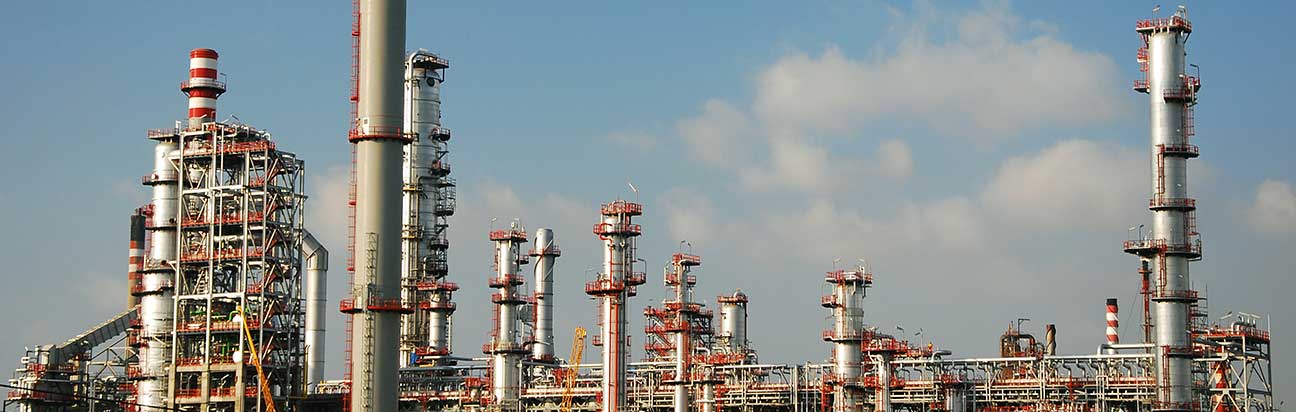
A blue collar job is generally a manual labor job. These jobs could be in manufacturing, agriculture, healthcare, hospitality or construction. Some require some level or skill, such a plumber, electrician, etc. While others are less skilled. Blue collar jobs are good for career growth and pay decent salaries.
The Fourth Industrial Revolution changes the employment market for manual workers. This revolution involves artificial intelligence (AI), robotics, machine-learning, and 3D printing. For companies to succeed, it will require a skilled workforce. Firms will have to move away transactional relationships in favor of more enduring ones.
Companies are often forced to hire workers from abroad. These workers might be hired to make per-item payment in some cases. Others could be paid by a project. Blue collar jobs are on the rise, which is positive in all cases.
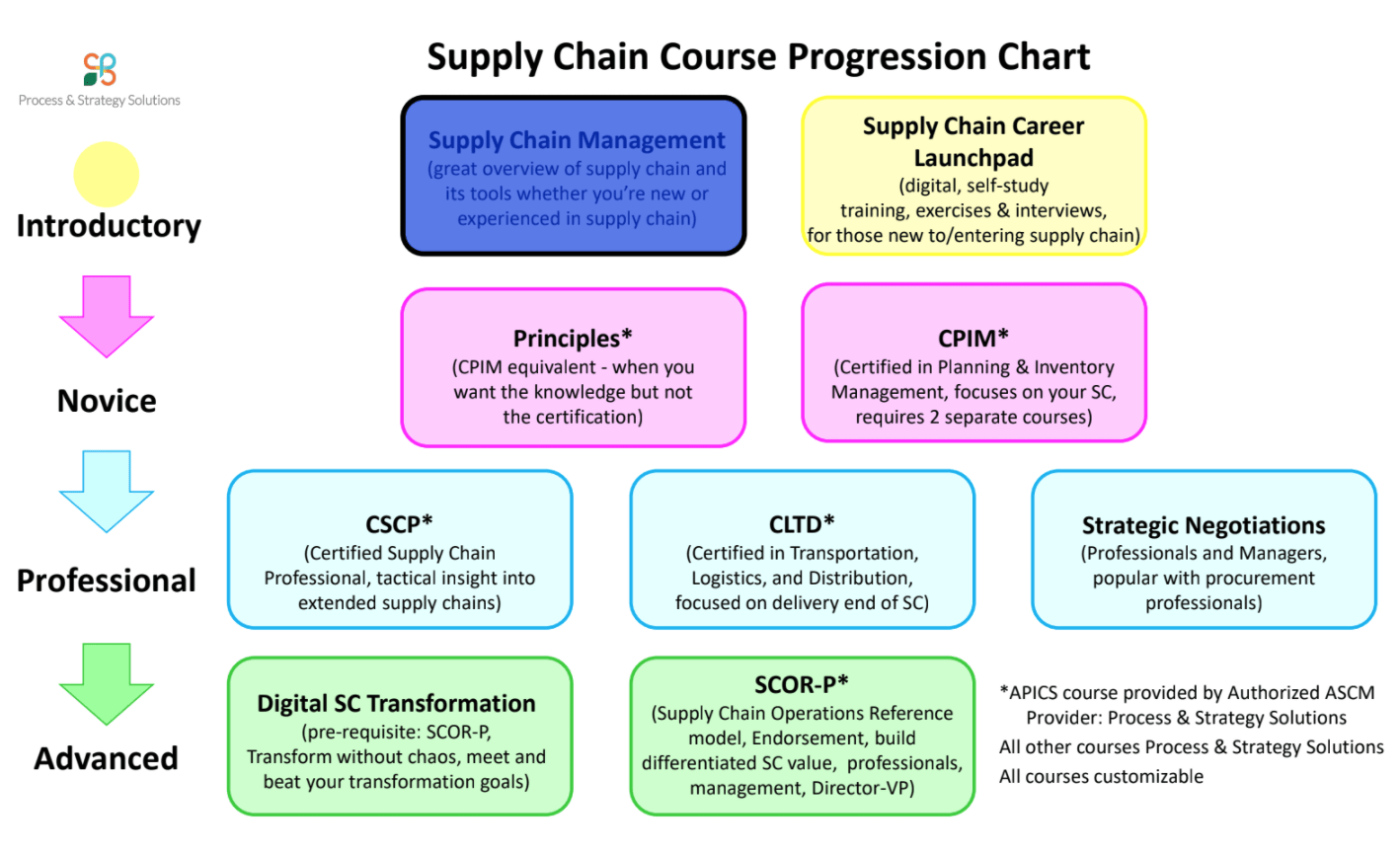
These jobs involve some manual labor, but they are better than white collar positions. Because these jobs are a good source of income, companies are willing to invest in training their employees. A few examples of these jobs include electrical and electronic repairers, signal and track switch repairers, and nuclear power reactor operators. These jobs require only a high school diploma, while others require on-the-job training.
Blue collar jobs are also more plentiful than white collar jobs. In fact, blue collar workers make up a substantial part of the Indian workforce. India has 210 million workers in the agricultural sector, and 290 million in the non-agricultural sector. The demand is for blue collar workers growing rapidly.
Companies' management of their blue-collar workforce is changing as well with the Fourth Industrial Revolution. Companies are moving away from transactional relationships to build lasting relationships, and replacing manual jobs by digital ones. Firms can create stronger relationships and better productivity by prioritizing their employees.
Although blue collar workers are highly in demand, they have to face competing realities. Some may worry about their job stability or retirement. Blue collar workers can be optimistic about their prospects, regardless of any concerns. In fact, the percentage of blue-collar workers saving for retirement is growing. The popularity of blue collar jobs is likely to increase as the economy recovers.
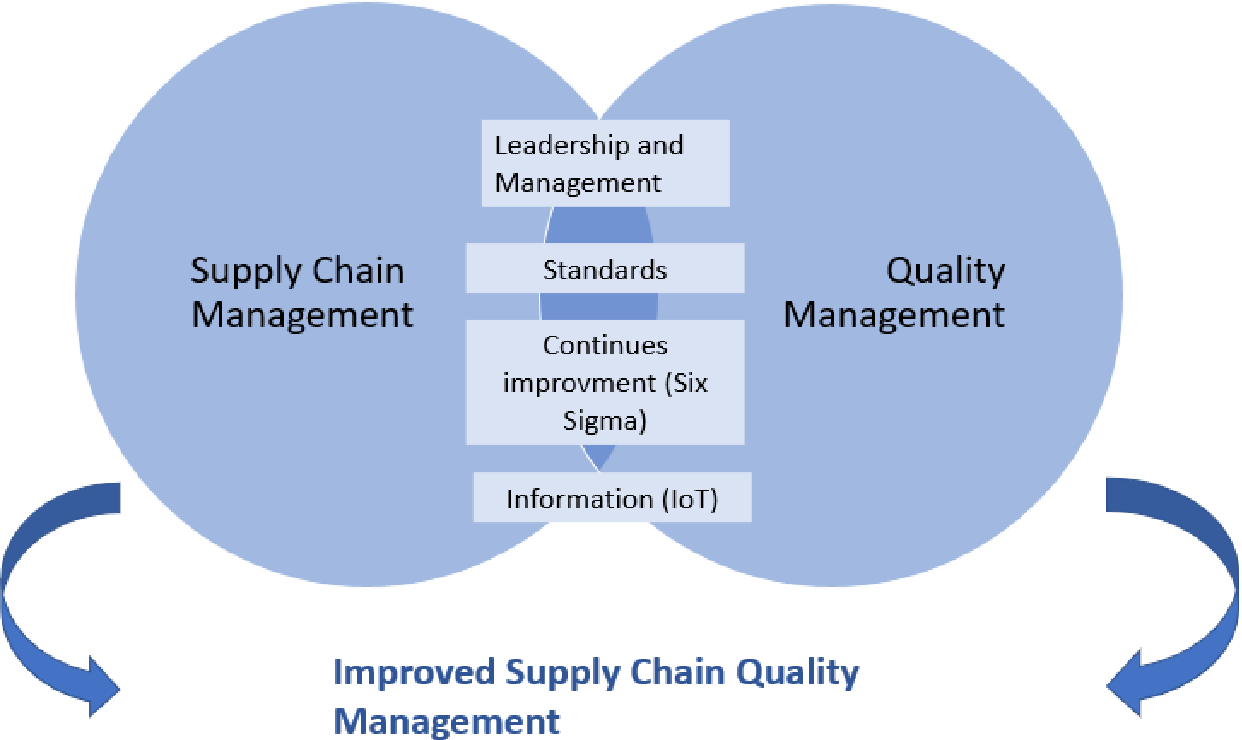
These jobs are not at risk from automation. The Association for Manufacturing Technology has found that for every job that is replaced by technology there are five new jobs. Signal and track switch repairers earned $76,210 an average salary, which was the largest increase in salaries.
In addition to being more lucrative, blue collar positions are also becoming more popular. Blue collar jobs offer a better pay than the average. Blue collar jobs are known for their ability to solve problems and offer good career opportunities.
FAQ
What is the importance of automation in manufacturing?
Automation is important not only for manufacturers but also for service providers. Automation allows them to deliver services quicker and more efficiently. It helps them to lower costs by reducing human errors, and improving productivity.
Are there any Manufacturing Processes that we should know before we can learn about Logistics?
No. You don't have to know about manufacturing processes before learning about logistics. Understanding the manufacturing process will allow you to better understand logistics.
What skills is required for a production planner?
Production planners must be flexible, organized, and able handle multiple tasks. You must also be able to communicate effectively with clients and colleagues.
How does a Production Planner differ from a Project Manager?
A production planner is more involved in the planning phase of the project than a project manger.
How can I learn about manufacturing?
Experience is the best way for you to learn about manufacturing. If that is not possible, you could always read books or view educational videos.
What are the main products of logistics?
Logistics involves the transportation of goods from point A and point B.
These include all aspects related to transport such as packaging, loading and transporting, storing, transporting, unloading and warehousing inventory management, customer service. Distribution, returns, recycling are some of the options.
Logisticians make sure that the right product arrives at the right place at the correct time and in safe conditions. They provide information on demand forecasts as well stock levels, production schedules and availability of raw material.
They keep track and monitor the transit of shipments, maintain quality standards, order replenishment and inventories, coordinate with suppliers, vendors, and provide support for sales and marketing.
Statistics
- (2:04) MTO is a production technique wherein products are customized according to customer specifications, and production only starts after an order is received. (oracle.com)
- According to a Statista study, U.S. businesses spent $1.63 trillion on logistics in 2019, moving goods from origin to end user through various supply chain network segments. (netsuite.com)
- [54][55] These are the top 50 countries by the total value of manufacturing output in US dollars for its noted year according to World Bank.[56] (en.wikipedia.org)
- You can multiply the result by 100 to get the total percent of monthly overhead. (investopedia.com)
- Job #1 is delivering the ordered product according to specifications: color, size, brand, and quantity. (netsuite.com)
External Links
How To
How to Use Six Sigma in Manufacturing
Six Sigma is defined as "the application of statistical process control (SPC) techniques to achieve continuous improvement." It was developed by Motorola's Quality Improvement Department at their plant in Tokyo, Japan, in 1986. Six Sigma's main goal is to improve process quality by standardizing processes and eliminating defects. In recent years, many companies have adopted this method because they believe there is no such thing as perfect products or services. Six Sigma seeks to reduce variation between the mean production value. If you take a sample and compare it with the average, you will be able to determine how much of the production process is different from the norm. If there is a significant deviation from the norm, you will know that something needs to change.
Understanding the nature of variability in your business is the first step to Six Sigma. Once you understand that, it is time to identify the sources of variation. These variations can also be classified as random or systematic. Random variations occur when people make mistakes; systematic ones are caused by factors outside the process itself. Random variations would include, for example, the failure of some widgets to fall from the assembly line. It would be considered a systematic problem if every widget that you build falls apart at the same location each time.
Once you've identified where the problems lie, you'll want to design solutions to eliminate those problems. The solution could involve changing how you do things, or redesigning your entire process. Test them again once you've implemented the changes. If they don't work you need to rework them and come up a better plan.