of state value every six to twelve mois to ensure that you are able to monitor your progress. You should update your future state map as new projects are launched and modifications made.
FAQ
How can overproduction in manufacturing be reduced?
Improved inventory management is the key to reducing overproduction. This would reduce the amount of time spent on unnecessary activities such as purchasing, storing, and maintaining excess stock. By doing this, we could free up resources for other productive tasks.
A Kanban system is one way to achieve this. A Kanbanboard is a visual tool that allows you to keep track of the work being done. A Kanban system allows work items to move through several states before reaching their final destination. Each state is assigned a different priority.
If work is moving from one stage to the other, then the current task can be completed and moved on to the next. A task that is still in the initial stages of a process will be considered complete until it moves on to the next stage.
This allows work to move forward and ensures that no work is missed. Managers can see how much work has been done and the status of each task at any time with a Kanban Board. This data allows them adjust their workflow based upon real-time data.
Lean manufacturing is another way to manage inventory levels. Lean manufacturing seeks to eliminate waste from every step of the production cycle. Any product that isn't adding value can be considered waste. Some common types of waste include:
-
Overproduction
-
Inventory
-
Unnecessary packaging
-
Materials in excess
These ideas can help manufacturers improve efficiency and reduce costs.
Why is logistics important for manufacturing?
Logistics are an integral part any business. They help you achieve great results by helping you manage all aspects of product flow, from raw materials to finished goods.
Logistics plays a significant role in reducing cost and increasing efficiency.
What does "warehouse" mean?
A warehouse is a place where goods are stored until they are sold. It can be either an indoor or outdoor space. In some cases, it may be a combination of both.
What is the responsibility of a logistics manager?
A logistics manager makes sure that all goods are delivered on-time and in good condition. This is done by using his/her experience and knowledge of the company's products. He/she should also ensure enough stock is available to meet demand.
What skills are required to be a production manager?
A production planner must be organized, flexible, and able multitask to succeed. It is also important to be able communicate with colleagues and clients.
Is there anything we should know about Manufacturing Processes prior to learning about Logistics.
No. No. Knowing about manufacturing processes will help you understand how logistics works.
Statistics
- You can multiply the result by 100 to get the total percent of monthly overhead. (investopedia.com)
- [54][55] These are the top 50 countries by the total value of manufacturing output in US dollars for its noted year according to World Bank.[56] (en.wikipedia.org)
- In 2021, an estimated 12.1 million Americans work in the manufacturing sector.6 (investopedia.com)
- Job #1 is delivering the ordered product according to specifications: color, size, brand, and quantity. (netsuite.com)
- (2:04) MTO is a production technique wherein products are customized according to customer specifications, and production only starts after an order is received. (oracle.com)
External Links
How To
How to Use lean manufacturing in the Production of Goods
Lean manufacturing refers to a method of managing that seeks to improve efficiency and decrease waste. It was first developed in Japan in the 1970s/80s by Taiichi Ahno, who was awarded the Toyota Production System (TPS), award from KanjiToyoda, the founder of TPS. Michael L. Watkins published the first book on lean manufacturing in 1990.
Lean manufacturing, often described as a set and practice of principles, is aimed at improving the quality, speed, cost, and efficiency of products, services, and other activities. It emphasizes eliminating waste and defects throughout the value stream. Lean manufacturing can be described as just-in–time (JIT), total productive maintenance, zero defect (TPM), or even 5S. Lean manufacturing seeks to eliminate non-value added activities, such as inspection, work, waiting, and rework.
In addition to improving product quality and reducing costs, lean manufacturing helps companies achieve their goals faster and reduces employee turnover. Lean Manufacturing is one of the most efficient ways to manage the entire value chains, including suppliers and customers as well distributors and retailers. Many industries worldwide use lean manufacturing. For example, Toyota's philosophy underpins its success in automobiles, electronics, appliances, healthcare, chemical engineering, aerospace, paper, food, etc.
Five fundamental principles underlie lean manufacturing.
-
Define Value: Identify the social value of your business and what sets you apart.
-
Reduce Waste – Eliminate all activities that don't add value throughout the supply chain.
-
Create Flow. Ensure that your work is uninterrupted and flows seamlessly.
-
Standardize and Simplify – Make processes as consistent, repeatable, and as simple as possible.
-
Build relationships - Develop and maintain personal relationships with both your internal and external stakeholders.
Lean manufacturing isn’t new, but it has seen a renewed interest since 2008 due to the global financial crisis. Many businesses are now using lean manufacturing to improve their competitiveness. Some economists even believe that lean manufacturing can be a key factor in economic recovery.
Lean manufacturing is now becoming a common practice in the automotive industry, with many benefits. These include better customer satisfaction and lower inventory levels. They also result in lower operating costs.
It can be applied to any aspect of an organisation. Lean manufacturing is most useful in the production sector of an organisation because it ensures that each step in the value-chain is efficient and productive.
There are three main types of lean manufacturing:
-
Just-in Time Manufacturing, (JIT): This kind of lean manufacturing is also commonly known as "pull-systems." JIT is a process in which components can be assembled at the point they are needed, instead of being made ahead of time. This strategy aims to decrease lead times, increase availability of parts and reduce inventory.
-
Zero Defects Manufacturing (ZDM),: ZDM is a system that ensures no defective units are left the manufacturing facility. You should repair any part that needs to be repaired during an assembly line. This applies to finished products, which may need minor repairs before they are shipped.
-
Continuous Improvement (CI): CI aims to improve the efficiency of operations by continuously identifying problems and making changes in order to eliminate or minimize waste. Continuous improvement refers to continuous improvement of processes as well people and tools.