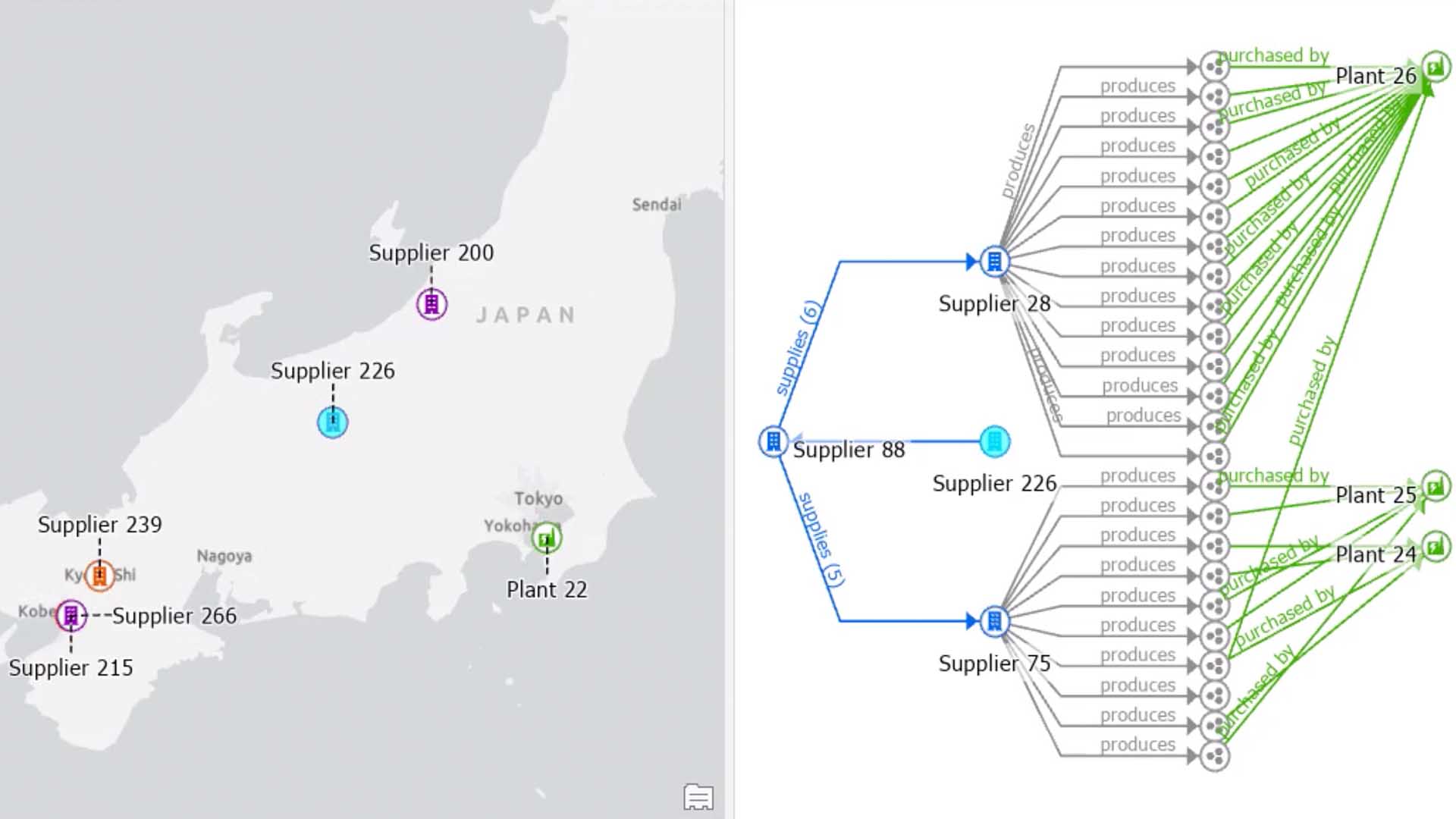
In many industries, supply chain disruptions have resulted in long-term productivity loss and economic losses. It is clear that companies have not been proactive in managing risk, which has led to disruptions.
In the face of growing internationalization, the defence industry has been affected by this trend. Several technologies, including high-quality carbon fibre and advanced semi-conductors, may run out of supplies. This can increase dependence on foreign capital as well as oligopolistic behavior. Dual products pose a greater risk. These products may present reliability and safety issues.
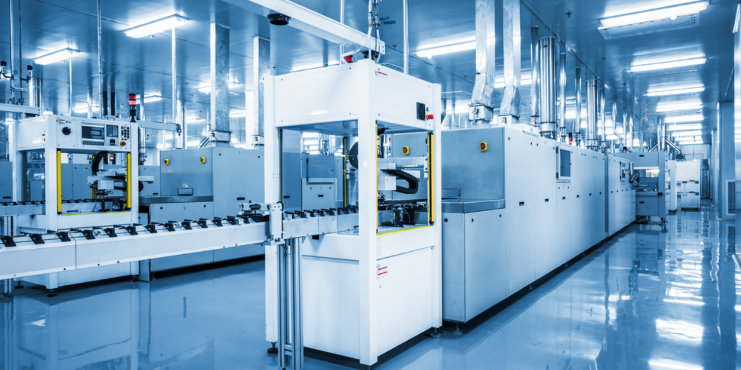
Globalization has made it crucial that critical minerals are protected in order to ensure the future development of industrial systems. Some minerals may be distributed in economically underdeveloped areas and are therefore vulnerable to political instability. Under different circumstances, the global optimal allocation of critical mineral resources changes. China is a critical node in the global critical minerals value chain, but the industry is highly dependent on other nations. It is important that governments establish a global critical metal allocation network that includes multiple nations, instead of concentrating resources within a single nation.
Discussions about the European Union's defense technology and industrial bases (DTIB), have been ongoing. The European Commission created the European Defence Agency to establish a framework for an EU-wide new defense industry. This new approach will bring about a number of changes in the EU's defence industry. Some technologies, for example, can only be provided by a small number of non-EU businesses. In the EU's defense sector, there will be both oligopoly as well as monopoly structures. Additionally, it will be easier to source certain raw materials from companies outside the EU. This will make it possible to develop a new type or sourcing strategy known as bundled volumes.
There is an increased focus on the development of a secure and resilient supply chain. There are many strategies that can be used to reduce the risk of disruptions in supply chains. One strategy is the implementation of a formal risk-management approach. Investing on a formal risk management strategy can help your supply chain thrive instead of just survive. It should involve both internal and external key stakeholders, including suppliers, investors and governments. Global supply chain dynamics should also be considered when managing the supply chain.
Security of the 99m/99mtc supply network is another critical policy issue. The policy approach created by the High-Level Group on Medical Radioisotopes(HLG-MR), ensures the long-term safety of the supply chain of radioisotopes. This included a review the global 99 M/99 M Tc supply chain, analysis of the economic effects of the supply, as well a policy approach.
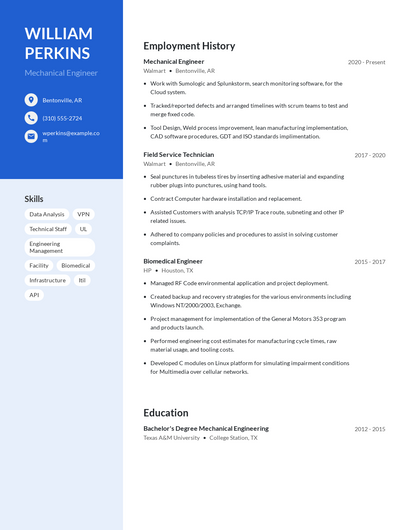
HLG-MR identified 2 main areas of vulnerability which should be addressed to improve the security of the 99m/99m supply chains. These include monopolistic behavior and foreign capital. These factors can cause significant risks and price increases. HLG-MR's policy approach also identified key steps to address these vulnerabilities.
FAQ
How can I learn about manufacturing?
Hands-on experience is the best way to learn more about manufacturing. If that is not possible, you could always read books or view educational videos.
What is production plan?
Production Planning refers to the development of a plan for every aspect of production. This document will ensure everything is in order and ready to go when you need it. You should also have information to ensure the best possible results on set. This includes location information, crew details, equipment specifications, and casting lists.
It is important to first outline the type of film you would like to make. You may already know where you want the film to be shot, or perhaps you have specific locations and sets you wish to use. Once you have identified the scenes and locations, you can start to determine which elements are required for each scene. If you decide you need a car and don't know what model to choose, this could be an example. In this case, you could start looking up cars online to find out what models are available and then narrow your choices by choosing between different makes and models.
After you've found the perfect car, it's time to start thinking about adding extras. Do you have people who need to be seated in the front seat? Or maybe you just need someone to push the car around. Maybe you want to change the interior color from black to white? These questions will help determine the look and feel you want for your car. Also, think about what kind of shots you would like to capture. You will be filming close-ups and wide angles. Perhaps you want to show the engine or the steering wheel? These things will help you to identify the car that you are looking for.
Once you have determined all of the above, you can move on to creating a schedule. You can use a schedule to determine when and where you need it to be shot. The schedule will show you when to get there, what time to leave, and when to return home. Everyone will know what they need and when. Book extra staff ahead of time if you need them. You should not hire anyone who doesn't show up because of your inaction.
When creating your schedule, you will also need to consider the number of days you need to film. Some projects may only take a couple of days, while others could last for weeks. You should consider whether you will need more than one shot per week when creating your schedule. Multiple takes of the same location will lead to higher costs and take more time. It is better to be cautious and take fewer shots than you risk losing money if you are not sure if multiple takes are necessary.
Another important aspect of production planning is setting budgets. You will be able to manage your resources if you have a realistic budget. Remember that you can always reduce the budget later on if you run into unforeseen problems. However, it is important not to overestimate the amount that you will spend. If you underestimate how much something costs, you'll have less money to pay for other items.
Production planning is a complicated process. But once you understand how everything works together, it becomes much easier to plan future project.
How can excess manufacturing production be reduced?
In order to reduce excess production, you need to develop better inventory management methods. This would reduce time spent on activities such as purchasing, stocking, and maintaining excess stock. This would allow us to use our resources for more productive tasks.
A Kanban system is one way to achieve this. A Kanbanboard is a visual tool that allows you to keep track of the work being done. A Kanban system allows work items to move through several states before reaching their final destination. Each state represents a different priority level.
For instance, when work moves from one stage to another, the current task is complete enough to be moved to the next stage. If a task is still in its beginning stages, it will continue to be so until it reaches the end.
This allows work to move forward and ensures that no work is missed. Managers can monitor the work being done by Kanban boards to see what is happening at any given time. This allows them to adjust their workflows based on real-time information.
Lean manufacturing can also be used to reduce inventory levels. Lean manufacturing works to eliminate waste throughout every stage of the production chain. Any product that isn't adding value can be considered waste. The following are examples of common waste types:
-
Overproduction
-
Inventory
-
Unnecessary packaging
-
Exceed materials
Manufacturers can increase efficiency and decrease costs by implementing these ideas.
How can manufacturing efficiency be improved?
The first step is to identify the most important factors affecting production time. The next step is to identify the most important factors that affect production time. You can start by identifying the most important factors that impact production time. Once you have identified the factors, then try to find solutions.
What types of jobs can you find in logistics
Logistics can offer many different jobs. Some of them are:
-
Warehouse workers – They load and unload pallets and trucks.
-
Transportation drivers – These drivers drive trucks and wagons to transport goods and pick up the goods.
-
Freight handlers, - They sort out and pack freight in warehouses.
-
Inventory managers - These are responsible for overseeing the stock of goods in warehouses.
-
Sales reps are people who sell products to customers.
-
Logistics coordinators: They plan and manage logistics operations.
-
Purchasing agents – They buy goods or services necessary to run a company.
-
Customer service representatives – They answer emails and phone calls from customers.
-
Shipping clerks: They process shipping requests and issue bills.
-
Order fillers - These people fill orders based on what has been ordered.
-
Quality control inspectors (QCI) - They inspect all incoming and departing products for potential defects.
-
Other - Logistics has many other job opportunities, including transportation supervisors, logistics specialists, and cargo specialists.
Is automation important in manufacturing?
Not only are service providers and manufacturers important, but so is automation. Automation allows them to deliver services quicker and more efficiently. It reduces human errors and improves productivity, which in turn helps them lower their costs.
Statistics
- In 2021, an estimated 12.1 million Americans work in the manufacturing sector.6 (investopedia.com)
- [54][55] These are the top 50 countries by the total value of manufacturing output in US dollars for its noted year according to World Bank.[56] (en.wikipedia.org)
- In the United States, for example, manufacturing makes up 15% of the economic output. (twi-global.com)
- Many factories witnessed a 30% increase in output due to the shift to electric motors. (en.wikipedia.org)
- It's estimated that 10.8% of the U.S. GDP in 2020 was contributed to manufacturing. (investopedia.com)
External Links
How To
How to use 5S to increase Productivity in Manufacturing
5S stands for "Sort", 'Set In Order", 'Standardize', & Separate>. Toyota Motor Corporation was the first to develop the 5S approach in 1954. It allows companies to improve their work environment, thereby achieving greater efficiency.
The idea behind standardizing production processes is to make them repeatable and measurable. It means tasks like cleaning, sorting or packing, labeling, and storing are done every day. Through these actions, workers can perform their jobs more efficiently because they know what to expect from them.
Implementing 5S involves five steps: Sort, Set in Order, Standardize Separate, Store, and Each step has a different action and leads to higher efficiency. By sorting, for example, you make it easy to find the items later. When you arrange items, you place them together. Next, organize your inventory into categories and store them in containers that are easily accessible. Labeling your containers will ensure that everything is correctly labeled.
Employees must be able to critically examine their work practices. Employees must understand why they do certain tasks and decide if there's another way to accomplish them without relying on the old ways of doing things. In order to use the 5S system effectively, they must be able to learn new skills.
The 5S method not only increases efficiency but also boosts morale and teamwork. They feel more motivated to work towards achieving greater efficiency as they see the results.